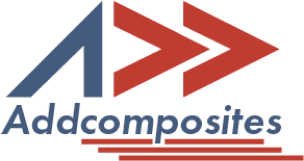
Filament winding is a sophisticated composite manufacturing process that has revolutionized the production of high-performance, lightweight structures across various industries.
Definition and Overview
Filament winding can be defined as a composite fabrication process where:
Key features:
Learn more about the fundamentals of composites manufacturing
Brief History and Development
Evolution highlights:
Explore the history of composites
Significance in Modern Manufacturing
Filament winding has become a cornerstone of composite manufacturing due to:
Key applications:
Discover the latest innovations in composite materials and their applications
As we delve deeper into the filament winding process, we'll explore its components, materials, types, and the engineering principles that make it a crucial technology in modern composite manufacturing.
The filament winding process involves several key components and steps to create high-quality composite structures. Understanding these elements is crucial for optimizing the manufacturing process and producing parts with desired properties.
A. Basic components and setup
The filament winding system typically consists of the following components:
Learn more about filament winding equipment
B. Step-by-step process description
C. Process parameters and control
Key process parameters that influence the quality and properties of the final product include:
These parameters are typically controlled through advanced CNC systems and specialized software.
The choice of materials in filament winding significantly impacts the properties and performance of the final composite structure. Two main components are considered: reinforcement fibers and matrix resins.
Fiber types
The most commonly used fibers in filament winding include:
Learn more about reinforcement fibers
Resin systems
Two main categories of resins are used in filament winding:
Explore thermoplastic and thermoset resins
Prepreg vs. wet winding
Filament winding can be performed using two main material formats:
Understand the differences between wet winding and prepreg
The selection of materials depends on factors such as desired mechanical properties, environmental conditions, production volume, and cost considerations.
Filament winding can be categorized based on the winding process and the fiber placement patterns. Understanding these types is crucial for selecting the appropriate technique for specific applications.
Winding Processes
Learn more about filament winding processes
Fiber Placement Patterns
Explore filament winding patterns and fiber stacking
Continuous vs. Interrupted Winding
The choice of winding type depends on factors such as the desired part geometry, required mechanical properties, production volume, and cost considerations.
The fiber winding pattern is a critical aspect of filament winding that significantly influences the mechanical properties and performance of the final composite structure. Understanding these patterns and the principles behind them is essential for optimizing the winding process.
Helical Winding
Polar Winding
Hoop Winding
Learn more about winding patterns
Clairaut's Relation for Geodesic Paths
Clairaut's relation is a fundamental principle in filament winding that describes the path of a fiber on a surface of revolution. It is particularly important for understanding geodesic winding paths.
Explore key design principles for filament winding
Understanding and applying these winding patterns and principles allows for the creation of optimized composite structures tailored to specific performance requirements.
The advancement of filament winding technology has been closely tied to improvements in process control and automation. These developments have led to increased precision, repeatability, and efficiency in composite manufacturing.
Evolution of Process Control in Filament Winding Machines
Learn about the evolution of automated fiber placement
Automated Filament Winding Systems
Explore automated fiber placement systems
Specific Aspects of Process Control
Understand process monitoring and AI in AFP composites manufacturing
Future Trends in Process Control and Automation
Discover the future of composites manufacturing
The continued advancement in process control and automation is driving the filament winding industry towards higher efficiency, improved quality, and the ability to produce increasingly complex composite structures.
Filament winding offers numerous benefits for composite manufacturing, but it also comes with certain limitations. Understanding these can help in determining the suitability of the process for specific applications.
Advantages of Filament Winding
Explore the advantages of filament winding
Limitations and Challenges
Understand the challenges in composites manufacturing
Understanding these advantages and limitations is crucial for determining the suitability of filament winding for specific applications and for optimizing the process to achieve the desired outcomes.
Filament winding has found widespread use across various industries due to its ability to produce high-strength, lightweight composite structures. Here are some key areas where this technology is applied:
Aerospace and Defense
Learn more about composites in aerospace
Automotive and Transportation
Explore composites in automotive applications
Oil and Gas Industry
Discover filament winding in pressure vessel manufacturing
Renewable Energy
Sports and Recreation
Industrial Applications
Explore innovations in composite materials and applications
The versatility of filament winding allows it to be adapted for a wide range of applications across these industries, often providing superior performance compared to traditional materials and manufacturing methods.
The field of filament winding is continually evolving, driven by advancements in materials science, automation, and manufacturing technologies. Here are some key trends and developments shaping the future of this technology:
Advanced Process Modeling and Simulation
Explore AI in composite manufacturing
Novel Materials and Hybrid Composites
Learn about advancements in composite materials
Integration of Sensor Technologies
Discover innovations in composite manufacturing
Additive Manufacturing Integration
Explore continuous fiber 3D printing
Expansion into New Applications
Learn about composites in urban transport
Sustainability and Circular Economy
Explore sustainable composites manufacturing
These trends indicate a future where filament winding will become more versatile, efficient, and sustainable, opening up new possibilities in composite manufacturing and expanding its application in various industries.
AddComposites. (n.d.). The Evolution of Automated Fiber Placement: Early Developments to Modern Applications. Retrieved from https://www.addcomposites.com/post/the-evolution-of-automated-fiber-placement-early-developments-to-modern-applications