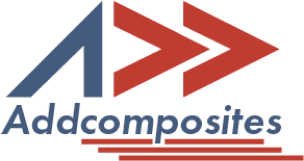
The aerospace industry has long pursued materials that offer high strength and stiffness at minimal weight to enhance aircraft performance and fuel efficiency. This pursuit led to the progressive replacement of traditional metallic alloys with polymer matrix composites, primarily those utilizing thermosetting resins. Landmark aircraft programs like the Boeing 787 Dreamliner and the Airbus A350 XWB exemplify this evolution, achieving airframes composed of over 50% composite materials by weight.1 These thermoset composites, typically carbon fiber reinforced polymers (CFRPs), delivered significant weight savings compared to their metallic predecessors. However, their manufacturing processes often involve complex chemical curing cycles, typically requiring large, energy-intensive autoclaves and lengthy processing times, posing challenges for achieving the high production rates demanded by modern commercial aircraft programs.2
Responding to the limitations of thermosets and the unceasing demand for improved efficiency and performance, thermoplastic composites (TPCs) have emerged as a compelling next-generation material solution for aerostructures.2 TPCs offer a unique combination of properties that address key industry drivers: the potential for significantly faster manufacturing cycles, enhanced material toughness and damage tolerance, inherent recyclability aligning with sustainability goals, and, crucially, the ability to be joined using welding techniques.2 Initially confined to smaller, non-critical components, TPCs are now being aggressively developed and implemented for larger, more complex, and structurally demanding applications, signaling a potential paradigm shift in aerostructure design and manufacturing.15
The drive towards TPCs reflects more than just material substitution; it embodies a fundamental shift in manufacturing philosophy. The aerospace industry faces mounting pressure to increase production rates, particularly for high-volume single-aisle aircraft, and to enable the rapid, cost-effective manufacture of vehicles for emerging markets like Urban Air Mobility (UAM) and Electric Vertical Takeoff and Landing (eVTOL) aircraft.8 TPCs, with their potential for rapid, out-of-autoclave processing, high levels of automation, and integrated assembly through welding, are seen as key enablers for these future manufacturing paradigms.3 The Multi-Functional Fuselage Demonstrator (MFFD) project, for instance, explicitly targeted high-rate production capabilities (60-100 aircraft per month) achievable through TPC technologies.25
Perhaps the most transformative characteristic of TPCs in the context of aerostructures is their weldability.5 Unlike thermosets, which undergo irreversible chemical changes during curing, thermoplastics can be repeatedly softened and resolidified by applying heat. This allows components to be joined through fusion bonding or welding, creating monolithic structures by melting and fusing the polymer matrix at the interface under pressure.29 This capability presents an attractive alternative to traditional joining methods like mechanical fastening (riveting or bolting) and adhesive bonding.5 Welding can eliminate thousands of fasteners, reducing part count, saving weight, simplifying assembly, and potentially lowering manufacturing costs.4
Furthermore, the ability to weld TPCs acts as a powerful design enabler. By removing the constraints imposed by fasteners (e.g., edge distance requirements, stress concentrations around holes) and the complexities of adhesive bonding (surface preparation, cure cycles), designers can conceptualize more integrated and structurally efficient components.1 This could involve consolidating multiple parts previously joined by fasteners into a single, welded TPC assembly, leading to lighter structures and potentially smoother aerodynamic surfaces free from rivet heads.1
Several aerospace manufacturers and suppliers are at the forefront of TPC development and implementation. Companies like Daher and Kawasaki Heavy Industries (KHI), the focus of this report, are actively investing in TPC materials, processing technologies, and welding capabilities.15 Other prominent players include Collins Aerospace (which acquired Dutch Thermoplastic Composites), Spirit AeroSystems, GKN Aerospace (Fokker), and major OEMs like Airbus and Boeing, who are driving demand and collaborating on key development programs.11 This progress is supported by a wider ecosystem of material suppliers, equipment manufacturers, research institutions (like DLR, NLR, TU Delft), and collaborative initiatives such as Europe's Clean Sky/Clean Aviation program and the US-based American Aerospace Materials Manufacturing Center (AAMMC).15
This report provides a comprehensive analysis of the role of thermoplastic composites and associated welding technologies in shaping next-generation aircraft structures. It begins by defining TPCs and contrasting their properties with traditional thermosets. It then delves into the primary welding techniques – ultrasonic, induction, and resistance welding – detailing their mechanisms, advantages, limitations, and applications in aerospace. Subsequently, it examines the specific strategies, developments, and implementations of TPCs and welding at Daher and Kawasaki Heavy Industries. Finally, the report analyzes broader market dynamics, key drivers, challenges, and future trends shaping the adoption of these advanced materials and processes in the aerospace sector.
The fundamental distinction between thermoplastic and thermosetting polymers lies in their molecular structure and response to heat.7 Thermoplastics consist of long, linear or branched polymer chains held together by secondary intermolecular forces (like Van der Waals bonds).7 When heated above their glass transition temperature (Tg) or melting temperature (Tm), these chains can move relative to each other, causing the material to soften and eventually melt into a viscous liquid. Upon cooling, the chains solidify, returning the material to a solid state. This process is a physical transformation and is entirely reversible, meaning thermoplastics can be repeatedly heated, reshaped, and cooled without altering their fundamental chemical structure.3
Thermosets, in contrast, start as liquid resins or low-viscosity materials containing reactive monomers or oligomers.43 During the curing process, typically initiated by heat, catalysts, or radiation, these molecules undergo an irreversible chemical reaction, forming strong, permanent covalent cross-links between the polymer chains.7 This creates a rigid, three-dimensional network structure. Once cured, thermosets cannot be remelted or reshaped by reheating; excessive heat will cause degradation rather than softening.5 Think of a thermoplastic like butter, which can be melted and resolidified, whereas a thermoset is like a cake batter that, once baked, cannot be returned to its liquid state.
The unique characteristics of thermoplastics translate into several compelling advantages for aerospace applications, driving their increasing adoption over both traditional metals and incumbent thermoset composites:
Despite their numerous advantages, TPCs also present challenges that need to be addressed for wider adoption:
The selection of specific TPC materials depends on the application requirements, balancing performance, processability, and cost.
Table 1: Thermoplastic vs. Thermoset Composites - Key Property Comparison
Aircraft are complex assemblies of numerous structural components. Wings, fuselage sections, control surfaces, ribs, stringers, and access panels must all be securely joined to form the complete airframe. For decades, the primary methods for joining aircraft structures, including those made from thermoset composites, have been mechanical fastening (rivets and bolts) and adhesive bonding.5
However, these traditional methods present drawbacks, particularly for composite structures. Mechanical fastening requires drilling holes, which cuts reinforcing fibers, creates stress concentrations, adds weight due to the fasteners themselves, and can be a time-consuming process.4 Adhesive bonding avoids fiber damage but requires meticulous surface preparation, involves potentially long cure times for structural adhesives, adds the weight of the adhesive layer, and raises concerns about long-term durability and non-destructive inspection (NDI) of the bondline.6
The ability of thermoplastics to be remelted provides a unique opportunity for joining via fusion bonding, commonly referred to as welding.5 This process involves heating the mating surfaces of TPC components to above the polymer's melt temperature (Tm for semi-crystalline, or above Tg for amorphous), applying pressure to ensure intimate contact and consolidation, and then cooling the joint to solidify the fused polymer.5 The result is ideally a monolithic joint with no discernible interface, effectively integrating the components.5
Welding offers significant potential benefits over traditional joining methods for TPCs:
Several welding technologies have been developed and adapted for joining TPCs in aerospace applications. The most prominent methods are ultrasonic welding, induction welding, and resistance welding.5
Regardless of the specific welding technique employed, successful industrial implementation for aerospace hinges on automation and rigorous process control.5 Achieving the consistent quality, tight tolerances, and high reliability demanded for flight-critical structures requires moving beyond manual operations. Robotic systems are essential for precisely manipulating welding heads (sonotrodes, induction coils) or applying pressure platens, ensuring repeatable positioning, movement, and force application, especially over large or complex geometries.5
Equally critical is the ability to monitor and control key process parameters in real-time. This includes precise management of temperature at the interface, applied pressure, energy input (vibration amplitude/power for USW, current/frequency for IW/RW), and process duration (weld time, hold time).7 Advanced systems incorporate sensors for in-situ monitoring (e.g., displacement sensors for USW 60, thermocouples or infrared thermography for temperature 59), providing feedback for closed-loop control and quality assurance. The feasibility of achieving high-rate TPC manufacturing relies heavily on mastering the automation of these welding processes. The inherent complexity of controlling heat flow, polymer melting and consolidation, and tool interaction necessitates sophisticated robotic integration, advanced sensor technology, and robust process modeling capabilities.5 Significant investment in these areas is therefore a prerequisite for unlocking the full production potential of TPC welding in aerospace.
Post-weld quality verification is also crucial, employing non-destructive inspection (NDI) techniques like ultrasonic inspection to detect voids or disbonds, alongside destructive mechanical testing (e.g., lap shear tests, peel tests) during process development and qualification to validate joint strength and failure modes.7
Table 2: Comparison of Primary TPC Welding Technologies
The selection of the most appropriate welding technology is therefore strongly influenced by the specific requirements of the application, particularly its scale and geometry. USW's speed makes it ideal for numerous small, localized joints like attaching clips or brackets.27 RW appears to be the preferred method for large, linear structural joints demanding high integrity, such as fuselage panel assemblies or pressure bulkheads, despite the inherent challenge of the embedded heating element.30 IW strikes a balance, offering non-contact heating suitable for continuous welds on large, potentially contoured surfaces, particularly advantageous when embedding an element is undesirable, though it faces hurdles related to initial cost and process control, especially for anisotropic materials.5 This specialization suggests a future manufacturing landscape where multiple welding techniques might be employed synergistically on a single aircraft, each optimized for the specific type of joint being created.
The theoretical advantages of TPCs and welding technologies are being actively translated into practical applications by leading aerospace companies. Examining the approaches of Daher and Kawasaki Heavy Industries provides valuable insight into the current state and future direction of TPC implementation.
Daher has strategically positioned itself as a frontrunner in the industrialization of thermoplastic composites for aerospace applications.15 While maintaining expertise in traditional thermosets, the company dedicates a significant portion of its R&D efforts towards maturing TPC technologies, recognizing their potential for lighter structures, faster production, recyclability, and weldability – key attributes for next-generation aircraft.15
Daher operates a highly automated factory in Nantes, France, specialized in TPC component production, considered one of the most advanced in Europe.15 To further accelerate development, Daher launched the Shap'in innovation center near Nantes in 2022. This center focuses on maturing advanced composite technologies, particularly TPCs, and scaling them for industrial production, collaborating closely with regional partners like the IRT Jules Verne and the EMC2 cluster.17
Daher's TPC portfolio includes a growing range of components, demonstrating the material's versatility:
Daher supplies TPC parts for various established aircraft programs, including the Dassault Rafale fighter jet, Airbus commercial aircraft (A340, A350, A380, A400M), and business jets from Gulfstream and Dassault.15 They are actively developing parts using high-performance resins like PEEK and LM PAEK, often reinforced with carbon fiber.15 They have also demonstrated capability in manufacturing thick TPC structures, collaborating with Victrex on a 32mm thick laminate panel and developing components for central wing boxes.23
Central to Daher's strategy is the mastery of advanced manufacturing processes suitable for TPCs. They utilize Automated Fiber Placement (AFP), a patented "Direct Stamping®" process that accelerates production cycles, compression molding, and co-consolidation techniques.15 Automation is a key focus to achieve the high production rates required by OEMs.15
A defining element of Daher's TPC approach is its strong emphasis on welding, particularly induction welding. Following the strategic acquisition of KVE Composites Group, a Dutch specialist in induction welding, in 2019, Daher has integrated and further developed this patented technology.34 They view welding as a critical enabler for reducing weight (by up to 15% through rivet elimination), increasing production rates, and simplifying assembly.15 The successful validation of induction welding on the full-scale TBM HTP torsion box demonstrator at the Shap'in center marked a significant milestone, proving the industrial feasibility of this fastener-free assembly method for complex aerostructures.34
Daher actively participates in collaborative R&D programs to advance TPC technology. They lead the TRAMPOLINE 2 project under France's CORAC framework, focusing specifically on developing a TPC horizontal tailplane assembled using induction welding instead of riveting.15 They are also involved in the CARAC TP project to characterize TPC materials for aerospace applications and are partners in Clean Sky initiatives like Airbus's Wing of Tomorrow.16 Furthermore, Daher is implementing structured TPC recycling processes, demonstrating a commitment to the material's lifecycle sustainability.15
Kawasaki Heavy Industries possesses extensive, proven expertise in manufacturing large, complex composite aerostructures, primarily demonstrated through its role as a major partner on the Boeing 787 Dreamliner program.38 KHI is responsible for designing and manufacturing the 787's forward fuselage section – notable for being a large, one-piece barrel structure made primarily of thermoset composites – as well as the main landing gear wheel well and parts of the wing's fixed trailing edge.38
To support this large-scale production, KHI has made substantial investments in its Nagoya Works 1 facility, establishing dedicated plants (North, South, and East) equipped with state-of-the-art machinery. This includes large autoclaves for curing thermoset components, multiple AFP machines for automated material layup, automated fastening systems, large-scale trim and drill machines, and advanced ultrasonic NDI equipment.53 Their experience extends to other Boeing programs (767, 777, 777X) and partnerships with Embraer.38
While KHI's most prominent composite application to date involves thermosets processed via AFP and autoclave curing, the company is actively engaged in research and development of thermoplastic composite technologies to leverage their potential benefits.35 Recognizing the industry trend towards OoA processing and higher rates, KHI has developed a novel manufacturing method for TPCs termed "local co-consolidation".35 This OoA process is designed for fabricating complex, stiffened TPC skin panels. It utilizes precisely controlled temperature distribution in molds combined with progressive feeding of a movable lower mold against a fixed upper mold. Significantly, this method integrates the simultaneous welding of stiffeners (like stringers) to the skin panel during the skin's consolidation phase. This innovative approach aims to produce large TPC stiffened panels with shorter flow times than autoclave processes, without requiring extremely large presses, and achieving stable quality through one-shot joining.35 KHI, in partnership with JAMCO, Toray, and others, presented this technology, demonstrating its potential for fuselage skin panels.35
Further evidence of KHI's TPC research includes presentations on joining CF/PEEK materials 59, R&D efforts encompassing TPCs alongside injection molded plastics 71, and the application of composite expertise (developed partly through aerospace) to other sectors, such as the "efWING" CFRP railway bogie.74 They are also developing large hydraulic press systems suitable for molding both thermoset and thermoplastic CFRP components 72 and have been involved in research using infrared thermography to monitor the USW process.59
Compared to Daher, KHI's public disclosures (based on the provided material) place less explicit emphasis on a broad portfolio of current TPC production parts or a specific patented welding technology like induction welding. Instead, KHI appears to be leveraging its deep experience in large-scale, automated composite manufacturing (from the 787) to develop unique, highly integrated OoA manufacturing processes for large TPC structures, such as the local co-consolidation technique that inherently incorporates welding.
KHI's broader R&D activities, encompassing areas like hydrogen technology, robotics, automation, and process innovation across its diverse business segments (Aerospace, Energy, Rail, Robotics), likely provide a synergistic foundation for its future advancements in TPC manufacturing.53
Comparing Daher and KHI reveals distinct but converging strategic paths in the TPC domain. Daher has made TPC industrialization, heavily leveraging welding (especially induction via its KVE acquisition), a central pillar of its public-facing strategy, aiming to supply a diverse range of TPC components.15 KHI, building on its formidable large-structure thermoset manufacturing base, is developing innovative, integrated OoA TPC processes like local co-consolidation that combine forming and welding in a single step, targeting large panel applications.35 Both companies clearly recognize OoA processing and welding as essential technologies for future aerostructures and are investing heavily in R&D and automation.
The advancement of TPC technology is not happening in isolation. The case studies and broader research highlight the critical role of ecosystem collaboration. Daher's partnerships with research institutes (IRT Jules Verne), industry clusters (EMC2), academia, and suppliers are integral to its Shap'in center and project successes.17 KHI collaborated with multiple partners to develop its local co-consolidation process.35 Large-scale demonstrators like the MFFD involved extensive consortia including OEMs (Airbus), Tier 1 suppliers (GKN), research organizations (DLR, NLR), and universities (TU Delft).25 Initiatives like the AAMMC in the US explicitly bring together industry, government, and academia to create shared testbed facilities and accelerate technology maturation.24 This collaborative model appears essential for tackling the complex challenges of material science, process development, automation, and standardization required to industrialize TPCs for widespread aerospace use. No single entity possesses all the necessary expertise or resources; progress relies on networked innovation.
Table 3: Examples of TPC Components and Manufacturing Processes at Daher & KHI
The global market for thermoplastic composites is experiencing robust growth, driven by increasing adoption across various industries, with aerospace and automotive being key sectors. Market size estimates and growth projections vary slightly between sources, but consistently point towards a significant upward trend.
Geographically, the Asia Pacific region currently represents the largest overall market for TPCs, largely driven by its significant automotive and electronics industries.13 However, Europe holds a dominant position in the A&D thermoplastic composites market (estimated 56.1% share in 2023), fueled by Airbus's significant use of TPCs (e.g., on the A350XWB) and the presence of key Tier 1 suppliers like Daher and GKN Aerospace.11 North America is expected to see strong growth, driven by Boeing's activities, defense applications, emerging UAM/eVTOL markets, and strategic initiatives like the AAMMC Tech Hub aimed at building domestic TPC supply chains.8
Several interconnected factors are propelling the adoption of TPCs in aerospace:
Despite the positive momentum, several hurdles remain for the widespread adoption of TPCs in primary aerostructures:
The future trajectory of TPCs in aerospace appears bright, shaped by several key trends:
The aerospace industry is undergoing a significant material evolution, with thermoplastic composites poised to play an increasingly critical role in the design and manufacture of next-generation aircraft. The compelling advantages offered by TPCs – substantial weight reduction, dramatically faster manufacturing cycles, superior toughness and damage tolerance, inherent recyclability, and simplified logistics due to long shelf life – address many of the key challenges facing the sector, including the relentless drive for fuel efficiency, the need for higher production rates, and the growing imperative for environmental sustainability.3
Crucially, the ability to join TPC components using fusion bonding, or welding, represents a transformative technological leap. Techniques like ultrasonic, induction, and resistance welding offer pathways to eliminate heavy and complex mechanical fasteners and adhesives, enabling the creation of lighter, more integrated, and potentially more aerodynamically efficient structures.4 The successful automation of these welding processes is fundamental to unlocking the high-rate production potential of TPCs.
Industry leaders like Daher and Kawasaki Heavy Industries exemplify the commitment to advancing TPC technology. Daher demonstrates a strong focus on industrializing TPC production across a range of components, with a particular emphasis on leveraging patented induction welding technology as a core competency.15 KHI, building upon its extensive experience in manufacturing large-scale thermoset composite structures for the Boeing 787, is developing innovative, integrated out-of-autoclave TPC processes like local co-consolidation, which combines forming and welding to tackle large panel applications.35 While their specific approaches may differ, both companies, along with other key players like Collins Aerospace and Spirit AeroSystems, are clearly investing in TPCs and welding as foundational technologies for future aircraft.
Significant challenges undoubtedly remain. The higher initial cost of TPC materials, the need for further standardization of manufacturing and joining processes, the complexities of scaling production to very large structures at high rates, and the requirement for mature predictive modeling tools must be addressed.4 However, the pace of innovation, driven by intensive R&D, advancements in automation and digitization, and vital collaborative efforts through consortia and shared testbeds, suggests these hurdles are surmountable.24
The trajectory is clear: thermoplastic composites, enabled by sophisticated welding techniques and highly automated manufacturing systems, are set to redefine aerostructure production. This shift promises not only lighter and more fuel-efficient aircraft but also more sustainable and potentially more cost-effective manufacturing processes. The integration of these technologies represents more than just an incremental improvement; it is a key enabler for achieving the performance, production rate, and environmental goals of the next generation of flight.