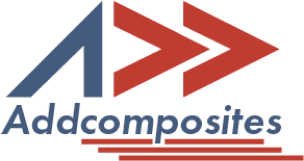
The compact AFP-XS upgrades any pre-existing robot into advanced Automated Fiber Placement systems. It is capable to achieve accurate layups over diverse materials with aerospace-grade quality production.
Read MoreThe robust, multi-tow AFP-X system — built for high-volume production, packed with increased material capacity and advanced sensors. Ensures continuous, precise operations, optimizing throughput for complex aerospace and large components.
Read MoreThe SCF3D creates functional components with enhanced structural integrity using Structural Continuous Fiber 3D printing. Produces stronger parts with less material, perfect for manufacturers revolutionizing production.
Read MoreAddPath streamlines AFP process with its user-friendly platform, offering sophisticated path planning, simulation, and data streaming to optimize fiber placement and control, enhancing efficiency and precision for all team sizes.
Read MoreAddPrint revolutionizes continuous fiber 3D printing with its expert interface, offering optimized path planning, simulation, data streaming, and advanced features for precise and efficient production, suitable for all team sizes.
Read MoreAddCell delivers tailored robotic cell solutions that seamlessly integrate with your AFP or printing system. Collaborate with our technical experts to design an optimized cell layout tailored to your specific needs, from research institutes to OEMs.
Read MoreAdaptable filament winding system for Towpreg, Thermoset, Thermoplastic, Dry fiber materials. Configurable as Filament Winding or AFP System, optimizing production speed, precision, and accuracy for pressure vessels, sleeves, and inserts.
Read MoreTailored Composite Solutions for Diverse Industry Demands
How AFP-X is Changing Automotive Manufacturing.