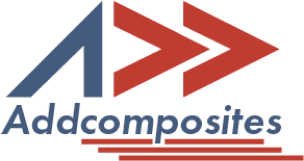
Additive manufacturing is quickly becoming the desirable method of manufacturing, but what is it? And what technologies are classified as additive manufacturing?
In a nutshell, additive manufacturing (AM) is any manufacturing process that creates a part by adding material, layer by layer.
Additive manufacturing is the opposite concept of subtractive manufacturing (think machining: the material is removed from the stock during processing to create the final part), where AM begins from nothing to create the final part.
AM usually involves the use of CAD, some form of automation to perform the work, and the input of layering material. Not all AM uses automation to create parts, however, as there is one industry that predates today's definition of additive manufacturing: composites!
The most common AM process is Fused Deposition Molding (FDM), commonly called 3D printing, where a printer lays subsequent layers of plastic on top of the previous one. Many different types of FDM manufacturing are available, as shown below.
This is commonly thought of as the only type of AM available, but technological advances have been increasing the capabilities of AM throughout many different industries, including composites.
Additive manufacturing in composites is a seemingly new concept when compared to general FDM, which is widely available nowadays.
This article provides more in-depth information on AM. There are three main AM technologies used in composite production:
FDM (Markforged)
CF3D Printing (Continuous Composites) / CFM (Moi Composites)
That's right, FDM isn't just for desktop projects anymore! Although this is the newest AM technology in composites, it is easiest to relate to.
This method uses strands of fiber and molten resin, acting in a similar fashion to the 3D printers everyone knows and loves.
This excels in producing complex shapes but is rather slows. It is ideal for creating complex prototypes or for limited production of very specific shapes.
Automated tape laying (ATL) is perhaps the most common form of advanced additive manufacturing in composites.
Introduced in the 1980s, it has been mainly contained within the Space, Aerospace, and Defense sectors due to the very high cost of implementation.
Generally, ATL is the ideal process for large and relatively simple aircraft structures such as fuselages and wings.
A variation of ATL is automated fiber placement (AFP). AFP is very similar to the concept of ATL; to the point where both terms are often used interchangeably.
The main difference between the two technologies is that ATL uses tapes (think packaging tape at the post office) whereas AFP uses multiple tows.
The tows are pre-impregnated with epoxy resin, much narrow than tapes (≤ 8mm), and lay down between 12 and 32 tows at a time. AFP is the new technology in composites and is in between ATL and FDM in terms of part complexity and deposition rates.
Depending on your application, the article Additive Manufacturing: Tape Laying or 3D Printing? provides insight on the basics and technicalities of how to decide which one to incorporate into your facility.
The key insight of the article is that despite all the benefits tape laying provides, a large majority of SMEs and even R&D centers do not have access to this technology.
In order to address this situation, Addcomposites has developed the smallest, most compact tape laying/fiber placement system available. The cost of entry and implementation is reduced drastically by offering a subscription-based approach for the AFP-XS.
This is possible thanks to the plug-and-play nature of the tool head to small, pre-existing robotic arms making it easy to install and uninstall. Request a quick demo here.
Now that you have a basic understanding of the recent advanced additive manufacturing technologies used in composites, you have the difficult task of determining which is right for your facility.
But don't worry, we have some pointers to guide you in your journey. Don't forget to evaluate all your options, and reach out to us to evaluate your ATL/AFP application needs at zero evaluation cost!
Addcomposites is the provider of the Automated Fiber Placement (AFP) system. The AFP system can be rented on a monthly basis to work with thermosets, thermoplastic, dry fiber placement, or in combination with 3d printers.
Additive manufacturing is quickly becoming the desirable method of manufacturing, but what is it? And what technologies are classified as additive manufacturing?
In a nutshell, additive manufacturing (AM) is any manufacturing process that creates a part by adding material, layer by layer.
Additive manufacturing is the opposite concept of subtractive manufacturing (think machining: the material is removed from the stock during processing to create the final part), where AM begins from nothing to create the final part.
AM usually involves the use of CAD, some form of automation to perform the work, and the input of layering material. Not all AM uses automation to create parts, however, as there is one industry that predates today's definition of additive manufacturing: composites!
The most common AM process is Fused Deposition Molding (FDM), commonly called 3D printing, where a printer lays subsequent layers of plastic on top of the previous one. Many different types of FDM manufacturing are available, as shown below.
This is commonly thought of as the only type of AM available, but technological advances have been increasing the capabilities of AM throughout many different industries, including composites.
Additive manufacturing in composites is a seemingly new concept when compared to general FDM, which is widely available nowadays.
This article provides more in-depth information on AM. There are three main AM technologies used in composite production:
FDM (Markforged)
CF3D Printing (Continuous Composites) / CFM (Moi Composites)
That's right, FDM isn't just for desktop projects anymore! Although this is the newest AM technology in composites, it is easiest to relate to.
This method uses strands of fiber and molten resin, acting in a similar fashion to the 3D printers everyone knows and loves.
This excels in producing complex shapes but is rather slows. It is ideal for creating complex prototypes or for limited production of very specific shapes.
Automated tape laying (ATL) is perhaps the most common form of advanced additive manufacturing in composites.
Introduced in the 1980s, it has been mainly contained within the Space, Aerospace, and Defense sectors due to the very high cost of implementation.
Generally, ATL is the ideal process for large and relatively simple aircraft structures such as fuselages and wings.
A variation of ATL is automated fiber placement (AFP). AFP is very similar to the concept of ATL; to the point where both terms are often used interchangeably.
The main difference between the two technologies is that ATL uses tapes (think packaging tape at the post office) whereas AFP uses multiple tows.
The tows are pre-impregnated with epoxy resin, much narrow than tapes (≤ 8mm), and lay down between 12 and 32 tows at a time. AFP is the new technology in composites and is in between ATL and FDM in terms of part complexity and deposition rates.
Depending on your application, the article Additive Manufacturing: Tape Laying or 3D Printing? provides insight on the basics and technicalities of how to decide which one to incorporate into your facility.
The key insight of the article is that despite all the benefits tape laying provides, a large majority of SMEs and even R&D centers do not have access to this technology.
In order to address this situation, Addcomposites has developed the smallest, most compact tape laying/fiber placement system available. The cost of entry and implementation is reduced drastically by offering a subscription-based approach for the AFP-XS.
This is possible thanks to the plug-and-play nature of the tool head to small, pre-existing robotic arms making it easy to install and uninstall. Request a quick demo here.
Now that you have a basic understanding of the recent advanced additive manufacturing technologies used in composites, you have the difficult task of determining which is right for your facility.
But don't worry, we have some pointers to guide you in your journey. Don't forget to evaluate all your options, and reach out to us to evaluate your ATL/AFP application needs at zero evaluation cost!
Addcomposites is the provider of the Automated Fiber Placement (AFP) system. The AFP system can be rented on a monthly basis to work with thermosets, thermoplastic, dry fiber placement, or in combination with 3d printers.