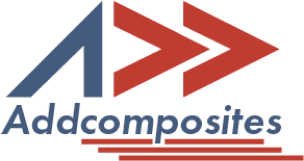
The 1960s were a Golden Age for composites manufacturing. The ongoing Space Race between the USA and USSR required innovative solutions to make the most advanced and safest space-bound structures. Considerable funding on both sides was put into R&D for these structures, and a unique manufacturing method of composites was created: automated tape laying (ATL). Since then, it grew in popularity in the space and military sectors. The so-called tapes were wide rolls of thermoset prepreg, capable of laying up 1-, 2-, and even 3-meter wide sections at a time. As great as it was, it did have some downsides, which are being realized more and more today.
Figure 1. Automated Tape Laying (ATL) Process
Using the wide rolls in ATL created considerable amounts of waste, but when beating the other guys was the only thing that mattered, material efficiency wasn't a priority. Nowadays, reducing manufacturing waste in composites is a main topic of research, and the way to achieve material savings is through using narrower tapes, or fibers.
In the 1980s, suppliers started taking their wide rolls of material and began "slitting" them into many smaller widths, now known as "slit tapes". This allowed for tapered sections to be laid up, creating a near-net-shape preform. Thermoset carbon fiber prepregs were the material of choice for this process, but this started to change. The common widths for these slit tapes are 1/4" (6.35mm), 1/2" (12.7mm), and 1" (25.4mm).
Figure 2. Automated Fiber Placement (AFP) Process
Thermoplastic material suppliers quickly recognized their materials might also be used in the same ways if machine technology could be adapted. This improves material savings further since the thermoplastic can be melted away and separated from the fibers, allowing for reusability. Popularity in this field of research has been continuously growing for the past couple of years, with the promise of being the material of tomorrow.
As 3D printing became commonplace in manufacturing for more industrial applications, 3D printing with continuous fiber has found its niche in structural components. Today, there is a slew of technology aiming toward achieving a higher fiber volume fraction, faster print of larger structures, or low-cost equipment to make composites more mainstream.
Figure 3. Materials Extrusion
As technology is constantly evolving, we start to see more of a combination of technologies. A good example of hybridization is the system from Electroimpact. They performed thermoplastic AFP layup on a 3D printed mold, within the same cell using the same system. This is a step-change in manufacturing efficiency, as the same system can 3D print a mold, then create a carbon fiber part from that mold.
Figure 3. Hybridization in composites manufacturing
On a smaller scale, this same process can be achieved by combining systems. Desktop 3D printers are becoming larger, and are more capable of producing accurate components. These components can be treated as a substrate on which thermoplastic tapes can be laid as a reinforcement. Addcomposites is one of the only companies that can offer a fiber placement system on this scale, that would be strategic to implement this method.
Let's provide a real example from a growing industry that has to make these types of decisions regularly: air mobility.
James, a product engineer, needs to choose manufacturing technology for the production of the door that consists of different components: door panels, handles, and the mechanism that will allow automatic opening/closing.
Figure 4. Formative, Subtractive, and Additive Manufacturing
As the air mobility company is just getting off the ground, the production quantity needed will remain under 1000 parts per/year, and the design will likely change frequently as changes are made for various reasons. In order to make the smartest decision for his company, James has to take many considerations into account.
Both production technologies have their pros and cons. Assuming both approaches would meet the criteria, then it comes down to the cost and time of implementing each system. The AFP (Thermoset) on easily 3D printable molds is the most effective solution for the door panel application for a number of reasons, one of which is that the mold will be able to be reused cure after cure, further saving costs.
For manufacturing the door handles, Yen could choose the 3D printing of the handles, then layup a few layers of reinforcing thermoplastic fiber to further increase strength. For the hinges or other mechanisms, Yen could choose the continuous fiber 3D printing option, creating strong and complex geometries, albeit at a slower rate.
Addcomposites is the provider of the Automated Fiber Placement (AFP) ecosystem - including the Fiber Placement System (AFP-XS), 3D Simulation and Programming Software (AddPath), and Robotic Cells (AddCell). With the leasing program for the AFP system (AFPnext), composites manufacturers can work with thermosets, thermoplastics, dry fiber placement, or in combination with 3D Printers on a monthly basis.
The 1960s were a Golden Age for composites manufacturing. The ongoing Space Race between the USA and USSR required innovative solutions to make the most advanced and safest space-bound structures. Considerable funding on both sides was put into R&D for these structures, and a unique manufacturing method of composites was created: automated tape laying (ATL). Since then, it grew in popularity in the space and military sectors. The so-called tapes were wide rolls of thermoset prepreg, capable of laying up 1-, 2-, and even 3-meter wide sections at a time. As great as it was, it did have some downsides, which are being realized more and more today.
Figure 1. Automated Tape Laying (ATL) Process
Using the wide rolls in ATL created considerable amounts of waste, but when beating the other guys was the only thing that mattered, material efficiency wasn't a priority. Nowadays, reducing manufacturing waste in composites is a main topic of research, and the way to achieve material savings is through using narrower tapes, or fibers.
In the 1980s, suppliers started taking their wide rolls of material and began "slitting" them into many smaller widths, now known as "slit tapes". This allowed for tapered sections to be laid up, creating a near-net-shape preform. Thermoset carbon fiber prepregs were the material of choice for this process, but this started to change. The common widths for these slit tapes are 1/4" (6.35mm), 1/2" (12.7mm), and 1" (25.4mm).
Figure 2. Automated Fiber Placement (AFP) Process
Thermoplastic material suppliers quickly recognized their materials might also be used in the same ways if machine technology could be adapted. This improves material savings further since the thermoplastic can be melted away and separated from the fibers, allowing for reusability. Popularity in this field of research has been continuously growing for the past couple of years, with the promise of being the material of tomorrow.
As 3D printing became commonplace in manufacturing for more industrial applications, 3D printing with continuous fiber has found its niche in structural components. Today, there is a slew of technology aiming toward achieving a higher fiber volume fraction, faster print of larger structures, or low-cost equipment to make composites more mainstream.
Figure 3. Materials Extrusion
As technology is constantly evolving, we start to see more of a combination of technologies. A good example of hybridization is the system from Electroimpact. They performed thermoplastic AFP layup on a 3D printed mold, within the same cell using the same system. This is a step-change in manufacturing efficiency, as the same system can 3D print a mold, then create a carbon fiber part from that mold.
Figure 3. Hybridization in composites manufacturing
On a smaller scale, this same process can be achieved by combining systems. Desktop 3D printers are becoming larger, and are more capable of producing accurate components. These components can be treated as a substrate on which thermoplastic tapes can be laid as a reinforcement. Addcomposites is one of the only companies that can offer a fiber placement system on this scale, that would be strategic to implement this method.
Let's provide a real example from a growing industry that has to make these types of decisions regularly: air mobility.
James, a product engineer, needs to choose manufacturing technology for the production of the door that consists of different components: door panels, handles, and the mechanism that will allow automatic opening/closing.
Figure 4. Formative, Subtractive, and Additive Manufacturing
As the air mobility company is just getting off the ground, the production quantity needed will remain under 1000 parts per/year, and the design will likely change frequently as changes are made for various reasons. In order to make the smartest decision for his company, James has to take many considerations into account.
Both production technologies have their pros and cons. Assuming both approaches would meet the criteria, then it comes down to the cost and time of implementing each system. The AFP (Thermoset) on easily 3D printable molds is the most effective solution for the door panel application for a number of reasons, one of which is that the mold will be able to be reused cure after cure, further saving costs.
For manufacturing the door handles, Yen could choose the 3D printing of the handles, then layup a few layers of reinforcing thermoplastic fiber to further increase strength. For the hinges or other mechanisms, Yen could choose the continuous fiber 3D printing option, creating strong and complex geometries, albeit at a slower rate.
Addcomposites is the provider of the Automated Fiber Placement (AFP) ecosystem - including the Fiber Placement System (AFP-XS), 3D Simulation and Programming Software (AddPath), and Robotic Cells (AddCell). With the leasing program for the AFP system (AFPnext), composites manufacturers can work with thermosets, thermoplastics, dry fiber placement, or in combination with 3D Printers on a monthly basis.