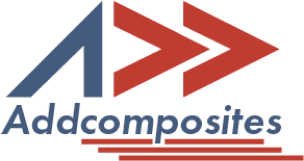
In an era marked by unprecedented volatility, supply chain resilience (SCR) has transitioned from a competitive advantage to a strategic imperative. Global disruptions, spanning geopolitical tensions, pandemics, natural disasters, and cyber threats, continually expose the vulnerabilities inherent in traditional, often elongated and complex, supply chains. Large Format Additive Manufacturing (LFAM), a subset of additive manufacturing (AM) capable of producing large-scale parts and tooling, emerges as a pivotal technology in addressing these challenges. This report provides a comprehensive analysis of how LFAM enhances supply chain resilience by enabling localized production, facilitating digital inventory management, and fostering greater manufacturing agility.
Supply chain resilience is fundamentally the ability to anticipate, withstand, adapt to, and rapidly recover from disruptions while maintaining continuity of operations. LFAM contributes significantly to this capability through several interconnected mechanisms. Firstly, it empowers localized and distributed production, allowing manufacturing to occur closer to the point of need, thereby reducing dependence on complex global logistics, shortening lead times, and mitigating risks associated with transportation and geopolitical instability. Secondly, LFAM is a key enabler of digital inventory, where physical stockpiles are replaced by secure digital design files, allowing parts (especially large tooling or spares) to be produced on-demand. This drastically cuts warehousing costs, eliminates obsolescence risk, and ensures faster access to critical components. Thirdly, LFAM enhances manufacturing agility, providing the flexibility to quickly switch production between different parts without the need for retooling, rapidly iterate designs, and scale production in response to fluctuating demand or unforeseen events.
The analysis indicates that LFAM offers tangible pathways to counter specific supply chain vulnerabilities. Applications in producing large tooling for aerospace and automotive sectors demonstrate dramatic reductions in lead times and costs. The ability to create large, monolithic parts simplifies assembly and reduces potential failure points. Furthermore, on-demand production of large spare parts using LFAM, particularly with technologies like Wire Arc Additive Manufacturing (WAAM) for metals, directly addresses inventory risks and operational downtime. However, the adoption of LFAM is not without challenges. Technological limitations related to material variety, quality control, consistency, and post-processing requirements persist. Significant capital investment, evolving material costs, and a pronounced skills gap in areas like Design for AM (DfAM) and LFAM operation present considerable hurdles.
The modern global economy operates on intricate networks of suppliers, manufacturers, distributors, and customers. While these complex supply chains have enabled unprecedented efficiency and global reach, they have also proven increasingly susceptible to a wide array of disruptions. Events ranging from natural disasters and pandemics to geopolitical conflicts and cyberattacks can trigger cascading failures, leading to significant financial losses, operational halts, reputational damage, and critical shortages. In this volatile environment, building and maintaining supply chain resilience (SCR) is no longer a niche concern but a fundamental requirement for business continuity and competitiveness.
Supply Chain Resilience (SCR) refers to the capability of a supply chain to anticipate, prepare for, respond to, adapt to, and recover from disruptions to meet customer demand and maintain operational continuity. It encompasses the ability to return to a state of equilibrium after an event causes operational results to deviate from expectations.
Key attributes underpinning SCR include:
The frequency, diversity, and impact of supply chain disruptions have intensified in recent years. Businesses face a complex and interconnected threat landscape encompassing both internal weaknesses and external shocks.
Internal Vulnerabilities often stem from operational inefficiencies or strategic choices within the organization's control:
External Vulnerabilities arise from factors largely outside an organization's direct control but can severely impact operations:
In response to the escalating complexity and frequency of disruptions, companies are increasingly turning to advanced manufacturing technologies as strategic enablers of supply chain resilience. Technologies falling under the Industry 4.0 umbrella, such as IoT, AI, Big Data analytics, and robotics, enhance visibility, automation, and data-driven decision-making. Among these, Additive Manufacturing (AM), or 3D printing, holds particular promise for fundamentally reshaping supply chain structures and mitigating traditional vulnerabilities.
AM's ability to create physical objects directly from digital designs allows for new production paradigms that directly counter traditional supply chain weaknesses. Key AM-enabled strategies for resilience include:
Within the diverse landscape of AM technologies, Large Format Additive Manufacturing (LFAM) stands out for its potential to impact supply chains dealing with large components, tooling, molds, and structures.
Additive Manufacturing (AM) is formally defined by the ISO/ASTM 52900 standard as the "process of joining materials to make parts from 3D model data, usually layer upon layer, as opposed to subtractive manufacturing and formative manufacturing methodologies." In simpler terms, AM builds three-dimensional objects by successively adding material based on a digital design, typically created using computer-aided design (CAD) software or 3D scanning. This contrasts sharply with traditional subtractive methods (like CNC machining), which remove material from a larger block, and formative methods (like injection molding or casting), which shape material using molds or dies.
The ISO/ASTM 52900 standard classifies AM technologies into seven distinct process categories based on the fundamental way material is joined:
Large Format Additive Manufacturing (LFAM), sometimes referred to as Large Scale Additive Manufacturing (LSAM), represents a significant scaling-up of AM principles to produce parts far exceeding the dimensions achievable with typical desktop or even many industrial AM systems. While there isn't a single, universally adopted standard, LFAM is generally characterized by systems with build volumes equal to or greater than one cubic meter (1m³).
A defining characteristic of LFAM, beyond sheer size, is its significantly higher material deposition rate compared to traditional AM techniques like FFF. While a standard FFF printer might extrude filament at rates below 0.5 kg/hr or even 1 kg/hr, LFAM systems are designed for throughputs that can be orders of magnitude higher, potentially reaching 36 kg/hr, 60 kg/hr, or even over 200 kg/hr (approx. 500 lbs/hr) depending on the specific technology and material.
This high throughput is often achieved by moving away from filament feedstock, which has inherent limitations in melting and extrusion speed. Instead, many LFAM systems utilize:
LFAM systems are typically implemented using either large gantry systems or robotic arms. Gantry systems, like the Cincinnati BAAM or Thermwood LSAM, offer high precision over large planar areas. Robotic systems, often mounting an extruder or welding torch on a multi-axis industrial robot, provide greater flexibility in movement.
The range of materials processable by LFAM depends heavily on the specific technology employed:
Polymer and Composite LFAM (FGF/BAAM/LSAM): These systems primarily process thermoplastics, often leveraging the cost-effectiveness of pellet feedstock used in injection molding. Common base polymers include ABS, Polycarbonate (PC), PETG, Polypropylene (PP), PLA, and high-performance polymers like PEEK.
To enhance mechanical properties and thermal stability, these base polymers are frequently reinforced with short fibers:
Metal LFAM (WAAM): WAAM utilizes standard welding wire feedstock, offering a wide range of established metal alloys:
While LFAM dramatically increases the scale achievable with AM, this often comes at the cost of resolution and surface finish. The large extrusion beads or weld deposits inherent in high-throughput LFAM processes result in rougher surfaces compared to smaller-scale AM like PBF or even FFF. Consequently, LFAM parts frequently require secondary machining operations.
Large Format Additive Manufacturing offers more than just the ability to print large objects; its core capabilities directly address several key vulnerabilities inherent in traditional supply chains.
One of the most significant impacts of LFAM on supply chain resilience stems from its ability to decouple production location from traditional constraints. Conventional manufacturing often relies on centralized, large-scale facilities, frequently located globally to leverage labor costs or specific resources.
LFAM, as a digital manufacturing technology, enables production to be shifted closer to the point of need or consumption. Instead of shipping large, bulky finished parts or tooling across continents, manufacturers can transmit digital design files electronically to LFAM systems located regionally, locally, or even on-site. This facilitates a distributed manufacturing model.
The resilience benefits of this localized/distributed approach are substantial:
This model is particularly advantageous for industries requiring large components in remote or challenging environments, such as defense (field repairs/parts), energy (offshore platforms, remote sites), or marine (parts produced at port or potentially onboard).
Traditional supply chains often rely on holding significant physical inventory to buffer against demand variability and potential supply disruptions. However, this physical inventory represents tied-up capital, incurs substantial warehousing and management costs, and carries the significant risk of obsolescence.
LFAM, combined with digital data management, enables a paradigm shift towards digital inventory or virtual warehousing. Instead of storing physical items, companies maintain a secure, managed library of digital files for their parts. When a part is needed, the digital file is retrieved and sent to an LFAM system for on-demand production.
The benefits for supply chain resilience are profound:
This approach is particularly powerful for managing inventories of spare parts and tooling, which are often characterized by unpredictable demand, long traditional lead times, and high obsolescence risk.
Beyond localization and inventory management, LFAM directly enhances the agility and flexibility of manufacturing operations, which are core components of supply chain resilience.
LFAM enhances both agility and flexibility in several ways:
This enhanced agility and flexibility translates directly into improved supply chain resilience. Companies using LFAM can react faster to sudden demand surges or drops, quickly produce replacement parts or tooling if a primary source is disrupted, adapt designs to overcome material shortages, and bring new or modified products to market faster.
Table 1: How LFAM Capabilities Address Supply Chain Vulnerabilities
Producing large tooling is often a significant bottleneck in conventional manufacturing, characterized by long lead times, high costs, and reliance on specialized suppliers. LFAM has emerged as a transformative solution in this domain.
Beyond tooling, LFAM technologies are increasingly used for producing large prototypes, functional parts, and facilitating repairs in the aerospace and defense sectors.
In the automotive industry, LFAM finds significant application in areas requiring speed, customization, and the production of large prototypes or low-volume components.
LFAM technologies are also making inroads into other sectors requiring large, often complex structures:
Table 2: LFAM Application Case Study Highlights
Despite the compelling benefits, the widespread adoption of Large Format Additive Manufacturing faces several challenges spanning technology, economics, and organizational factors.
LFAM vs. Traditional Manufacturing (CNC Machining, Injection Molding, Casting):
LFAM vs. Other AM Technologies (FFF, PBF - SLS/SLM):
Table 3: LFAM vs. Alternative Manufacturing Methods for Large Parts/Tooling
Several key technological developments are shaping the future of LFAM:
The overall Additive Manufacturing market continues to grow. According to the Wohlers Report 2025, the global AM industry reached USD $21.9 billion in 2024, reflecting 9.1% growth. Projections suggest the market could reach $115 billion by 2034.
Key market dynamics include:
The capabilities offered by LFAM are poised to significantly influence future supply chain structures:
However, the transition to fully decentralized models faces hurdles related to economics, infrastructure investment, and quality consistency, suggesting a hybrid approach may be more prevalent in the near term.
LFAM presents several potential environmental advantages:
Organizations considering LFAM to bolster supply chain resilience should adopt a measured and strategic approach:
Large Format Additive Manufacturing offers a powerful and increasingly viable technological pathway towards enhancing supply chain resilience. By fundamentally enabling shifts towards localized production, facilitating the transition to digital inventories, and providing unprecedented manufacturing agility for large parts and tooling, LFAM directly addresses many of the vulnerabilities exposed in traditional, globalized supply chains.
The ability to produce large tooling rapidly and cost-effectively reduces critical bottlenecks in industries like aerospace and automotive. On-demand manufacturing of large spare parts from digital files mitigates inventory risks and minimizes operational downtime in sectors such as energy and marine. The flexibility to quickly adapt production and designs empowers businesses to respond effectively to market volatility and unforeseen disruptions.
However, LFAM is not a panacea. Significant challenges related to technological maturity, quality control, material limitations, economic viability, post-processing requirements, and workforce skills must be carefully considered and addressed. Successful adoption requires strategic planning, targeted application selection, ecosystem collaboration, and investment in both technology and people.
The future trajectory of LFAM points towards continued improvements in speed, materials, quality assurance (driven by AI and sensors), and automation, further strengthening its value proposition. While complete decentralization may face near-term hurdles, the move towards more regionalized and digitally orchestrated supply networks leveraging LFAM is undeniable. Furthermore, the growing alignment of LFAM with sustainability objectives adds another compelling dimension to its strategic importance.
Ultimately, Large Format Additive Manufacturing provides organizations with a potent tool to not only defend against supply chain disruptions but also to build more agile, responsive, and competitive operations for the future. By strategically integrating LFAM capabilities, businesses can transform their supply chains from potential liabilities into sources of resilient competitive advantage.