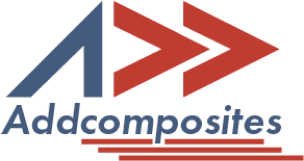
This blog explores the present state of the composites design applied with the DFM approach.
AFP - Automated Fiber Placement
DFM - Design For Manufacturing
AFP manufacturing process kinematics, process parameters, and gathered data from the process are constantly used to optimize the design of the part, Contrary to other composites layup processes where the laminates are made either by complete sheets or by continuous processes, AFP works like true Additive manufacturing technology, enabling the placement of right material in the right shape, orientation, etc. This leads to a solution space that is very vast for a manual designer to explore. Thus generative designs that is constrained by AFP process limitation populate the solution space. Selecting the most suitable solution and producing it a few times, can provide an infinite improvement loop from the process data, [Link]
The cost/weight optimization framework works by accounting for the material consumption and process time, it is trying to find tradeoffs between the structural
performance of a component and its manufacturing cost. The methodology is aimed to be used in the preliminary design phase; thus, the output of the optimization is neither detailed manufacturing documentation nor a ply book. The introduction of a draping model in this phase is rather a way to
After the mechanical characterization of the CFRP material, it is possible to calibrate the numerical material model, to properly design and perform experimental tests on
thin-walled tubular structures. The simplified tested model is later extended to the conical crash component. In such cases, manufacturing is always assumed to be hand layup work [Link]. A similar approach is also touted by commercial designers as well in the automotive industry [Link].
Optimization of manufacturing cost, NDT cost, and the weight formed by a simplified version of the direct operating cost. It's a very academic framework and is very rarely used in commercial operations. [Link]
The DFM method developed is focusing on efforts in the first phase of the product development process called preliminary product development. There are six stages in the implementation of the DFM method [Link]
This approach mainly relies on having CATIA software in-house. A simplified process overview is shown in the video here. Essentially a serialized approach to design i.e. Shape design -> material assignment -> manufacturability; ignores the benefits of composites tailorability and treats the composites design as a sheet metal design. This limits the exploration capability of the user to draw strip-by-strip the part and draw with the limitation of the provided suit. Siemens offers a similar suit called Fibersim, following a similar design philosophy these suits try to provide a complete workflow. The key dropback is the high cost and rigidity in the design philosophy,
The approach is used to ensure requirements/specifications are met while at the same time reducing risk by demonstrating material equivalency between successive layers. That is, at each scale, the part behavior can be described or predicted from the lower scale. Simply put, the materials and structures on the aircraft behave as expected from the lab-scale tests. This can be subdivided into chemical, physical, and mechanical perspectives: for example, is the degree of cure the same, is the volume fraction the same, is the compressive strength the same. As large-scale testing is particularly expensive, the idea is to minimize the number of large-scale tests by increasing the number of cheaper, coupon-level tests. [Link]
Addcomposites is the provider of the Automated Fiber Placement (AFP) ecosystem - including the Fiber Placement System (AFP-XS), 3D Simulation and Programming Software (AddPath), and Robotic Cells (AddCell). With the leasing program for the AFP system (AFPnext), composites manufacturers can work with thermosets, thermoplastics, dry fiber placement, or in combination with 3D Printers on a monthly basis.
This blog explores the present state of the composites design applied with the DFM approach.
AFP - Automated Fiber Placement
DFM - Design For Manufacturing
AFP manufacturing process kinematics, process parameters, and gathered data from the process are constantly used to optimize the design of the part, Contrary to other composites layup processes where the laminates are made either by complete sheets or by continuous processes, AFP works like true Additive manufacturing technology, enabling the placement of right material in the right shape, orientation, etc. This leads to a solution space that is very vast for a manual designer to explore. Thus generative designs that is constrained by AFP process limitation populate the solution space. Selecting the most suitable solution and producing it a few times, can provide an infinite improvement loop from the process data, [Link]
The cost/weight optimization framework works by accounting for the material consumption and process time, it is trying to find tradeoffs between the structural
performance of a component and its manufacturing cost. The methodology is aimed to be used in the preliminary design phase; thus, the output of the optimization is neither detailed manufacturing documentation nor a ply book. The introduction of a draping model in this phase is rather a way to
After the mechanical characterization of the CFRP material, it is possible to calibrate the numerical material model, to properly design and perform experimental tests on
thin-walled tubular structures. The simplified tested model is later extended to the conical crash component. In such cases, manufacturing is always assumed to be hand layup work [Link]. A similar approach is also touted by commercial designers as well in the automotive industry [Link].
Optimization of manufacturing cost, NDT cost, and the weight formed by a simplified version of the direct operating cost. It's a very academic framework and is very rarely used in commercial operations. [Link]
The DFM method developed is focusing on efforts in the first phase of the product development process called preliminary product development. There are six stages in the implementation of the DFM method [Link]
This approach mainly relies on having CATIA software in-house. A simplified process overview is shown in the video here. Essentially a serialized approach to design i.e. Shape design -> material assignment -> manufacturability; ignores the benefits of composites tailorability and treats the composites design as a sheet metal design. This limits the exploration capability of the user to draw strip-by-strip the part and draw with the limitation of the provided suit. Siemens offers a similar suit called Fibersim, following a similar design philosophy these suits try to provide a complete workflow. The key dropback is the high cost and rigidity in the design philosophy,
The approach is used to ensure requirements/specifications are met while at the same time reducing risk by demonstrating material equivalency between successive layers. That is, at each scale, the part behavior can be described or predicted from the lower scale. Simply put, the materials and structures on the aircraft behave as expected from the lab-scale tests. This can be subdivided into chemical, physical, and mechanical perspectives: for example, is the degree of cure the same, is the volume fraction the same, is the compressive strength the same. As large-scale testing is particularly expensive, the idea is to minimize the number of large-scale tests by increasing the number of cheaper, coupon-level tests. [Link]
Addcomposites is the provider of the Automated Fiber Placement (AFP) ecosystem - including the Fiber Placement System (AFP-XS), 3D Simulation and Programming Software (AddPath), and Robotic Cells (AddCell). With the leasing program for the AFP system (AFPnext), composites manufacturers can work with thermosets, thermoplastics, dry fiber placement, or in combination with 3D Printers on a monthly basis.