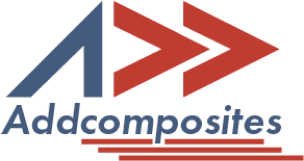
How we learn about composites and light structures design has changed drastically be it due to Covid-19, zoom classes, or open-access software, This article focuses on the transition and elaborates on the new way of learning called e-training. Let's dive into it!
Since the start of the pandemic, colleges have to shut down and students are forced to study from home. This has forced the teaching curriculum to be updated on the go and do what is possible from home. Online teaching has now come to a point where we start to feel comfortable. Online teaching has already been educating in the third-world countries way before the pandemic, due to the high accessibility and low cost of distribution.
Education with composites has not been much different than conventional metal design and production. it has required understanding the material and process landscape with stiffness matric calculations. In the recent curriculums, most institutes added the design and analysis with FEA programs and a few also added some manufacturing processes simulation. The e-learning with composites has now seemed to be shifting online with the composites e-learning courses, such as
Paid classes / tutorials
Free classes/tutorials
Despite the vast amount of courses being helpful in gaining fundamental knowledge, they are unable to provide real-life hands-on problem-solving skills. As a team composites engineer, at Addcomposites, we perform a lot of work on our computers, as more and more composites manufacturing is going digital and Automated fiber placement, Kitting solutions and continuous fiber 3D printing processes are taking over the conventional process in real industries.
It is a framework to learn and work with digital composites design, manufacturing, testing, and business modeling framework that enables solving of real-life problems. The key steps are
Let's try to understand how the e-training goes
Pre-requisite: Access to open FEA software and AddPath.
This step is usually carried out in a project scope document, where all the key factors about the product requirements, test qualification, parts to be produced, manufacturing-cost/part criteria, etc are provided. We are going to take an example part to walk through the steps of the process.
Case: Need to design a turbine blade optimized for lightweight. A lightweight design produced at a large scale usually relies on continuous fiber-reinforced parts and other lattice design principles to optimize the weight.
The next step focuses on the manufacturable design that meets the product requirements.
- Aerodynamics and fluid simulation
- Vibration
- Impact
- Thermal
- AFP
- Continuous fiber 3D printing
- Adhesive Bonding
- Optimise design for manufacturing
In order to make the fan blade mold, the following steps should be followed:
Planning the layup on a 3D mold shape has been made very simple and accessible thanks to AddPath. A step-by-step process of planning via AddPath is depicted in the picture below. The process with different planning strategies while allowing the user to define their own paths by simply drawing a curve in the chosen CAD modeling software and importing it.
Simulating the process via AddPath is very critical to make sure the following items are being met without error:
Virtual Testing is the simulation of a physical test, using finite element analysis tools, multi-body dynamic analysis tools, and RPC iteration techniques to derive accurate loads, motion, and damage information of a system. Virtualized production data from AddPath with accurate loads, motion, and damages to validate the part in a virtualized environment.
The key benefit of Virtual Testing is it relies on digital twin data from real-world products and physics real simulation data from the manufacturing software. This produces simulation very close to the real world in an almost completely digital manner.
This step often gets missed out in most training and is often the most important for the economic feasibility of the production. In order to build the business case for the process, the key input is the production output required on annual basis, lets's assume we want to produce 1000 units of the blade per year, then the major cost item can be divided into the following
7.1 Material cost/part i.e. €400
7.2 Production time/Part i.e. 20 min i.e. 528/month
7.3 Cost of Machines capital invested i.e. €5000/month
7.4 No. of Labour: 2
7.5 Production cost/part
Material cost + (cost of machine /mo+labour cost/mo) / (part produced/month) + Overhead 20% = €510
e-training is essentially the next major step after basics e-learning platforms and offers the following key benefits
Opening access to AFP programming and simulation software - AddPath enables students and academia to learn about the nuances of AFP during their courses, while researchers and SMEs can explore different path planning strategies for design optimization. The cloud-based license will allow anyone to create programs and perform simulations for AFP on their personal or work computers, enabling digital composites additive manufacturing from home or the office.
To support e-learning and e-training, Addcomposites has developed and published extensive resources, such as the single-two fiber placement (AFP-XS), robots from various manufacturers (i.e, Kuka, ABB, FANUC, etc.), sample projects, sample geometries, tutorials, etc. The resources library is continuously expanding based on inputs from the composites community and adding further capabilities to support specific use cases.
You can download the AddPath online now by following this link.
Addcomposites is the provider of the Automated Fiber Placement (AFP) ecosystem - including the Fiber Placement System (AFP-XS), 3D Simulation and Programming Software (AddPath), and Robotic Cells (AddCell). With the leasing program for the AFP system (AFPnext), composites manufacturers can work with thermosets, thermoplastics, dry fiber placement, or in combination with 3D Printers on a monthly basis
How we learn about composites and light structures design has changed drastically be it due to Covid-19, zoom classes, or open-access software, This article focuses on the transition and elaborates on the new way of learning called e-training. Let's dive into it!
Since the start of the pandemic, colleges have to shut down and students are forced to study from home. This has forced the teaching curriculum to be updated on the go and do what is possible from home. Online teaching has now come to a point where we start to feel comfortable. Online teaching has already been educating in the third-world countries way before the pandemic, due to the high accessibility and low cost of distribution.
Education with composites has not been much different than conventional metal design and production. it has required understanding the material and process landscape with stiffness matric calculations. In the recent curriculums, most institutes added the design and analysis with FEA programs and a few also added some manufacturing processes simulation. The e-learning with composites has now seemed to be shifting online with the composites e-learning courses, such as
Paid classes / tutorials
Free classes/tutorials
Despite the vast amount of courses being helpful in gaining fundamental knowledge, they are unable to provide real-life hands-on problem-solving skills. As a team composites engineer, at Addcomposites, we perform a lot of work on our computers, as more and more composites manufacturing is going digital and Automated fiber placement, Kitting solutions and continuous fiber 3D printing processes are taking over the conventional process in real industries.
It is a framework to learn and work with digital composites design, manufacturing, testing, and business modeling framework that enables solving of real-life problems. The key steps are
Let's try to understand how the e-training goes
Pre-requisite: Access to open FEA software and AddPath.
This step is usually carried out in a project scope document, where all the key factors about the product requirements, test qualification, parts to be produced, manufacturing-cost/part criteria, etc are provided. We are going to take an example part to walk through the steps of the process.
Case: Need to design a turbine blade optimized for lightweight. A lightweight design produced at a large scale usually relies on continuous fiber-reinforced parts and other lattice design principles to optimize the weight.
The next step focuses on the manufacturable design that meets the product requirements.
- Aerodynamics and fluid simulation
- Vibration
- Impact
- Thermal
- AFP
- Continuous fiber 3D printing
- Adhesive Bonding
- Optimise design for manufacturing
In order to make the fan blade mold, the following steps should be followed:
Planning the layup on a 3D mold shape has been made very simple and accessible thanks to AddPath. A step-by-step process of planning via AddPath is depicted in the picture below. The process with different planning strategies while allowing the user to define their own paths by simply drawing a curve in the chosen CAD modeling software and importing it.
Simulating the process via AddPath is very critical to make sure the following items are being met without error:
Virtual Testing is the simulation of a physical test, using finite element analysis tools, multi-body dynamic analysis tools, and RPC iteration techniques to derive accurate loads, motion, and damage information of a system. Virtualized production data from AddPath with accurate loads, motion, and damages to validate the part in a virtualized environment.
The key benefit of Virtual Testing is it relies on digital twin data from real-world products and physics real simulation data from the manufacturing software. This produces simulation very close to the real world in an almost completely digital manner.
This step often gets missed out in most training and is often the most important for the economic feasibility of the production. In order to build the business case for the process, the key input is the production output required on annual basis, lets's assume we want to produce 1000 units of the blade per year, then the major cost item can be divided into the following
7.1 Material cost/part i.e. €400
7.2 Production time/Part i.e. 20 min i.e. 528/month
7.3 Cost of Machines capital invested i.e. €5000/month
7.4 No. of Labour: 2
7.5 Production cost/part
Material cost + (cost of machine /mo+labour cost/mo) / (part produced/month) + Overhead 20% = €510
e-training is essentially the next major step after basics e-learning platforms and offers the following key benefits
Opening access to AFP programming and simulation software - AddPath enables students and academia to learn about the nuances of AFP during their courses, while researchers and SMEs can explore different path planning strategies for design optimization. The cloud-based license will allow anyone to create programs and perform simulations for AFP on their personal or work computers, enabling digital composites additive manufacturing from home or the office.
To support e-learning and e-training, Addcomposites has developed and published extensive resources, such as the single-two fiber placement (AFP-XS), robots from various manufacturers (i.e, Kuka, ABB, FANUC, etc.), sample projects, sample geometries, tutorials, etc. The resources library is continuously expanding based on inputs from the composites community and adding further capabilities to support specific use cases.
You can download the AddPath online now by following this link.
Addcomposites is the provider of the Automated Fiber Placement (AFP) ecosystem - including the Fiber Placement System (AFP-XS), 3D Simulation and Programming Software (AddPath), and Robotic Cells (AddCell). With the leasing program for the AFP system (AFPnext), composites manufacturers can work with thermosets, thermoplastics, dry fiber placement, or in combination with 3D Printers on a monthly basis