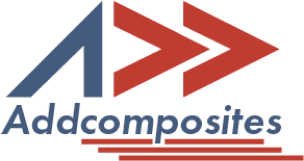
Filament winding is a manufacturing process that involves applying continuous fiber roving, impregnated with resin, onto a rotating mandrel along predetermined patterns. This process is often used to create composite structures that have high specific stiffness and strength, as well as excellent corrosion resistance. The main advantage of composites is their anisotropy, meaning they are much stronger and stiffer in the fiber direction than perpendicular to the fibers. This allows designers to tailor their designs to meet performance requirements optimally. However, the filament winding process has limited design freedom, making it difficult to approach the optimal laminate lay-up in all given geometrical scenarios.
Designing with composites involves selecting the appropriate material, defining an appropriate configuration, and finding a suitable way to manufacture it. In the case of metal components, the geometry is typically defined independently from the material, and the material only comes into play during the final dimensioning stage. With composites, however, the material must be designed along with the structure. This requires several iterations, as there are no closed formulas for designing optimal laminates. Designers have a range of tools at their disposal, from simple laminate software in the preliminary design stage to more advanced analysis techniques like finite element analysis as the design progresses.
There are several factors to consider when designing filament winding. These include the manufacturing aspects and limitations of the winding process, the design tools available, and the process parameters that can significantly impact material properties and composite performance. The key limitations of conventional filament windings to keep in mind are
Some of the key process parameters to consider include the resin compound, mixing and distribution within the composite, the required resin viscosity and its evolution during winding, the feasible and allowable temperature variations and gradients during curing, and the environmental conditions during manufacture. Additionally, the winding tension in the fiber and the fiber positioning accuracy should be taken into account.
There are several approaches to designing with filament winding, including optimizing the laminate lay-up, combining shape and lay-up optimization, and using semi-geodesic winding to increase design freedom. A standard workflow can be seen below image. The process involves providing key inputs i.e. Pressure, polar opening radius, etc to arrive at an initial fiber angle distribution in dome and hoop regions. This approach helps with designing the first draft.
As the initial design is ready, the design can be optimized in the following ways. One method of lay-up optimization involves using stress analysis to determine the ideal fiber orientations and ply thicknesses and then adapting the lay-up to meet the strength requirements while taking into account the limitations of the winding process.
Another approach is to combine shape and lay-up optimization, using analysis software and optimization algorithms to determine the optimal shape and lay-up that will meet performance requirements. This can be done using either geodesic or semi-geodesic winding. Semi-geodesic winding allows for more advanced design optimization, and can also be used to wind previously unwindable shapes or incorporate inserts that distribute the loads.
Filament winding imposes restrictions on the design freedom of the composite material, as the trajectory of the fiber path and the corresponding fiber angles cannot be chosen freely. This limits the ability to achieve optimal laminate lay-ups. However, semi-geodesic winding offers more design freedom by allowing for a greater range of fiber angles.
The coverage pattern, or how the fibers are arranged on the component, is another important factor to consider in filament winding design.
For axisymmetric components, a single fiber path can be repeated over the circumference. Non-axisymmetric components require more advanced calculations to achieve complete coverage. The winding strategy, or the interweaving of the fibers, can also be used as a design parameter to improve the end-product quality.
In recent years, design tools for filament winding have become more advanced with the integration of computers in the design process. These tools include software for winding simulation, stress analysis, and optimization. The use of computer-aided winding equipment also has greatly improved design capabilities.
There are several approaches to design methodologies for filament winding, including shape optimization, lay-up optimization, and a combination of both. Shape optimization involves finding the optimal shape of the component, while lay-up optimization involves finding the optimal arrangement of the fibers within the shape. By combining both shape and lay-up optimization, the design process can more fully exploit the advantages of composite materials.
A case study is presented on the design and production of composite LPG tanks. With the increasing adoption of hydrogen tanks such adoption towards lighter energy storage units would make the transition to sustainable energy faster.
In conclusion, filament winding is a popular manufacturing technique for producing wound composite structures. However, its design freedom is limited due to the constraints of the winding process. To optimize the use of composites despite these limitations, several approaches can be taken. These include lay-up optimization methodologies, as well as combining geometry and lay-up optimization. While geodesic winding offers limited freedom, semi-geodesic winding allows for more advanced design optimization and can even make previously unwindable shapes windable. A case study on the production of composite spinning pots demonstrates the complete filament winding design process, including the optimization of both lay-up and geometry. By appropriately varying the slippage tendency, a 12% performance increase compared to a similar geodesically wound dome can be achieved. However, further research is needed to understand how to optimally apply friction in both design problems without any penalty for the matrix.
Filament winding is a manufacturing process that involves applying continuous fiber roving, impregnated with resin, onto a rotating mandrel along predetermined patterns. This process is often used to create composite structures that have high specific stiffness and strength, as well as excellent corrosion resistance. The main advantage of composites is their anisotropy, meaning they are much stronger and stiffer in the fiber direction than perpendicular to the fibers. This allows designers to tailor their designs to meet performance requirements optimally. However, the filament winding process has limited design freedom, making it difficult to approach the optimal laminate lay-up in all given geometrical scenarios.
Designing with composites involves selecting the appropriate material, defining an appropriate configuration, and finding a suitable way to manufacture it. In the case of metal components, the geometry is typically defined independently from the material, and the material only comes into play during the final dimensioning stage. With composites, however, the material must be designed along with the structure. This requires several iterations, as there are no closed formulas for designing optimal laminates. Designers have a range of tools at their disposal, from simple laminate software in the preliminary design stage to more advanced analysis techniques like finite element analysis as the design progresses.
There are several factors to consider when designing filament winding. These include the manufacturing aspects and limitations of the winding process, the design tools available, and the process parameters that can significantly impact material properties and composite performance. The key limitations of conventional filament windings to keep in mind are
Some of the key process parameters to consider include the resin compound, mixing and distribution within the composite, the required resin viscosity and its evolution during winding, the feasible and allowable temperature variations and gradients during curing, and the environmental conditions during manufacture. Additionally, the winding tension in the fiber and the fiber positioning accuracy should be taken into account.
There are several approaches to designing with filament winding, including optimizing the laminate lay-up, combining shape and lay-up optimization, and using semi-geodesic winding to increase design freedom. A standard workflow can be seen below image. The process involves providing key inputs i.e. Pressure, polar opening radius, etc to arrive at an initial fiber angle distribution in dome and hoop regions. This approach helps with designing the first draft.
As the initial design is ready, the design can be optimized in the following ways. One method of lay-up optimization involves using stress analysis to determine the ideal fiber orientations and ply thicknesses and then adapting the lay-up to meet the strength requirements while taking into account the limitations of the winding process.
Another approach is to combine shape and lay-up optimization, using analysis software and optimization algorithms to determine the optimal shape and lay-up that will meet performance requirements. This can be done using either geodesic or semi-geodesic winding. Semi-geodesic winding allows for more advanced design optimization, and can also be used to wind previously unwindable shapes or incorporate inserts that distribute the loads.
Filament winding imposes restrictions on the design freedom of the composite material, as the trajectory of the fiber path and the corresponding fiber angles cannot be chosen freely. This limits the ability to achieve optimal laminate lay-ups. However, semi-geodesic winding offers more design freedom by allowing for a greater range of fiber angles.
The coverage pattern, or how the fibers are arranged on the component, is another important factor to consider in filament winding design.
For axisymmetric components, a single fiber path can be repeated over the circumference. Non-axisymmetric components require more advanced calculations to achieve complete coverage. The winding strategy, or the interweaving of the fibers, can also be used as a design parameter to improve the end-product quality.
In recent years, design tools for filament winding have become more advanced with the integration of computers in the design process. These tools include software for winding simulation, stress analysis, and optimization. The use of computer-aided winding equipment also has greatly improved design capabilities.
There are several approaches to design methodologies for filament winding, including shape optimization, lay-up optimization, and a combination of both. Shape optimization involves finding the optimal shape of the component, while lay-up optimization involves finding the optimal arrangement of the fibers within the shape. By combining both shape and lay-up optimization, the design process can more fully exploit the advantages of composite materials.
A case study is presented on the design and production of composite LPG tanks. With the increasing adoption of hydrogen tanks such adoption towards lighter energy storage units would make the transition to sustainable energy faster.
In conclusion, filament winding is a popular manufacturing technique for producing wound composite structures. However, its design freedom is limited due to the constraints of the winding process. To optimize the use of composites despite these limitations, several approaches can be taken. These include lay-up optimization methodologies, as well as combining geometry and lay-up optimization. While geodesic winding offers limited freedom, semi-geodesic winding allows for more advanced design optimization and can even make previously unwindable shapes windable. A case study on the production of composite spinning pots demonstrates the complete filament winding design process, including the optimization of both lay-up and geometry. By appropriately varying the slippage tendency, a 12% performance increase compared to a similar geodesically wound dome can be achieved. However, further research is needed to understand how to optimally apply friction in both design problems without any penalty for the matrix.