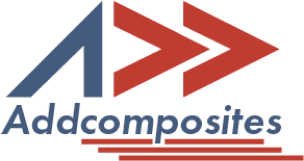
Automated Fiber Placement (AFP) has revolutionized composites manufacturing, enabling the production of complex geometries with high precision and efficiency. However, the reliance on manual inspection has become a significant bottleneck, posing challenges in quality control and production throughput. This section delves into the inherent limitations of manual inspection processes in composites manufacturing, specifically within the context of AFP operations.
Manual inspection, traditionally performed after the deposition stage, not only interrupts the manufacturing flow but also demands considerable time and resources. Studies have shown that inspection and re-work can consume up to 42% of the total build time for composite parts. This substantial percentage underscores a critical inefficiency, as non-conforming parts require reworking or, in severe defect cases, complete scrapping—resulting in significant material waste and increased production costs.
Furthermore, manual inspection methods are inherently limited by human error and the subjective assessment of defects. The intricacies of AFP-produced components, characterized by complex fiber orientations and layup sequences, exacerbate these challenges, necessitating a high level of expertise and experience from inspectors. Despite these efforts, the potential for oversight remains, which can compromise the structural integrity and performance of the final composite parts.
The discussion on manual inspection inefficiencies is not merely academic; it reflects a pressing industrial challenge that impacts the sustainability and competitiveness of composites manufacturing. The industry's move toward Industry 4.0 emphasizes the urgent need for advanced solutions that can integrate seamlessly with automated manufacturing processes, ensuring high-quality output without sacrificing efficiency.
In exploring the limitations of manual inspection in AFP, it becomes evident that innovation in real-time inspection and process control is not just beneficial but essential for the future of composites manufacturing. The subsequent sections will delve into the advancements in sensor technologies and control systems that aim to address these challenges, marking a pivotal shift towards fully automated, high-precision composite production.
The exploration of manual inspection's challenges sets the stage for understanding the critical need for advancements in AFP technology, specifically the integration of real-time defect detection and correction mechanisms. While the document provides a comprehensive overview, it also highlights the absence of detailed statistical data on the efficiency losses attributed to manual inspection, suggesting an area for future research and development within the sector.
Automated Fibre Placement (AFP) stands at the forefront of composites manufacturing technology, boasting the ability to lay down fibres with high precision across complex geometries. Yet, this advanced technique is not without its challenges. A significant hurdle in AFP manufacturing is the occurrence of deposition defects, which can compromise the integrity and performance of the final composite parts. This section delves into the nuances of detecting and correcting such defects in real-time, a critical advancement in maintaining the quality and efficiency of AFP processes.
Deposition defects in AFP, including gaps, overlaps, and wrinkles, can lead to significant material wastage and reduced structural performance. Traditionally, these defects were identified through post-process inspection, a method fraught with inefficiencies and high costs associated with rework or scrap. The manual inspection process, while thorough, significantly extends production timelines and increases the environmental footprint through waste.
The introduction of real-time detection and correction technologies represents a paradigm shift in AFP manufacturing. By integrating profilometry sensors within the AFP machinery, manufacturers can now detect defects as they occur, during the fibre placement process. These sensors, capable of high-resolution surface measurements, enable the identification of minute irregularities in the layup, which might be indicative of underlying defects.
The core advantage of real-time defect detection lies in its ability to significantly reduce, if not eliminate, the need for post-process inspection and rework. By catching defects at the moment of occurrence, the system allows for immediate correction, either through machine adjustments or operator interventions. This not only ensures that each layer of fibre is deposited flawlessly but also contributes to a leaner manufacturing process with reduced waste and higher throughput.
The integration of profilometry sensors and software control systems represents a significant technological leap towards optimizing the composite manufacturing process. This integration is pivotal for enhancing the accuracy, reliability, and overall efficiency of AFP, addressing the critical challenges posed by deposition defects and manual inspection inefficiencies.
The AFP process, while highly automated and precise, is susceptible to various types of defects, such as gaps, overlaps, and wrinkles in the fiber layup. These defects not only undermine the structural integrity of the composite material but also contribute to increased waste and production costs due to the need for rework or part rejection. Traditional methods of defect detection, primarily reliant on post-process inspection, introduce delays and inefficiencies into the manufacturing cycle.
The introduction of profilometry sensors into the AFP machine architecture marks a transformative approach to overcoming these challenges. Profilometry, a technique for measuring the surface topography, enables the real-time detection of anomalies in the fiber deposition process. These high-resolution sensors can accurately capture the width, thickness, and even the texture of the fiber as it is laid down, providing invaluable data for assessing the quality of the layup.
Coupled with advanced software control systems, the data from profilometry sensors can be analyzed in real time to identify potential defects as they occur. This immediate feedback loop allows for the dynamic adjustment of process parameters, such as compaction force, deposition speed, and heating temperature, to correct detected anomalies before they propagate through subsequent layers of the composite material. Such capabilities significantly reduce the likelihood of defects that could compromise the part's structural integrity and performance.
Moreover, this integrated system facilitates a deeper understanding of the AFP process by providing detailed data on the material behavior and machine performance during deposition. This insight can be leveraged to refine the process further, optimizing the parameters for enhanced quality and efficiency based on empirical evidence rather than trial and error.
Implementing profilometry sensors and software control in AFP machines does not merely address the issue of defect detection and correction. It represents a shift towards more intelligent manufacturing practices, where data-driven decision-making and automation converge to produce high-quality composite materials at reduced costs and environmental impact. The continuous improvement and integration of such technologies are vital for maintaining competitiveness in the rapidly evolving field of composites manufacturing. AddPath is one of the very first AFP digital twin software to offer integration of sensors natively in the planning and monitoring of the data. Read more here
The integration of advanced profilometry sensors and sophisticated software control within AFP machines is a game-changer in composite manufacturing. This innovation doesn't just push the envelope—it completely redefines the boundaries of manufacturing efficiency, quality, and environmental responsibility. Here, we delve into the transformative impact of real-time process control in AFP, a technological leap forward that significantly enhances production rates while minimizing waste.
Even minor deposition defects can lead to significant material wastage and compromise the structural integrity of composite materials. Traditional methods, reliant on post-process inspection, are fraught with inefficiencies, often requiring extensive rework or resulting in increased scrap rates. However, with the advent of real-time process control, the landscape of composite manufacturing is undergoing a radical transformation.
By employing profilometry sensors, AFP machines can now detect anomalies in fiber placement as they occur. This real-time detection capability is coupled with dynamic software control systems that instantly adjust process parameters, correcting potential defects before they propagate through the material. This not only ensures a dramatic reduction in defect rates but also significantly enhances the overall quality of the final product.
The practical implications of this technological advancement are profound. Manufacturers can now achieve higher production rates, thanks to the reduction in downtime associated with manual inspections and rework. Furthermore, the precise control and efficiency offered by real-time process control lead to a substantial decrease in material waste, aligning composite manufacturing processes more closely with sustainability goals.
Moreover, the economic benefits of implementing real-time process control are equally compelling. By streamlining the manufacturing process and reducing the incidence of defects, companies can realize significant cost savings. Less waste and rework translate directly into lower production costs, improving profitability while also enhancing the environmental footprint of manufacturing operations.
We'd like to extend our deepest gratitude to Duc H. Nguyen, Xiaochuan Sun, Iryna Tretiak, Mario A. Valverde, and James Kratz for their invaluable contributions to the field of AFP technology. Their pioneering work, as detailed in the study "Automatic process control of an automated fibre placement machine," marks a significant advancement in composite manufacturing technology. Their dedication and innovative approach have provided critical insights and practical solutions that promise to enhance the efficiency, quality, and sustainability of composite production. We are truly inspired by their achievements and look forward to seeing the continued impact of their research on the industry.
Discover the future of composite manufacturing with Addcomposites! Here's how you can get involved:
At Addcomposites, we are dedicated to revolutionizing composite manufacturing. Our AFP systems and comprehensive support services are waiting for you to harness. So, don't wait – get started on your journey to the future of manufacturing today!
Automated Fiber Placement (AFP) has revolutionized composites manufacturing, enabling the production of complex geometries with high precision and efficiency. However, the reliance on manual inspection has become a significant bottleneck, posing challenges in quality control and production throughput. This section delves into the inherent limitations of manual inspection processes in composites manufacturing, specifically within the context of AFP operations.
Manual inspection, traditionally performed after the deposition stage, not only interrupts the manufacturing flow but also demands considerable time and resources. Studies have shown that inspection and re-work can consume up to 42% of the total build time for composite parts. This substantial percentage underscores a critical inefficiency, as non-conforming parts require reworking or, in severe defect cases, complete scrapping—resulting in significant material waste and increased production costs.
Furthermore, manual inspection methods are inherently limited by human error and the subjective assessment of defects. The intricacies of AFP-produced components, characterized by complex fiber orientations and layup sequences, exacerbate these challenges, necessitating a high level of expertise and experience from inspectors. Despite these efforts, the potential for oversight remains, which can compromise the structural integrity and performance of the final composite parts.
The discussion on manual inspection inefficiencies is not merely academic; it reflects a pressing industrial challenge that impacts the sustainability and competitiveness of composites manufacturing. The industry's move toward Industry 4.0 emphasizes the urgent need for advanced solutions that can integrate seamlessly with automated manufacturing processes, ensuring high-quality output without sacrificing efficiency.
In exploring the limitations of manual inspection in AFP, it becomes evident that innovation in real-time inspection and process control is not just beneficial but essential for the future of composites manufacturing. The subsequent sections will delve into the advancements in sensor technologies and control systems that aim to address these challenges, marking a pivotal shift towards fully automated, high-precision composite production.
The exploration of manual inspection's challenges sets the stage for understanding the critical need for advancements in AFP technology, specifically the integration of real-time defect detection and correction mechanisms. While the document provides a comprehensive overview, it also highlights the absence of detailed statistical data on the efficiency losses attributed to manual inspection, suggesting an area for future research and development within the sector.
Automated Fibre Placement (AFP) stands at the forefront of composites manufacturing technology, boasting the ability to lay down fibres with high precision across complex geometries. Yet, this advanced technique is not without its challenges. A significant hurdle in AFP manufacturing is the occurrence of deposition defects, which can compromise the integrity and performance of the final composite parts. This section delves into the nuances of detecting and correcting such defects in real-time, a critical advancement in maintaining the quality and efficiency of AFP processes.
Deposition defects in AFP, including gaps, overlaps, and wrinkles, can lead to significant material wastage and reduced structural performance. Traditionally, these defects were identified through post-process inspection, a method fraught with inefficiencies and high costs associated with rework or scrap. The manual inspection process, while thorough, significantly extends production timelines and increases the environmental footprint through waste.
The introduction of real-time detection and correction technologies represents a paradigm shift in AFP manufacturing. By integrating profilometry sensors within the AFP machinery, manufacturers can now detect defects as they occur, during the fibre placement process. These sensors, capable of high-resolution surface measurements, enable the identification of minute irregularities in the layup, which might be indicative of underlying defects.
The core advantage of real-time defect detection lies in its ability to significantly reduce, if not eliminate, the need for post-process inspection and rework. By catching defects at the moment of occurrence, the system allows for immediate correction, either through machine adjustments or operator interventions. This not only ensures that each layer of fibre is deposited flawlessly but also contributes to a leaner manufacturing process with reduced waste and higher throughput.
The integration of profilometry sensors and software control systems represents a significant technological leap towards optimizing the composite manufacturing process. This integration is pivotal for enhancing the accuracy, reliability, and overall efficiency of AFP, addressing the critical challenges posed by deposition defects and manual inspection inefficiencies.
The AFP process, while highly automated and precise, is susceptible to various types of defects, such as gaps, overlaps, and wrinkles in the fiber layup. These defects not only undermine the structural integrity of the composite material but also contribute to increased waste and production costs due to the need for rework or part rejection. Traditional methods of defect detection, primarily reliant on post-process inspection, introduce delays and inefficiencies into the manufacturing cycle.
The introduction of profilometry sensors into the AFP machine architecture marks a transformative approach to overcoming these challenges. Profilometry, a technique for measuring the surface topography, enables the real-time detection of anomalies in the fiber deposition process. These high-resolution sensors can accurately capture the width, thickness, and even the texture of the fiber as it is laid down, providing invaluable data for assessing the quality of the layup.
Coupled with advanced software control systems, the data from profilometry sensors can be analyzed in real time to identify potential defects as they occur. This immediate feedback loop allows for the dynamic adjustment of process parameters, such as compaction force, deposition speed, and heating temperature, to correct detected anomalies before they propagate through subsequent layers of the composite material. Such capabilities significantly reduce the likelihood of defects that could compromise the part's structural integrity and performance.
Moreover, this integrated system facilitates a deeper understanding of the AFP process by providing detailed data on the material behavior and machine performance during deposition. This insight can be leveraged to refine the process further, optimizing the parameters for enhanced quality and efficiency based on empirical evidence rather than trial and error.
Implementing profilometry sensors and software control in AFP machines does not merely address the issue of defect detection and correction. It represents a shift towards more intelligent manufacturing practices, where data-driven decision-making and automation converge to produce high-quality composite materials at reduced costs and environmental impact. The continuous improvement and integration of such technologies are vital for maintaining competitiveness in the rapidly evolving field of composites manufacturing. AddPath is one of the very first AFP digital twin software to offer integration of sensors natively in the planning and monitoring of the data. Read more here
The integration of advanced profilometry sensors and sophisticated software control within AFP machines is a game-changer in composite manufacturing. This innovation doesn't just push the envelope—it completely redefines the boundaries of manufacturing efficiency, quality, and environmental responsibility. Here, we delve into the transformative impact of real-time process control in AFP, a technological leap forward that significantly enhances production rates while minimizing waste.
Even minor deposition defects can lead to significant material wastage and compromise the structural integrity of composite materials. Traditional methods, reliant on post-process inspection, are fraught with inefficiencies, often requiring extensive rework or resulting in increased scrap rates. However, with the advent of real-time process control, the landscape of composite manufacturing is undergoing a radical transformation.
By employing profilometry sensors, AFP machines can now detect anomalies in fiber placement as they occur. This real-time detection capability is coupled with dynamic software control systems that instantly adjust process parameters, correcting potential defects before they propagate through the material. This not only ensures a dramatic reduction in defect rates but also significantly enhances the overall quality of the final product.
The practical implications of this technological advancement are profound. Manufacturers can now achieve higher production rates, thanks to the reduction in downtime associated with manual inspections and rework. Furthermore, the precise control and efficiency offered by real-time process control lead to a substantial decrease in material waste, aligning composite manufacturing processes more closely with sustainability goals.
Moreover, the economic benefits of implementing real-time process control are equally compelling. By streamlining the manufacturing process and reducing the incidence of defects, companies can realize significant cost savings. Less waste and rework translate directly into lower production costs, improving profitability while also enhancing the environmental footprint of manufacturing operations.
We'd like to extend our deepest gratitude to Duc H. Nguyen, Xiaochuan Sun, Iryna Tretiak, Mario A. Valverde, and James Kratz for their invaluable contributions to the field of AFP technology. Their pioneering work, as detailed in the study "Automatic process control of an automated fibre placement machine," marks a significant advancement in composite manufacturing technology. Their dedication and innovative approach have provided critical insights and practical solutions that promise to enhance the efficiency, quality, and sustainability of composite production. We are truly inspired by their achievements and look forward to seeing the continued impact of their research on the industry.
Discover the future of composite manufacturing with Addcomposites! Here's how you can get involved:
At Addcomposites, we are dedicated to revolutionizing composite manufacturing. Our AFP systems and comprehensive support services are waiting for you to harness. So, don't wait – get started on your journey to the future of manufacturing today!