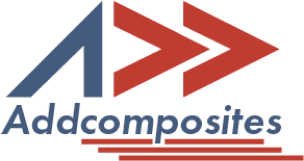
This blog describes a development project to evaluate the efficiency and benefits of automated fiber placement technology through the design, prototyping, and testing of composite bars. Discussions focus on the concept of “design-for-manufacturing” and provide an overview of the process going through selecting project objectives, material choices, processes and compensations, engineering and structural considerations, and the set of parts and accessories.
Recurring costs have become an important factor in helicopter design, and although composite materials are widely used in aircraft parts, in many cases, manual manufacturing processes impede profitability. Automatic manufacturing techniques can not only reduce production costs but can also provide repeatable, high-quality parts, digital traceability of defects, lower worker costs and help achieve higher production rates helping lower the cost even further. The introduction of automation in industrial processes affects not only how parts are manufactured, but also how they are designed.
As discussed in the previous design guide "steps in the process flow of designing the composites part", the first step is to Set out a program objective, In this conceptual design phase, the selected criteria are as follows
Design constraints related to customer satisfaction include the number of man-hours, downtime, and specialized tooling associated with scheduled and unscheduled maintenance and part replacement. The composite tailboom was evaluated at scheduled “gates” by customer support representatives to highlight and debate maintainability issues throughout the evolution of the design.
The airframe structure can account for as much as 25% of the non-recurring cost of a typical commercial light helicopter, and manufacturing cost is a primary driver for the design of aerospace structures. Two main approaches
A typical business case based on sales per calendar year for the introduction of this kind of component into the commercial helicopter market can justify a significant non-recurring. A compact AFP solution on a monthly subscription plan with high material and shape flexibility is chosen to reduce the significant non-recurring cost. Additionally, flexibility with material enables the production of ready blanks of dry per-form, thermoset prepregs for complex geometries hand layups.
Reducing the total number of parts by either combining parts into one or deleting the unnecessary component. A thorough analysis of all the parts that can be combined into a single part is done and an example of such is shown in the image below
The weight of a composite tailboom is driven by two major factors. The first is the need to satisfy electrical wiring, avionics shielding, current return, HIRF, and lightning strike requirements.
The other important influence on structural weight is associated with structural and fatigue design criteria. Compared to metallic airframe design, composite have a very high fatigue tolerance. The lack of data for the tailboom fatigue test may require extensive testing of the produced prototype.
Automated manufacturing processes, such as AFP, used to require design and analysis engineers to develop and orient the design specifically for AFP. However, now with the advent of open access software for AFP planning and simulation, the process has become extremely simple.
A CAD model of a tailboom approx 3-4 m in length and less than 0.5 m in diameter is drawn as an example here. If the starting point is a metallic structure with holes and other sub-assemblies the work of building mold becomes more tediuos as it requires cleaning up of the provided part. In order to make cleaner mold following points are proposed to clear a tool design:
Planning the layup on a 3D mold shape has been made very simple and accessible thanks to AddPath. A step-by-step process of planning via AddPath is depicted in the picture below. The process also allows user to define their own paths by simply drawing a curve in the chosen CAD modeling software and importing it.
Simulating the process via 3D Programming Software - AddPath is very critical to make sure the following items are being met without error:
AddPath allows for modification of mold position to optimize the planned layup placement, thus enabling the part to be optimally designed. Below is the video showcasing the simulation in the finalized position.
This case study can be downloaded from the AddPath repository
Key learning from the simulation
- Fiber steering is under the limit of given fiber width-GSM combinations
- Time and estimated material for creating a business case for the production/pricing
- Overlap/ gaps analysis for the certain fiber orientations and performing right width of AFP with ply drop strategies
The AFP tailboom is designed as a one-piece cone in order to provide an optimum surface of revolution for efficient AFP processing. The resulting one-piece tailboom skin structure requires a different philosophy for manufacturing and assembly. The tailboom's internal structure consists of 6 full frames fastened to the inside of the tailboom skin.
IML tooling (shown in the picture below) for the tailboom cone provides a tool-controlled surface on the interior of the part.
1. Design for Manufacturing – One-Piece, FibrePlaced Composite Helicopter Tailboom
This blog describes a development project to evaluate the efficiency and benefits of automated fiber placement technology through the design, prototyping, and testing of composite bars. Discussions focus on the concept of “design-for-manufacturing” and provide an overview of the process going through selecting project objectives, material choices, processes and compensations, engineering and structural considerations, and the set of parts and accessories.
Recurring costs have become an important factor in helicopter design, and although composite materials are widely used in aircraft parts, in many cases, manual manufacturing processes impede profitability. Automatic manufacturing techniques can not only reduce production costs but can also provide repeatable, high-quality parts, digital traceability of defects, lower worker costs and help achieve higher production rates helping lower the cost even further. The introduction of automation in industrial processes affects not only how parts are manufactured, but also how they are designed.
As discussed in the previous design guide "steps in the process flow of designing the composites part", the first step is to Set out a program objective, In this conceptual design phase, the selected criteria are as follows
Design constraints related to customer satisfaction include the number of man-hours, downtime, and specialized tooling associated with scheduled and unscheduled maintenance and part replacement. The composite tailboom was evaluated at scheduled “gates” by customer support representatives to highlight and debate maintainability issues throughout the evolution of the design.
The airframe structure can account for as much as 25% of the non-recurring cost of a typical commercial light helicopter, and manufacturing cost is a primary driver for the design of aerospace structures. Two main approaches
A typical business case based on sales per calendar year for the introduction of this kind of component into the commercial helicopter market can justify a significant non-recurring. A compact AFP solution on a monthly subscription plan with high material and shape flexibility is chosen to reduce the significant non-recurring cost. Additionally, flexibility with material enables the production of ready blanks of dry per-form, thermoset prepregs for complex geometries hand layups.
Reducing the total number of parts by either combining parts into one or deleting the unnecessary component. A thorough analysis of all the parts that can be combined into a single part is done and an example of such is shown in the image below
The weight of a composite tailboom is driven by two major factors. The first is the need to satisfy electrical wiring, avionics shielding, current return, HIRF, and lightning strike requirements.
The other important influence on structural weight is associated with structural and fatigue design criteria. Compared to metallic airframe design, composite have a very high fatigue tolerance. The lack of data for the tailboom fatigue test may require extensive testing of the produced prototype.
Automated manufacturing processes, such as AFP, used to require design and analysis engineers to develop and orient the design specifically for AFP. However, now with the advent of open access software for AFP planning and simulation, the process has become extremely simple.
A CAD model of a tailboom approx 3-4 m in length and less than 0.5 m in diameter is drawn as an example here. If the starting point is a metallic structure with holes and other sub-assemblies the work of building mold becomes more tediuos as it requires cleaning up of the provided part. In order to make cleaner mold following points are proposed to clear a tool design:
Planning the layup on a 3D mold shape has been made very simple and accessible thanks to AddPath. A step-by-step process of planning via AddPath is depicted in the picture below. The process also allows user to define their own paths by simply drawing a curve in the chosen CAD modeling software and importing it.
Simulating the process via 3D Programming Software - AddPath is very critical to make sure the following items are being met without error:
AddPath allows for modification of mold position to optimize the planned layup placement, thus enabling the part to be optimally designed. Below is the video showcasing the simulation in the finalized position.
This case study can be downloaded from the AddPath repository
Key learning from the simulation
- Fiber steering is under the limit of given fiber width-GSM combinations
- Time and estimated material for creating a business case for the production/pricing
- Overlap/ gaps analysis for the certain fiber orientations and performing right width of AFP with ply drop strategies
The AFP tailboom is designed as a one-piece cone in order to provide an optimum surface of revolution for efficient AFP processing. The resulting one-piece tailboom skin structure requires a different philosophy for manufacturing and assembly. The tailboom's internal structure consists of 6 full frames fastened to the inside of the tailboom skin.
IML tooling (shown in the picture below) for the tailboom cone provides a tool-controlled surface on the interior of the part.
1. Design for Manufacturing – One-Piece, FibrePlaced Composite Helicopter Tailboom