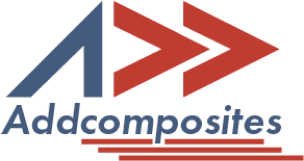
When most engineers think of carbon fiber motor sleeves, their minds immediately jump to electric vehicles—and for good reason. Tesla's groundbreaking "carbon-wrapped" motor has captured imaginations worldwide, demonstrating how composite sleeves can push motor speeds beyond 20,000 RPM while maintaining structural integrity. But as someone who spent years developing composite components for satellites at ISRO before founding Addcomposites, I've witnessed firsthand how this technology's impact extends far beyond the automotive sector.
Carbon fiber composite sleeves have quietly revolutionized high-speed rotating machinery across multiple industries, each with unique challenges that demand the exceptional properties only advanced composites can deliver. Let's explore five industries where this technology is enabling previously impossible innovations.
In aerospace applications, every gram matters. When developing gas turbine engines capable of operating at speeds exceeding 80,000 RPM, traditional metallic containment solutions simply can't compete. Carbon fiber composite sleeves offer a compelling advantage: they're 50% lighter than aluminum alternatives while providing 2-5 times the specific strength.
The real game-changer lies in their electromagnetic transparency. Unlike Inconel or titanium sleeves that generate significant eddy current losses—sometimes exceeding 680W in high-speed applications—carbon fiber sleeves virtually eliminate these parasitic losses. This means more efficient operation at altitude, where every watt counts.
But here's where it gets really interesting from a materials perspective. We're working with carbon fibers that have tensile strengths reaching 2,420 MPa while maintaining densities as low as 1.52 g/cm³. The manufacturing process involves transforming polyacrylonitrile (PAN) fibers through pre-oxidation at temperatures below 300°C, followed by carbonization in an inert environment at 1,000-1,500°C. For the highest modulus applications, we push into graphitization at 2,000-3,000°C.
For next-generation turbofan engines requiring operational temperatures of 150-200°C, advanced carbon fiber sleeves with hybrid thermoset resins demonstrate 30% better thermal stability than earlier iterations. The anisotropic thermal conductivity of carbon fiber—with axial conductivity reaching 600-1,300 W/(m·K)—actually exceeds copper's 401 W/(m·K) when properly oriented. This thermal resilience, combined with their inherent vibration damping properties (up to 10 times better than steel), makes them indispensable for aerospace applications where failure is not an option.
At Addcomposites, our AFP-XS system enables aerospace manufacturers to produce these critical components with the precision required for flight-certified applications, while our PathPilot software ensures optimal fiber placement for maximum strength-to-weight ratios.
Perhaps no application pushes the boundaries of material science quite like flywheel energy storage systems (FESS). Here, carbon fiber sleeves aren't just advantageous—they're the enabling technology that makes modern grid-scale energy storage possible.
Consider Beacon Power's 20 MW facility in New York, where 200 individual flywheel units provide critical grid frequency regulation. At the heart of each unit spins a carbon fiber composite rim at 16,000 RPM, storing kinetic energy with minimal losses. But that's just the beginning. Advanced research facilities are now testing systems approaching 100,000 RPM, where surface speeds can reach Mach 2.
The physics are unforgiving: kinetic energy increases with the square of rotational speed (E = ½Iω²), making higher speeds exponentially more valuable. Carbon fiber's tensile strength of up to 3,500 MPa enables these extreme speeds while maintaining safety factors impossible with metallic alternatives. The centrifugal force at 100,000 RPM generates stresses that would tear apart any metal sleeve—we're talking about forces where Fc = mω²r creates material stresses exceeding 1,000 MPa in the hoop direction.
What's fascinating is how we achieve the necessary pre-stress through high-tension filament winding. By applying fiber tension up to 95% of the tensile failure limit during manufacturing, we create compressive pre-stress levels around 100 MPa on the rotor assembly. This pre-stress must balance three major stress components during operation: the initial pre-stress itself, thermal expansion stresses (which can add another 50-75 MPa), and the centrifugal loads.
When these systems do reach their limits, carbon fiber's gradual failure mode—progressing from inter-fiber cracks to controlled delamination—provides predictable, manageable failure patterns rather than catastrophic rupture. The failure typically initiates with matrix cracking at about 60% of ultimate load, followed by fiber-matrix debonding, before final fiber breakage.
In medical applications, carbon fiber motor sleeves enable a unique combination of performance characteristics essential for both patient safety and clinical efficacy. High-speed surgical drills and bone saws benefit from carbon fiber's exceptional strength-to-weight ratio, reducing surgeon fatigue during lengthy procedures while maintaining the precision required for delicate operations.
But the advantages extend beyond ergonomics. Carbon fiber's radiolucency—its transparency to X-rays—proves invaluable for equipment used alongside medical imaging. Unlike metallic sleeves that create artifacts in CT or MRI scans, carbon fiber remains invisible, allowing real-time imaging guidance during procedures.
Ultra-high-speed medical centrifuges, some exceeding 100,000 RPM for specialized separation processes, rely on carbon fiber sleeves to achieve the necessary g-forces while maintaining compact footprints suitable for laboratory environments. The material's chemical inertness and ability to withstand repeated autoclave sterilization cycles make it ideal for maintaining strict medical hygiene standards.
Our AddPath software's specialized winding patterns have been adapted by medical device manufacturers to create sleeves with variable stiffness zones, optimizing both performance and safety in these life-critical applications.
Modern manufacturing demands ever-increasing precision and speed. In high-speed CNC machining, where spindle speeds routinely exceed 80,000 RPM—and can reach 100,000 RPM for micro-machining applications—carbon fiber sleeves have become the standard for premium spindle designs.
The challenge in these applications isn't just speed; it's maintaining micron-level precision while spinning at these extreme velocities. Carbon fiber's exceptionally low coefficient of thermal expansion (CTE), which can even be negative along the fiber direction (-1 to +8 × 10⁻⁶/K), provides dimensional stability that metallic sleeves simply cannot match. Compare this to stainless steel's CTE of 17 × 10⁻⁶/K, and you understand why carbon fiber is revolutionary for precision applications.
The numbers tell the story: at 80,000 RPM with a 40mm diameter spindle, the surface velocity reaches 167 m/s. The centrifugal acceleration at the sleeve surface exceeds 140,000 g. Under these conditions, a steel sleeve would experience radial growth of 15-20 microns—enough to destroy precision bearings. Carbon fiber sleeves limit this growth to under 3 microns.
Furthermore, carbon fiber's superior damping characteristics—with a loss factor around 0.02 compared to steel's 0.001—significantly reduce chatter and vibration. For manufacturers working with difficult-to-machine materials like titanium or Inconel, this vibration reduction can mean the difference between scrapped parts and profitable production. The natural frequency of a carbon fiber spindle shaft can be 40% higher than its steel counterpart, pushing resonance issues well above operating speeds.
Research has shown that carbon fiber spindle components can reduce thermal deformation by up to 60% compared to traditional steel designs, while simultaneously improving dynamic stiffness by 25%. This combination enables manufacturers to push the boundaries of what's possible in precision manufacturing, achieving surface finishes below 0.1 μm Ra in materials previously considered unmachineable at high speeds.
The automotive industry's push toward electrification has created an unexpected application for carbon fiber motor sleeves: electric turbochargers (e-turbos). These systems eliminate traditional turbo lag by using high-speed electric motors to spool the compressor independently of exhaust gas flow.
Operating speeds in e-turbos can exceed 100,000 RPM, with some advanced designs pushing toward 200,000 RPM. At these speeds, the centrifugal forces are immense—increasing with the square of angular velocity. Carbon fiber sleeves enable these extreme speeds while adding minimal inertia to the system, preserving the instant response that makes e-turbos valuable.
The electromagnetic benefits prove equally important here. The low electrical conductivity of carbon fiber minimizes losses from the high-frequency magnetic fields generated by the motor's rapid switching. This efficiency gain becomes crucial in 48V mild-hybrid systems where every watt must be carefully managed.
Our automated fiber placement technology, originally developed for aerospace applications, has been adapted by leading turbocharger manufacturers to produce sleeves with optimized fiber orientations that balance hoop strength with thermal management requirements.
As we look ahead, the convergence of manufacturing automation and materials science promises even greater possibilities. Thermoplastic carbon fiber systems, processable at room temperature, eliminate the risk of demagnetizing permanent magnets during sleeve installation. In-situ consolidation techniques enabled by modern AFP systems can reduce production times from hours to minutes, making carbon fiber sleeves economically viable for broader applications.
The key to unlocking these opportunities lies not in viewing carbon fiber as a simple replacement for metal, but in embracing a holistic design approach. Each application demands careful consideration of electromagnetic properties, thermal management, and mechanical loads. Success requires deep collaboration between motor designers and composite manufacturing specialists from the earliest design stages.
At Addcomposites, we've seen this transformation firsthand. From our origins in making space technology accessible, we've witnessed how democratizing advanced manufacturing capabilities enables innovation across industries. Whether it's our plug-and-play AFP-XS system bringing aerospace-grade precision to emerging applications or our digital twin capabilities in AddPath optimizing designs before the first fiber is placed, the goal remains constant: making the impossible possible.
The five industries explored here represent just the beginning. As carbon fiber sleeve technology continues to mature and manufacturing costs decrease through automation and scale, we anticipate applications we haven't yet imagined. The only certainty is that wherever extreme speeds, electromagnetic efficiency, and reliability converge, carbon fiber composite sleeves will play a crucial role in pushing the boundaries of what's achievable.
Whether you're pushing the boundaries in aerospace, energy storage, medical devices, or industrial automation, Addcomposites has the complete ecosystem to bring your carbon fiber sleeve designs to life.
Start Your Journey with Multiple Entry Points:
🔧 For Prototyping & R&D: Begin with our AddPath simulation software to optimize your fiber paths and winding patterns before committing to hardware. Our digital twin capabilities let you perfect your design virtually, saving time and material costs.
🏭 For Production: Access our complete suite of manufacturing solutions under one roof:
💡 Flexible Engagement Models:
Our systems can process both thermoset and thermoplastic composites, with special capabilities for high-temperature thermoplastics like PEEK and PEI that enable room-temperature processing—critical for maintaining magnet integrity.
The Addcomposites Advantage: Unlike traditional AFP systems that cost millions and require massive infrastructure, our plug-and-play solutions democratize access to advanced composite manufacturing. We've taken the technology that was once exclusive to aerospace giants and made it accessible to innovators everywhere.
📞 Connect with our engineering team to discuss your specific requirements. Whether you need to achieve 100,000 RPM, minimize eddy current losses, or solve a unique thermal management challenge, we'll help you design and manufacture the optimal solution.
From ISRO to your workshop—making the impossible possible, one fiber at a time.