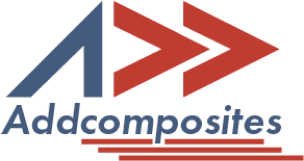
This article provides an overview of the manufacturing process of fiber-reinforced thermoplastic polymer (FRTP) composites, including traditional manufacturing processes and their limitations. The article then introduces automated fiber placement (AFP) and filament winding (FW) with in situ consolidation (ISC) and compares it with traditional manufacturing processes, highlighting the advantages of AFP and FW, including better precision in fiber orientation and reduced production times. The article also delves into the details of the AFP and FW processes, including their advantages, limitations, and improvements in technology. The in situ consolidation (ISC) process is discussed, along with factors that affect its quality, such as surface treatment, consolidation pressure, and temperature. Finally, the article explains modeling crystallization and other aspects of FRTP composite manufacturing and concludes with a summary of the key points. This article is based on a research paper titled "Review: Filament Winding and Automated Fiber Placement with In Situ Consolidation for Fiber Reinforced Thermoplastic Polymer Composites".
Jump to the right section
Fiber-reinforced thermoplastic polymer (FRTP) composites are highly valued in various industries due to their excellent specific strength and stiffness. However, traditional manufacturing methods, such as compression molding and the autoclave process, are slow and costly. To address these limitations, computer-aided manufacturing processes, including automated fiber placement (AFP) and filament winding (FW), with in situ consolidation (ISC) have been developed.
This article provides a detailed discussion on the manufacturing of FRTP composites using AFP and FW with ISC, which allows for faster and more cost-effective production of FRTP components. The article covers different modeling and simulation techniques for heat transfer and FRTP consolidation, along with various factors affecting the quality of ISC, such as surface treatment, consolidation pressure, and temperature. Additionally, advancements, limitations, and improvements in technology related to AFP and FW processes are discussed. The article concludes with a summary of optimized processing parameters from past studies and highlights the importance of these processes in the manufacturing industry.
The manufacturing of FRTP components involves three stages of heating, consolidation, and cooling. In the heating stage, the thermoplastic matrix is melted or softened to allow for bonding. Pressure is then applied during the consolidation stage to produce components with low void content. Lastly, during the cooling stage, the cooling rate is controlled to achieve the desired microstructure in the thermoplastic material.
Traditionally, the two most commonly used manufacturing processes for FRTP composites have been compression molding and the autoclave process. For the autoclave process, the FRTP preform is manually laid on a tool or positioned using automated fiber placement (AFP), and then sealed in a vacuum bag assembly. The assembly is then placed within an autoclave where heat and pressure are applied to the FRTP composite. While the autoclave process is advantageous in being able to fabricate complex and large components with consistent quality, it is difficult to automate and the convection heating involved in consolidation takes longer.
Compression molding, on the other hand, involves the use of a compression press and mold set to shape the FRTP component from a preform, which can be made by hand or using AFP. Heat is applied during the molding stage to facilitate bonding. Compression molding has the advantage of being able to produce components quickly and can be automated, but it is known to result in defects caused by wrinkles/waviness in the fiber reinforcement.
Computer aided manufacturing processes AFP and filament winding (FW) provide several benefits over traditional methods. The main advantage is the ability to achieve better precision in fiber orientation, which ultimately leads to better mechanical properties in the final product. Additionally, AFP and FW are capable of utilizing in-situ consolidation (ISC) that enables the fabrication of FRTP composite components in a single step, thus reducing production time. The automation of these processes also helps to increase productivity and reduce labor costs.
In summary, the manufacturing of FRTP components involves heating, consolidation, and cooling stages. While compression molding and the autoclave process are traditionally the most popular methods of fabrication, AFP and FW offer many advantages, including better precision in fiber orientation and ISC that enables one-step fabrication, reducing production time. Both processes have the potential to increase productivity and reduce labor costs, though further research is needed to optimize the automated manufacturing of complex FRTP composite components.
Automated Fiber Placement (AFP) is a computer-aided manufacturing process used for the fabrication of fiber-reinforced thermoplastic polymer (FRTP) composites. It involves laying down strips of FRTP prepreg tapes on a tool, usually by a robot arm equipped with a fiber placement head, and guiding the tape onto the substrate. The AFP process is controlled by a computer program to lay the FRTP prepreg tapes in the designed layup configuration. The tape is heated at the nip point by a heat source and pressed onto the substrate by a compaction roller for in situ consolidation (ISC). Finally, the tape is cut into strips of specified lengths by the cutting unit.
The AFP process offers several advantages over traditional methods such as compression molding and the autoclave process, including better precision in the fiber orientation and ISC that enables the fabrication of FRTP composite components in a single step, thus reducing production times. Advanced AFP machines allow for fiber placement speeds (or line speeds) of up to 3 m/s, which increases the productivity of the process. For the fabrication of large components, multiple tapes can be placed simultaneously.
However, one of the major issues with AFP processes is the incidence of manufacturing defects, including wrinkling and waviness in the fiber reinforcement, which can reduce the quality of the FRTP composite components. Therefore, researchers are developing strategies to improve the defect detection using online process monitoring methods such as thermographic imaging and machine learning techniques to detect and classify defects in AFP processes.
To fabricate complex FRTP composite components using AFP with ISC, researchers are optimizing the processing parameters to prevent overheating and degradation of the thermoplastic. These parameters include the size of the compaction roller, the arrangements of the feeding and cutting units, and the size of the heat source. The use of high-powered lasers and pulsed light sources for the ISC heat source enables the AFP process to be carried out at high line speeds.
In conclusion, AFP with ISC is a promising technology for the fabrication of FRTP composite components with improved fiber direction accuracy and reduced production times. However, further research is required to better understand the effects of processing parameters on the fabrication of complex shapes, and to optimize the defect detection methods to improve the quality of the FRTP composite components.
Filament winding (FW) is a manufacturing process for fiber-reinforced thermoplastic polymer (FRTP) composites that involves winding FRTP yarns or prepreg tapes onto a rotating mandrel. FW with in-situ consolidation (ISC) is carried out using a heat source and a compaction roller. FW is a continuous process where cutting the FRTP yarns or prepreg tapes is not required during winding, making it a cost-effective option for manufacturing axisymmetric FRP components such as pipes and pressure vessels.
FW has been used for decades, and recent advancements in robotics have made it possible to make non-axisymmetric components with more complex shapes. FW offers numerous advantages over traditional methods, including better precision in fiber orientation, ISC that enables fabrication in a single step, and reduced production times.
The compact Automated Fiber Placement system, AFP-XS, developed by Addcomposites, has revolutionized the manufacturing process of fiber-reinforced composites. This technology combines the functionalities of traditional Automated Fiber Placement (AFP) and filament winding (FW) into a single machine, resulting in better equipment utilization and cost-effectiveness.
Recent advancements in the software capability of the AFP-XS have further improved its performance and functionality. The added cut and restart capability allows for selective reinforcement, enabling the production of complex-shaped composite structures with reduced material waste. Additionally, the capability of fiber steering provides the ability to generate new stress-based path patterns, resulting in better load distribution and improved mechanical performance of composite structures.
These technological advancements have addressed some of the limitations of traditional filament winding and have made the AFP-XS a preferred choice for the manufacturing of composite structures. With the ability to produce complex shapes with improved mechanical properties and cost-effectiveness, the compact AFP-XS technology is becoming increasingly popular in various industries.
In situ consolidation (ISC) is a critical step in the manufacturing process of fiber-reinforced thermoplastic polymer (FRTP) composites using automated fiber placement (AFP) and filament winding (FW). Several factors affect the quality of ISC
Various modeling and simulation techniques have been developed to optimize heat transfer and FRTP consolidation. For instance, analytical solutions and numerical simulations exploiting finite difference method (FDM) have shown conduction within the tape and environment temperature are key parameters for FRTP consolidation. Some ISC heat sources include hot gas torch, infrared (IR) heater, laser, and ultrasonic welder. The choice of the ISC heat source has a significant impact on productivity, quality, and cost.
Consolidation of commingled yarns and powder impregnated materials is also important during the ISC process. Commingled yarns are created by entangling and grouping of fibers from the two different material systems. Significant effort has been put into developing and investigating consolidation techniques for commingled yarns. On the other hand, powder impregnated materials are prepared by impregnating polymer powders onto fiber materials. Consolidation of powder impregnated materials is particularly challenging since the powder particles can pose problems during compaction.
Blog provides a detailed and comprehensive analysis of the manufacturing process of fiber-reinforced thermoplastic polymer (FRTP) composites using automated fiber placement (AFP) and filament winding (FW) with in situ consolidation (ISC). The advantages of using these computerized manufacturing processes over traditional methods, such as compression molding and the autoclave process, are highlighted, including better precision in fiber orientation and reduced production time. The article also covers various modeling and simulation techniques for heat transfer and FRTP consolidation, along with factors affecting the quality of ISC, such as surface treatment, consolidation pressure, and temperature. While there is no single set of optimization parameters due to the variation in machine setup and material systems used, this blog provides a comprehensive understanding of the manufacturing and improvement of FRTP composites using AFP and FW with ISC, making it a valuable resource for anyone interested in this field.
This article provides an overview of the manufacturing process of fiber-reinforced thermoplastic polymer (FRTP) composites, including traditional manufacturing processes and their limitations. The article then introduces automated fiber placement (AFP) and filament winding (FW) with in situ consolidation (ISC) and compares it with traditional manufacturing processes, highlighting the advantages of AFP and FW, including better precision in fiber orientation and reduced production times. The article also delves into the details of the AFP and FW processes, including their advantages, limitations, and improvements in technology. The in situ consolidation (ISC) process is discussed, along with factors that affect its quality, such as surface treatment, consolidation pressure, and temperature. Finally, the article explains modeling crystallization and other aspects of FRTP composite manufacturing and concludes with a summary of the key points. This article is based on a research paper titled "Review: Filament Winding and Automated Fiber Placement with In Situ Consolidation for Fiber Reinforced Thermoplastic Polymer Composites".
Jump to the right section
Fiber-reinforced thermoplastic polymer (FRTP) composites are highly valued in various industries due to their excellent specific strength and stiffness. However, traditional manufacturing methods, such as compression molding and the autoclave process, are slow and costly. To address these limitations, computer-aided manufacturing processes, including automated fiber placement (AFP) and filament winding (FW), with in situ consolidation (ISC) have been developed.
This article provides a detailed discussion on the manufacturing of FRTP composites using AFP and FW with ISC, which allows for faster and more cost-effective production of FRTP components. The article covers different modeling and simulation techniques for heat transfer and FRTP consolidation, along with various factors affecting the quality of ISC, such as surface treatment, consolidation pressure, and temperature. Additionally, advancements, limitations, and improvements in technology related to AFP and FW processes are discussed. The article concludes with a summary of optimized processing parameters from past studies and highlights the importance of these processes in the manufacturing industry.
The manufacturing of FRTP components involves three stages of heating, consolidation, and cooling. In the heating stage, the thermoplastic matrix is melted or softened to allow for bonding. Pressure is then applied during the consolidation stage to produce components with low void content. Lastly, during the cooling stage, the cooling rate is controlled to achieve the desired microstructure in the thermoplastic material.
Traditionally, the two most commonly used manufacturing processes for FRTP composites have been compression molding and the autoclave process. For the autoclave process, the FRTP preform is manually laid on a tool or positioned using automated fiber placement (AFP), and then sealed in a vacuum bag assembly. The assembly is then placed within an autoclave where heat and pressure are applied to the FRTP composite. While the autoclave process is advantageous in being able to fabricate complex and large components with consistent quality, it is difficult to automate and the convection heating involved in consolidation takes longer.
Compression molding, on the other hand, involves the use of a compression press and mold set to shape the FRTP component from a preform, which can be made by hand or using AFP. Heat is applied during the molding stage to facilitate bonding. Compression molding has the advantage of being able to produce components quickly and can be automated, but it is known to result in defects caused by wrinkles/waviness in the fiber reinforcement.
Computer aided manufacturing processes AFP and filament winding (FW) provide several benefits over traditional methods. The main advantage is the ability to achieve better precision in fiber orientation, which ultimately leads to better mechanical properties in the final product. Additionally, AFP and FW are capable of utilizing in-situ consolidation (ISC) that enables the fabrication of FRTP composite components in a single step, thus reducing production time. The automation of these processes also helps to increase productivity and reduce labor costs.
In summary, the manufacturing of FRTP components involves heating, consolidation, and cooling stages. While compression molding and the autoclave process are traditionally the most popular methods of fabrication, AFP and FW offer many advantages, including better precision in fiber orientation and ISC that enables one-step fabrication, reducing production time. Both processes have the potential to increase productivity and reduce labor costs, though further research is needed to optimize the automated manufacturing of complex FRTP composite components.
Automated Fiber Placement (AFP) is a computer-aided manufacturing process used for the fabrication of fiber-reinforced thermoplastic polymer (FRTP) composites. It involves laying down strips of FRTP prepreg tapes on a tool, usually by a robot arm equipped with a fiber placement head, and guiding the tape onto the substrate. The AFP process is controlled by a computer program to lay the FRTP prepreg tapes in the designed layup configuration. The tape is heated at the nip point by a heat source and pressed onto the substrate by a compaction roller for in situ consolidation (ISC). Finally, the tape is cut into strips of specified lengths by the cutting unit.
The AFP process offers several advantages over traditional methods such as compression molding and the autoclave process, including better precision in the fiber orientation and ISC that enables the fabrication of FRTP composite components in a single step, thus reducing production times. Advanced AFP machines allow for fiber placement speeds (or line speeds) of up to 3 m/s, which increases the productivity of the process. For the fabrication of large components, multiple tapes can be placed simultaneously.
However, one of the major issues with AFP processes is the incidence of manufacturing defects, including wrinkling and waviness in the fiber reinforcement, which can reduce the quality of the FRTP composite components. Therefore, researchers are developing strategies to improve the defect detection using online process monitoring methods such as thermographic imaging and machine learning techniques to detect and classify defects in AFP processes.
To fabricate complex FRTP composite components using AFP with ISC, researchers are optimizing the processing parameters to prevent overheating and degradation of the thermoplastic. These parameters include the size of the compaction roller, the arrangements of the feeding and cutting units, and the size of the heat source. The use of high-powered lasers and pulsed light sources for the ISC heat source enables the AFP process to be carried out at high line speeds.
In conclusion, AFP with ISC is a promising technology for the fabrication of FRTP composite components with improved fiber direction accuracy and reduced production times. However, further research is required to better understand the effects of processing parameters on the fabrication of complex shapes, and to optimize the defect detection methods to improve the quality of the FRTP composite components.
Filament winding (FW) is a manufacturing process for fiber-reinforced thermoplastic polymer (FRTP) composites that involves winding FRTP yarns or prepreg tapes onto a rotating mandrel. FW with in-situ consolidation (ISC) is carried out using a heat source and a compaction roller. FW is a continuous process where cutting the FRTP yarns or prepreg tapes is not required during winding, making it a cost-effective option for manufacturing axisymmetric FRP components such as pipes and pressure vessels.
FW has been used for decades, and recent advancements in robotics have made it possible to make non-axisymmetric components with more complex shapes. FW offers numerous advantages over traditional methods, including better precision in fiber orientation, ISC that enables fabrication in a single step, and reduced production times.
The compact Automated Fiber Placement system, AFP-XS, developed by Addcomposites, has revolutionized the manufacturing process of fiber-reinforced composites. This technology combines the functionalities of traditional Automated Fiber Placement (AFP) and filament winding (FW) into a single machine, resulting in better equipment utilization and cost-effectiveness.
Recent advancements in the software capability of the AFP-XS have further improved its performance and functionality. The added cut and restart capability allows for selective reinforcement, enabling the production of complex-shaped composite structures with reduced material waste. Additionally, the capability of fiber steering provides the ability to generate new stress-based path patterns, resulting in better load distribution and improved mechanical performance of composite structures.
These technological advancements have addressed some of the limitations of traditional filament winding and have made the AFP-XS a preferred choice for the manufacturing of composite structures. With the ability to produce complex shapes with improved mechanical properties and cost-effectiveness, the compact AFP-XS technology is becoming increasingly popular in various industries.
In situ consolidation (ISC) is a critical step in the manufacturing process of fiber-reinforced thermoplastic polymer (FRTP) composites using automated fiber placement (AFP) and filament winding (FW). Several factors affect the quality of ISC
Various modeling and simulation techniques have been developed to optimize heat transfer and FRTP consolidation. For instance, analytical solutions and numerical simulations exploiting finite difference method (FDM) have shown conduction within the tape and environment temperature are key parameters for FRTP consolidation. Some ISC heat sources include hot gas torch, infrared (IR) heater, laser, and ultrasonic welder. The choice of the ISC heat source has a significant impact on productivity, quality, and cost.
Consolidation of commingled yarns and powder impregnated materials is also important during the ISC process. Commingled yarns are created by entangling and grouping of fibers from the two different material systems. Significant effort has been put into developing and investigating consolidation techniques for commingled yarns. On the other hand, powder impregnated materials are prepared by impregnating polymer powders onto fiber materials. Consolidation of powder impregnated materials is particularly challenging since the powder particles can pose problems during compaction.
Blog provides a detailed and comprehensive analysis of the manufacturing process of fiber-reinforced thermoplastic polymer (FRTP) composites using automated fiber placement (AFP) and filament winding (FW) with in situ consolidation (ISC). The advantages of using these computerized manufacturing processes over traditional methods, such as compression molding and the autoclave process, are highlighted, including better precision in fiber orientation and reduced production time. The article also covers various modeling and simulation techniques for heat transfer and FRTP consolidation, along with factors affecting the quality of ISC, such as surface treatment, consolidation pressure, and temperature. While there is no single set of optimization parameters due to the variation in machine setup and material systems used, this blog provides a comprehensive understanding of the manufacturing and improvement of FRTP composites using AFP and FW with ISC, making it a valuable resource for anyone interested in this field.