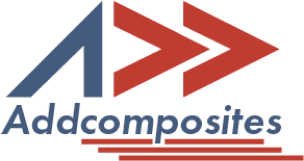
Fibers are usually circular or nearly circular and are significantly stronger in the long direction because they are normally made by either drawing or pulling during the manufacturing process. Drawing orients the molecules so that tension loads on the fibers pull more against the molecular chains themselves than against a mere entanglement of chains. Due to the strength and stiffness advantages of fibers, they are the predominant reinforcement for advanced composites. Fibers may be continuous or discontinuous, depending on the application and manufacturing process.
Before going over various types of fibers used as composite reinforcements, the major terminology used for fiber technology will be reviewed. Fibers are produced and sold in many forms
It is a benchmark specification to meet production manufacturing requirements. It is also a standard (one of many) upon which different materials are compared.
There are many different types of fibers that can be used to reinforce polymer matrix composites. The most common are carbon fibers (AS4, IM7, etc.) and fiberglass (S-glass, E-glass, etc.). As with the matrix, the fiber chosen will be determined by the end application.
Carbon fibers are conductive, have an excellent combination of high modulus and high tensile strength, have a very low (slightly negative) CTE, and offer good resistance to high temperatures.
Figure 1. Carbon Fiber Composites Examples
Carbon fibers are frequently categorized using tensile modulus. There are five categories of carbon fibers generally used in composites; low modulus, standard modulus, intermediate modulus, high modulus, and ultra-high modulus. The exact cut-off for these categories will vary depending on the reference consulted, but in general, low modulus fibers have a tensile modulus of less than 30Msi and ultra-high-modulus fibers have a tensile modulus greater than 75Msi. As a point of comparison, steel has a tensile modulus of 29Msi.
As the modulus increases, the fibers tend to get more brittle, more expensive, and harder to handle. Further, the tensile strength of the fibers generally increases as the modulus increases from low to intermediate but then tends to fall off in the high and ultra-high modulus fibers. I.e. the tensile strength of carbon fibers tends to be the greatest for the intermediate modulus fibers. For these reasons, standard and intermediate modulus fibers tend to give the best overall performance, unless the application is very stiffness oriented. This is illustrated even more clearly when fiber price and availability are also taken into consideration.
Fiberglass is, as its name implies, glass that has been spun into the form of fibers. Fiberglass is not as strong or stiff as carbon fibers, but it has characteristics that make it desirable in many applications. Fiberglass is non-conductive (i.e. an insulator) and it is generally invisible to most types of transmissions. This makes it a good choice when dealing with electrical or broadcast applications.
Figure 2. The application of fiberglass in infrastructure efficiency and sustainability (Source: CompositesWorld)
There are five major types of fiberglass.
E-glass and S-glass are, by far, the most common types found in composites. These types have good combinations of chemical resistance, mechanical properties, and insulating properties. Of the two, E-glass offers the more attractive economics, and S-glass offers better mechanical performance.
Natural fiber can be wood, sisal, hemp, coconut, cotton, kenaf, flax, jute, abaca, banana leaf fibers, bamboo, wheat straw, or other fibrous material. Natural fibers have low density, high specific properties, are biodegradable, are derived from renewable resources, have a small carbon footprint, and provide good thermal and acoustical insulation.
Figure 3. Natural Fiber Composites Application (Source: MDI)
A political/social advantage is that some products can be ‘farmed out’ to semi-skilled indigenous workers. Replacement of fiberglass with natural fiber removes the concern about the potential of lung disease caused by the former and is a move toward sustainable development.
Aramid fibers are most commonly known as Kevlar, Nomex, and Technora. Aramids are generally prepared by the reaction between an amine group and a carboxylic acid halide group (aramid); commonly this occurs when an aromatic polyamide is spun from a liquid concentration of sulfuric acid into a crystallized fiber. Fibers are then spun into larger threads in order to weave into large ropes or woven fabrics (Aramid). Aramid fibers are manufactured with varying grades based on varying qualities for strength and rigidity, so that the material can be somewhat tailored to specific design needs concerns, such as cutting the tough material during manufacture.
Each fiber mentioned above has many unique variables that must be taken into consideration when determining which to use for your project. This blog shows some examples of common products where each of the different fibers excels at.
Fibers are usually supplied in the form of rovings (glass fibers) or tows (carbon fibers). Rovings consist of straight continuous glass fiber strands or bundles of about 200 filaments; the number of strands depends on the end user, and these may be several kilometers long. Tows are likewise available in various configurations. The fibers are typically sized (coated) during production to promote wetting and adhesion, silane coupling agents being widely used for glass fibers. They may be woven into fabrics if required, including ad hoc fiber preforms for specific applications. Chopped fiber lengths range from less than 1 mm for injection to around 50 mm in randomly oriented mats for laminates.
Tow is the thread used to weave carbon fiber fabrics. As a standalone product, it can be used to make wound parts, pultrusion, or chopped for local reinforcement. A 24K tow (or strand) is composed of 24,000 individual filaments.
Tapes consist of unidirectionally aligned fiber tows pre-impregnated, prepregged for short, with a thermoset or thermoplastic resin. The resins most commonly used in aerospace and other high-performance applications are high-performance 2 part thermoset epoxies, and the following high-performance thermoplastics: polyetheretherketone (PEEK), polyetherketoneketone (PEKK), polyaryletherketone (PAEK), polyetherimide (PEI), and polyphenylene sulfide (PPS)
Two-dimensional woven products are usually offered as a 0º, 90º construction. However, bias weaves (45º, -45º) can be made by twisting the basic 0º, 90º construction. Weaves are made on a loom by interlacing two orthogonal (mutually perpendicular) sets of yarns (warp and fill). The warp direction is parallel to the length of the roll, while the fill, weft, or woof direction is perpendicular to the length of the roll. Textile looms (Fig. 2.18) produce woven cloth by separation of the warp yarns and insertion of the fill yarns. Most weaves contain similar numbers of fibers and use the same material in both the warp and fill directions.
Reinforced mats are made of either chopped strands or continuous strands lay down in a swirl pattern. Chopped strand mats are just that, mats made up of strands of glass fiber that have been chopped to shorter lengths, while continuous strand mats consist of fibers that run the full length of the mat. Mats are generally held together by resinous binders. They are used for medium-strength parts having uniform cross-sections. Both chopped and continuous-strand reinforcing mats are available in weights varying from 240 to 1430 g/m2 and in various widths. Surfacing mats, or veils, are thin, lightweight materials used in conjunction with reinforcing mats and fabrics to provide a good surface finish.
Prepregs are composite materials in which a reinforcement fiber is pre-impregnated with a thermoplastic or thermoset resin matrix in a specific ratio. Prepregs are most commonly found in conjunction with carbon fiber, as they have unique properties stemming from the fact that they have specific heat and pressure requirements. These materials are more widely used in aerospace and other high-end industries.
Addcomposites is the provider of the Automated Fiber Placement (AFP) ecosystem - including the Fiber Placement System (AFP-XS), 3D Simulation and Programming Software (AddPath), and Robotic Cells (AddCell). With the leasing program for the AFP system (AFPnext), composites manufacturers can work with thermosets, thermoplastics, dry fiber placement, or in combination with 3D Printers on a monthly basis.
Introduction to composites materials by Tri-Dung Ngo
Fibers are usually circular or nearly circular and are significantly stronger in the long direction because they are normally made by either drawing or pulling during the manufacturing process. Drawing orients the molecules so that tension loads on the fibers pull more against the molecular chains themselves than against a mere entanglement of chains. Due to the strength and stiffness advantages of fibers, they are the predominant reinforcement for advanced composites. Fibers may be continuous or discontinuous, depending on the application and manufacturing process.
Before going over various types of fibers used as composite reinforcements, the major terminology used for fiber technology will be reviewed. Fibers are produced and sold in many forms
It is a benchmark specification to meet production manufacturing requirements. It is also a standard (one of many) upon which different materials are compared.
There are many different types of fibers that can be used to reinforce polymer matrix composites. The most common are carbon fibers (AS4, IM7, etc.) and fiberglass (S-glass, E-glass, etc.). As with the matrix, the fiber chosen will be determined by the end application.
Carbon fibers are conductive, have an excellent combination of high modulus and high tensile strength, have a very low (slightly negative) CTE, and offer good resistance to high temperatures.
Figure 1. Carbon Fiber Composites Examples
Carbon fibers are frequently categorized using tensile modulus. There are five categories of carbon fibers generally used in composites; low modulus, standard modulus, intermediate modulus, high modulus, and ultra-high modulus. The exact cut-off for these categories will vary depending on the reference consulted, but in general, low modulus fibers have a tensile modulus of less than 30Msi and ultra-high-modulus fibers have a tensile modulus greater than 75Msi. As a point of comparison, steel has a tensile modulus of 29Msi.
As the modulus increases, the fibers tend to get more brittle, more expensive, and harder to handle. Further, the tensile strength of the fibers generally increases as the modulus increases from low to intermediate but then tends to fall off in the high and ultra-high modulus fibers. I.e. the tensile strength of carbon fibers tends to be the greatest for the intermediate modulus fibers. For these reasons, standard and intermediate modulus fibers tend to give the best overall performance, unless the application is very stiffness oriented. This is illustrated even more clearly when fiber price and availability are also taken into consideration.
Fiberglass is, as its name implies, glass that has been spun into the form of fibers. Fiberglass is not as strong or stiff as carbon fibers, but it has characteristics that make it desirable in many applications. Fiberglass is non-conductive (i.e. an insulator) and it is generally invisible to most types of transmissions. This makes it a good choice when dealing with electrical or broadcast applications.
Figure 2. The application of fiberglass in infrastructure efficiency and sustainability (Source: CompositesWorld)
There are five major types of fiberglass.
E-glass and S-glass are, by far, the most common types found in composites. These types have good combinations of chemical resistance, mechanical properties, and insulating properties. Of the two, E-glass offers the more attractive economics, and S-glass offers better mechanical performance.
Natural fiber can be wood, sisal, hemp, coconut, cotton, kenaf, flax, jute, abaca, banana leaf fibers, bamboo, wheat straw, or other fibrous material. Natural fibers have low density, high specific properties, are biodegradable, are derived from renewable resources, have a small carbon footprint, and provide good thermal and acoustical insulation.
Figure 3. Natural Fiber Composites Application (Source: MDI)
A political/social advantage is that some products can be ‘farmed out’ to semi-skilled indigenous workers. Replacement of fiberglass with natural fiber removes the concern about the potential of lung disease caused by the former and is a move toward sustainable development.
Aramid fibers are most commonly known as Kevlar, Nomex, and Technora. Aramids are generally prepared by the reaction between an amine group and a carboxylic acid halide group (aramid); commonly this occurs when an aromatic polyamide is spun from a liquid concentration of sulfuric acid into a crystallized fiber. Fibers are then spun into larger threads in order to weave into large ropes or woven fabrics (Aramid). Aramid fibers are manufactured with varying grades based on varying qualities for strength and rigidity, so that the material can be somewhat tailored to specific design needs concerns, such as cutting the tough material during manufacture.
Each fiber mentioned above has many unique variables that must be taken into consideration when determining which to use for your project. This blog shows some examples of common products where each of the different fibers excels at.
Fibers are usually supplied in the form of rovings (glass fibers) or tows (carbon fibers). Rovings consist of straight continuous glass fiber strands or bundles of about 200 filaments; the number of strands depends on the end user, and these may be several kilometers long. Tows are likewise available in various configurations. The fibers are typically sized (coated) during production to promote wetting and adhesion, silane coupling agents being widely used for glass fibers. They may be woven into fabrics if required, including ad hoc fiber preforms for specific applications. Chopped fiber lengths range from less than 1 mm for injection to around 50 mm in randomly oriented mats for laminates.
Tow is the thread used to weave carbon fiber fabrics. As a standalone product, it can be used to make wound parts, pultrusion, or chopped for local reinforcement. A 24K tow (or strand) is composed of 24,000 individual filaments.
Tapes consist of unidirectionally aligned fiber tows pre-impregnated, prepregged for short, with a thermoset or thermoplastic resin. The resins most commonly used in aerospace and other high-performance applications are high-performance 2 part thermoset epoxies, and the following high-performance thermoplastics: polyetheretherketone (PEEK), polyetherketoneketone (PEKK), polyaryletherketone (PAEK), polyetherimide (PEI), and polyphenylene sulfide (PPS)
Two-dimensional woven products are usually offered as a 0º, 90º construction. However, bias weaves (45º, -45º) can be made by twisting the basic 0º, 90º construction. Weaves are made on a loom by interlacing two orthogonal (mutually perpendicular) sets of yarns (warp and fill). The warp direction is parallel to the length of the roll, while the fill, weft, or woof direction is perpendicular to the length of the roll. Textile looms (Fig. 2.18) produce woven cloth by separation of the warp yarns and insertion of the fill yarns. Most weaves contain similar numbers of fibers and use the same material in both the warp and fill directions.
Reinforced mats are made of either chopped strands or continuous strands lay down in a swirl pattern. Chopped strand mats are just that, mats made up of strands of glass fiber that have been chopped to shorter lengths, while continuous strand mats consist of fibers that run the full length of the mat. Mats are generally held together by resinous binders. They are used for medium-strength parts having uniform cross-sections. Both chopped and continuous-strand reinforcing mats are available in weights varying from 240 to 1430 g/m2 and in various widths. Surfacing mats, or veils, are thin, lightweight materials used in conjunction with reinforcing mats and fabrics to provide a good surface finish.
Prepregs are composite materials in which a reinforcement fiber is pre-impregnated with a thermoplastic or thermoset resin matrix in a specific ratio. Prepregs are most commonly found in conjunction with carbon fiber, as they have unique properties stemming from the fact that they have specific heat and pressure requirements. These materials are more widely used in aerospace and other high-end industries.
Addcomposites is the provider of the Automated Fiber Placement (AFP) ecosystem - including the Fiber Placement System (AFP-XS), 3D Simulation and Programming Software (AddPath), and Robotic Cells (AddCell). With the leasing program for the AFP system (AFPnext), composites manufacturers can work with thermosets, thermoplastics, dry fiber placement, or in combination with 3D Printers on a monthly basis.
Introduction to composites materials by Tri-Dung Ngo