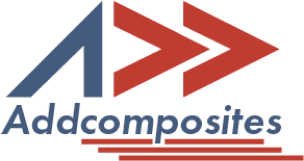
When people think of composites, they immediately picture the black carbon fiber weave that is prevalent in high-end sports cars.
While that is not incorrect, there is much more to a composite material than that. The very basic definition of composite material is: a material made up of various recognizable individual components. They can either be naturally occurring or man-made, which ultimately creates a part that is much stronger than each individual component on its own, usually a reinforcement and a matrix. Advanced composite materials have been contained mainly within the aerospace, space, and defense sectors, and is only recently gaining widespread attention, which is why most people think they are a new invention or are just beginning to learn of them. However, this couldn't be further from the truth!
General composites have been used as construction materials from as early as the Ancient Mesopotamians, (See complete composites history here) when they invented plywood. That's right! One of the most common building materials today is a composite, as it is one material made up of separate components, in this case, wood (reinforcement) and glue (matrix). Other examples of historical composites include huts made from grass (reinforcement) and mud (matrix) and paper maché made from paper (reinforcement) and glue (matrix). Now that the concept of composites is clear, let's dive into the advanced composites of today.
Advanced composites, or fiber-reinforced plastics (FRP), have many other names such as: glass fiber reinforced polymer (GFRP or fiberglass), carbon fiber reinforced polymer (CFRP or carbon fiber), or even simply composites. They are all comprised of fiber reinforcements and a plastic matrix. Initially, glass was used as the main reinforcement, which was a groundbreaking discovery in the 1930s. This creation was comparable to the strength of steel and weight of aluminum, but could be molded into much more complex shapes than the metal counterparts. Then in 1960, Richard Millington created a fiber made up of 99% carbon, and is still the most advanced material used in manufacturing today.
By volume, a composite using carbon fiber as the reinforcement is 5 times stronger than steel and 10 times lighter than aluminum, making it the ideal material to produce aircraft components. The main drawback of carbon fiber, however, is that it is very expensive to produce, making it only viable for the aerospace, space, and defense sectors for much of its existence. But thanks to technological advancements, the cost is continually decreasing, increasing their viability in "non-traditional" markets. To put it in perspective, the cost of carbon fiber as recent as 2016 was €30/kg ($15/lb). Today, only three years later in 2019, the cost dropped by about 50% to €15/kg ($7/lb).
The great advantage of composites is that the engineer is not limited to a single set of material properties, as they leverage the characteristics of both components. Composites take advantage of the compressive strength of the matrix, and the tensile strength of the embedded fibers. These two materials are mutually dependent - without the fiber, the plastic is only as strong as its specific properties; without the matrix, the fiber has no structure and therefore cannot maintain its shape. The matrix creates space so that the fiber has a lever arm to stabilize against the applied load. When combined, they synergize to form a composite material with greater strength in both compression and tension than either component can offer individually. Image 1 below provides a great visualization of what advanced composites consist of.
Now that we have a good grasp on what basic and advanced composite materials are, in the coming articles we will discuss how to manufacture parts using advanced composites. See ya next time in "Advanced Composites: Manufacturing Basics"!
Addcomposites is the provider of the Automated Fiber Placement (AFP) system. The AFP system provided by Addcomposites can be rented on a monthly basis to work with thermosets, thermoplastic, dry fiber placement, or in combination with 3d printers
When people think of composites, they immediately picture the black carbon fiber weave that is prevalent in high-end sports cars.
While that is not incorrect, there is much more to a composite material than that. The very basic definition of composite material is: a material made up of various recognizable individual components. They can either be naturally occurring or man-made, which ultimately creates a part that is much stronger than each individual component on its own, usually a reinforcement and a matrix. Advanced composite materials have been contained mainly within the aerospace, space, and defense sectors, and is only recently gaining widespread attention, which is why most people think they are a new invention or are just beginning to learn of them. However, this couldn't be further from the truth!
General composites have been used as construction materials from as early as the Ancient Mesopotamians, (See complete composites history here) when they invented plywood. That's right! One of the most common building materials today is a composite, as it is one material made up of separate components, in this case, wood (reinforcement) and glue (matrix). Other examples of historical composites include huts made from grass (reinforcement) and mud (matrix) and paper maché made from paper (reinforcement) and glue (matrix). Now that the concept of composites is clear, let's dive into the advanced composites of today.
Advanced composites, or fiber-reinforced plastics (FRP), have many other names such as: glass fiber reinforced polymer (GFRP or fiberglass), carbon fiber reinforced polymer (CFRP or carbon fiber), or even simply composites. They are all comprised of fiber reinforcements and a plastic matrix. Initially, glass was used as the main reinforcement, which was a groundbreaking discovery in the 1930s. This creation was comparable to the strength of steel and weight of aluminum, but could be molded into much more complex shapes than the metal counterparts. Then in 1960, Richard Millington created a fiber made up of 99% carbon, and is still the most advanced material used in manufacturing today.
By volume, a composite using carbon fiber as the reinforcement is 5 times stronger than steel and 10 times lighter than aluminum, making it the ideal material to produce aircraft components. The main drawback of carbon fiber, however, is that it is very expensive to produce, making it only viable for the aerospace, space, and defense sectors for much of its existence. But thanks to technological advancements, the cost is continually decreasing, increasing their viability in "non-traditional" markets. To put it in perspective, the cost of carbon fiber as recent as 2016 was €30/kg ($15/lb). Today, only three years later in 2019, the cost dropped by about 50% to €15/kg ($7/lb).
The great advantage of composites is that the engineer is not limited to a single set of material properties, as they leverage the characteristics of both components. Composites take advantage of the compressive strength of the matrix, and the tensile strength of the embedded fibers. These two materials are mutually dependent - without the fiber, the plastic is only as strong as its specific properties; without the matrix, the fiber has no structure and therefore cannot maintain its shape. The matrix creates space so that the fiber has a lever arm to stabilize against the applied load. When combined, they synergize to form a composite material with greater strength in both compression and tension than either component can offer individually. Image 1 below provides a great visualization of what advanced composites consist of.
Now that we have a good grasp on what basic and advanced composite materials are, in the coming articles we will discuss how to manufacture parts using advanced composites. See ya next time in "Advanced Composites: Manufacturing Basics"!
Addcomposites is the provider of the Automated Fiber Placement (AFP) system. The AFP system provided by Addcomposites can be rented on a monthly basis to work with thermosets, thermoplastic, dry fiber placement, or in combination with 3d printers