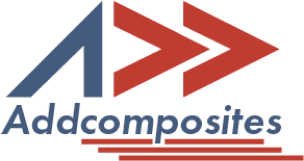
A composites structure design goes through multiple steps. We have covered the previous two steps in the Structural Composites Design: Concepts and Composites Design Software: Tools for Designers. In this blog, we will deep dive into the next step i.e. production simulation of composites.
The application of virtual manufacturing simulation tools ensures that composite manufacturing processes lead to high-quality and cost-effective components. The simulation tools are used over a wide range of processes to validate the design and predict material behavior at each step of the processing. A wide gamut of virtual manufacturing simulations is available for different process simulations.
Automated depositing of fiber tapes using Automated Fiber Placement (AFP) is increasingly being adopted by the industry. After the FEA analysis, the main outcome is the fiber orientation and other selective reinforcements. In order to convert the ply data from the FEA model into an AFP program, the general flow of steps is outlined below:
FEA model is exported into a CAD format such as .step or .igs. The CAD model shape provides the surface geometry of the tool. The tooling will be used for the layup with compaction force and the curing of parts all occurring on the tool itself. Typical mold design considerations e.g. sufficient draft angles, complex geometries, or multi-piece/sacrificial tooling might be required and taken into consideration. Additionally, tension and part shrinkage can contribute to a condition known as ‘spring-in’ with cured parts, requiring an angular compensation in the tool design.
Tooling and mandrels for automated fiber placement and tape-laying processes typically are designed to provide the appropriate inner-most-loft or outer-most-loft surface. Tools and mandrels of this type may be designed to index on an automated machine-bed platform for use with AFP or ATL equipment. Any modern CAD software can be used to draw the tool CAD model with the above considerations.
Figure 1. Part model for tooling design
The tooling design step from the CAD model is shown in the figure below. The tool has extended boundaries for the AFP tool runways and vacuum bagging operations. The hole has been filled up to create a continuous surface for runways within the part. The mounting feature should be considered in the tooling design e.g. in the example shown below the tooling is mounted on the rotary chuck, so an extended shaft is added for mounting onto the rotary axis. Depending on the mold manufacturing method, the rest of the details can be created accordingly.
The tooling CAD model is imported into the offline programming software (OLP) to create layup definitions in two steps i.e. Planning and Simulation.
Off-line Programming Software (OLP) software like AddPath is used for AFP process workflow as presented in the figure below. The OLP Software takes the tooling CAD models as input. The first step is to define the layup area and boundary. Next, the processing parameters such as fiber orientations, runway, approach, clearance, speed, and heating intensity, are input based on your needs. Based on this information, the OLP can create motion paths for the fiber placement tool with multiple strategies.
Figure 2. Composite Software overview
In addition to the motion paths, there are multiple parameters e.g. tape weight (GSM), gaps, and staggering, that the engineer can choose from to configure the motion path. Typical OLP is capable of:
The generated paths will be followed by the AFP robot. While the AFP head is trying to follow the motion paths, there arise possibilities that it might hit the tooling or pass the robot singularities. In order to visualize these occurrences, robot motion simulation is evaluated either by automated analysis or by the operator to eliminate such problems. The key benefit of running the simulation in the virtual environment is avoiding costly collision and damage to the AFP head, robot, part, or tooling!
The stages to reach simulation are shown in the image below. The process of simulating your layup can be described as follows:
1. Select/define boundary and layup area
2. Define the fiber orientation and stacking sequence
3. Run a simulation to visualize anomalies within the virtual environment.
Figure 3. Path Planning Stages in Off-line Planning (OLP) Software
Once the paths have been analyzed and the simulation is verified to function appropriately, the robot program is generated in the specific robot language. Major programming languages are KRL (KUKA), RAPID (ABB), and Karel (Fanuc). The language is determined based on the robot input at the beginning of the Programmation phase. The program can now be uploaded into the robot controller for production. The program is built so the global variables e.g. speed, heat, etc., can be modified at the robot HMI (Human Machine Interface), without needing to reprogram the entire layup again.
Virtual simulation tools are used for converting the design obtained from the FEA simulations into manufacturing simulation environments. Using an automated deposition technique i.e. AFP and ATL, a process flow is described. The process begins with the tooling design and manufacturing planning, then the engineer is able to simulate the process and the production program is created by the OLP.
Figure 4. The Simulation and Programming Software from Addcomposites - AddPath
Besides, Addcomposites introduces open access to AddPath for everyone to use (download here). AddPath is an open-access platform for 3D Composites Manufacturing that enables students and academia to learn about the nuances of AFP during their courses, while researchers and SMEs can explore different path planning strategies for design optimization. The cloud-based license will allow anyone to create programs and perform simulations for AFP on their personal or work computers, enabling digital composites additive manufacturing from home or the office.
Addcomposites is the provider of the Automated Fiber Placement (AFP) ecosystem - including the Fiber Placement System (AFP-XS), 3D Simulation and Programming Software (AddPath), and Robotic Cells (AddCell). With the leasing program for the AFP system (AFPnext), composites manufacturers can work with thermosets, thermoplastics, dry fiber placement, or in combination with 3D Printers on a monthly basis.
A composites structure design goes through multiple steps. We have covered the previous two steps in the Structural Composites Design: Concepts and Composites Design Software: Tools for Designers. In this blog, we will deep dive into the next step i.e. production simulation of composites.
The application of virtual manufacturing simulation tools ensures that composite manufacturing processes lead to high-quality and cost-effective components. The simulation tools are used over a wide range of processes to validate the design and predict material behavior at each step of the processing. A wide gamut of virtual manufacturing simulations is available for different process simulations.
Automated depositing of fiber tapes using Automated Fiber Placement (AFP) is increasingly being adopted by the industry. After the FEA analysis, the main outcome is the fiber orientation and other selective reinforcements. In order to convert the ply data from the FEA model into an AFP program, the general flow of steps is outlined below:
FEA model is exported into a CAD format such as .step or .igs. The CAD model shape provides the surface geometry of the tool. The tooling will be used for the layup with compaction force and the curing of parts all occurring on the tool itself. Typical mold design considerations e.g. sufficient draft angles, complex geometries, or multi-piece/sacrificial tooling might be required and taken into consideration. Additionally, tension and part shrinkage can contribute to a condition known as ‘spring-in’ with cured parts, requiring an angular compensation in the tool design.
Tooling and mandrels for automated fiber placement and tape-laying processes typically are designed to provide the appropriate inner-most-loft or outer-most-loft surface. Tools and mandrels of this type may be designed to index on an automated machine-bed platform for use with AFP or ATL equipment. Any modern CAD software can be used to draw the tool CAD model with the above considerations.
Figure 1. Part model for tooling design
The tooling design step from the CAD model is shown in the figure below. The tool has extended boundaries for the AFP tool runways and vacuum bagging operations. The hole has been filled up to create a continuous surface for runways within the part. The mounting feature should be considered in the tooling design e.g. in the example shown below the tooling is mounted on the rotary chuck, so an extended shaft is added for mounting onto the rotary axis. Depending on the mold manufacturing method, the rest of the details can be created accordingly.
The tooling CAD model is imported into the offline programming software (OLP) to create layup definitions in two steps i.e. Planning and Simulation.
Off-line Programming Software (OLP) software like AddPath is used for AFP process workflow as presented in the figure below. The OLP Software takes the tooling CAD models as input. The first step is to define the layup area and boundary. Next, the processing parameters such as fiber orientations, runway, approach, clearance, speed, and heating intensity, are input based on your needs. Based on this information, the OLP can create motion paths for the fiber placement tool with multiple strategies.
Figure 2. Composite Software overview
In addition to the motion paths, there are multiple parameters e.g. tape weight (GSM), gaps, and staggering, that the engineer can choose from to configure the motion path. Typical OLP is capable of:
The generated paths will be followed by the AFP robot. While the AFP head is trying to follow the motion paths, there arise possibilities that it might hit the tooling or pass the robot singularities. In order to visualize these occurrences, robot motion simulation is evaluated either by automated analysis or by the operator to eliminate such problems. The key benefit of running the simulation in the virtual environment is avoiding costly collision and damage to the AFP head, robot, part, or tooling!
The stages to reach simulation are shown in the image below. The process of simulating your layup can be described as follows:
1. Select/define boundary and layup area
2. Define the fiber orientation and stacking sequence
3. Run a simulation to visualize anomalies within the virtual environment.
Figure 3. Path Planning Stages in Off-line Planning (OLP) Software
Once the paths have been analyzed and the simulation is verified to function appropriately, the robot program is generated in the specific robot language. Major programming languages are KRL (KUKA), RAPID (ABB), and Karel (Fanuc). The language is determined based on the robot input at the beginning of the Programmation phase. The program can now be uploaded into the robot controller for production. The program is built so the global variables e.g. speed, heat, etc., can be modified at the robot HMI (Human Machine Interface), without needing to reprogram the entire layup again.
Virtual simulation tools are used for converting the design obtained from the FEA simulations into manufacturing simulation environments. Using an automated deposition technique i.e. AFP and ATL, a process flow is described. The process begins with the tooling design and manufacturing planning, then the engineer is able to simulate the process and the production program is created by the OLP.
Figure 4. The Simulation and Programming Software from Addcomposites - AddPath
Besides, Addcomposites introduces open access to AddPath for everyone to use (download here). AddPath is an open-access platform for 3D Composites Manufacturing that enables students and academia to learn about the nuances of AFP during their courses, while researchers and SMEs can explore different path planning strategies for design optimization. The cloud-based license will allow anyone to create programs and perform simulations for AFP on their personal or work computers, enabling digital composites additive manufacturing from home or the office.
Addcomposites is the provider of the Automated Fiber Placement (AFP) ecosystem - including the Fiber Placement System (AFP-XS), 3D Simulation and Programming Software (AddPath), and Robotic Cells (AddCell). With the leasing program for the AFP system (AFPnext), composites manufacturers can work with thermosets, thermoplastics, dry fiber placement, or in combination with 3D Printers on a monthly basis.