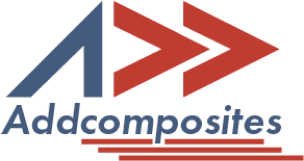
The global transition towards cleaner energy sources has placed hydrogen firmly in the spotlight.1 Recognized for its potential as a clean, high-energy fuel, hydrogen offers a pathway to decarbonize sectors like transportation and provide large-scale energy storage solutions.1 However, harnessing hydrogen's potential hinges significantly on overcoming a fundamental challenge: efficient storage. Especially for mobile applications like vehicles, hydrogen must be stored densely to provide adequate range and performance. This necessitates storing hydrogen gas at very high pressures, commonly 700 bar (over 10,000 psi), to achieve practical energy densities both by weight (gravimetric efficiency) and volume (volumetric efficiency).2
Meeting these demanding pressure requirements while minimizing weight has led manufacturers to embrace advanced composite materials. Carbon Fiber Reinforced Polymers (CFRP) have become the material of choice for high-pressure hydrogen tanks, primarily due to their exceptional strength-to-weight ratio, which far surpasses that of traditional metal tanks.3 For years, Filament Winding (FW) has been the standard manufacturing technique for producing these composite pressure vessels (CPVs), particularly the prevalent Type IV tanks.5 This established process involves winding continuous fiber strands around a liner to create the tank structure.
While FW has served the industry well, the push for even greater efficiency, lighter weights, and enhanced safety demands further innovation in manufacturing. Automated Fiber Placement (AFP) represents this next evolutionary step. AFP is a cutting-edge composite manufacturing technology offering unprecedented precision and design flexibility, poised to overcome some limitations inherent in traditional methods and unlock superior performance in hydrogen storage systems.14 This article explores how AFP technology is set to revolutionize the manufacturing of composite hydrogen tanks, delves into its specific advantages compared to filament winding, and examines how innovative solutions are enabling this transition towards next-generation hydrogen storage.
The industry classifies high-pressure hydrogen storage tanks into several types, with Type IV and Type V representing the current state-of-the-art for lightweight, high-performance applications.
Type IV tanks are currently the most common type used in applications demanding low weight, such as fuel cell electric vehicles (FCEVs).5 These tanks consist of a non-load-bearing polymer liner, typically made from high-density polyethylene (HDPE) or polyamide (PA), which acts as the primary gas barrier. This liner is then fully overwrapped with a structural composite shell, usually carbon fiber embedded in a polymer matrix.1 They are designed to operate at high pressures, commonly 700 bar, although designs up to 875 bar exist.2
The main advantages of Type IV tanks include their significantly lower weight compared to earlier types (Type I, II, and III) and their ability to store hydrogen at high densities, making them suitable for mobile applications.12 However, they also present challenges. The manufacturing process, often involving filament winding over the liner, is complex.5 Hydrogen, being the smallest molecule, can permeate through the polymer liner over time, requiring careful material selection and design considerations.18 Furthermore, the substantial amount of high-strength carbon fiber required makes these tanks relatively expensive, with carbon fiber being a major cost driver.8
Type V tanks represent the cutting edge of hydrogen storage technology, aiming for the ultimate in lightweight design by eliminating the liner altogether.7 In a Type V vessel, the all-composite structure must perform the dual role of providing structural integrity to withstand high pressures and acting as the barrier to prevent hydrogen leakage.26
The potential benefits are significant: eliminating the liner could reduce tank weight by approximately 20% compared to Type IV designs and potentially simplify the overall structure.18 However, Type V technology faces considerable hurdles. The most critical challenge is managing hydrogen permeation directly through the composite wall, as there is no dedicated liner material.7 Ensuring the composite laminate's integrity over many pressure cycles without developing micro-cracks, which could become leak paths, is paramount.27 Due to these challenges, Type V technology is still considered less mature and largely experimental compared to Type IV.7 Innovative approaches, such as the Oak Ridge National Laboratory's concept using a 3D-printed dissolvable mandrel and an internal barrier coating, aim to address these manufacturing and permeation challenges.24 The progression from Type IV to Type V clearly illustrates the drive towards lighter, more efficient storage, but highlights permeation and structural integrity as key obstacles that advanced manufacturing techniques must address.
Filament winding has long been the dominant manufacturing method for composite pressure vessels, including Type IV hydrogen tanks. Understanding its process and limitations provides context for the advantages offered by newer technologies like AFP.
The filament winding process involves winding continuous reinforcement fibers, typically carbon fiber tow, onto a rotating mandrel.13 For Type IV tanks, the polymer liner serves as the mandrel.5 The fibers can be pre-impregnated with a thermoset resin (towpreg, often termed "dry winding") or impregnated with resin during the winding process ("wet winding").5 The fibers are wound under controlled tension, and the winding angle relative to the mandrel axis is precisely controlled by coordinating the mandrel's rotation speed and the movement speed of the fiber delivery head (carriage).13 After winding, the resin is typically cured, often by heating in an oven, to consolidate the composite structure.5
Filament winding offers several advantages that have contributed to its widespread use. It is a mature, well-understood technology with a long history, providing reliability and predictability.14 For producing simple, axisymmetric shapes like cylinders and spheres, FW can be highly efficient and cost-effective, capable of high production speeds suitable for large volumes.14 The process naturally aligns fibers in tension-dominated paths, resulting in parts with excellent strength-to-weight ratios, particularly for pressure containment.14
Despite its strengths, FW faces limitations, particularly when pushing the boundaries of performance and efficiency for advanced hydrogen tanks:
Filament winding thus presents a trade-off: it offers proven reliability, speed, and lower initial costs for standard shapes but faces inherent challenges related to void formation, design optimization limitations, and material efficiency, particularly for the increasingly complex and performance-driven requirements of advanced hydrogen storage.
Automated Fiber Placement (AFP) is an advanced additive manufacturing process for composites that addresses many of the limitations of traditional methods like filament winding, offering enhanced precision, design freedom, and quality control.
In the AFP process, a robotic arm or gantry system manipulates an AFP head that precisely lays down multiple individual strips, or "tows," of composite material onto a mold or mandrel surface.14 These tows, typically 3-6 mm wide, can be thermoset or thermoplastic prepreg tapes, or dry fibers.14 The tows are fed from a creel system through the AFP head.38 A key feature is the application of heat (often via laser, infrared lamp, or hot gas) at the deposition point to ensure tackiness and promote adhesion between layers, followed immediately by pressure applied through a compaction roller.37 The entire process is driven by numerical control (NC) programs generated from CAD/CAM software, which dictate the precise path, orientation, speed, and tension for each tow.16 For thermoplastic materials, AFP can incorporate in-situ consolidation (ISC), where sufficient heat and pressure are applied during placement to fully consolidate the laminate, potentially eliminating the need for a separate autoclave cure cycle.14
Several core principles distinguish AFP:
AFP fundamentally shifts the manufacturing paradigm. Instead of the design being constrained by the manufacturing process (as often occurs with FW), AFP allows the manufacturing process to adapt to the optimal design determined by engineering analysis. This design-driven approach is key to maximizing composite performance.
When applied to the demanding requirements of high-pressure hydrogen tank manufacturing, AFP offers distinct advantages over traditional filament winding across several critical areas, including quality, design optimization, material usage, and overall performance potential.
The precision inherent in the AFP process directly translates to higher quality laminates with fewer defects. By accurately placing each tow and applying controlled heat and compaction at the point of deposition, AFP minimizes the formation of voids, gaps, overlaps, and fiber wrinkling that can plague filament-wound structures.14 The ability to control tension for each tow individually further contributes to uniform layup quality.44 Studies investigating AFP for thermoplastic composites, which require high temperatures and pressures for consolidation, have shown that optimizing process parameters like laydown speed and compaction force can achieve void contents below the critical 2% threshold.34 This contrasts favorably with the higher void ratios sometimes observed in FW tanks.5
This reduction in defects has significant implications for mechanical performance. Fewer voids mean fewer stress concentration points and a more homogenous material structure, leading to improved static strength, enhanced fatigue resistance, and greater overall durability.5 Comparative tests have shown AFP-manufactured laminates exhibiting higher tensile and compression moduli, and similar strength levels to traditionally autoclaved parts, demonstrating the high quality achievable through automated placement.47 For hydrogen tanks, where reliability and long service life under cyclic loading are critical, minimizing defects through AFP offers a substantial advantage.
Perhaps the most transformative advantage of AFP is its ability to place fibers along complex, non-geodesic paths.14 Finite Element Analysis (FEA) can precisely map the stress distribution across a pressure vessel, dictating the optimal fiber orientation at every point for maximum structural efficiency.20 Filament winding, constrained largely to geodesic trajectories, often cannot place fibers precisely along these optimal paths, especially in the geometrically complex dome ends where stresses are concentrated.14
AFP overcomes this limitation. Its tow-steering capability allows the placement head to follow the paths prescribed by FEA, precisely aligning fibers with the principal stress directions.37 This enables engineers to tailor the laminate structure with unprecedented accuracy, reinforcing high-stress areas while minimizing material in lower-stress regions.10 This design freedom moves beyond the geometric constraints of FW, allowing for truly performance-driven designs that maximize strength and minimize weight, pushing the boundaries of what's possible in pressure vessel efficiency.10
The precision of AFP not only enhances performance but also improves material efficiency. By placing material only where structurally required and minimizing overlaps or unnecessary buildup, AFP significantly reduces material scrap compared to FW, particularly when manufacturing complex shapes or highly optimized layups.14 Documented cases comparing AFP combined with hand layup to a mix of filament winding and hand layup have shown dramatic reductions in material wastage, for instance, from 62% down to 6%.37
This reduction in material consumption directly impacts cost, especially critical given that high-strength carbon fiber constitutes the largest portion of the cost for Type IV and Type V hydrogen tanks.8 Projects exploring hybrid manufacturing approaches, using FW for the cylindrical sections and AFP for the complex domes, have demonstrated the potential for significant composite material savings (e.g., 32% reported in one DOE-funded project) and corresponding cost reductions (e.g., 20% in the same project).10 While AFP systems require a higher initial capital investment compared to FW equipment 14, the long-term economic benefits derived from substantial material savings, reduced labor costs due to automation, potentially higher part quality leading to less rework, and the ability to produce higher-performance, lighter-weight parts often justify the initial expense.14 The hybrid AFP/FW approach presents a particularly compelling pathway, leveraging the speed and cost-effectiveness of FW on simple geometries and the precision and optimization capability of AFP on complex features like domes, potentially lowering the barrier for adopting optimized designs.10
The advantages in quality, design freedom, and material efficiency collectively contribute to superior performance characteristics for AFP-manufactured hydrogen tanks compared to those made solely with traditional FW.
The high degree of automation inherent in AFP offers significant benefits beyond part quality. It drastically reduces the reliance on manual labor compared to hand layup or even semi-automated FW processes, leading to lower labor costs and increased throughput.14 More importantly, automation ensures high levels of repeatability and consistency from part to part, which is crucial for quality assurance and certification,
especially in safety-critical applications like hydrogen storage. As the demand for hydrogen vehicles and storage solutions grows, the scalability offered by automated processes like AFP will be essential to meet projected production volumes, such as the 500,000 units per year target mentioned in relation to DOE cost goals.10
Navigating the transition to advanced composite manufacturing techniques like AFP requires capable tools and expertise. Addcomposites provides an ecosystem designed to facilitate the adoption and optimization of these processes for applications such as high-performance hydrogen tanks.
A cornerstone of the Addcomposites offering is the AddPath software platform.36 Uniquely, AddPath is designed to program, simulate, and control both AFP and Filament Winding operations, often using the same robotic hardware.36 This integrated approach offers significant flexibility. Manufacturers can leverage existing robotic systems for multiple tasks, seamlessly switch between AFP and FW modes, or even implement hybrid manufacturing strategies that combine the strengths of both techniques on a single part.10 AddPath provides sophisticated tools for path planning, pattern definition, kinematic simulation, collision detection, and process optimization for both filament winding (including complex dome winding and pattern control) and tape placement (handling complex geometries and non-geodesic paths).36 This unified software environment simplifies the adoption of advanced methods, breaking down traditional barriers between different manufacturing technologies. It effectively democratizes access to advanced programming capabilities that were often proprietary or tied to specific hardware vendors 43, allowing companies to utilize standard industrial robots 49 and enabling greater flexibility, experimentation, and cost-effectiveness in process development.
AddPath incorporates specific functionalities highly relevant to optimizing hydrogen tank production. Its capabilities include modules for continuous winding on cylindrical tanks with integrated dome geometries 57, enabling the precise layup required for these common pressure vessel forms. Crucially, when used with an AFP head, AddPath allows for selective reinforcement – the ability to cut and restart tows mid-process to add localized patches of material exactly where needed for strength or repair.49 Furthermore, the software supports non-geodesic winding paths when operating in AFP mode, allowing fiber placement strategies that minimize material buildup on dome ends and achieve more uniform thickness and optimized stress distribution.49 AddPath is designed to work with a wide range of materials, including thermoset and thermoplastic towpregs, as well as dry fibers for subsequent infusion processes.36 This material versatility, combined with advanced path control, empowers manufacturers to explore innovative designs and materials for next-generation tanks. Addcomposites also offers complementary hardware, such as the AFP-XS system, which integrates seamlessly with AddPath to provide a complete, accessible AFP and advanced winding solution.44 The strategic focus is not just on promoting AFP, but on providing the tools and flexibility needed to select and implement the optimal manufacturing process—be it AFP, advanced FW, or a hybrid combination—for any given hydrogen storage application.
The journey towards efficient and widespread hydrogen utilization relies heavily on advancements in storage technology. Composite pressure vessels are key, and Automated Fiber Placement stands out as a pivotal manufacturing technology capable of delivering the next generation of lighter, stronger, and more reliable hydrogen tanks. Compared to traditional filament winding, AFP offers demonstrable advantages in laminate quality through reduced void content, greater design freedom via non-geodesic path capabilities leading to optimized structures, improved material efficiency crucial for cost reduction, and enhanced overall performance. These attributes make AFP particularly enabling for the development of challenging technologies like linerless Type V tanks.
Realizing the full potential of advanced manufacturing processes like AFP and sophisticated filament winding requires powerful, accessible software tools. Platforms like AddPath play a crucial role by unifying process planning, simulation, and control for both AFP and FW, empowering manufacturers with the flexibility and capability needed to innovate. By enabling precise control over fiber placement, supporting hybrid approaches, and working with diverse materials, such tools lower the barrier to entry and accelerate the development cycle for optimized hydrogen storage solutions.
For early adopters in the hydrogen sector seeking to push the performance envelope of their storage systems, exploring the capabilities of AFP is paramount. The potential for lighter weights, improved structural integrity, enhanced durability, and greater design flexibility offers a clear path towards more competitive and efficient hydrogen solutions.
Ready to revolutionize your hydrogen tank manufacturing? Contact the Addcomposites team today to discuss your specific needs and learn how AFP systems and the versatile AddPath software can elevate your production. Request your free license of AddPath for filament winding and tape placement to start exploring the possibilities!