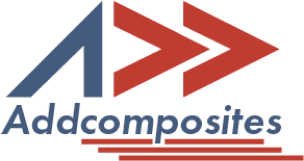
High-pressure tanks (250 bar) have been used safely in compressed natural gas vehicles for many years. Improved versions of these tanks made of high-strength composite materials are now used to store hydrogen at higher pressures (350 and 700 bar) to achieve a greater range in hydrogen-fueled mobility. High-pressure hydrogen tanks are designed not to rupture and are held to rigorous performance requirements. This article summarizes major regulations, codes, and standards in different aspects of hydrogen tank storage. The article further dives into the testing and certification process of hydrogen tanks.
There has been extensive work evaluating regulations, codes, and standards (RCS) for the emerging fuel cell market, such as the infrastructure required to support fuel cell electric vehicles. However, there has not been a similar RCS evaluation and development process for these larger systems. This section highlights the key ideas behind RCS.
The below images indicate the major RCS used in different use case scenarios. Marine and railway have yet to finalize any major RCS that can be used, but it is anticipated that they are more likely to also follow the EC79/EU406.
Over the last decade, the international hydrogen community has worked hard to develop codes and standards for onboard gaseous hydrogen storage composite tanks. Currently, there are multiple available regulations and codes applicable to composite hydrogen tanks as mentioned in the previous section. The following is a list of the tests required for the qualification of hydrogen tanks, with the most significant in tests of safety highlighted in boldface:
A hydrostatic burst test is conducted to determine the burst pressure of the tank. The determination of the burst pressure (BP) is critical for the composite tank’s safety and reliability. It is a primary and most important qualification test for a hydrogen tank. Minimum values of the burst pressure ratio for different types of fibers are listed in the table below.
The flame exposure test is performed to evaluate the ability of the hydrogen tank to withstand exposure to fire. The temperature profile for the fire exposure test according to UN GTR 13 is shown in the figure below, and the test procedure is as follows:
The cyclic test or the performance durability test of hydrogen storage containers is performed according to the figure above c,d. Three containers must be hydraulically pressurized for 22,000 cycles or until a leak occurs at (20+/-5) ◦C to 125 percent NWP (+2/ -0 MPa) without breakage. Considering a service life of 15 years, leakage must be prevented within 11,000 cycles. Only one container is evaluated if the pressure cycle life measurements are greater than 11,000 cycles or if they are all within 25% of one another. If not, three containers should be examined. Further details can be found in R134CE.
In the unlikely case that an advanced composite tank leaks, it can be removed from service without incident. It is highly unlikely that these tanks will fail in a way that will directly endanger the occupants of a hydrogen-fueled vehicle. These tanks have remained intact in collisions and in vehicle fires, and, when tested after such events, have passed various pressure tests under flame exposure. In case of vehicle fires or events in which a fire from another vehicle may engulf the tank, the tank's pressure relief device is activated when the temperature of the tank exceeds a set point (typically 102°C). When the pressure relief device is activated, the hydrogen gas in the tank is released in a safe manner.
Additional standards are being developed and validated (SAE J2579, ISO 15869) to further improve and validate safety standards for high-pressure hydrogen tanks. Vehicle manufacturers (domestic and foreign) are working closely together with tank manufacturers and others to develop robust test procedures to ensure the safety of the tanks and the entire vehicle.
The above article is part of the course Design and Development of Compressed Hydrogen Storage Tanks. The course covers a lot more, starting with discussing challenges in material selection and manufacturing practices, as well as cutting-edge trends being explored. Key problems in the design and analysis of the hydrogen reservoir are also addressed. Finally, testing and certification requirements are discussed as they play an important role in industry acceptance.
High-pressure tanks (250 bar) have been used safely in compressed natural gas vehicles for many years. Improved versions of these tanks made of high-strength composite materials are now used to store hydrogen at higher pressures (350 and 700 bar) to achieve a greater range in hydrogen-fueled mobility. High-pressure hydrogen tanks are designed not to rupture and are held to rigorous performance requirements. This article summarizes major regulations, codes, and standards in different aspects of hydrogen tank storage. The article further dives into the testing and certification process of hydrogen tanks.
There has been extensive work evaluating regulations, codes, and standards (RCS) for the emerging fuel cell market, such as the infrastructure required to support fuel cell electric vehicles. However, there has not been a similar RCS evaluation and development process for these larger systems. This section highlights the key ideas behind RCS.
The below images indicate the major RCS used in different use case scenarios. Marine and railway have yet to finalize any major RCS that can be used, but it is anticipated that they are more likely to also follow the EC79/EU406.
Over the last decade, the international hydrogen community has worked hard to develop codes and standards for onboard gaseous hydrogen storage composite tanks. Currently, there are multiple available regulations and codes applicable to composite hydrogen tanks as mentioned in the previous section. The following is a list of the tests required for the qualification of hydrogen tanks, with the most significant in tests of safety highlighted in boldface:
A hydrostatic burst test is conducted to determine the burst pressure of the tank. The determination of the burst pressure (BP) is critical for the composite tank’s safety and reliability. It is a primary and most important qualification test for a hydrogen tank. Minimum values of the burst pressure ratio for different types of fibers are listed in the table below.
The flame exposure test is performed to evaluate the ability of the hydrogen tank to withstand exposure to fire. The temperature profile for the fire exposure test according to UN GTR 13 is shown in the figure below, and the test procedure is as follows:
The cyclic test or the performance durability test of hydrogen storage containers is performed according to the figure above c,d. Three containers must be hydraulically pressurized for 22,000 cycles or until a leak occurs at (20+/-5) ◦C to 125 percent NWP (+2/ -0 MPa) without breakage. Considering a service life of 15 years, leakage must be prevented within 11,000 cycles. Only one container is evaluated if the pressure cycle life measurements are greater than 11,000 cycles or if they are all within 25% of one another. If not, three containers should be examined. Further details can be found in R134CE.
In the unlikely case that an advanced composite tank leaks, it can be removed from service without incident. It is highly unlikely that these tanks will fail in a way that will directly endanger the occupants of a hydrogen-fueled vehicle. These tanks have remained intact in collisions and in vehicle fires, and, when tested after such events, have passed various pressure tests under flame exposure. In case of vehicle fires or events in which a fire from another vehicle may engulf the tank, the tank's pressure relief device is activated when the temperature of the tank exceeds a set point (typically 102°C). When the pressure relief device is activated, the hydrogen gas in the tank is released in a safe manner.
Additional standards are being developed and validated (SAE J2579, ISO 15869) to further improve and validate safety standards for high-pressure hydrogen tanks. Vehicle manufacturers (domestic and foreign) are working closely together with tank manufacturers and others to develop robust test procedures to ensure the safety of the tanks and the entire vehicle.
The above article is part of the course Design and Development of Compressed Hydrogen Storage Tanks. The course covers a lot more, starting with discussing challenges in material selection and manufacturing practices, as well as cutting-edge trends being explored. Key problems in the design and analysis of the hydrogen reservoir are also addressed. Finally, testing and certification requirements are discussed as they play an important role in industry acceptance.