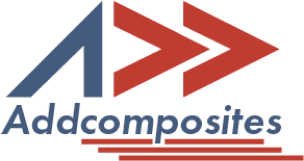
Picture this: A rotor spinning at 20,000 RPM experiences centrifugal forces that would tear apart most materials like tissue paper. At the outer edge of a high-speed rotor, permanent magnets endure forces exceeding 1,000 times gravity. Without proper containment, these brittle ceramic magnets would simply explode outward, destroying your motor in milliseconds.
During my time at ISRO, I witnessed firsthand how traditional solutions to such extreme engineering challenges often came with astronomical price tags. Today at Addcomposites, we're democratizing access to the technology that makes these extreme applications possible: precision-engineered composite sleeves with carefully controlled pre-stress.
The centrifugal force challenge is simple yet brutal - doubling your motor's RPM quadruples the forces trying to tear it apart. For modern electric motors pushing beyond 20,000 RPM, we're dealing with stresses that exceed what traditional materials can handle.
Consider this stark reality:
Advanced composite sleeves have been designed for tip speeds as high as 1200 m/s - that's Mach 2 at the rotor edge.
Pre-stress is like a precisely engineered bear hug for your magnets. By applying controlled compressive force when the rotor is at rest, we ensure the magnets stay compressed even under extreme centrifugal loads.
The goal is elegantly simple: Keep the magnets in compression at all times while staying within the sleeve's design limits.
This is where our AFP (Automated Fiber Placement) technology truly shines. Our systems offer unprecedented control:
For extreme applications, we offer a specialized high-tension configuration:
This high-tension capability allows us to push the boundaries of what's possible, enabling rotor designs that were previously unachievable.
The mismatch between carbon fiber's near-zero expansion and metal's significant growth creates a complex stress state that must be carefully managed. Our solution leverages:
Research shows that improper winding angle can reduce strength by 20-25% - precision matters.
Unlike metallic sleeves that fail catastrophically, composite sleeves give you warning. This graduated failure process has saved countless motors from complete destruction.
When implemented properly, the numbers tell the story:
At Addcomposites, we've created a complete ecosystem for composite sleeve manufacturing:
AddPath Software - Your digital twin environment
AFP-XS System - From €3,499/month
AFP-X System - Production ready
One Platform, Multiple Processes Switch between filament winding and AFP on the same system - no need for separate equipment.
Thermoplastic Revolution In-situ consolidation eliminates autoclaves:
Expert Support Included
Whether you're developing next-gen EV motors at 25,000 RPM, aerospace generators at 80,000 RPM, or pushing toward 100,000 RPM for energy storage, we have the solution.
Start Your Journey:
Take action today:
Download our resources:
From simulation to production, from 50N to 2000N tension capability, Addcomposites makes advanced composite manufacturing accessible to innovators everywhere.
Because at Mach 2, there's no room for compromise.
Ideate | Innovate | Automate