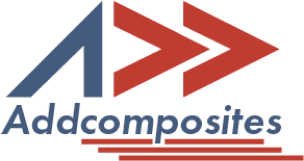
Welcome to the world of fibers and reinforcements—the unsung heroes behind many of
today's advanced composite materials. These integral components are found in diverse industries, from aerospace to sports equipment, offering lightweight, high-performance solutions.
We delve into various fiber types, each with unique attributes. Glass fibers are celebrated for their cost-effectiveness and strength, while aramid fibers, like Kevlar, excel in impact resistance. UHMWPE fibers stand out with their remarkable strength and stiffness, and carbon and graphite fibers are renowned for their superior tensile strength, fatigue characteristics, and corrosion resistance.
The scope of reinforcements extends to woven fabrics, unidirectional tapes, and chopped fibers. We also touch on prepregs, prevalent in advanced composite manufacturing due to their fiber-resin composition. Join us as we unravel the intricate world of fibers and reinforcements, where science and engineering intertwine.
Basic terminologyGlass FibersWhat are glass fibers and how are they produced?And where do these strands of strength find their home?Aramid FibersWhat are Aramid fibers?What are some of the advantages and uses of Aramid fibers?UHMWPEWhat are UHMWPE fibers and how do they differ from other fibers?What unique properties do UHMWPE fibers have?In which industries are UHMWPE fibers commonly used?Carbon and Graphite fibersHow are carbon and graphite fibers different from each other?What are the key applications of carbon and graphite fibers?Woven FabricsHow are fibers used in the production of woven fabrics?What are the benefits of using woven fabrics in various industries?Fiber reinforced matsWhat are reinforced mats and how are they made?What applications do reinforced mats have?Chopped fibersHow are chopped fibers produced and what are their uses?Why are chopped fibers important in certain industries?PrepregsExplain the process of prepreg manufacturing.What are the advantages of using prepregs?Summary Reference
Dive into the dynamic world of fibers and reinforcements! Here, we unravel the terminology that forms the basis of this intriguing field. Think of fibers as the leading actors on the stage. They come in different forms like fiber, filament, and end, each playing its unique role. One key term is the "aspect ratio", a ratio of fiber length to its diameter, often exceeding 100 in this realm. Read more about fiber terminology
Fibers have their own 'personalities', determined by their composition—glass, carbon, or aramid, each with its distinctive set of properties shaped by their composition and manufacturing journey. Selecting the right 'character' for the job is essential, and understanding this language makes the task easier.
Now, let's meet the 'supporting cast'. Reinforcements aren't just fibers; they can be particles, whiskers, or fibers. Particles are the cost-cutters, often used as fillers, while whiskers, single crystal formations, provide impressive strength but can be challenging to disperse. Fibers, however, steal the spotlight with their length, standing out among particles and whiskers.
Fibers also come in different 'costumes', appearing in circular, elliptical, or rectangular cross-sections. The way they 'dance' or orient within the matrix is pivotal, impacting the strength and stiffness of the composite material. Whether they are randomly oriented, unidirectional, or woven into a fabric, each orientation adds its unique touch to the performance.
In a nutshell, understanding this dynamic language of fibers is like having a backstage pass. It helps you choose the right performers and orchestrate a performance that hits the right notes in terms of strength, stiffness, and cost-effectiveness. So, let's keep exploring!
Embark on the journey of glass fibers – the unsung heroes in the realm of composite materials. Born from a fusion of silica sand, limestone, boric acid, and a sprinkle of additional elements like clay and coal, these fibers are crafted through an artful process. Picture a high-temperature furnace, where these ingredients melt and merge into a material ready to be transformed.
Two significant methods take center stage in the creation of high-strength glass fibers: the marble process and the direct melt process. The marble process is akin to a ballet dance. The molten materials are gently poured onto a spinning machine, creating elegant threads of fiber. The direct melt process, on the other hand, is more direct and efficient. Here, the ingredients are melted in a furnace with platinum-rhodium bushings to give birth to continuous filaments.
Glass fibers are the stars of the show in many commercial composite applications. Thanks to their affordability, impressive tensile strength, high impact resistance, and commendable chemical resistance, they are the material of choice for a myriad of applications. From automotive parts and aerospace components to wind turbine blades, boat hulls, and even sporting goods - glass fibers play a pivotal role. While they might not match the might of carbon fibers in high-performance applications, they certainly hold their own in the world of composites. Enjoy the ride as we explore more about these remarkable materials!
Take a step into the world of aramid fibers, the organic heroes that strike a perfect balance between the stiffness and strength of glass and carbon fibers. The most famous name on this stage is Dupont's Kevlar fiber, a proud member of the nylon family. Imagine a dance of chemistry, where paraphenylene diamine waltzes with terephthaloyl chloride in an organic solvent, giving birth to polyparaphenylene terephthalamide - or simply, aramid.
The drama unfolds as this product of condensation is extruded, stretched, and drawn. After a refreshing wash, it dissolves in sulfuric acid, transforming into a partially oriented liquid crystal. Then comes the grand finale: the polymer solution is extruded through tiny spinnerets, orienting the fibers in solution and during spinning.
But what makes aramid fibers truly noteworthy are their exceptional properties. Picture materials with high tensile strength, impressive modulus, superior impact resistance, and commendable heat resistance. These qualities make aramid fibers the stars of many arenas.
Imagine a high-strength, heat-resistant fiber that can stop a bullet in its tracks. That's aramid for you, the secret behind the remarkable ballistic protection offered by body armor. Consider the demanding environment of aerospace, where every gram matters.
Aramid fibers rise to the occasion, contributing to aircraft panels, rotor blades, and engine parts. They also make appearances in sporting goods, lending their strength to tennis rackets, hockey sticks, and bicycle frames. And let's not forget high-performance tires, where aramid fibers enhance durability and puncture resistance.
Picture a material so robust yet light, capable of withstanding extreme conditions while being lighter than water. Welcome to the captivating world of Ultrahigh Molecular Weight Polyethylene fibers, or UHMWPE fibers. Made from high-density polyethylene through a process known as solid-state drawing, these fibers are a marvel of modern engineering.
The strength and stiffness of UHMWPE fibers are in the realm of the extraordinary, making them ideal for applications that demand high strength-to-weight ratios. But what truly sets them apart is their low density - a mere 0.97 g/cm3. Yes, that's lighter than aramid fibers, lighter even than water!
The resilience of UHMWPE fibers extends beyond physical strength. Picture a material that stands up to moisture, perfect for the harshest wet environments. Furthermore, they possess unique electrical properties, with a low dielectric constant and low loss tangent, making them an excellent choice for electrical applications.
But it's not all rainbows and sunshine. UHMWPE fibers, like all materials, have their limitations. Their bonding with the matrix material is relatively weak, leading to poor transverse tension and compression strengths. Being a thermoplastic fiber, they are also prone to creep under continuous loading.
Despite these limitations, the applications of UHMWPE fibers are impressively diverse. They find their way into body armor, providing protection for those in the line of duty. They form the lifelines of ropes and cables, and the delicate yet resilient threads of fishing lines. Even in the medical field, they make their mark as durable implants.
Imagine a material so versatile that it caters to the needs of different industries, from defense and security to aerospace and sports. UHMWPE fibers are such a marvel, seamlessly making their way into various applications due to their unique and exciting properties.
In the world of materials, carbon and graphite fibers are like twin siblings, similar yet distinct in their own ways. They dance to the tune of high performance, but the steps they take are slightly different.
Let's start with their birth. Carbon fibers spring to life from precursors like rayon, pitch or PAN, nurtured under heat treatments at lower temperatures. Their sibling, graphite fibers, are a bit more hardened, withstanding heat treatments above a scorching 3,000°C.
Now, what about their inner structure? Imagine a bustling city filled with skyscrapers, orderly roads, and grids - that's graphite fibers, with a 3D ordering of their atoms. Carbon fibers, on the other hand, are more like a charming countryside town, where there's less order, but plenty of character.
The carbon content? Graphite fibers boast a robust 99%, while carbon fibers have a slightly lower carbon content ranging from 93-95%. And when it comes to the elastic modulus, graphite fibers flex their muscles with a modulus greater than 50 msi, while carbon fibers exhibit a more modest range from 30 to 45 msi.
But don't be fooled by these differences. Both siblings possess formidable tensile and compressive strength, and impressive fatigue characteristics, and they both laugh in the face of corrosion.
So where do these wonder fibers find their home? In industries far and wide! They jet off to the aerospace sector, forming aircraft panels, rotor blades, and engine parts. They zoom into automotive, shaping body panels, brake discs, and suspension parts. Sports equipment? You'll find them there too, lending their strength to tennis rackets, golf clubs, and bicycle frames.
The story doesn't end here. They ascend to great heights in wind turbine blades, dive into the realm of biocompatibility in medical implants, and even strengthen the backbone of our buildings in the construction industry. And let's not forget the realm of electronics, where graphite fibers show off their thermal conductivity properties.
Imagine a dance. The dance of creation, where each move intertwines with another, creates a beautiful, intricate tapestry. This is the world of woven fabrics, where individual threads come together, under the choreography of a loom, to create a piece of art that is as sturdy as it is elegant.
The first act of this dance starts with spinning fibers into yarns. These yarns then form the foundation of our woven fabric on a loom. The warp yarns, like disciplined soldiers, stretch out in perfect lengthwise alignment. Against them, the fill yarns weave their way across, crisscrossing at right angles.
The loom becomes the stage, and the warp threads rise and fall, creating a space, an invitation for the fill thread to pass through. This rhythmic dance repeats itself across the breadth of the fabric, again and again, until a stunning piece of woven fabric comes to life.
But the artistry doesn't end there. Depending on how the threads embrace each other, we get different forms of woven fabric - the simple yet classic plain weave, the elegant twill weave, or the sleek satin weave. And when these threads are made from high-performance fibers like carbon, glass, or aramid, the woven fabric stands as a testament to strength and stiffness.
So, why do industries around the world love this dance? The reasons are many. The strength and stiffness of woven fabrics, especially those reinforced with high-performance fibers, are music to the ears of industries requiring high-performance structures.
Picture yourself standing in front of a swirling masterpiece. It's not a painting, though – it's a reinforced mat, a marvel of engineering where art meets science. Reinforced mats are like composite tapestries, intricately made from either chopped strands or continuous strands laid down in a captivating swirl pattern. They're the unsung heroes in medium-strength parts with uniform cross-sections, their hidden strength bound together by resinous binders.
Now, imagine a continuous fiber strand, long and unbroken. It's chopped into tiny lengths and scattered onto a conveyor belt like autumn leaves in the wind, creating a random, unique pattern. A resinous binder steps in, bonding these fibers together and voila - we have a chopped strand mat.
But, there's another story to tell. This time, imagine continuous strands of fibers laying down in a rhythmic swirl pattern onto a conveyor belt. Once again, the resinous binder plays its role, securing these fibers to form a continuous strand mat.
Both these versions of reinforced mats come in various weights and widths, offering a versatile range of options. But the innovation doesn't stop there. We can add an extra layer of finesse with surfacing mats or veils. These thin, lightweight materials can enhance the surface finish of composite parts, adding an extra touch of quality.
Now, you might be wondering where these reinforced mats make their grand appearance. The stage is vast and varied.
Picture a sleek car cruising down the highway – its body panels, hoods, and fenders owe their existence to reinforced mats. Or consider a majestic yacht cutting through the waves – its hull and deck are products of these mats.
Imagine an airplane soaring high above the clouds, its fairings, wing skins, and interior panels all made possible by reinforced mats. Even the solid roof over your head, the wall panels, and the pipes running through your building – you guessed it, they're all applications of reinforced mats.
And let's not forget about sports - tennis rackets, golf clubs, hockey sticks - all made stronger and more durable thanks to these mats. Even the massive blades of wind turbines, harnessing the power of the wind, are products of this incredible material.
So there you have it, the story of reinforced mats, an unseen but essential element in the tapestry of our daily lives.
Imagine you're standing in a bustling factory where the air hums with the ceaseless activity of machines. You're witnessing the birth of chopped fibers, a crucial ingredient in some of the most versatile and resilient materials used in modern manufacturing.
It all begins with continuous strands of fibers, as long and thin as a river. These strands are fed into a mechanical titan that chops them into short lengths, typically between 0.125 to 2 inches.
These freshly chopped fibers are then swept up and blended into a cocktail of resins and other additives. This blend transforms into a molding compound, a malleable material ready to be shaped and formed through processes like compression or injection moldings, and encapsulation.
Chopped fibers are the secret sauce in creating parts that need to be stronger than their weight suggests. They infuse thermosetting and thermoplastic resin systems with a superpower - an enhanced mechanical strength that brings stiffness, resilience, and impact resistance.
Imagine a glass fiber, chopped and treated for optimal compatibility with thermosetting and thermoplastic resin systems. Different lengths of fibers can be produced, each with a particular mission. Shorter milled fibers, longer fibers – each serves a unique purpose in the grand scheme of manufacturing.
The importance of chopped fibers stretches across various industries. In the world of automobiles, they are the silent heroes that lend strength to body panels, hoods, and fenders. These parts are not just lightweight but also tough enough to shrug off impacts.
So, the next time you admire a sleek car, or gaze at a soaring plane, or even when you're comfortably tucked away in your home, remember the unsung hero – the chopped fiber, a tiny but mighty force that helps shape the world around us.
Picture this: You're in a bustling factory, surrounded by gleaming machinery, and we're about to embark on the exciting journey of creating prepregs, the unsung heroes of the composite manufacturing world. The journey starts with the magical elixir of resin. This is mixed with a hardener, a secret ingredient that bestows strength and resistance. The right blend of additives is added into this mixture, tailoring the potion to the desired properties.
Once our resin potion is ready, it's time to introduce it to the star of the show - the fibers. These fibers take a luxurious bath in the resin, soaking up the liquid through methods like roll coating, dip coating, or spray coating. Then, they go through a rigorous rolling massage to ensure an even coating of resin - no fiber is left behind!
Following this, the impregnated fibers enter the 'B-staging' spa. Here, they are transformed into a semi-solid state - solid at room temperature, but easily melted when heated. It's a bit like turning into a superhero with the power to change forms. This stage allows for easy handling and storage of the prepreg, patiently waiting for its moment of transformation.
Our prepreg's spa journey is now nearing an end. It's cut into sheets or tapes, packaged neatly in plastic bags, and tucked into a cozy freezer bed until it's time for the next adventure.
The beauty of prepregs is that they are versatile. They can be used in a variety of processes - think of them as actors ready to play any role, from wet filament winding to liquid molding or pultrusion. The result is a composite structure with improved mechanical properties, strong as a superhero and resilient as a champion.
Prepregs bring a host of advantages to the table. They ensure consistent quality, a result of their birth in controlled conditions. They make life easier and reduce labor costs with their readiness for use. Prepregs are the material equivalent of a superhero - they offer enhanced strength, stiffness, and impact resistance.
They are also eco-warriors, reducing waste by being supplied in specific sizes and shapes, and using less resin than other manufacturing methods. And if that wasn't enough, they give designers the freedom to create complex shapes and geometries that might seem impossible with other methods.
So next time you come across a high-performance composite, remember the journey of prepregs, from their humble beginnings in a resin bath to their transformation into a material superhero.
Imagine this as the final chapter of a gripping saga, where the unsung heroes are not knights in shining armor, but fibers and reinforcements! They are the primary source of strength, the backbone of our tale, adding resilience and robustness to the composite materials that are central to our story.
From the humble beginnings of glass to the more sophisticated characters like carbon and aramid, and not forgetting the natural fibers – all of them have their unique tale to tell. They play a range of roles, morphing into woven fabrics, unidirectional tapes, or chopped fibers, each adding a new dimension to the plot.
Now, meet our star – the prepreg! A popular figure in the world of advanced composite manufacturing, this character is a true maestro. It's a beautiful tapestry of fibers wrapped in a B-staged resin, a unique blend that makes prepreg stand out in a crowd.
Let's not forget the supporting actor – chopped fibers. Their strength lies in their ability to create robust parts through compression and injection molding. They know how to blend in, mixing smoothly with resins and additives to prepare molding compounds for a variety of exciting scenarios.
The making of our star, the prepreg, is a story in itself. It begins with a precise dance of resin mixing, followed by the delicate art of fiber impregnation. The journey continues through the mysterious phase of B-staging, before concluding with a grand finale of cutting and packaging.
And as with all heroes, prepregs come with an array of superpowers. They promise consistent quality and reduce labor costs, making them the hero of the working class. Their mechanical properties are unmatched, offering strength and resilience. And they are the champions of the environment, reducing waste and their overall environmental impact.
They are not just heroes, but also artists, offering design flexibility that inspires creativity, allowing for the creation of shapes and structures that are only limited by imagination.
Welcome to the world of fibers and reinforcements—the unsung heroes behind many of
today's advanced composite materials. These integral components are found in diverse industries, from aerospace to sports equipment, offering lightweight, high-performance solutions.
We delve into various fiber types, each with unique attributes. Glass fibers are celebrated for their cost-effectiveness and strength, while aramid fibers, like Kevlar, excel in impact resistance. UHMWPE fibers stand out with their remarkable strength and stiffness, and carbon and graphite fibers are renowned for their superior tensile strength, fatigue characteristics, and corrosion resistance.
The scope of reinforcements extends to woven fabrics, unidirectional tapes, and chopped fibers. We also touch on prepregs, prevalent in advanced composite manufacturing due to their fiber-resin composition. Join us as we unravel the intricate world of fibers and reinforcements, where science and engineering intertwine.
Basic terminologyGlass FibersWhat are glass fibers and how are they produced?And where do these strands of strength find their home?Aramid FibersWhat are Aramid fibers?What are some of the advantages and uses of Aramid fibers?UHMWPEWhat are UHMWPE fibers and how do they differ from other fibers?What unique properties do UHMWPE fibers have?In which industries are UHMWPE fibers commonly used?Carbon and Graphite fibersHow are carbon and graphite fibers different from each other?What are the key applications of carbon and graphite fibers?Woven FabricsHow are fibers used in the production of woven fabrics?What are the benefits of using woven fabrics in various industries?Fiber reinforced matsWhat are reinforced mats and how are they made?What applications do reinforced mats have?Chopped fibersHow are chopped fibers produced and what are their uses?Why are chopped fibers important in certain industries?PrepregsExplain the process of prepreg manufacturing.What are the advantages of using prepregs?Summary Reference
Dive into the dynamic world of fibers and reinforcements! Here, we unravel the terminology that forms the basis of this intriguing field. Think of fibers as the leading actors on the stage. They come in different forms like fiber, filament, and end, each playing its unique role. One key term is the "aspect ratio", a ratio of fiber length to its diameter, often exceeding 100 in this realm. Read more about fiber terminology
Fibers have their own 'personalities', determined by their composition—glass, carbon, or aramid, each with its distinctive set of properties shaped by their composition and manufacturing journey. Selecting the right 'character' for the job is essential, and understanding this language makes the task easier.
Now, let's meet the 'supporting cast'. Reinforcements aren't just fibers; they can be particles, whiskers, or fibers. Particles are the cost-cutters, often used as fillers, while whiskers, single crystal formations, provide impressive strength but can be challenging to disperse. Fibers, however, steal the spotlight with their length, standing out among particles and whiskers.
Fibers also come in different 'costumes', appearing in circular, elliptical, or rectangular cross-sections. The way they 'dance' or orient within the matrix is pivotal, impacting the strength and stiffness of the composite material. Whether they are randomly oriented, unidirectional, or woven into a fabric, each orientation adds its unique touch to the performance.
In a nutshell, understanding this dynamic language of fibers is like having a backstage pass. It helps you choose the right performers and orchestrate a performance that hits the right notes in terms of strength, stiffness, and cost-effectiveness. So, let's keep exploring!
Embark on the journey of glass fibers – the unsung heroes in the realm of composite materials. Born from a fusion of silica sand, limestone, boric acid, and a sprinkle of additional elements like clay and coal, these fibers are crafted through an artful process. Picture a high-temperature furnace, where these ingredients melt and merge into a material ready to be transformed.
Two significant methods take center stage in the creation of high-strength glass fibers: the marble process and the direct melt process. The marble process is akin to a ballet dance. The molten materials are gently poured onto a spinning machine, creating elegant threads of fiber. The direct melt process, on the other hand, is more direct and efficient. Here, the ingredients are melted in a furnace with platinum-rhodium bushings to give birth to continuous filaments.
Glass fibers are the stars of the show in many commercial composite applications. Thanks to their affordability, impressive tensile strength, high impact resistance, and commendable chemical resistance, they are the material of choice for a myriad of applications. From automotive parts and aerospace components to wind turbine blades, boat hulls, and even sporting goods - glass fibers play a pivotal role. While they might not match the might of carbon fibers in high-performance applications, they certainly hold their own in the world of composites. Enjoy the ride as we explore more about these remarkable materials!
Take a step into the world of aramid fibers, the organic heroes that strike a perfect balance between the stiffness and strength of glass and carbon fibers. The most famous name on this stage is Dupont's Kevlar fiber, a proud member of the nylon family. Imagine a dance of chemistry, where paraphenylene diamine waltzes with terephthaloyl chloride in an organic solvent, giving birth to polyparaphenylene terephthalamide - or simply, aramid.
The drama unfolds as this product of condensation is extruded, stretched, and drawn. After a refreshing wash, it dissolves in sulfuric acid, transforming into a partially oriented liquid crystal. Then comes the grand finale: the polymer solution is extruded through tiny spinnerets, orienting the fibers in solution and during spinning.
But what makes aramid fibers truly noteworthy are their exceptional properties. Picture materials with high tensile strength, impressive modulus, superior impact resistance, and commendable heat resistance. These qualities make aramid fibers the stars of many arenas.
Imagine a high-strength, heat-resistant fiber that can stop a bullet in its tracks. That's aramid for you, the secret behind the remarkable ballistic protection offered by body armor. Consider the demanding environment of aerospace, where every gram matters.
Aramid fibers rise to the occasion, contributing to aircraft panels, rotor blades, and engine parts. They also make appearances in sporting goods, lending their strength to tennis rackets, hockey sticks, and bicycle frames. And let's not forget high-performance tires, where aramid fibers enhance durability and puncture resistance.
Picture a material so robust yet light, capable of withstanding extreme conditions while being lighter than water. Welcome to the captivating world of Ultrahigh Molecular Weight Polyethylene fibers, or UHMWPE fibers. Made from high-density polyethylene through a process known as solid-state drawing, these fibers are a marvel of modern engineering.
The strength and stiffness of UHMWPE fibers are in the realm of the extraordinary, making them ideal for applications that demand high strength-to-weight ratios. But what truly sets them apart is their low density - a mere 0.97 g/cm3. Yes, that's lighter than aramid fibers, lighter even than water!
The resilience of UHMWPE fibers extends beyond physical strength. Picture a material that stands up to moisture, perfect for the harshest wet environments. Furthermore, they possess unique electrical properties, with a low dielectric constant and low loss tangent, making them an excellent choice for electrical applications.
But it's not all rainbows and sunshine. UHMWPE fibers, like all materials, have their limitations. Their bonding with the matrix material is relatively weak, leading to poor transverse tension and compression strengths. Being a thermoplastic fiber, they are also prone to creep under continuous loading.
Despite these limitations, the applications of UHMWPE fibers are impressively diverse. They find their way into body armor, providing protection for those in the line of duty. They form the lifelines of ropes and cables, and the delicate yet resilient threads of fishing lines. Even in the medical field, they make their mark as durable implants.
Imagine a material so versatile that it caters to the needs of different industries, from defense and security to aerospace and sports. UHMWPE fibers are such a marvel, seamlessly making their way into various applications due to their unique and exciting properties.
In the world of materials, carbon and graphite fibers are like twin siblings, similar yet distinct in their own ways. They dance to the tune of high performance, but the steps they take are slightly different.
Let's start with their birth. Carbon fibers spring to life from precursors like rayon, pitch or PAN, nurtured under heat treatments at lower temperatures. Their sibling, graphite fibers, are a bit more hardened, withstanding heat treatments above a scorching 3,000°C.
Now, what about their inner structure? Imagine a bustling city filled with skyscrapers, orderly roads, and grids - that's graphite fibers, with a 3D ordering of their atoms. Carbon fibers, on the other hand, are more like a charming countryside town, where there's less order, but plenty of character.
The carbon content? Graphite fibers boast a robust 99%, while carbon fibers have a slightly lower carbon content ranging from 93-95%. And when it comes to the elastic modulus, graphite fibers flex their muscles with a modulus greater than 50 msi, while carbon fibers exhibit a more modest range from 30 to 45 msi.
But don't be fooled by these differences. Both siblings possess formidable tensile and compressive strength, and impressive fatigue characteristics, and they both laugh in the face of corrosion.
So where do these wonder fibers find their home? In industries far and wide! They jet off to the aerospace sector, forming aircraft panels, rotor blades, and engine parts. They zoom into automotive, shaping body panels, brake discs, and suspension parts. Sports equipment? You'll find them there too, lending their strength to tennis rackets, golf clubs, and bicycle frames.
The story doesn't end here. They ascend to great heights in wind turbine blades, dive into the realm of biocompatibility in medical implants, and even strengthen the backbone of our buildings in the construction industry. And let's not forget the realm of electronics, where graphite fibers show off their thermal conductivity properties.
Imagine a dance. The dance of creation, where each move intertwines with another, creates a beautiful, intricate tapestry. This is the world of woven fabrics, where individual threads come together, under the choreography of a loom, to create a piece of art that is as sturdy as it is elegant.
The first act of this dance starts with spinning fibers into yarns. These yarns then form the foundation of our woven fabric on a loom. The warp yarns, like disciplined soldiers, stretch out in perfect lengthwise alignment. Against them, the fill yarns weave their way across, crisscrossing at right angles.
The loom becomes the stage, and the warp threads rise and fall, creating a space, an invitation for the fill thread to pass through. This rhythmic dance repeats itself across the breadth of the fabric, again and again, until a stunning piece of woven fabric comes to life.
But the artistry doesn't end there. Depending on how the threads embrace each other, we get different forms of woven fabric - the simple yet classic plain weave, the elegant twill weave, or the sleek satin weave. And when these threads are made from high-performance fibers like carbon, glass, or aramid, the woven fabric stands as a testament to strength and stiffness.
So, why do industries around the world love this dance? The reasons are many. The strength and stiffness of woven fabrics, especially those reinforced with high-performance fibers, are music to the ears of industries requiring high-performance structures.
Picture yourself standing in front of a swirling masterpiece. It's not a painting, though – it's a reinforced mat, a marvel of engineering where art meets science. Reinforced mats are like composite tapestries, intricately made from either chopped strands or continuous strands laid down in a captivating swirl pattern. They're the unsung heroes in medium-strength parts with uniform cross-sections, their hidden strength bound together by resinous binders.
Now, imagine a continuous fiber strand, long and unbroken. It's chopped into tiny lengths and scattered onto a conveyor belt like autumn leaves in the wind, creating a random, unique pattern. A resinous binder steps in, bonding these fibers together and voila - we have a chopped strand mat.
But, there's another story to tell. This time, imagine continuous strands of fibers laying down in a rhythmic swirl pattern onto a conveyor belt. Once again, the resinous binder plays its role, securing these fibers to form a continuous strand mat.
Both these versions of reinforced mats come in various weights and widths, offering a versatile range of options. But the innovation doesn't stop there. We can add an extra layer of finesse with surfacing mats or veils. These thin, lightweight materials can enhance the surface finish of composite parts, adding an extra touch of quality.
Now, you might be wondering where these reinforced mats make their grand appearance. The stage is vast and varied.
Picture a sleek car cruising down the highway – its body panels, hoods, and fenders owe their existence to reinforced mats. Or consider a majestic yacht cutting through the waves – its hull and deck are products of these mats.
Imagine an airplane soaring high above the clouds, its fairings, wing skins, and interior panels all made possible by reinforced mats. Even the solid roof over your head, the wall panels, and the pipes running through your building – you guessed it, they're all applications of reinforced mats.
And let's not forget about sports - tennis rackets, golf clubs, hockey sticks - all made stronger and more durable thanks to these mats. Even the massive blades of wind turbines, harnessing the power of the wind, are products of this incredible material.
So there you have it, the story of reinforced mats, an unseen but essential element in the tapestry of our daily lives.
Imagine you're standing in a bustling factory where the air hums with the ceaseless activity of machines. You're witnessing the birth of chopped fibers, a crucial ingredient in some of the most versatile and resilient materials used in modern manufacturing.
It all begins with continuous strands of fibers, as long and thin as a river. These strands are fed into a mechanical titan that chops them into short lengths, typically between 0.125 to 2 inches.
These freshly chopped fibers are then swept up and blended into a cocktail of resins and other additives. This blend transforms into a molding compound, a malleable material ready to be shaped and formed through processes like compression or injection moldings, and encapsulation.
Chopped fibers are the secret sauce in creating parts that need to be stronger than their weight suggests. They infuse thermosetting and thermoplastic resin systems with a superpower - an enhanced mechanical strength that brings stiffness, resilience, and impact resistance.
Imagine a glass fiber, chopped and treated for optimal compatibility with thermosetting and thermoplastic resin systems. Different lengths of fibers can be produced, each with a particular mission. Shorter milled fibers, longer fibers – each serves a unique purpose in the grand scheme of manufacturing.
The importance of chopped fibers stretches across various industries. In the world of automobiles, they are the silent heroes that lend strength to body panels, hoods, and fenders. These parts are not just lightweight but also tough enough to shrug off impacts.
So, the next time you admire a sleek car, or gaze at a soaring plane, or even when you're comfortably tucked away in your home, remember the unsung hero – the chopped fiber, a tiny but mighty force that helps shape the world around us.
Picture this: You're in a bustling factory, surrounded by gleaming machinery, and we're about to embark on the exciting journey of creating prepregs, the unsung heroes of the composite manufacturing world. The journey starts with the magical elixir of resin. This is mixed with a hardener, a secret ingredient that bestows strength and resistance. The right blend of additives is added into this mixture, tailoring the potion to the desired properties.
Once our resin potion is ready, it's time to introduce it to the star of the show - the fibers. These fibers take a luxurious bath in the resin, soaking up the liquid through methods like roll coating, dip coating, or spray coating. Then, they go through a rigorous rolling massage to ensure an even coating of resin - no fiber is left behind!
Following this, the impregnated fibers enter the 'B-staging' spa. Here, they are transformed into a semi-solid state - solid at room temperature, but easily melted when heated. It's a bit like turning into a superhero with the power to change forms. This stage allows for easy handling and storage of the prepreg, patiently waiting for its moment of transformation.
Our prepreg's spa journey is now nearing an end. It's cut into sheets or tapes, packaged neatly in plastic bags, and tucked into a cozy freezer bed until it's time for the next adventure.
The beauty of prepregs is that they are versatile. They can be used in a variety of processes - think of them as actors ready to play any role, from wet filament winding to liquid molding or pultrusion. The result is a composite structure with improved mechanical properties, strong as a superhero and resilient as a champion.
Prepregs bring a host of advantages to the table. They ensure consistent quality, a result of their birth in controlled conditions. They make life easier and reduce labor costs with their readiness for use. Prepregs are the material equivalent of a superhero - they offer enhanced strength, stiffness, and impact resistance.
They are also eco-warriors, reducing waste by being supplied in specific sizes and shapes, and using less resin than other manufacturing methods. And if that wasn't enough, they give designers the freedom to create complex shapes and geometries that might seem impossible with other methods.
So next time you come across a high-performance composite, remember the journey of prepregs, from their humble beginnings in a resin bath to their transformation into a material superhero.
Imagine this as the final chapter of a gripping saga, where the unsung heroes are not knights in shining armor, but fibers and reinforcements! They are the primary source of strength, the backbone of our tale, adding resilience and robustness to the composite materials that are central to our story.
From the humble beginnings of glass to the more sophisticated characters like carbon and aramid, and not forgetting the natural fibers – all of them have their unique tale to tell. They play a range of roles, morphing into woven fabrics, unidirectional tapes, or chopped fibers, each adding a new dimension to the plot.
Now, meet our star – the prepreg! A popular figure in the world of advanced composite manufacturing, this character is a true maestro. It's a beautiful tapestry of fibers wrapped in a B-staged resin, a unique blend that makes prepreg stand out in a crowd.
Let's not forget the supporting actor – chopped fibers. Their strength lies in their ability to create robust parts through compression and injection molding. They know how to blend in, mixing smoothly with resins and additives to prepare molding compounds for a variety of exciting scenarios.
The making of our star, the prepreg, is a story in itself. It begins with a precise dance of resin mixing, followed by the delicate art of fiber impregnation. The journey continues through the mysterious phase of B-staging, before concluding with a grand finale of cutting and packaging.
And as with all heroes, prepregs come with an array of superpowers. They promise consistent quality and reduce labor costs, making them the hero of the working class. Their mechanical properties are unmatched, offering strength and resilience. And they are the champions of the environment, reducing waste and their overall environmental impact.
They are not just heroes, but also artists, offering design flexibility that inspires creativity, allowing for the creation of shapes and structures that are only limited by imagination.