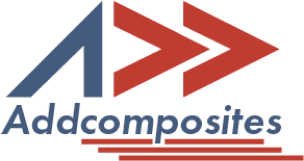
Composites typically comprise a polymer material and a reinforcing material, like continuous fiber. The composite material offers higher strength and stiffness compared to non-reinforced polymers due to the presence of fiber, the polymer plays the role of the stress distribution medium. Continuous fiber ensures the load is distributed across the length without a weak point.
The matrix has a key role to play as a structural member in transferring the load between the fiber.
In order to be able to do that, the polymer should be
As the fiber is the most critical member taking the load, you aiming to maximize the percentage of fiber in given composites.
A theoretical maximum for fiber is 66.66% but for some of the best composites structures any range between 60-65% is considered ideal.
Automated Fiber Placement (AFP) is the additive manufacturing process that uses fiber-polymer tape as input and the AFP head places this fiber-polymer tapes with the help of heat and pressure.
This process can result in additively manufactured parts that are two times stronger than steel at one-fifth of the weight (which is excellent); however, the technology traditionally requires million-dollar AFP systems (which is not great).
Addcomposites has recently launched its new AFP-XS platform, which utilizes a technology they call “plug-n-produce” automated fiber placement (AFP-XS), which radically reduces the structure and cost of the typical AFP process.
Fiber printing refers to the extrusion technologies where a fiber-polymer filament is heated and extruded in an X-Y plane.
The extrusion technologies have a layer to layer bonding issues as there is no pressure applied at the end of each layer. However, the pointed tip enables much more complex part production.
First, it is essential to understand that base materials are "mixed" to create these composite materials. Almost all the materials used in this process are a blend of fiber elements, for example, carbon fiber or fiberglass and a polymer such as nylon, PEEK, or PEKK. The Fiber platform allows for the blending of these materials in a machine that is small enough and safe enough to use in an office setting.
What are they and how do they differ? Each process has its strengths and weaknesses. We will dive into them and provide insight on which one you should choose for your specific application. Let's get started!
While choosing a technology for your futuristic manufacturing needs, polymer-based additive manufacturing (3D printing) is oftentimes one of the most obvious choices. However, despite their ubiquitous presence and low cost, the technology is still finding its place in the dog-eat-dog world of manufacturing.
The main challenge has been the degradation of the 3D printed part over its lifetime, and its structural strength when compared to conventional processes. In order to address this, one of the most interesting developments in 3D printing has been the advent of composites (fiber-reinforced) 3D printing. The key here is to combine the high-strength, lightweight composites with low-cost, rapid 3D printing manufacturing.
An alternative method of digitized production of composites, which has been gaining popularity only recently, is called Automated Fiber Placement (FP). This method was developed in the 1970s, primarily for producing aerospace structural parts. This meant that the capability to repeatedly produce aerospace-grade parts far outweighed the overall cost, leading to each system costing millions of dollars in acquisition alone.
Given the difference in the cost and operational flexibility of 3D printing and AFP, it is worth exploring the validity of composite 3D printing for your needs.
The purpose of this article is to bring the differences between composite 3D printing and AFP processes to light, so let's start with briefly defining the technologies.
A single plan layer of melted material reinforced with fiber is extruded onto a flat mold surface. The two main categories we will focus on are short fiber and continuous fiber.
Short fiber printing uses individual sections of fiber, creating a part with decent overall strength, but not great in any one direction. This is similar to creating parts with chopped strand mat glass.
Continuous fiber printing uses long fibers that are similar to unidirectional (UD) sheets, and provide excellent strength in tension. The differences are shown below.
Whereas in 3D printing the material is extruded, tape laying works by pulling strips of tape (usually unidirectional) along a surface, where complexity is determined by the tool's capabilities.
The tapes can be either pre-impregnated with resin or dry, which are pulled from the laying tool, then heated and pressed onto the shaped mold. There are two main categories here as well: tapes using either thermoset resin or thermoplastic resin.
Thermoset resin is the most common type of matrix material used today and is primarily used in aerospace, automotive, or marine applications. Thermoplastic is gaining popularity due to recyclability and development in its strength and is mainly used for pipes in the oil and gas industry.
The difference in the fundamental approach to producing fiber reinforced plastic (FRP) components using these processes creates unique results. The table below indicates the key advantages and disadvantages of these two methods.
While each of these technologies uses the same principle of additive manufacturing, they are very different from each other.
Neither technology is great at everything, and each provides unique use cases. So how do you know which one to choose?
We need to look into the existing market solutions and determine which suits your needs better.
Given the history of each technology, they were predetermined to which industry and applications would be most suitable. Read more about the history of automated fiber placement and 3D printing.
Given the history of AFP, it makes sense that this technology has proven use cases in space, aerospace, and defense applications. Since this article is not focused on providing specific use cases, this page of CompositesWorld provides excellent examples.
The main idea is that AFP has been tested and proven in the most rigorous environments; from fighter jets to wind turbine blades. Well if it's so great, why isn't everyone employing AFP, you ask?
The main drawback, and it's a big one, is the associated costs. You can expect to spend upwards of a million USD on just the system alone, never mind facility upgrades needed to support such a large system.
With those numbers, it just isn't feasible for SMEs, the backbone of manufacturing, to purchase.
Addcomposites has created a plug-n-play tool head that is easily mounted onto any existing manufacturing robotic arm.
With the popular assumption that most future factories would employ robots and automation, this tool head can be moved around anywhere in the facility without disturbing ongoing production.
The subscription-based model, with its low monthly payments, greatly reduces the main challenge of high acquisition costs, while maintaining the quality standards expected of tape laying systems.
Basic 3D printing has been around since the early 1980s, but we're not talking about that today. For a more in-depth look at 3D printing history and technology, visit this PC Guide article.
Fast forward to 2013, when the first carbon fiber 3D printer was developed by Markforged, and we are just beginning to talk about printing carbon fiber on a mass scale today. Despite them being the first, and currently the biggest, company to do this, they have decided to transition away from composite 3D printing and turn their attention towards metallic 3D printing.
The assumption to be made here is that the listed use cases by Markforged could not be expanded to the conventional composites markets or products. This isn't to say that there won't be parts designed specifically using this technology in the future, as CompositesWorld summarizes very well.
Since this technology is still in its early stages, it remains to be seen how the new 3D printing technologies would be able to merge with the matured process of AFP, to create an accessible advanced manufacturing solution
Choosing between these two capable and exciting technologies can be a daunting task, and requires a clear set of goals based on many different variables. In the next article, we will declutter the approach for selecting the correct futuristic production technology for your needs.
Addcomposites is the provider of the Automated Fiber Placement (AFP) system. The AFP system can be rented on a monthly basis to work with thermosets, thermoplastic, dry fiber placement, or in combination with 3d printers.
Composites typically comprise a polymer material and a reinforcing material, like continuous fiber. The composite material offers higher strength and stiffness compared to non-reinforced polymers due to the presence of fiber, the polymer plays the role of the stress distribution medium. Continuous fiber ensures the load is distributed across the length without a weak point.
The matrix has a key role to play as a structural member in transferring the load between the fiber.
In order to be able to do that, the polymer should be
As the fiber is the most critical member taking the load, you aiming to maximize the percentage of fiber in given composites.
A theoretical maximum for fiber is 66.66% but for some of the best composites structures any range between 60-65% is considered ideal.
Automated Fiber Placement (AFP) is the additive manufacturing process that uses fiber-polymer tape as input and the AFP head places this fiber-polymer tapes with the help of heat and pressure.
This process can result in additively manufactured parts that are two times stronger than steel at one-fifth of the weight (which is excellent); however, the technology traditionally requires million-dollar AFP systems (which is not great).
Addcomposites has recently launched its new AFP-XS platform, which utilizes a technology they call “plug-n-produce” automated fiber placement (AFP-XS), which radically reduces the structure and cost of the typical AFP process.
Fiber printing refers to the extrusion technologies where a fiber-polymer filament is heated and extruded in an X-Y plane.
The extrusion technologies have a layer to layer bonding issues as there is no pressure applied at the end of each layer. However, the pointed tip enables much more complex part production.
First, it is essential to understand that base materials are "mixed" to create these composite materials. Almost all the materials used in this process are a blend of fiber elements, for example, carbon fiber or fiberglass and a polymer such as nylon, PEEK, or PEKK. The Fiber platform allows for the blending of these materials in a machine that is small enough and safe enough to use in an office setting.
What are they and how do they differ? Each process has its strengths and weaknesses. We will dive into them and provide insight on which one you should choose for your specific application. Let's get started!
While choosing a technology for your futuristic manufacturing needs, polymer-based additive manufacturing (3D printing) is oftentimes one of the most obvious choices. However, despite their ubiquitous presence and low cost, the technology is still finding its place in the dog-eat-dog world of manufacturing.
The main challenge has been the degradation of the 3D printed part over its lifetime, and its structural strength when compared to conventional processes. In order to address this, one of the most interesting developments in 3D printing has been the advent of composites (fiber-reinforced) 3D printing. The key here is to combine the high-strength, lightweight composites with low-cost, rapid 3D printing manufacturing.
An alternative method of digitized production of composites, which has been gaining popularity only recently, is called Automated Fiber Placement (FP). This method was developed in the 1970s, primarily for producing aerospace structural parts. This meant that the capability to repeatedly produce aerospace-grade parts far outweighed the overall cost, leading to each system costing millions of dollars in acquisition alone.
Given the difference in the cost and operational flexibility of 3D printing and AFP, it is worth exploring the validity of composite 3D printing for your needs.
The purpose of this article is to bring the differences between composite 3D printing and AFP processes to light, so let's start with briefly defining the technologies.
A single plan layer of melted material reinforced with fiber is extruded onto a flat mold surface. The two main categories we will focus on are short fiber and continuous fiber.
Short fiber printing uses individual sections of fiber, creating a part with decent overall strength, but not great in any one direction. This is similar to creating parts with chopped strand mat glass.
Continuous fiber printing uses long fibers that are similar to unidirectional (UD) sheets, and provide excellent strength in tension. The differences are shown below.
Whereas in 3D printing the material is extruded, tape laying works by pulling strips of tape (usually unidirectional) along a surface, where complexity is determined by the tool's capabilities.
The tapes can be either pre-impregnated with resin or dry, which are pulled from the laying tool, then heated and pressed onto the shaped mold. There are two main categories here as well: tapes using either thermoset resin or thermoplastic resin.
Thermoset resin is the most common type of matrix material used today and is primarily used in aerospace, automotive, or marine applications. Thermoplastic is gaining popularity due to recyclability and development in its strength and is mainly used for pipes in the oil and gas industry.
The difference in the fundamental approach to producing fiber reinforced plastic (FRP) components using these processes creates unique results. The table below indicates the key advantages and disadvantages of these two methods.
While each of these technologies uses the same principle of additive manufacturing, they are very different from each other.
Neither technology is great at everything, and each provides unique use cases. So how do you know which one to choose?
We need to look into the existing market solutions and determine which suits your needs better.
Given the history of each technology, they were predetermined to which industry and applications would be most suitable. Read more about the history of automated fiber placement and 3D printing.
Given the history of AFP, it makes sense that this technology has proven use cases in space, aerospace, and defense applications. Since this article is not focused on providing specific use cases, this page of CompositesWorld provides excellent examples.
The main idea is that AFP has been tested and proven in the most rigorous environments; from fighter jets to wind turbine blades. Well if it's so great, why isn't everyone employing AFP, you ask?
The main drawback, and it's a big one, is the associated costs. You can expect to spend upwards of a million USD on just the system alone, never mind facility upgrades needed to support such a large system.
With those numbers, it just isn't feasible for SMEs, the backbone of manufacturing, to purchase.
Addcomposites has created a plug-n-play tool head that is easily mounted onto any existing manufacturing robotic arm.
With the popular assumption that most future factories would employ robots and automation, this tool head can be moved around anywhere in the facility without disturbing ongoing production.
The subscription-based model, with its low monthly payments, greatly reduces the main challenge of high acquisition costs, while maintaining the quality standards expected of tape laying systems.
Basic 3D printing has been around since the early 1980s, but we're not talking about that today. For a more in-depth look at 3D printing history and technology, visit this PC Guide article.
Fast forward to 2013, when the first carbon fiber 3D printer was developed by Markforged, and we are just beginning to talk about printing carbon fiber on a mass scale today. Despite them being the first, and currently the biggest, company to do this, they have decided to transition away from composite 3D printing and turn their attention towards metallic 3D printing.
The assumption to be made here is that the listed use cases by Markforged could not be expanded to the conventional composites markets or products. This isn't to say that there won't be parts designed specifically using this technology in the future, as CompositesWorld summarizes very well.
Since this technology is still in its early stages, it remains to be seen how the new 3D printing technologies would be able to merge with the matured process of AFP, to create an accessible advanced manufacturing solution
Choosing between these two capable and exciting technologies can be a daunting task, and requires a clear set of goals based on many different variables. In the next article, we will declutter the approach for selecting the correct futuristic production technology for your needs.
Addcomposites is the provider of the Automated Fiber Placement (AFP) system. The AFP system can be rented on a monthly basis to work with thermosets, thermoplastic, dry fiber placement, or in combination with 3d printers.