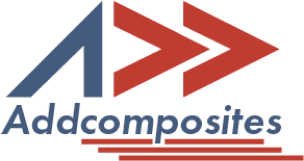
Articles, Videos, and Tutorials designed to teach you different aspects of Additive Manufacturing at your fingertips.
Get your part's production simulation with AFP - just send a part file (Non-disclosure Agreement) or request for a trial license for simulation software.
Developing a new material and would like to run the production trial with AFP?
Run a pilot production with AFP to evaluate the capability at Addcomposites facility or virtually using AddPath.
Get support for your R&D work on running new material, production strategies, applications.
We work with universities providing rentals for the duration of a semester or a student project.
We are an experienced Finnish consortium partner to work in EU funded advanced manufacturing projects.