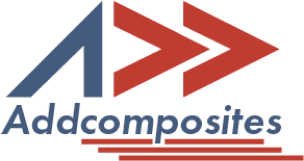
In the ever-evolving world of materials science, composites have emerged as a cornerstone, offering unparalleled advantages in strength, flexibility, and potential applications. Yet, for many, the intricate processes behind manufacturing these materials remain a mystery. In this article, brought to you by Addcomposites, we demystify the core procedures that breathe life into composites. Delve into the fundamental steps that are pivotal in composites manufacturing, understand their significance, and discover how they interplay to produce the high-performance materials that are revolutionizing industries. Whether you're a seasoned professional or a curious enthusiast, this guide promises to shed light on the art and science of composites manufacturing.
There are four fundamental steps involved in composites manufacturing:
These four steps are common in all composites production, although, the order of operations will be different depending on the application and manufacturing process!
In the impregnation process, the resin is applied to the previous dry fiber and ensures the fiber is thoroughly soaked during the process. The outcome of this process is called a lamina. Different methods are used to achieve thorough and uniform impregnation, although automation is the most common method today and uses a compaction roller to ensure that the resin flows evenly across fibers.
For example, in a filament winding process, fibers are passed through the resin bath for impregnation. In a hand lay-up process, materials that are already impregnated by the material supplier in a controlled environment are used. In the automated fiber placement process this step is done at the impregnation lines. The produce of the impregnation line is known as prepreg.
In the layup process, composite laminates are formed by placing either the fiber and impregnating it later, or by placing the combined fiber/resin prepregs, at desired locations and orientations. The composite part thickness is built up by placing various layers of the material.
In filament winding, the desired fiber distribution is obtained by the relative motions of the mandrel and carriage unit. Fiber has directional strength, and the orientation of the fibers directly results in the strength of the final part, thus they must be placed at a specific fiber orientation, either manually or by automated fiber placement systems.
In an RTM process, the dry preform is placed in a shaped mold for infusion. The preform is created from braiding, AFP, cutting & kitting, etc. then resin is injected and consolidated to form the laminate.
In the consolidation process, pressure is applied with the intention of obtaining a monolithic structure from discrete plies, simultaneously removing voids and volatiles, achieving desired fiber volume fractions in the part, and obtaining correct dimensional tolerances.
This pressure can be obtained by vacuum, compaction, pressing, or wrapping. Vacuum is the most common method of consolidation, used in most epoxy resin manufacturing. In the AFP processes, the consolidation force is applied at the time of layup with a compaction roller. In RTM, the consolidation occurs at the time of impregnation within the press. In filament winding, the consolidation force is applied initially while winding, and later by wrapping under tension with thin plastic film.
The final step is solidification, which may take less than a minute for thermoplastics or up to 120 minutes for thermosets. Either vacuum or positive pressure, or both, is maintained during this period to ensure proper consolidation.
In thermoset composites, the rate of solidification depends on the resin formulation and cure kinetics. Heat is supplied during solidification to expedite the cure rate of the resin. In thermoset resins, usually the higher the cure temperature, the faster the cross-linking process, although careful attention must be paid to the material data sheet in order for the best outcome.
In thermoplastics, there is no chemical change during solidification and therefore solidification requires the least amount of time and temperature. In thermoplastic processing, the rate of solidification depends on the cooling rate of the process. Generally, the lower the solidification time, the higher the production rate achievable by the process.
The world of composites has a lot of conditionals, so making a blanket statement is difficult to do, but these four steps are the common steps throughout all composites production processes, no matter if the material is thermosets or thermoplastics. The order of operations and the methods of applying these steps differ depending on the final part requirements, manufacturing process, and type of material used.
Prepreg and thermoplastic materials are impregnated before a layup and are most common for use in the aerospace industry where the standards are the highest. Lower requirement parts, such as sports and leisure (excluding high-performance equipment), would generally perform the layup and then impregnate the fibers with resin. Consolidation is independent of solidification, however, a part cannot be cured (thermosets) or solidified (thermoplastics) unless there is simultaneous consolidation.
Discover the future of composite manufacturing with Addcomposites! Here's how you can get involved:
At Addcomposites, we are dedicated to revolutionizing composite manufacturing. Our AFP systems and comprehensive support services are waiting for you to harness. So, don't wait – get started on your journey to the future of manufacturing today!
Composites Manufacturing Processes
Composite Manufacturing Methods
A Guide to Understanding the Composites Manufacturing Process
In the ever-evolving world of materials science, composites have emerged as a cornerstone, offering unparalleled advantages in strength, flexibility, and potential applications. Yet, for many, the intricate processes behind manufacturing these materials remain a mystery. In this article, brought to you by Addcomposites, we demystify the core procedures that breathe life into composites. Delve into the fundamental steps that are pivotal in composites manufacturing, understand their significance, and discover how they interplay to produce the high-performance materials that are revolutionizing industries. Whether you're a seasoned professional or a curious enthusiast, this guide promises to shed light on the art and science of composites manufacturing.
There are four fundamental steps involved in composites manufacturing:
These four steps are common in all composites production, although, the order of operations will be different depending on the application and manufacturing process!
In the impregnation process, the resin is applied to the previous dry fiber and ensures the fiber is thoroughly soaked during the process. The outcome of this process is called a lamina. Different methods are used to achieve thorough and uniform impregnation, although automation is the most common method today and uses a compaction roller to ensure that the resin flows evenly across fibers.
For example, in a filament winding process, fibers are passed through the resin bath for impregnation. In a hand lay-up process, materials that are already impregnated by the material supplier in a controlled environment are used. In the automated fiber placement process this step is done at the impregnation lines. The produce of the impregnation line is known as prepreg.
In the layup process, composite laminates are formed by placing either the fiber and impregnating it later, or by placing the combined fiber/resin prepregs, at desired locations and orientations. The composite part thickness is built up by placing various layers of the material.
In filament winding, the desired fiber distribution is obtained by the relative motions of the mandrel and carriage unit. Fiber has directional strength, and the orientation of the fibers directly results in the strength of the final part, thus they must be placed at a specific fiber orientation, either manually or by automated fiber placement systems.
In an RTM process, the dry preform is placed in a shaped mold for infusion. The preform is created from braiding, AFP, cutting & kitting, etc. then resin is injected and consolidated to form the laminate.
In the consolidation process, pressure is applied with the intention of obtaining a monolithic structure from discrete plies, simultaneously removing voids and volatiles, achieving desired fiber volume fractions in the part, and obtaining correct dimensional tolerances.
This pressure can be obtained by vacuum, compaction, pressing, or wrapping. Vacuum is the most common method of consolidation, used in most epoxy resin manufacturing. In the AFP processes, the consolidation force is applied at the time of layup with a compaction roller. In RTM, the consolidation occurs at the time of impregnation within the press. In filament winding, the consolidation force is applied initially while winding, and later by wrapping under tension with thin plastic film.
The final step is solidification, which may take less than a minute for thermoplastics or up to 120 minutes for thermosets. Either vacuum or positive pressure, or both, is maintained during this period to ensure proper consolidation.
In thermoset composites, the rate of solidification depends on the resin formulation and cure kinetics. Heat is supplied during solidification to expedite the cure rate of the resin. In thermoset resins, usually the higher the cure temperature, the faster the cross-linking process, although careful attention must be paid to the material data sheet in order for the best outcome.
In thermoplastics, there is no chemical change during solidification and therefore solidification requires the least amount of time and temperature. In thermoplastic processing, the rate of solidification depends on the cooling rate of the process. Generally, the lower the solidification time, the higher the production rate achievable by the process.
The world of composites has a lot of conditionals, so making a blanket statement is difficult to do, but these four steps are the common steps throughout all composites production processes, no matter if the material is thermosets or thermoplastics. The order of operations and the methods of applying these steps differ depending on the final part requirements, manufacturing process, and type of material used.
Prepreg and thermoplastic materials are impregnated before a layup and are most common for use in the aerospace industry where the standards are the highest. Lower requirement parts, such as sports and leisure (excluding high-performance equipment), would generally perform the layup and then impregnate the fibers with resin. Consolidation is independent of solidification, however, a part cannot be cured (thermosets) or solidified (thermoplastics) unless there is simultaneous consolidation.
Discover the future of composite manufacturing with Addcomposites! Here's how you can get involved:
At Addcomposites, we are dedicated to revolutionizing composite manufacturing. Our AFP systems and comprehensive support services are waiting for you to harness. So, don't wait – get started on your journey to the future of manufacturing today!
Composites Manufacturing Processes
Composite Manufacturing Methods
A Guide to Understanding the Composites Manufacturing Process