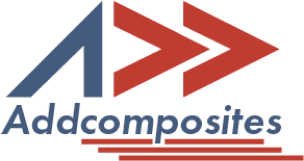
Embarking on a journey through the intricate world of Filament Winding, this blog unfolds the myriad facets of this pivotal technique in the composites industry. Here’s a brief executive summary of what to anticipate:
Filament winding has evolved as a pivotal technique in the composites industry, particularly for manufacturing composite preforms. The process has been in use for over 50 years, with significant modernization occurring predominantly in the last decade. The filament winding process, especially in its early stages, was quite manual, involving steps like manually loading mandrels, mixing resin, tying fibers to the mandrel, changing fiber types, cutting rovings post-winding, and unloading the wet-wound mandrels into the oven. The modern filament winding process has witnessed a revolution, incorporating automation and sophisticated technologies, such as robotic or handling device-assisted loading/unloading of mandrels and automatic resin-mixing systems.
The basic helical horizontal filament winding machine system was introduced as a fundamental tool in the filament winding process. In the early stages of filament winding, machines were mechanically controlled, utilizing gearboxes to determine winding angles and chains to define the part length to be wound. Adjustments to the winding angle and part length were manual and required an understanding of the relationships within the gearboxes and how these related to the produced winding angles on the manufactured parts.
Filament winding offers notable economic and weight advantages, particularly when compared to metal products. The process is recognized for its capability to deliver excellent mechanical properties from continuous aligned fibers, especially in the creation of axisymmetric bodies. The geometric constraints and the necessity to program a single circuit of the fiber wind path, which can be repeated to provide a fiber layer completely covering the mandrel, are among the main limitations of the winding process. However, the method has proven to be cost-effective and efficient, especially in applications where the mechanical properties of aligned fibers can be fully utilized.
Fiber slippage is a prevalent issue in filament winding, especially in large-diameter windings. The fibers can potentially slip free of the mandrel during the curing process due to the lower resin viscosity. The friction and resistance to slippage can originate from various physical mechanisms beyond pure mechanical friction. For instance, when winding with a tacky tow-preg (resin-preimpregnated tow), there is some physical adhesion between the fiber being applied and the mandrel. Additionally, during wet winding with high fiber tension, there is a tendency to compress the new fiber into the material already laid, generating a degree of mechanical interlock. Advanced software systems used for programming filament winding machines must incorporate the concept of some friction, and users must be able to specify a limiting (i.e., non-slip) value for the materials being used.
Large-diameter windings present their own set of challenges in filament winding. The fibers, especially in larger diameters, can experience uncontrollable slippage. The winding process for axisymmetric shapes, such as cylinders, tapered shafts, spheres, and cones, is common, with pipes for fluid transport or cylinders with closed ends (usually spherical, elliptical, or torispherical) being the most manufactured parts for pressure or storage vessels. Filament winding offers several advantages over other manufacturing processes, including being one of the few automated processes for producing composite preforms. However, the geometric constraints and the necessity to program a single circuit of the fiber wind path, which can be repeated to provide a fiber layer completely covering the mandrel, are among the main limitations of the winding process.
Creels play a pivotal role in the filament winding process, serving as a device that holds the necessary number of roving balls or supply packages in a designated position for unwinding onto the mandrel during filament winding. The creel ensures that the fiber can be pulled from the center of the bundle without tension but with a twist, which has its own set of consequences and considerations in the winding process.
There are several types of creels utilized in filament winding, each with its own specific application and functionality:
When fibers, also referred to as tows or rovings, are removed from a package, they are not twisted in their packages. The fiber removal process, especially from the first guide, should ideally be on the horizontal centerline of the package to prevent fall-off of wraps at the edges and to minimize scuffing. The departure angle becomes more acute if the first guide from the package is shifted to either side of the centerline, resulting in lateral slippage as it unwinds, scuffing the underlying fiber. All redirects must be generously radiused or beveled to minimize friction and prevent fiber damage. Excessive tension should be avoided to prevent increased self-abrasion over the roll surface and in guides, possible breakage of the tow, and the tendency of the tow to embed itself in underlying layers.
The In-Plane (Polar) Winder is a distinctive type of filament winding machine that operates on a unique mechanism where the mandrel rotates while a fiber-delivery carriage moves around it, but not in the shortest distance from one end to the other on the cylindrical surface. Instead, the motion places the fibers on a path that is polar, meaning it is not the direct path from end to end on the cylindrical surface. This mechanism is illustrated in figure, providing a visual representation of its operational methodology. The fibers, in this context, are not directly liable to assume maximum internal stress, which is a crucial aspect to consider in the winding process.
The design of the In-Plane Filament Winding Machine is inherently aimed at ensuring that the fibers are placed in a specific path that, while not being the shortest, is meticulously calculated to achieve desired winding outcomes. The movement of the fiber-delivery carriage in relation to the rotating mandrel is engineered to facilitate a polar path for the fibers, which has its own set of advantages and considerations in the filament winding process. The design and functional simplicity of the In-Plane Winder are pivotal in ensuring that the fibers are wound in a manner that is conducive to the structural and functional integrity of the final product.
“S” wraps, consisting of two static bars placed one over the other, have proven to be an effective method for spreading the fiber in the filament winding process. The pair of static bars can be rotated as a unit to minimize or maximize the fiber contact or to provide tension in the fiber. The longer the fiber is in contact with the surface (residence time) on the static rods, the greater the spread width will be. Interestingly, running speed has little to no effect on the spread width. If multiple “S” wraps or static bars are used, path length does have an effect on the spread width, with a path of 2 to 4 ft (0.6 to 1.2 m) being a good working range. Beyond that, the fiber will tend to rope up or come back together, especially important with resin-wetted fiber.
Path length and back tension are critical factors in fiber spreading. A longer path length, especially beyond the optimal working range, may cause the fiber to rope up or reconverge, particularly with resin-wetted fiber. The higher the back tension on the fiber, the more critical the sweep angle becomes during unwinding. If the package is mounted with a spring, washers, and nut arrangement (for tension control) on a shaft, the package should rotate in the direction that loosens the nut. Otherwise, it will tighten the nut until the package is literally seized, presenting challenges in the winding process.
Mandrels play a pivotal role in filament winding, acting as a tool that provides the inside surface and shape for forming the wound product. Various types of mandrels have been utilized in manufacturing, including those made from materials ranging from cardboard to stainless steel. The fundamental requirement is that they can be extracted from the wound component, or in certain applications, such as pressure vessels, remain in the component as a liner. Some alternate approaches to mandrel design and usage are illustrated in the book. For instance, a filament-wound vessel with fibers at ±54.75° will expand in both directions under internal pressure, maintaining the wind angle. This fact is utilized in the filament winding mandrel to simplify the extraction of a filament-wound pipe that was wound onto it. The mandrel is fabricated by overwinding both ends of a dissolvable mandrel or a compressible foam mandrel, using center shafts with end-pressure connections.
Mandrels must be designed to resist various factors, such as winding tension, curing heat, and deformations caused by the weight of the product and the mandrel itself. They must be manufactured to the necessary tolerances and possess sufficient durability. When considering resistance factors, it is crucial to explore how the mandrel interacts with the winding process and how it withstands the various stresses and strains introduced during manufacturing. For example, if the package is mounted with a spring, washers, and nut arrangement (for tension control) on a shaft, the package should rotate in the direction that loosens the nut to prevent seizing.
Filament winding is a pivotal technique in the composites industry, offering a versatile method for producing robust, high-strength structures across various sectors. From aerospace to civil engineering, filament winding facilitates the manufacturing of diverse components and structures, demonstrating its widespread applicability and efficacy.
Filament winding, as explored in the preceding sections, stands out as a versatile and efficient technique in the composites industry, enabling the creation of robust, high-strength structures across a myriad of applications. From understanding the fundamental processes, navigating through challenges, exploring various machines like In-Plane Winders, and diving into the intricacies of components like Creels and Mandrels, we've navigated through the multifaceted world of filament winding. The technique not only offers economic and weight advantages but also provides solutions to challenges in large-diameter windings and fiber slippage issues.
While filament winding presents numerous advantages and applications across industries, it is not without its challenges. Fiber slippage, challenges in large-diameter windings, and considerations in fiber spreading techniques are among the issues that practitioners and researchers in the field grapple with. The exploration of novel materials, innovative design approaches for Creels and Mandrels, and advancements in machinery like the In-Plane Winder present open areas for research and development. Furthermore, diving deeper into the applications and case studies of filament winding in various industries can pave the way for innovative applications and solutions to existing challenges.
Discover the future of composite manufacturing with Addcomposites! Here's how you can get involved:
At Addcomposites, we are dedicated to revolutionizing composite manufacturing. Our AFP systems and comprehensive support services are waiting for you to harness. So, don't wait – get started on your journey to the future of manufacturing today!
Embarking on a journey through the intricate world of Filament Winding, this blog unfolds the myriad facets of this pivotal technique in the composites industry. Here’s a brief executive summary of what to anticipate:
Filament winding has evolved as a pivotal technique in the composites industry, particularly for manufacturing composite preforms. The process has been in use for over 50 years, with significant modernization occurring predominantly in the last decade. The filament winding process, especially in its early stages, was quite manual, involving steps like manually loading mandrels, mixing resin, tying fibers to the mandrel, changing fiber types, cutting rovings post-winding, and unloading the wet-wound mandrels into the oven. The modern filament winding process has witnessed a revolution, incorporating automation and sophisticated technologies, such as robotic or handling device-assisted loading/unloading of mandrels and automatic resin-mixing systems.
The basic helical horizontal filament winding machine system was introduced as a fundamental tool in the filament winding process. In the early stages of filament winding, machines were mechanically controlled, utilizing gearboxes to determine winding angles and chains to define the part length to be wound. Adjustments to the winding angle and part length were manual and required an understanding of the relationships within the gearboxes and how these related to the produced winding angles on the manufactured parts.
Filament winding offers notable economic and weight advantages, particularly when compared to metal products. The process is recognized for its capability to deliver excellent mechanical properties from continuous aligned fibers, especially in the creation of axisymmetric bodies. The geometric constraints and the necessity to program a single circuit of the fiber wind path, which can be repeated to provide a fiber layer completely covering the mandrel, are among the main limitations of the winding process. However, the method has proven to be cost-effective and efficient, especially in applications where the mechanical properties of aligned fibers can be fully utilized.
Fiber slippage is a prevalent issue in filament winding, especially in large-diameter windings. The fibers can potentially slip free of the mandrel during the curing process due to the lower resin viscosity. The friction and resistance to slippage can originate from various physical mechanisms beyond pure mechanical friction. For instance, when winding with a tacky tow-preg (resin-preimpregnated tow), there is some physical adhesion between the fiber being applied and the mandrel. Additionally, during wet winding with high fiber tension, there is a tendency to compress the new fiber into the material already laid, generating a degree of mechanical interlock. Advanced software systems used for programming filament winding machines must incorporate the concept of some friction, and users must be able to specify a limiting (i.e., non-slip) value for the materials being used.
Large-diameter windings present their own set of challenges in filament winding. The fibers, especially in larger diameters, can experience uncontrollable slippage. The winding process for axisymmetric shapes, such as cylinders, tapered shafts, spheres, and cones, is common, with pipes for fluid transport or cylinders with closed ends (usually spherical, elliptical, or torispherical) being the most manufactured parts for pressure or storage vessels. Filament winding offers several advantages over other manufacturing processes, including being one of the few automated processes for producing composite preforms. However, the geometric constraints and the necessity to program a single circuit of the fiber wind path, which can be repeated to provide a fiber layer completely covering the mandrel, are among the main limitations of the winding process.
Creels play a pivotal role in the filament winding process, serving as a device that holds the necessary number of roving balls or supply packages in a designated position for unwinding onto the mandrel during filament winding. The creel ensures that the fiber can be pulled from the center of the bundle without tension but with a twist, which has its own set of consequences and considerations in the winding process.
There are several types of creels utilized in filament winding, each with its own specific application and functionality:
When fibers, also referred to as tows or rovings, are removed from a package, they are not twisted in their packages. The fiber removal process, especially from the first guide, should ideally be on the horizontal centerline of the package to prevent fall-off of wraps at the edges and to minimize scuffing. The departure angle becomes more acute if the first guide from the package is shifted to either side of the centerline, resulting in lateral slippage as it unwinds, scuffing the underlying fiber. All redirects must be generously radiused or beveled to minimize friction and prevent fiber damage. Excessive tension should be avoided to prevent increased self-abrasion over the roll surface and in guides, possible breakage of the tow, and the tendency of the tow to embed itself in underlying layers.
The In-Plane (Polar) Winder is a distinctive type of filament winding machine that operates on a unique mechanism where the mandrel rotates while a fiber-delivery carriage moves around it, but not in the shortest distance from one end to the other on the cylindrical surface. Instead, the motion places the fibers on a path that is polar, meaning it is not the direct path from end to end on the cylindrical surface. This mechanism is illustrated in figure, providing a visual representation of its operational methodology. The fibers, in this context, are not directly liable to assume maximum internal stress, which is a crucial aspect to consider in the winding process.
The design of the In-Plane Filament Winding Machine is inherently aimed at ensuring that the fibers are placed in a specific path that, while not being the shortest, is meticulously calculated to achieve desired winding outcomes. The movement of the fiber-delivery carriage in relation to the rotating mandrel is engineered to facilitate a polar path for the fibers, which has its own set of advantages and considerations in the filament winding process. The design and functional simplicity of the In-Plane Winder are pivotal in ensuring that the fibers are wound in a manner that is conducive to the structural and functional integrity of the final product.
“S” wraps, consisting of two static bars placed one over the other, have proven to be an effective method for spreading the fiber in the filament winding process. The pair of static bars can be rotated as a unit to minimize or maximize the fiber contact or to provide tension in the fiber. The longer the fiber is in contact with the surface (residence time) on the static rods, the greater the spread width will be. Interestingly, running speed has little to no effect on the spread width. If multiple “S” wraps or static bars are used, path length does have an effect on the spread width, with a path of 2 to 4 ft (0.6 to 1.2 m) being a good working range. Beyond that, the fiber will tend to rope up or come back together, especially important with resin-wetted fiber.
Path length and back tension are critical factors in fiber spreading. A longer path length, especially beyond the optimal working range, may cause the fiber to rope up or reconverge, particularly with resin-wetted fiber. The higher the back tension on the fiber, the more critical the sweep angle becomes during unwinding. If the package is mounted with a spring, washers, and nut arrangement (for tension control) on a shaft, the package should rotate in the direction that loosens the nut. Otherwise, it will tighten the nut until the package is literally seized, presenting challenges in the winding process.
Mandrels play a pivotal role in filament winding, acting as a tool that provides the inside surface and shape for forming the wound product. Various types of mandrels have been utilized in manufacturing, including those made from materials ranging from cardboard to stainless steel. The fundamental requirement is that they can be extracted from the wound component, or in certain applications, such as pressure vessels, remain in the component as a liner. Some alternate approaches to mandrel design and usage are illustrated in the book. For instance, a filament-wound vessel with fibers at ±54.75° will expand in both directions under internal pressure, maintaining the wind angle. This fact is utilized in the filament winding mandrel to simplify the extraction of a filament-wound pipe that was wound onto it. The mandrel is fabricated by overwinding both ends of a dissolvable mandrel or a compressible foam mandrel, using center shafts with end-pressure connections.
Mandrels must be designed to resist various factors, such as winding tension, curing heat, and deformations caused by the weight of the product and the mandrel itself. They must be manufactured to the necessary tolerances and possess sufficient durability. When considering resistance factors, it is crucial to explore how the mandrel interacts with the winding process and how it withstands the various stresses and strains introduced during manufacturing. For example, if the package is mounted with a spring, washers, and nut arrangement (for tension control) on a shaft, the package should rotate in the direction that loosens the nut to prevent seizing.
Filament winding is a pivotal technique in the composites industry, offering a versatile method for producing robust, high-strength structures across various sectors. From aerospace to civil engineering, filament winding facilitates the manufacturing of diverse components and structures, demonstrating its widespread applicability and efficacy.
Filament winding, as explored in the preceding sections, stands out as a versatile and efficient technique in the composites industry, enabling the creation of robust, high-strength structures across a myriad of applications. From understanding the fundamental processes, navigating through challenges, exploring various machines like In-Plane Winders, and diving into the intricacies of components like Creels and Mandrels, we've navigated through the multifaceted world of filament winding. The technique not only offers economic and weight advantages but also provides solutions to challenges in large-diameter windings and fiber slippage issues.
While filament winding presents numerous advantages and applications across industries, it is not without its challenges. Fiber slippage, challenges in large-diameter windings, and considerations in fiber spreading techniques are among the issues that practitioners and researchers in the field grapple with. The exploration of novel materials, innovative design approaches for Creels and Mandrels, and advancements in machinery like the In-Plane Winder present open areas for research and development. Furthermore, diving deeper into the applications and case studies of filament winding in various industries can pave the way for innovative applications and solutions to existing challenges.
Discover the future of composite manufacturing with Addcomposites! Here's how you can get involved:
At Addcomposites, we are dedicated to revolutionizing composite manufacturing. Our AFP systems and comprehensive support services are waiting for you to harness. So, don't wait – get started on your journey to the future of manufacturing today!