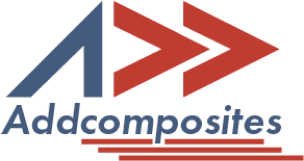
Using composites to manufacture complex products such as the load-bearing structure of an aircraft requires designers to consider specific material and fabrication limitations when creating designs. The difference between conceptual design and composite manufacturing is so great that approximately 80% of manufacturing costs are based on design decisions made at the conceptual design stage of a composite component.
The article highlights the presently conceptualized and tried approaches as mentioned below. these approaches have been designed around the provided constraints e.g. available resources, time to project, minimum failure, data gathering, analysis possibilities, etc.
The article highlights the challenges posed to composites designers. The specific nature of the problem makes the best approach indeterminate due to too many variables. The two key aspects to understanding the problem can be summarized in the two following points
The fundamentals of composites design along with a step-by-step guide for achieving a manufacturing optimized design. The key difference of the approach presented here is that it considers manufacturing and material as an integral part of the design process. below are the links to quickly jump to respective sections
The focus is on understanding the key steps in designing structural composites with examples of aerospace components; i.e. wing and fuselage.
Composite structure designs are challenging due to the wide range of design variables e.g. materials, laminates, and interactions. The use of a design tool speeds up the process and allows investigation for an optimal solution. The focus is on structural design tools at different stages of the design process.
The application of virtual manufacturing simulation tools ensures that composite manufacturing processes lead to high-quality and cost-effective components. The simulation tools are used over a wide range of processes to validate the design and predict material behavior at each step of the processing. A wide gamut of virtual manufacturing simulations is available for different process simulations. In this article, the focus is on the next step i.e. production simulation of composites.
The article describes a development project to evaluate the efficiency and benefits of automated fiber placement technology through the design, prototyping, and testing of composite bars. Discussions focus on the concept of “design-for-manufacturing” and provide an overview of the process going through selecting project objectives, material choices, processes and compensations, engineering and structural considerations, and the set of parts and accessories.
Using composites to manufacture complex products such as the load-bearing structure of an aircraft requires designers to consider specific material and fabrication limitations when creating designs. The difference between conceptual design and composite manufacturing is so great that approximately 80% of manufacturing costs are based on design decisions made at the conceptual design stage of a composite component.
The article highlights the presently conceptualized and tried approaches as mentioned below. these approaches have been designed around the provided constraints e.g. available resources, time to project, minimum failure, data gathering, analysis possibilities, etc.
The article highlights the challenges posed to composites designers. The specific nature of the problem makes the best approach indeterminate due to too many variables. The two key aspects to understanding the problem can be summarized in the two following points
The fundamentals of composites design along with a step-by-step guide for achieving a manufacturing optimized design. The key difference of the approach presented here is that it considers manufacturing and material as an integral part of the design process. below are the links to quickly jump to respective sections
The focus is on understanding the key steps in designing structural composites with examples of aerospace components; i.e. wing and fuselage.
Composite structure designs are challenging due to the wide range of design variables e.g. materials, laminates, and interactions. The use of a design tool speeds up the process and allows investigation for an optimal solution. The focus is on structural design tools at different stages of the design process.
The application of virtual manufacturing simulation tools ensures that composite manufacturing processes lead to high-quality and cost-effective components. The simulation tools are used over a wide range of processes to validate the design and predict material behavior at each step of the processing. A wide gamut of virtual manufacturing simulations is available for different process simulations. In this article, the focus is on the next step i.e. production simulation of composites.
The article describes a development project to evaluate the efficiency and benefits of automated fiber placement technology through the design, prototyping, and testing of composite bars. Discussions focus on the concept of “design-for-manufacturing” and provide an overview of the process going through selecting project objectives, material choices, processes and compensations, engineering and structural considerations, and the set of parts and accessories.