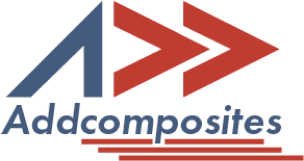
Tailored Composite Solutions for Diverse Industry Demands
Automated Fiber Placement (AFP) technology is pivotal in aerospace applications for producing lightweight, high-strength components. It is used to manufacture propeller blades, wing skins for air taxis, turbojet engine blades, structural elements of fuselages, aircraft wings, wing boxes, and interior structures of aircraft. These applications enhance the performance, efficiency, and safety of aerospace vehicles.
Read MoreAutomated Fiber Placement (AFP) technology is extensively used in the automotive industry to create lightweight and strong components. This includes battery enclosure systems, carbon fiber sleeves for electric motors, structural batteries, and energy storage hydrogen tanks. AFP is also employed in the manufacturing of driveshafts, bumpers, dashboard components, and various under-the-hood components, enhancing vehicle performance and efficiency.
Read MoreAutomated Fiber Placement (AFP) technology is crucial in marine applications for constructing lightweight and durable components. It is used to manufacture boat hulls, propeller blades, hydrofoils, and masts, enhancing the performance and efficiency of marine vessels.
Read MoreAutomated Fiber Placement (AFP) technology is vital for manufacturing lightweight and durable components for space applications, including solar panels, deployable booms, trusses, reflectors, antennas, propellant tanks, interstages, and satellite structures.
Read MoreAutomated Fiber Placement (AFP) technology is extensively used in defense applications to manufacture lightweight and high-strength components. This includes reflectors and antennas, missile components, and ballistic protection systems. AFP is also critical in producing UAVs (Unmanned Aerial Vehicles), including their blades and fins, as well as the structures of armored vehicles, enhancing their performance and durability.
Read MoreThe AFP-XS is a versatile, user-friendly system that easily switches from thermoset to dry fibers and thermoplastics. It integrates with humm3, enhancing fiber placement research and supporting local SMEs at Compositadour. In defense, AFP technology is essential for advanced composite components in aircraft, UAVs, and other applications. We look forward to partnering with Addcomposites to advance composite technologies in the defense sector.
The AFP-XS is a compact, efficient AFP system ideal for material testing, featuring AddPath's easy-to-use interface. Addcomposites' expertise and dedication are exceptional. In the marine industry, AFP technology is vital for high-performance composite hulls, decks, and structural parts. The AFP-XS is perfect for enhancing capabilities in this field.
Addcomposites has effectively integrated their tool into a complex robot cell with legacy equipment, showcasing their expertise. In the aerospace industry, AFP technology is vital for high-performance composite components in aircraft structures and satellite assemblies. We look forward to collaborating with Addcomposites and sharing knowledge at TU Delft. Their ability to adapt to our specific needs has been invaluable.