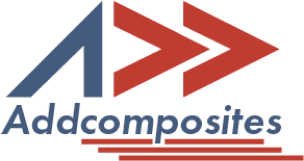
Thermoplastic Tape Winding (TTW) is a highly automated process for manufacturing tubular-like fiber-reinforced thermoplastic composites such as flywheels and pipes. One of the crucial parameters in the TTW process is the temperature of the nip point at which the incoming prepreg tape is bonded with the substrate by a compaction roller.
In thermoplastic tape filament winding, complete in-situ consolidation occurs during winding and no post-processing in the oven is required. Therefore, rolled thermoplastic parts can be processed in one production step. The inline fusion of the thermoplastic prepreg takes place instantly, in a fraction of a second, almost during a welding process. This allows for greater freedom of geometries that can be fabricated without post-processing, including flat and concave shapes. Another possible improvement involves the ability to orient the reinforcement locally. Thermoplastic consolidation avoids fiber slippage, providing stability for various winding paths beyond geodesic trajectories.
Making tanks/tubes with the conventional fiber winding process has been around for a long time, but with tape winding designers and manufacturers are offered a new level of freedom to:
For critical products like pressure vessels, it is important to assure a continuously high level of product quality also in mass production. The TTW is the exact temperature control of the nip point, which can be solved by implementing thermal sensors as shown in the image below and supporting them with model-based learning.
Moreover, the geometrical position of the tapes is very important for the component quality. Especially the positions of the tapes relative to each other are relevant to the mechanical properties of the pressure vessel. The ideal condition assumes the tapes lying in the path directly close to each other. There are mainly two irregularities from that ideal condition that can influence the further production process and therefore the mechanical properties: gaps between the tape paths and overlaps.
Gaps can cause mechanical instabilities because the material is missing in areas where it is expected to be However, there are low influences on the further process because the gap if it is not too wide.
On the other hand, overlaps of two tape paths cause uneven surface structures and are consequently able to influence the contact pressure roller and can prohibit a correct bond of the underlying tape.
These errors arise from the absolute continuous path following the accuracy of the robots caused by load variation, construction of robot arm, speed calculation delays, etc.
Like in any additive manufacturing process, the first ply in TTW is an issue due to dissimilar materials getting "bonded". For tank production using a metallic liner or soluble liners, a bonding approach should be considered. Comparing the case of hoop winding Vs. a helical Vs Axial layup slippage limitation should be considered and the planning should be done as dry filament winding.
During TTW processes, the heat is distributed between the incoming tape and the substrate. However, as light cast different shadows for different geometries, the heat energy focused on different shapes cast a different energy distribution.
Thermal management is a key factor to achieve adequate interlayer adhesion as well as full potential crystallinity in the thermoplastic matrix. One should consider reducing layup speed, increasing temperature, and longer heating time to ensure molecular diffusion.
Tape dimensions are a crucial parameter in tape winding. Obtaining a constant tape width and thickness from the supplier will enable repeatable and uniform products. However, tape dimensions also define design flexibility. For example, with an axial layup on a tubular mandrel, the tape width should be narrow enough to be compliant with the mandrel curvature.
Thermoplastic Tape Winding uses revolutionary heating technology to improve process control, and during its lifecycle, it produces fewer emissions than traditional machines. There is less waste produced in the manufacture of products on the machine. The use of thermoplastic-impregnated tape makes tanks Strong, Lightweight, and Recyclable. Improved machine-learned heating control for the specific geometric variation ensures the produced tanks are manufactured reliably with an unprecedented level of quality.
Addcomposites now offers the tape and filament winding capability for the AFP system that can work across the material line from Dry Fiber, Thermoset, and Thermoplastic. (Learn more >)
The above article is part of the course Design and Development of Compressed Hydrogen Storage Tanks. The course covers a lot more, starting with discussing challenges in material selection and manufacturing practices, as well as cutting-edge trends being explored. Key problems in the design and analysis of the hydrogen reservoir are also addressed. Finally, testing and certification requirements are discussed as they play an important role in industry acceptance.
Thermoplastic Tape Winding (TTW) is a highly automated process for manufacturing tubular-like fiber-reinforced thermoplastic composites such as flywheels and pipes. One of the crucial parameters in the TTW process is the temperature of the nip point at which the incoming prepreg tape is bonded with the substrate by a compaction roller.
In thermoplastic tape filament winding, complete in-situ consolidation occurs during winding and no post-processing in the oven is required. Therefore, rolled thermoplastic parts can be processed in one production step. The inline fusion of the thermoplastic prepreg takes place instantly, in a fraction of a second, almost during a welding process. This allows for greater freedom of geometries that can be fabricated without post-processing, including flat and concave shapes. Another possible improvement involves the ability to orient the reinforcement locally. Thermoplastic consolidation avoids fiber slippage, providing stability for various winding paths beyond geodesic trajectories.
Making tanks/tubes with the conventional fiber winding process has been around for a long time, but with tape winding designers and manufacturers are offered a new level of freedom to:
For critical products like pressure vessels, it is important to assure a continuously high level of product quality also in mass production. The TTW is the exact temperature control of the nip point, which can be solved by implementing thermal sensors as shown in the image below and supporting them with model-based learning.
Moreover, the geometrical position of the tapes is very important for the component quality. Especially the positions of the tapes relative to each other are relevant to the mechanical properties of the pressure vessel. The ideal condition assumes the tapes lying in the path directly close to each other. There are mainly two irregularities from that ideal condition that can influence the further production process and therefore the mechanical properties: gaps between the tape paths and overlaps.
Gaps can cause mechanical instabilities because the material is missing in areas where it is expected to be However, there are low influences on the further process because the gap if it is not too wide.
On the other hand, overlaps of two tape paths cause uneven surface structures and are consequently able to influence the contact pressure roller and can prohibit a correct bond of the underlying tape.
These errors arise from the absolute continuous path following the accuracy of the robots caused by load variation, construction of robot arm, speed calculation delays, etc.
Like in any additive manufacturing process, the first ply in TTW is an issue due to dissimilar materials getting "bonded". For tank production using a metallic liner or soluble liners, a bonding approach should be considered. Comparing the case of hoop winding Vs. a helical Vs Axial layup slippage limitation should be considered and the planning should be done as dry filament winding.
During TTW processes, the heat is distributed between the incoming tape and the substrate. However, as light cast different shadows for different geometries, the heat energy focused on different shapes cast a different energy distribution.
Thermal management is a key factor to achieve adequate interlayer adhesion as well as full potential crystallinity in the thermoplastic matrix. One should consider reducing layup speed, increasing temperature, and longer heating time to ensure molecular diffusion.
Tape dimensions are a crucial parameter in tape winding. Obtaining a constant tape width and thickness from the supplier will enable repeatable and uniform products. However, tape dimensions also define design flexibility. For example, with an axial layup on a tubular mandrel, the tape width should be narrow enough to be compliant with the mandrel curvature.
Thermoplastic Tape Winding uses revolutionary heating technology to improve process control, and during its lifecycle, it produces fewer emissions than traditional machines. There is less waste produced in the manufacture of products on the machine. The use of thermoplastic-impregnated tape makes tanks Strong, Lightweight, and Recyclable. Improved machine-learned heating control for the specific geometric variation ensures the produced tanks are manufactured reliably with an unprecedented level of quality.
Addcomposites now offers the tape and filament winding capability for the AFP system that can work across the material line from Dry Fiber, Thermoset, and Thermoplastic. (Learn more >)
The above article is part of the course Design and Development of Compressed Hydrogen Storage Tanks. The course covers a lot more, starting with discussing challenges in material selection and manufacturing practices, as well as cutting-edge trends being explored. Key problems in the design and analysis of the hydrogen reservoir are also addressed. Finally, testing and certification requirements are discussed as they play an important role in industry acceptance.