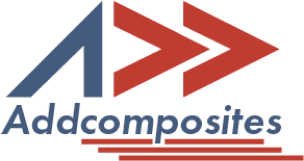
This article will be focused on basic manufacturing techniques, which are the easiest for beginner manufacturers to get started with producing composite products.
When producing parts from advanced composites, many factors need to be taken into account when choosing the appropriate manufacturing process.
The most common practice, and subject of this article, is to do everything by hand, through a process called manual layup. This begins with taking a sheet made up of the desired fiber and cutting it to the correct size and outline necessary to fit the shape of the mold.
A predetermined number of sections (called plies) are layered until the desired thickness is reached. There are multiple types of material used in composites manufacturing, but we will focus on unidirectional from here on out.
As Image 1 shows, a sheet of unidirectional fiber has all the fibers going in the same direction. The other types of fiber sheets can be biaxial, triaxial, twill, etc. where fibers can go in multiple different directions, creating strength no matter the orientation.
When using unidirectional fiber, it is of utmost importance that the fibers are in the correct orientation, as this dictates the strength of the final part.
Even a few degrees of fiber deviation can have detrimental effects on the final part. Once the sheets are laid upon the mold, the material has to be 'wetted'. Wetting is when the uncured matrix is applied onto the fibers until they become totally saturated.
After the part is sufficiently wetted out, the 'bagging' process can begin. Bagging is a multistep process where the end result is an airtight seal between a plastic film and the mold.
Bagging consists of a layering breather (plastic film with holes) and bleeder (the fabric that absorbs excess resin) on top of the wetted fibers, covered by a solid plastic film that is adhered to the mold surface, creating the airtight seal. Vacuum is then applied to the bagged part, which is where the airtight seal comes into play.
This seal is very important because it determines the amount of consolidation of the plies, which determines the overall quality of the final part. If they aren't consolidated correctly, there is a high risk of ply separation, called delamination (delay for short), drastically compromising the strength of the final part.
The part is then put into an oven or autoclave to cure, based upon the matrix curing requirements. This entire process is very slow, and advancements have made resin infusion technology accessible for high-volume manufacturers.
Resin transfer is one such technology that is employed across many manufacturers. Generally, this process is the same as hand layup until the resin application step. There are two main types of resin transfer processes.
The first uses the vacuum bag and vacuum from before to suck resin through the fibers, called Vacuum Assisted Resin Transfer Molding (VARTM). See Image 2 below.
In VARTM, the fibers are bagged while still being dry, then a resin tank is attached at one end of the part, and a vacuum at the other. As the vacuum is applied, it begins sucking resin throughout the entire part, until all the fabric is wetted through.
The resin tank is carefully detached and sealed off, with vacuum still applied, and the part begins the curing process in an oven or autoclave.
The second method is much more advanced and expensive, making it viable only where very large quantities of the same part are produced. The main industry using this process in the automotive industry, where quantities are upwards of hundreds of thousands of the same part per year which is called Resin Transfer Molding (RTM).
The process is yet again very similar to VARTM, but instead of using a bag to consolidate plies, it uses a two-part mold, commonly referred to as a clamshell. This clamshell has a top and bottom mold that are hydraulically closed into each other, creating the airtight seal by sheer force.
Two-part epoxy resin is then forced throughout the mold and fibers via a pump creating positive pressure. See Image 3 below.
The RTM process' speed can be controlled by the amount of pressure applied by the pump. High pressure, high speed. Low pressure, low speed. This process is also much better at controlling the part thickness and surface finish, making it even more ideal for automotive manufacturing.
The metal mold is heated as the resin is pushed through, beginning the curing process even before the fiber is fully wetted. The industry has optimized this process so much so that each part is wetted and cured within a couple of minutes!
Ultimately, the decision must be made on what suits your needs best. VARTM is best for larger parts with a lower quantity, while RTM is best for smaller parts with a much higher quantity. It also depends on which surface needs an A-class finish; that is an exposed surface requiring a defect-free, smooth finish.
If only one side needs to be A-class, VARTM would be the financially responsible route to take, whereas if both sides need the perfect finish, RTM would meet your requirements much more repeatably.
Up until recent years, the manufacturing process leading up to resin transfer has been primarily done by hand.
Sure, there are certain steps of the process where machines have reduced processing time and human interaction, such as ply cutting and resin transfer, but the actual application of plies to the mold is still done manually, outside of the aerospace, space, and defense industries.
Addcomposites is the provider of the Automated Fiber Placement (AFP) system. The AFP system can be rented on a monthly basis to work with thermosets, thermoplastic, dry fiber placement, or in combination with 3d printers.
This article will be focused on basic manufacturing techniques, which are the easiest for beginner manufacturers to get started with producing composite products.
When producing parts from advanced composites, many factors need to be taken into account when choosing the appropriate manufacturing process.
The most common practice, and subject of this article, is to do everything by hand, through a process called manual layup. This begins with taking a sheet made up of the desired fiber and cutting it to the correct size and outline necessary to fit the shape of the mold.
A predetermined number of sections (called plies) are layered until the desired thickness is reached. There are multiple types of material used in composites manufacturing, but we will focus on unidirectional from here on out.
As Image 1 shows, a sheet of unidirectional fiber has all the fibers going in the same direction. The other types of fiber sheets can be biaxial, triaxial, twill, etc. where fibers can go in multiple different directions, creating strength no matter the orientation.
When using unidirectional fiber, it is of utmost importance that the fibers are in the correct orientation, as this dictates the strength of the final part.
Even a few degrees of fiber deviation can have detrimental effects on the final part. Once the sheets are laid upon the mold, the material has to be 'wetted'. Wetting is when the uncured matrix is applied onto the fibers until they become totally saturated.
After the part is sufficiently wetted out, the 'bagging' process can begin. Bagging is a multistep process where the end result is an airtight seal between a plastic film and the mold.
Bagging consists of a layering breather (plastic film with holes) and bleeder (the fabric that absorbs excess resin) on top of the wetted fibers, covered by a solid plastic film that is adhered to the mold surface, creating the airtight seal. Vacuum is then applied to the bagged part, which is where the airtight seal comes into play.
This seal is very important because it determines the amount of consolidation of the plies, which determines the overall quality of the final part. If they aren't consolidated correctly, there is a high risk of ply separation, called delamination (delay for short), drastically compromising the strength of the final part.
The part is then put into an oven or autoclave to cure, based upon the matrix curing requirements. This entire process is very slow, and advancements have made resin infusion technology accessible for high-volume manufacturers.
Resin transfer is one such technology that is employed across many manufacturers. Generally, this process is the same as hand layup until the resin application step. There are two main types of resin transfer processes.
The first uses the vacuum bag and vacuum from before to suck resin through the fibers, called Vacuum Assisted Resin Transfer Molding (VARTM). See Image 2 below.
In VARTM, the fibers are bagged while still being dry, then a resin tank is attached at one end of the part, and a vacuum at the other. As the vacuum is applied, it begins sucking resin throughout the entire part, until all the fabric is wetted through.
The resin tank is carefully detached and sealed off, with vacuum still applied, and the part begins the curing process in an oven or autoclave.
The second method is much more advanced and expensive, making it viable only where very large quantities of the same part are produced. The main industry using this process in the automotive industry, where quantities are upwards of hundreds of thousands of the same part per year which is called Resin Transfer Molding (RTM).
The process is yet again very similar to VARTM, but instead of using a bag to consolidate plies, it uses a two-part mold, commonly referred to as a clamshell. This clamshell has a top and bottom mold that are hydraulically closed into each other, creating the airtight seal by sheer force.
Two-part epoxy resin is then forced throughout the mold and fibers via a pump creating positive pressure. See Image 3 below.
The RTM process' speed can be controlled by the amount of pressure applied by the pump. High pressure, high speed. Low pressure, low speed. This process is also much better at controlling the part thickness and surface finish, making it even more ideal for automotive manufacturing.
The metal mold is heated as the resin is pushed through, beginning the curing process even before the fiber is fully wetted. The industry has optimized this process so much so that each part is wetted and cured within a couple of minutes!
Ultimately, the decision must be made on what suits your needs best. VARTM is best for larger parts with a lower quantity, while RTM is best for smaller parts with a much higher quantity. It also depends on which surface needs an A-class finish; that is an exposed surface requiring a defect-free, smooth finish.
If only one side needs to be A-class, VARTM would be the financially responsible route to take, whereas if both sides need the perfect finish, RTM would meet your requirements much more repeatably.
Up until recent years, the manufacturing process leading up to resin transfer has been primarily done by hand.
Sure, there are certain steps of the process where machines have reduced processing time and human interaction, such as ply cutting and resin transfer, but the actual application of plies to the mold is still done manually, outside of the aerospace, space, and defense industries.
Addcomposites is the provider of the Automated Fiber Placement (AFP) system. The AFP system can be rented on a monthly basis to work with thermosets, thermoplastic, dry fiber placement, or in combination with 3d printers.