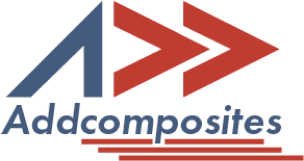
In the previous article - Software Tools for Composites Structural Designers, we focused on structural design tools used at different stages of the design process. In this blog, we will deep dive into the next step i.e. production simulation of composites.
The application of virtual manufacturing simulation tools ensures that composite manufacturing processes lead to high-quality and cost-effective components. The simulation tools are used over a wide range of processes to validate the design and predict material behavior at each step of the processing. A wide gamut of virtual manufacturing simulations is available for different process simulations.
Automated depositing of fiber tapes using Automated Fiber Placement (AFP) is increasingly being adopted by the industry. After the FEA analysis, the main outcome is fiber orientation and other selective reinforcements. In order to convert the ply data from the FEA model into an AFP program, the general flow of steps is outlined below:
FEA model is exported into a CAD format such as .step or .igs. The CAD model shape provides the surface geometry of the tool. The tooling will be used for the layup with compaction force and the curing of parts all occurring on the tool itself. Typical mold design considerations e.g. sufficient draft angles, complex geometries, or multi-piece/sacrificial tooling might be required and taken into consideration. Additionally, tension and part shrinkage can contribute to a condition known as ‘spring-in’ with cured parts, requiring an angular compensation in the tool design.
Tooling and mandrels for automated fiber placement and tape-laying processes typically are designed to provide the appropriate inner-most-loft or outer-most-loft surface. Tools and mandrels of this type may be designed to index on an automated machine-bed platform for use with AFP or ATL equipment. Any modern CAD software can be used to draw the tool CAD model with the above considerations.
A detailed article on the tool design can be found here Things to consider when Designing for ATL/AFP Manufacturing
The tooling design step from the CAD model is shown in the figure below. The tool has extended boundaries for the AFP tool runways and vacuum bagging operations. The hole has been filled up to create a continuous surface for runways within the part. The mounting feature should be considered in the tooling design e.g. in the example shown below the tooling is mounted on the rotary chuck, so an extended shaft is added for mounting onto the rotary axis. Depending on the mold manufacturing method, the rest of the details can be created accordingly.
The tooling CAD model is imported into the offline programming software (OLP) to create layup definitions in two steps i.e. Planning and Simulation.
OLP software used for AFP process workflow is presented in the figure below. The OLP Software takes the tooling CAD models as input. The first step is to define the layup area and boundary. Next, the processing parameters such as fiber orientations, runway, approach, clearance, speed, and heating intensity, are input based on your needs. Based on this information, the OLP can create motion paths for the fiber placement tool with multiple strategies.
In addition to the motion paths, there are multiple parameters e.g. tape weight (GSM), gaps, and staggering, that the engineer can choose from to configure the motion path. Typical OLP is capable of:
The generated paths will be followed by the AFP robot. While the AFP head is trying to follow the motion paths, there arise possibilities that it might hit the tooling or pass the robot singularities. In order to visualize these occurrences, robot motion simulation is evaluated either by automated analysis or by the operator to eliminate such problems. The key benefit of running the simulation in the virtual environment is avoiding costly collision and damage to the AFP head, robot, part, or tooling!
Collision detection: Essentially measuring the distances between the AFP Head and the tooling while moving over the planned motion paths, enables the detection of collision occurrences i.e. where the AFP head would physically collide or interfere with the tooling.
Collision avoidance: If a collision is detected, repositioning the mold may be able to create enough clearance for the tool. Options for repositioning the mold are: moving the mold horizontally, flipping the motion paths, editing the motion frames to increase tool angle or another similar workaround that can be identified and implemented.
Robot singularities: Using algorithms, the AFP head and robot digitally simulate the movement over the planned motion paths to detect robot singularities i.e. a configuration in which the AFP robot becomes blocked in certain directions. The OLP provides automatic detection of such positions. In order to avoid singularities repositioning the mold, flipping the motion paths could help.
The stages to reach the simulation are shown in the image below. The process of simulating your layup can be described as follows:
1. Select/define boundary and layup area
2. Define the fiber orientation and stacking sequence
3. Run a simulation to visualize anomalies within the virtual environment.
Based on balance equations of mass, momentum, energy, and species, many computer models have been developed to simulate the mold-filling process in resin transfer molding (RTM). All of these models treat the mold-filling process as the fluid flows through porous media. Darcy’s law is used to describe resin flow through fiber reinforcements. After the mold and process design such as inlet and outlet
locations, mold and resin temperature, resin flow rates or injection pressure at inlets, fiber permeability, porosity, and part geometric parameters are inputted, resin flow fronts, filling time, pressure, temperature, and conversion distributions are obtained by solving the equations. The below image shows the simulated rules that were performed and found to be matching the simulated results. [Link]
Transient heat transfer simulation established the temperature responses during
the cure cycle over the surface as well as through-the-thickness of the panel model. The degree of cure, viscosity response, and resin modulus variation during the curing cycle were computed using the cure-kinetic models of the resin. Selected heat transfer boundary conditions on the tooling surfaces allowed for heat conduction into
the prepreg material. [Link]
Are you looking for a way to automate your composite manufacturing? Sign up for a demo with Pravin Luthada or James Kuligoski via LinkedIn to learn more about our solution - virtual composite manufacturing.
Addcomposites is the provider of the Automated Fiber Placement (AFP) ecosystem - including the Fiber Placement System (AFP-XS), 3D Simulation and Programming Software (AddPath), and Robotic Cells (AddCell). With the leasing program for the AFP system (AFPnext), composites manufacturers can work with thermosets, thermoplastics, dry fiber placement, or in combination with 3D Printers on a monthly basis.
In the previous article - Software Tools for Composites Structural Designers, we focused on structural design tools used at different stages of the design process. In this blog, we will deep dive into the next step i.e. production simulation of composites.
The application of virtual manufacturing simulation tools ensures that composite manufacturing processes lead to high-quality and cost-effective components. The simulation tools are used over a wide range of processes to validate the design and predict material behavior at each step of the processing. A wide gamut of virtual manufacturing simulations is available for different process simulations.
Automated depositing of fiber tapes using Automated Fiber Placement (AFP) is increasingly being adopted by the industry. After the FEA analysis, the main outcome is fiber orientation and other selective reinforcements. In order to convert the ply data from the FEA model into an AFP program, the general flow of steps is outlined below:
FEA model is exported into a CAD format such as .step or .igs. The CAD model shape provides the surface geometry of the tool. The tooling will be used for the layup with compaction force and the curing of parts all occurring on the tool itself. Typical mold design considerations e.g. sufficient draft angles, complex geometries, or multi-piece/sacrificial tooling might be required and taken into consideration. Additionally, tension and part shrinkage can contribute to a condition known as ‘spring-in’ with cured parts, requiring an angular compensation in the tool design.
Tooling and mandrels for automated fiber placement and tape-laying processes typically are designed to provide the appropriate inner-most-loft or outer-most-loft surface. Tools and mandrels of this type may be designed to index on an automated machine-bed platform for use with AFP or ATL equipment. Any modern CAD software can be used to draw the tool CAD model with the above considerations.
A detailed article on the tool design can be found here Things to consider when Designing for ATL/AFP Manufacturing
The tooling design step from the CAD model is shown in the figure below. The tool has extended boundaries for the AFP tool runways and vacuum bagging operations. The hole has been filled up to create a continuous surface for runways within the part. The mounting feature should be considered in the tooling design e.g. in the example shown below the tooling is mounted on the rotary chuck, so an extended shaft is added for mounting onto the rotary axis. Depending on the mold manufacturing method, the rest of the details can be created accordingly.
The tooling CAD model is imported into the offline programming software (OLP) to create layup definitions in two steps i.e. Planning and Simulation.
OLP software used for AFP process workflow is presented in the figure below. The OLP Software takes the tooling CAD models as input. The first step is to define the layup area and boundary. Next, the processing parameters such as fiber orientations, runway, approach, clearance, speed, and heating intensity, are input based on your needs. Based on this information, the OLP can create motion paths for the fiber placement tool with multiple strategies.
In addition to the motion paths, there are multiple parameters e.g. tape weight (GSM), gaps, and staggering, that the engineer can choose from to configure the motion path. Typical OLP is capable of:
The generated paths will be followed by the AFP robot. While the AFP head is trying to follow the motion paths, there arise possibilities that it might hit the tooling or pass the robot singularities. In order to visualize these occurrences, robot motion simulation is evaluated either by automated analysis or by the operator to eliminate such problems. The key benefit of running the simulation in the virtual environment is avoiding costly collision and damage to the AFP head, robot, part, or tooling!
Collision detection: Essentially measuring the distances between the AFP Head and the tooling while moving over the planned motion paths, enables the detection of collision occurrences i.e. where the AFP head would physically collide or interfere with the tooling.
Collision avoidance: If a collision is detected, repositioning the mold may be able to create enough clearance for the tool. Options for repositioning the mold are: moving the mold horizontally, flipping the motion paths, editing the motion frames to increase tool angle or another similar workaround that can be identified and implemented.
Robot singularities: Using algorithms, the AFP head and robot digitally simulate the movement over the planned motion paths to detect robot singularities i.e. a configuration in which the AFP robot becomes blocked in certain directions. The OLP provides automatic detection of such positions. In order to avoid singularities repositioning the mold, flipping the motion paths could help.
The stages to reach the simulation are shown in the image below. The process of simulating your layup can be described as follows:
1. Select/define boundary and layup area
2. Define the fiber orientation and stacking sequence
3. Run a simulation to visualize anomalies within the virtual environment.
Based on balance equations of mass, momentum, energy, and species, many computer models have been developed to simulate the mold-filling process in resin transfer molding (RTM). All of these models treat the mold-filling process as the fluid flows through porous media. Darcy’s law is used to describe resin flow through fiber reinforcements. After the mold and process design such as inlet and outlet
locations, mold and resin temperature, resin flow rates or injection pressure at inlets, fiber permeability, porosity, and part geometric parameters are inputted, resin flow fronts, filling time, pressure, temperature, and conversion distributions are obtained by solving the equations. The below image shows the simulated rules that were performed and found to be matching the simulated results. [Link]
Transient heat transfer simulation established the temperature responses during
the cure cycle over the surface as well as through-the-thickness of the panel model. The degree of cure, viscosity response, and resin modulus variation during the curing cycle were computed using the cure-kinetic models of the resin. Selected heat transfer boundary conditions on the tooling surfaces allowed for heat conduction into
the prepreg material. [Link]
Are you looking for a way to automate your composite manufacturing? Sign up for a demo with Pravin Luthada or James Kuligoski via LinkedIn to learn more about our solution - virtual composite manufacturing.
Addcomposites is the provider of the Automated Fiber Placement (AFP) ecosystem - including the Fiber Placement System (AFP-XS), 3D Simulation and Programming Software (AddPath), and Robotic Cells (AddCell). With the leasing program for the AFP system (AFPnext), composites manufacturers can work with thermosets, thermoplastics, dry fiber placement, or in combination with 3D Printers on a monthly basis.