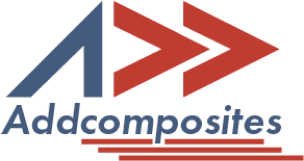
During my years at ISRO, I witnessed firsthand how advanced composite materials could push the boundaries of what's possible in extreme environments. Today, I'm excited to share how these same materials are revolutionizing a technology much closer to Earth – high-speed electric motors. The humble carbon fiber sleeve, often overlooked in discussions about electric vehicle innovation, is quietly enabling a new generation of motors that operate at speeds once thought impossible.
Let me paint you a picture of the forces at play. When a motor rotor spins at 20,000 RPM – now common in modern electric vehicles – every component experiences centrifugal forces that follow a quadratic relationship with speed. Double the RPM, and you quadruple the forces trying to tear the rotor apart.
The equation is deceptively simple: F = mω²r
But the implications are profound. At these speeds, the permanent magnets in surface-mounted motors – typically made from brittle rare-earth materials like neodymium-iron-boron (NdFeB) – experience tensile stresses they simply cannot withstand. With tensile strengths around 74 MPa, these ceramic-like materials would literally explode outward without proper containment.
Consider this: at 30,000 RPM, a magnet just 50mm from the rotation axis experiences forces exceeding 500 times gravity. Without containment, catastrophic failure isn't a possibility – it's a certainty.
The stress distribution in the sleeve follows thick-walled cylinder theory, where the hoop stress (σ_θ) is the dominant component. For a rotating sleeve, this stress is approximately:
σ_θ = ρω²(r_o² + r_i²)/2
Where ρ is density, ω is angular velocity, and r_o, r_i are the outer and inner radii. This reveals why material density becomes critical – it directly multiplies with the square of speed.
Historically, engineers turned to high-strength metallic sleeves made from materials like Inconel 718, titanium alloys, or specialized stainless steels. These materials offered the necessary strength and were well-understood from decades of aerospace applications.
But here's where the story gets interesting – and where my experience in satellite design becomes relevant. In space applications, every gram matters, and we learned that strength alone isn't the complete answer. The metal sleeves that seemed like the obvious solution carried hidden penalties that only became apparent when pushing the performance envelope.
Let's dive into the numbers. Inconel 718, a superalloy champion, offers:
That electrical conductivity becomes a massive problem. When rotating through the motor's magnetic field harmonics – caused by slot effects, PWM switching, and field variations – the conductive sleeve generates eddy currents. The power loss follows:
P_eddy = π²t²f²B²l²/6ρ_e
Where t is sleeve thickness, f is frequency, B is flux density, l is length, and ρ_e is electrical resistivity. For a typical high-speed motor, this translates to 300-700W of pure heat generation.
Carbon fiber composite sleeves represent a fundamental shift in how we approach rotor containment. Let me break down why this material is revolutionary:
Carbon fiber sleeves are 50% lighter than aluminum and up to 75% lighter than steel alternatives. But the real story isn't just about weight – it's about where that weight sits. In a high-speed rotor, the sleeve must contain not only the magnets but also itself. A heavy metal sleeve generates substantial self-induced stress, consuming much of its own strength just to stay together.
With a density of just 1.55-1.64 g/cm³ compared to steel's 7.85 g/cm³, carbon fiber dedicates more of its strength to actually containing the magnets rather than fighting against its own mass.
The specific strength (strength/density) comparison is striking:
Modern carbon fibers achieve tensile strengths of 2,000-3,000 MPa – nearly triple that of high-performance Inconel alloys. But unlike metals, this strength can be precisely oriented. Through careful fiber placement, we can align the strength exactly where it's needed: in the circumferential (hoop) direction to resist centrifugal forces.
The anisotropic nature of composites becomes an advantage here. By using high-angle helical winding (typically 85-89°), we can achieve:
This is where advanced manufacturing techniques become crucial. At Addcomposites, we've seen how our AFP-XS system enables manufacturers to achieve fiber orientations within ±1 degree, maximizing the strength utilization of every fiber. The tension control during winding is critical – we typically apply 50-70% of the fiber's ultimate tensile strength during winding to create compressive prestress on the magnets.
Here's where carbon fiber truly shines – or rather, doesn't. While metallic sleeves are electrical conductors, carbon fiber composites have extremely low electrical conductivity. This "electromagnetic transparency" eliminates a major source of motor inefficiency: eddy current losses.
The electrical conductivity comparison tells the story:
When a conductive metal sleeve rotates through the motor's fluctuating magnetic fields, it generates circular currents that produce heat and sap efficiency. Studies have shown these losses can reach 600-700 watts in high-speed motors with metallic sleeves. Carbon fiber? Near-zero eddy current losses.
But there's a trade-off: carbon fiber's thermal conductivity is also low (~0.7-7 W/m·K transverse), compared to metals (16-25 W/m·K). This means heat generated in the magnets can't easily escape radially. However, the massive reduction in heat generation more than compensates for this limitation.
The challenge with carbon fiber sleeves has never been about material properties – it's been about manufacturing. Traditional composite manufacturing methods were either too slow, too expensive, or unable to achieve the precision required for motor applications.
Creating effective carbon fiber sleeves requires applying tremendous pre-stress during manufacturing. This compressive load on the magnets must be carefully calculated to ensure:
The pre-stress calculation involves solving coupled equations:
σ_prestress = σ_centrifugal(max_speed) + σ_thermal(ΔT) + safety_margin
Typical values range from 50-150 MPa of compressive stress on the magnets.
High-tension filament winding and automated fiber placement (AFP) can now produce sleeves with:
What excites me most is how accessible this technology has become. When I worked on satellite components at ISRO, AFP systems cost millions and required specialized facilities. Today, our AFP-XS system brings this same capability to manufacturers for the price of a luxury car, with systems that can switch between sleeve winding and complex 3D surface placement in minutes.
The manufacturing parameters are critical:
Let's look at what carbon fiber sleeves enable in practice:
Tesla's Carbon-Wrapped Motor: Achieves 20,000+ RPM with a sleeve thickness of just 2.5mm, enabling an air gap reduction of 50% compared to their previous metal-sleeved design. The result? 5% higher power density and 2% better efficiency.
Formula E Racing Motors: Spinning at 30,000 RPM, these motors use carbon sleeves with integrated cooling channels made possible by combining AFP with our SCF3D continuous fiber 3D printing. Temperature reduction: 40°C at peak power.
Industrial Drone Motors: Achieving 50,000 RPM with sleeve weight of just 15 grams. The entire rotor assembly weighs less than a smartphone.
The real revolution isn't just in the material – it's in making this technology accessible. Just as SpaceX democratized access to space, we need to democratize access to advanced composite manufacturing.
Modern manufacturing cells combining continuous fiber 3D printing with traditional AFP can produce complex motor components that were impossible just five years ago:
The numbers tell the story:
As someone who's witnessed the transformation of impossible-to-access space technology into democratized manufacturing tools, I'm convinced that carbon fiber motor sleeves represent more than just a material substitution. They're a glimpse into a future where advanced materials and accessible manufacturing converge to enable previously impossible performance.
The beauty of modern composite manufacturing is that you don't need to invest millions to begin. At Addcomposites, we've structured our offerings to match your journey:
Ready to revolutionize your motor design? Whether you're looking to produce carbon fiber sleeves for 50,000 RPM drone motors or 20,000 RPM EV motors, we have the tools and expertise to make it happen.
Start with a free consultation to discuss your application, or download our motor sleeve design guide to dive deeper into the technical details. For those ready to take the leap, our AFP-XS rental program gets you manufacturing in weeks, not years.
The next time you see an electric vehicle silently accelerating with breathtaking speed, remember that this performance is enabled by a thin layer of carefully placed carbon fibers, spinning at speeds that would have been engineering fantasy just a decade ago.
The revolution isn't coming – it's already spinning at 20,000 RPM. The question is: will you be part of it?
Want to see these systems in action? Schedule a live demo or visit our applications lab in Finland to witness the future of composite manufacturing firsthand.