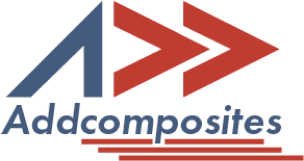
A groundbreaking new method for the additive manufacturing of carbon fiber-reinforced thermoset composites promises to revolutionize how we produce lightweight structural materials. Researchers at Colorado State University and Arizona State University have developed a technique that could dramatically reduce manufacturing time, eliminate the need for expensive tooling, and open new possibilities for complex designs in aerospace, automotive, and energy applications.
Fiber-reinforced polymer composites (FRPCs) are in high demand across multiple industries for their exceptional strength-to-weight ratio. However, traditional manufacturing methods have remained stubbornly inefficient—requiring expensive tooling, energy-intensive processing, and lengthy production times that can limit design complexity and drive up costs.
The new technique, described in a recent Nature Communications article, leverages a thermoresponsive thermoset resin as the matrix and uses localized, remote heating of carbon fiber reinforcements through photothermal conversion to enable rapid, in-situ curing without further post-processing.
"Despite the increasing use of fiber-reinforced polymer composites across multiple industries for the development of lightweight structures, the conventional manufacturing methods for composites still remain lengthy, inflexible, labor-intensive, energy-inefficient, and cost-prohibitive," notes the research team.
Figure 1: Revolutionary Photothermal Printing Process. This schematic illustrates how the blue laser beam precisely heats carbon fibers to rapidly cure the surrounding resin, enabling immediate solidification of the printed composite material without external heating or post-processing steps.
The innovation combines two key elements:
For discontinuous fiber composites, the team used Direct Ink Writing (DIW) to extrude composite inks through a printing nozzle, followed by in-situ photothermal curing. Printable inks with shear-thinning behavior were prepared by partially curing the DCPD resin to create a viscoelastic gel with 15 vol% milled carbon fibers.
Figure 2: Real-Time Printing and Thermal Curing. Left: Digital image showing a composite filament being printed in mid-air without support structures. Right: Infrared thermal imaging reveals the precise localized heating (bright spot) as the laser cures the material instantly upon deposition, reaching temperatures of 220-240°C in just 100-200 milliseconds.
For continuous fiber composites, the process was modified to allow controlled placement of uncured material along designated print paths, followed by immediate photothermal curing. This approach enables manufacturing with fiber volume fractions between 50-70% while maintaining minimal void content (0-1.5 vol%).
The research demonstrates several significant benefits compared to traditional and existing additive manufacturing approaches:
The mechanical performance of the additively manufactured composites was impressive. Tensile tests performed on unidirectional printed and control cast composite samples (fiber volume fraction, Vf = 51.4% for both samples) revealed similar mechanical performance, with a modulus of 106.7 ± 9.2 GPa and 110.7 ± 18.9 GPa and strength of 1.48 ± 0.10 GPa and 1.66 ± 0.15 GPa for printed and cast samples, respectively.
Figure 3: Performance Validation - No Compromise on Strength. Comparative analysis of flexural modulus and strength between 3D printed composites and traditionally manufactured controls. The data confirms that rapid photothermal curing maintains mechanical properties equivalent to conventional manufacturing methods, with printed samples achieving over 100 GPa modulus and 1.4 GPa strength.
Dynamic mechanical analysis (DMA) measurements showed similar viscoelastic behavior between in-situ and oven-cured samples, with comparable storage moduli and glass transition temperatures (Tg) ranging from 159.8°C to 163.3°C.
The researchers demonstrated several impressive applications of the technology, including freeform printing of composites between various surfaces using a 6-axis robotic arm, manufacturing a continuous 1.8-meter path across multiple substrates in just 204 seconds, and creating complex multilayer structures.
Figure 4: Defying Gravity with Precision. A high-aspect-ratio composite beam (aspect ratio = 750) printed entirely in mid-air demonstrates the technology's ability to create self-supporting structures without sagging or deformation. The beam's minimal deflection under its own weight showcases the immediate structural integrity achieved through rapid curing.
Figure 5: Multi-Surface Manufacturing Breakthrough. This sequence shows continuous composite printing across a 1.8-meter path spanning multiple substrates and mid-air sections, completed in just 204 seconds. The demonstration proves the technology's capability for large-scale, complex geometries that would be impossible with traditional manufacturing methods.
Figure 6: Complex Geometries Made Simple. Up: A sophisticated bracket structure combining freeform and layer-by-layer printing strategies, manufactured in 100 seconds using only 0.45 kJ of energy—four orders of magnitude less than conventional oven curing. Down: Curved composite parts demonstrating the design freedom enabled by eliminating traditional tooling constraints.
The approach is potentially applicable to a wide variety of thermoresponsive resins and reinforcement materials (such as aramid, glass, and basalt fibers) by selecting the appropriate electromagnetic radiation source. The authors envision the method enabling rapid and scalable manufacture of composite tooling and complex parts, repair of existing structures, and multimaterial printing of multiscale composites.
This groundbreaking research offers a promising path forward for rapid, flexible, and energy-efficient fabrication of high-performance composite structures. As the industry continues to seek ways to reduce costs and increase manufacturing efficiency while maintaining high performance, this additive manufacturing approach could represent a significant leap forward in composite manufacturing technology.