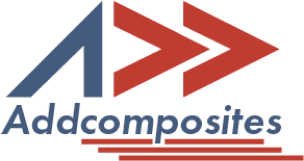
Several industries, such as automotive and aerospace, today rely heavily on high-throughput automated composite manufacturing. The article reviews the present state of the art in automated composite manufacturing methods. focusing on methods and materials manufacturing possibilities.
Composites are used for many applications in the aerospace and automotive industry due to their high specific strength. Traditional manufacturing methods for composites are labor intensive and it is increasingly becoming difficult to find experienced workers for the manual layup. Even a highly trained technician lays about 1 to 1.5 kg of composite material per hour; making this approach highly localized and unscalable. For this particular reason, most of the hand layup work has moved to low-cost countries.
In order to bring the benefit of high composites structures to the masses an automated manufacturing approach is needed that relies on
Though there are many methods to create composites, not all are suited for high-volume output automation. Injection molding is good for a large number of parts, but customization of the parts is costly due to the need for dedicated molds. The optimum production capacity for composite manufacturing methods is given the increasing level of automation. As can be noticed there is huge potential in the 10,000-50,000 parts processes to provide customized high-volume products.
The potential identified above can be exploited with additive manufacturing techniques of the past combined with recent advancements. The manufacturing of composites lends itself to additive manufacturing because of the use of layer-by-layer addition of continuous fiber materials, which are easily shaped through a substrate and robotic motion. Currently, the industrial composite production process makes use of prepreg tapes or narrower, tows to create a part. These processes leverage the existing automation of robotic arms or low-cost gantry systems with programmable motion and sensor controls to meticulously place composite tapes and tows to fabricate a specific part structure. All of these processes make use of continuous fibers dry or impregnated with matrices. Matrices could be of plastic, ceramic, or metallic nature.
Filament Winding is an automatic method to create axisymmetrically as well as some non-axisymmetric parts (i.e. pipe bends) by winding continuous fiber rovings or tapes around a rotating substrate (axisymmetric / non-axisymmetric).
Dry Filament Winding may use dry fibers passed through a series of creels, grouping the fibers by passing them through a textile board or comb, pulling the grouped fibers through the winding eye, and wrapping it around the closed-shaped mandrel. For an open tube winding, additional pins at the end of the mandrel can be used to provide the necessary anchoring point. This approach allows for the RTM style infusion process later, allowing for a faster production rate and near net shape outer surface.
Wet Filament Winding may use dry fibers passed through a series of creels, grouping the fibers by passing them through a textile board or comb, and pulling the grouped fibers through a resin bath before finally passing it through a winding eye/comb and wrapping it around the closed shaped mandrel. At the end of the winding cycle, a compaction tape is wounded with additional pressure to squeeze out access resin and provide a smooth finish.
Towpreg Filament Winding uses prepreg tows that are passed through a series of creels, grouping under higher tension before finally passing it through a winding eye/comb and wrapping it around the closed-shaped mandrel. Much higher consistency is achieved with fiber volume fraction as the tow preg ensures very high consistency of the impregnation.
All of the above winding approaches can be considered a bit traditional, as they all use thermoset resin in one or the other forms. However, they lack the recyclability of the used material. Recent material innovation may soon enable the above techniques to also become sustainable i.e. Vitrimus or Elium resin by Arkema.
With much higher processing temperatures, thermoplastic tape winding processes require thermoplastic prepreg tapes and high energy heating sources i.e., laser or flash lamp, or humm3. Using a similar setup a thermoplastic AFP head can be converted to place thermoplastic tapes onto the mandrel.
for further details about Filament winding please look into
Using an ATL machine, prepreg tapes or continuous fabric strips with widths ranging from 75-300 mm are laid onto flat surfaces in a variety of orientations. ATL machines store material spools on the head so they can be used during production. ATL machines typically have tape spools, winders, winder guides, compaction rollers, tape cutters, and a position sensor at their heads. An articulating robot can be used to hold the machine's head.
By using a soft silicone roller, a starting amount of prepreg tape is deposited on the mold. The machine then deposits the tape as defined by fiber paths. At the end of layup, the tape is automatically cut by rotating or pinching blades. The speed at which the machine cuts the tape depends on the complexity of the part. To create non-flat structures, a second forming step is used to shape the laminate sheet of an ATL laminate. ATL is an efficient way to manufacture large noncomplex parts.
It is important to note that if the curvature of the laminate is too large, it tends to warp and buckle during the forming process. Buckling is heavily influenced by prepreg tackiness and tow width, according to analysis. The way to combat buckling is to enforce a minimum turning radius of the machine depending on the material and tow width being used.
With controlled tension and compaction pressure, AFP places tow or slit tape from 3.625 to 25.4 mm (0.325'' to 1''). AFP can place dry fiber, thermoset, and thermoplastic materials. AFP uses individual control, which allows for stopping, cutting, and restarting each tow during placement. Using individual tow control, each tow is laid at its own speed, allowing the material to be deposited along a radius. A variable width part can be created by stopping individual tows and changing the width of the tape.
New compact AFP systems that can support 10,000 parts/year production are now becoming highly accessible due to the lower cost of robotic arms and open-access software like AddPath. This enables every composites manufacturer to own an automated system on monthly basis, to enable automation alongside the existing workforce.
ATL layup system combined with an ultrasonic cutter and robotic pick-and-place technique using a single robotic arm creates composite laminates with near-net shape and places them in the Thermoforming/RTM molds for further curing/forming. These techniques enable higher throughput production for gentle geometric shapes.
Tailored Fiber Placement (TFP) is an embroidery-based tow-steering process that enables complete control over fiber placement and directionality in a composite preform. During the process, continuous tow is stitched to a backing material using numerical control. Several fibrous materials like carbon, glass, basalt, aramid, natural, thermo-plastic, ceramic fibers, or metallic threads can be placed in a near-net shape on a carrier material by TFP.
An interesting evolution of the Liquid Deposition Modeling approach is represented by UV-assisted 3D (UV-3D) printing, in which the feed material is constituted by photo-cross-linkable resin systems that can be cured at room temperature right after exiting the extrusion nozzle by means of UV-light irradiation. Several examples of successful fabrication of 3D objects by means of UV-3D printing have appeared in the past few years. (Source)
Long-fiber sheets of carbon or fiberglass are fed into the printer. Layered shapes from CAD slices are printed onto the fiber sheets using clear fluid and thermal inkjet technology. High-performance polymer powder is applied to the fiber sheet adhering to the printing fluid. Sheets are stacked then heated to the melting point of the polymer and compressed to consolidate the part to the designed height. Through a mechanical or chemical process, unbonded portions of sheet fibers are removed, revealing the final part. (Source)
Material extrusion composite additive manufacturing can be divided into two major subsections, depending on the feed material used: (1) thermoplastic material and (2) thermosetting resin. For thermoplastic materials, a heated nozzle melts the polymer-fiber blend and deposits it onto a surface. The thermosetting resin is less commonly used as an additive manufacturing material but is rapidly gaining favor in additive manufacturing because of the resin’s strength and toughness
Structural Continuous Fiber Printing requires new and innovative approaches to satisfy the key characteristic. To understand these processes, a set of terminology is explained below. The reader must keep this in mind that these are not exclusive and can be combined in innovative ways, let's get into it [Source]
Dry fiber is fed into the nozzle while a matrix material is injected through one or more inflows during deposition by co-extrusion. The matrix is thus introduced, heated, and in-situ impregnates the fiber before being deposited.
Instead of dry fiber, towpreg/thin prepreg tape is fed into the nozzle, heated, and co-extruded with the additional matrix material. Typically, the matrix in the towpreg is identical to that in the co-extrusion.
The towpreg input is heated and extruded without any additional material.
A compact thermoplastic automated fiber placement (AFP) where the input thermoplastic towpreg/prepreg tape is consolidated in-situ when deposited. The feedstock is heated by an external energy source at the nozzle during the feeding process and is then placed and consolidated by a pressure roller during deposition.
The fiber is impregnated while it is transported into the print head, similar to 3D filament winding. As with towpreg extrusion, the deposition takes place via a nozzle.
The opportunity of composites is about 2-3 times higher than that of the metallic application. The processes mentioned above are constantly increasing in their productivity/cost; just in the last decade the cost to perform has improved by 10 times and the innovation in material and software are yet to show their impact on the market.
As the material innovation in room temperature thermosets is eliminating the need for cold storage and transportation and higher shelf life/reduced material wastage, This will lower the raw material cost by 2-3x while reducing waste. In addition, with improved consumption, we expect the material form factor for the above-mentioned system to become extremely cost-effective over the coming years.
With marginally zero cost of computation and improved digital twin planning software (e.g. Addpath), the processes are expected to become more digitized, help reduce the scrape rate and quality issues, eliminating the need for a paper trail and lengthy meetings. Overall we can expect to see As the system improvements in productivity, the input material will likely go lower in cost by a healthy 3x-5x depending on the volumetric increase.
Do you want to learn more about how AFP can help your business thrive? Request a demo or collaboration with Pravin Luthada or James Kuligoski via LinkedIn today.
Addcomposites is the provider of the Automated Fiber Placement (AFP) ecosystem - including the Fiber Placement System (AFP-XS), 3D Simulation and Programming Software (AddPath), and Robotic Cells (AddCell). With the leasing program for the AFP system (AFPnext), composites manufacturers can work with thermosets, thermoplastics, dry fiber placement, or in combination with 3D Printers on a monthly basis.
Several industries, such as automotive and aerospace, today rely heavily on high-throughput automated composite manufacturing. The article reviews the present state of the art in automated composite manufacturing methods. focusing on methods and materials manufacturing possibilities.
Composites are used for many applications in the aerospace and automotive industry due to their high specific strength. Traditional manufacturing methods for composites are labor intensive and it is increasingly becoming difficult to find experienced workers for the manual layup. Even a highly trained technician lays about 1 to 1.5 kg of composite material per hour; making this approach highly localized and unscalable. For this particular reason, most of the hand layup work has moved to low-cost countries.
In order to bring the benefit of high composites structures to the masses an automated manufacturing approach is needed that relies on
Though there are many methods to create composites, not all are suited for high-volume output automation. Injection molding is good for a large number of parts, but customization of the parts is costly due to the need for dedicated molds. The optimum production capacity for composite manufacturing methods is given the increasing level of automation. As can be noticed there is huge potential in the 10,000-50,000 parts processes to provide customized high-volume products.
The potential identified above can be exploited with additive manufacturing techniques of the past combined with recent advancements. The manufacturing of composites lends itself to additive manufacturing because of the use of layer-by-layer addition of continuous fiber materials, which are easily shaped through a substrate and robotic motion. Currently, the industrial composite production process makes use of prepreg tapes or narrower, tows to create a part. These processes leverage the existing automation of robotic arms or low-cost gantry systems with programmable motion and sensor controls to meticulously place composite tapes and tows to fabricate a specific part structure. All of these processes make use of continuous fibers dry or impregnated with matrices. Matrices could be of plastic, ceramic, or metallic nature.
Filament Winding is an automatic method to create axisymmetrically as well as some non-axisymmetric parts (i.e. pipe bends) by winding continuous fiber rovings or tapes around a rotating substrate (axisymmetric / non-axisymmetric).
Dry Filament Winding may use dry fibers passed through a series of creels, grouping the fibers by passing them through a textile board or comb, pulling the grouped fibers through the winding eye, and wrapping it around the closed-shaped mandrel. For an open tube winding, additional pins at the end of the mandrel can be used to provide the necessary anchoring point. This approach allows for the RTM style infusion process later, allowing for a faster production rate and near net shape outer surface.
Wet Filament Winding may use dry fibers passed through a series of creels, grouping the fibers by passing them through a textile board or comb, and pulling the grouped fibers through a resin bath before finally passing it through a winding eye/comb and wrapping it around the closed shaped mandrel. At the end of the winding cycle, a compaction tape is wounded with additional pressure to squeeze out access resin and provide a smooth finish.
Towpreg Filament Winding uses prepreg tows that are passed through a series of creels, grouping under higher tension before finally passing it through a winding eye/comb and wrapping it around the closed-shaped mandrel. Much higher consistency is achieved with fiber volume fraction as the tow preg ensures very high consistency of the impregnation.
All of the above winding approaches can be considered a bit traditional, as they all use thermoset resin in one or the other forms. However, they lack the recyclability of the used material. Recent material innovation may soon enable the above techniques to also become sustainable i.e. Vitrimus or Elium resin by Arkema.
With much higher processing temperatures, thermoplastic tape winding processes require thermoplastic prepreg tapes and high energy heating sources i.e., laser or flash lamp, or humm3. Using a similar setup a thermoplastic AFP head can be converted to place thermoplastic tapes onto the mandrel.
for further details about Filament winding please look into
Using an ATL machine, prepreg tapes or continuous fabric strips with widths ranging from 75-300 mm are laid onto flat surfaces in a variety of orientations. ATL machines store material spools on the head so they can be used during production. ATL machines typically have tape spools, winders, winder guides, compaction rollers, tape cutters, and a position sensor at their heads. An articulating robot can be used to hold the machine's head.
By using a soft silicone roller, a starting amount of prepreg tape is deposited on the mold. The machine then deposits the tape as defined by fiber paths. At the end of layup, the tape is automatically cut by rotating or pinching blades. The speed at which the machine cuts the tape depends on the complexity of the part. To create non-flat structures, a second forming step is used to shape the laminate sheet of an ATL laminate. ATL is an efficient way to manufacture large noncomplex parts.
It is important to note that if the curvature of the laminate is too large, it tends to warp and buckle during the forming process. Buckling is heavily influenced by prepreg tackiness and tow width, according to analysis. The way to combat buckling is to enforce a minimum turning radius of the machine depending on the material and tow width being used.
With controlled tension and compaction pressure, AFP places tow or slit tape from 3.625 to 25.4 mm (0.325'' to 1''). AFP can place dry fiber, thermoset, and thermoplastic materials. AFP uses individual control, which allows for stopping, cutting, and restarting each tow during placement. Using individual tow control, each tow is laid at its own speed, allowing the material to be deposited along a radius. A variable width part can be created by stopping individual tows and changing the width of the tape.
New compact AFP systems that can support 10,000 parts/year production are now becoming highly accessible due to the lower cost of robotic arms and open-access software like AddPath. This enables every composites manufacturer to own an automated system on monthly basis, to enable automation alongside the existing workforce.
ATL layup system combined with an ultrasonic cutter and robotic pick-and-place technique using a single robotic arm creates composite laminates with near-net shape and places them in the Thermoforming/RTM molds for further curing/forming. These techniques enable higher throughput production for gentle geometric shapes.
Tailored Fiber Placement (TFP) is an embroidery-based tow-steering process that enables complete control over fiber placement and directionality in a composite preform. During the process, continuous tow is stitched to a backing material using numerical control. Several fibrous materials like carbon, glass, basalt, aramid, natural, thermo-plastic, ceramic fibers, or metallic threads can be placed in a near-net shape on a carrier material by TFP.
An interesting evolution of the Liquid Deposition Modeling approach is represented by UV-assisted 3D (UV-3D) printing, in which the feed material is constituted by photo-cross-linkable resin systems that can be cured at room temperature right after exiting the extrusion nozzle by means of UV-light irradiation. Several examples of successful fabrication of 3D objects by means of UV-3D printing have appeared in the past few years. (Source)
Long-fiber sheets of carbon or fiberglass are fed into the printer. Layered shapes from CAD slices are printed onto the fiber sheets using clear fluid and thermal inkjet technology. High-performance polymer powder is applied to the fiber sheet adhering to the printing fluid. Sheets are stacked then heated to the melting point of the polymer and compressed to consolidate the part to the designed height. Through a mechanical or chemical process, unbonded portions of sheet fibers are removed, revealing the final part. (Source)
Material extrusion composite additive manufacturing can be divided into two major subsections, depending on the feed material used: (1) thermoplastic material and (2) thermosetting resin. For thermoplastic materials, a heated nozzle melts the polymer-fiber blend and deposits it onto a surface. The thermosetting resin is less commonly used as an additive manufacturing material but is rapidly gaining favor in additive manufacturing because of the resin’s strength and toughness
Structural Continuous Fiber Printing requires new and innovative approaches to satisfy the key characteristic. To understand these processes, a set of terminology is explained below. The reader must keep this in mind that these are not exclusive and can be combined in innovative ways, let's get into it [Source]
Dry fiber is fed into the nozzle while a matrix material is injected through one or more inflows during deposition by co-extrusion. The matrix is thus introduced, heated, and in-situ impregnates the fiber before being deposited.
Instead of dry fiber, towpreg/thin prepreg tape is fed into the nozzle, heated, and co-extruded with the additional matrix material. Typically, the matrix in the towpreg is identical to that in the co-extrusion.
The towpreg input is heated and extruded without any additional material.
A compact thermoplastic automated fiber placement (AFP) where the input thermoplastic towpreg/prepreg tape is consolidated in-situ when deposited. The feedstock is heated by an external energy source at the nozzle during the feeding process and is then placed and consolidated by a pressure roller during deposition.
The fiber is impregnated while it is transported into the print head, similar to 3D filament winding. As with towpreg extrusion, the deposition takes place via a nozzle.
The opportunity of composites is about 2-3 times higher than that of the metallic application. The processes mentioned above are constantly increasing in their productivity/cost; just in the last decade the cost to perform has improved by 10 times and the innovation in material and software are yet to show their impact on the market.
As the material innovation in room temperature thermosets is eliminating the need for cold storage and transportation and higher shelf life/reduced material wastage, This will lower the raw material cost by 2-3x while reducing waste. In addition, with improved consumption, we expect the material form factor for the above-mentioned system to become extremely cost-effective over the coming years.
With marginally zero cost of computation and improved digital twin planning software (e.g. Addpath), the processes are expected to become more digitized, help reduce the scrape rate and quality issues, eliminating the need for a paper trail and lengthy meetings. Overall we can expect to see As the system improvements in productivity, the input material will likely go lower in cost by a healthy 3x-5x depending on the volumetric increase.
Do you want to learn more about how AFP can help your business thrive? Request a demo or collaboration with Pravin Luthada or James Kuligoski via LinkedIn today.
Addcomposites is the provider of the Automated Fiber Placement (AFP) ecosystem - including the Fiber Placement System (AFP-XS), 3D Simulation and Programming Software (AddPath), and Robotic Cells (AddCell). With the leasing program for the AFP system (AFPnext), composites manufacturers can work with thermosets, thermoplastics, dry fiber placement, or in combination with 3D Printers on a monthly basis.