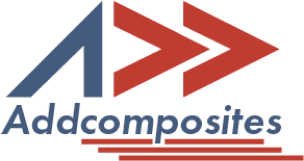
The bicycle industry has witnessed a remarkable transformation with the advent of composite materials. These materials, primarily carbon fiber composites, have revolutionized bicycle design and performance, offering a unique combination of lightweight, strength, and stiffness. This article explores the current state of composite materials in the bicycle industry, examining their types, applications, advantages, disadvantages, and the latest advancements driving innovation in this sector.
Composite materials are formed by combining two or more materials with different properties to create a new material with enhanced characteristics. In the bicycle industry, the most common composite material is carbon fiber reinforced polymer (CFRP). CFRP consists of carbon fibers embedded in a resin matrix, typically epoxy. The carbon fibers provide exceptional strength and stiffness, while the resin holds the fibers together and distributes loads1. The resin itself is a crucial component, with different types offering varying properties depending on the desired application. For instance, some resins are engineered for high-temperature resistance, while others prioritize impact resistance or flexibility1.
One of the key advantages of composite materials like CFRP is their anisotropic nature. Unlike isotropic materials like steel or aluminum, which have the same strength and stiffness in all directions, composite materials exhibit different properties depending on the direction of the applied force. This allows manufacturers to tailor the strength and stiffness of bicycle frames by strategically orienting the carbon fibers during the manufacturing process2.
The quality and characteristics of carbon fiber composites are also influenced by the type of carbon fiber used. Carbon fiber is often categorized by the "K" designation, which refers to the number of fibers in a bundle. Common designations include 3K (3,000 fibers) and 12K (12,000 fibers). The higher the "K" value, the larger the fiber bundle and the more prominent the weave pattern in the finished product1.
In addition to carbon fiber, other materials like fiberglass, Kevlar, and even biocomposites are used in bicycle manufacturing. Fiberglass offers good strength and cost-effectiveness, while Kevlar provides excellent impact resistance. Biocomposites, made from recycled fibers and vegetable resins, are gaining popularity as a more sustainable alternative to traditional carbon fiber composites1.
It's also worth noting that metal often plays a crucial role in carbon fiber frame construction. Aluminum and titanium are commonly used for bonding and reinforcing carbon fiber frames, particularly in areas that require high strength or wear resistance, such as bottom brackets, headsets, and dropouts1.
Another important aspect of composite materials in bicycle manufacturing is the use of "prepreg." Prepreg refers to carbon fiber fabric that has been pre-impregnated with resin. This material simplifies the manufacturing process and ensures consistent resin content throughout the composite structure2.
Composite materials have found widespread applications in various bicycle components. Here's a closer look at some of the key areas where composites are making a difference:
Carbon fiber frames are highly sought after for their lightweight, stiffness, and ability to absorb vibrations. They offer a significant performance advantage over traditional steel or aluminum frames, particularly in road cycling and mountain biking, where weight and efficiency are paramount5. Carbon fiber forks complement these frames by providing excellent vibration damping and precise steering control, further enhancing ride comfort and handling7.
There are two primary methods for manufacturing carbon fiber composite frames:
The choice of manufacturing method depends on factors such as the desired frame design, production volume, and cost considerations.
Carbon fiber rims offer several advantages over traditional aluminum rims. They are lighter, which reduces rotational inertia and improves acceleration. They are also stiffer, which enhances power transfer and handling precision. Moreover, carbon fiber rims can be aerodynamically optimized to reduce wind resistance, leading to increased speed and efficiency5.
The "cockpit" of a bicycle refers to the handlebars, stem, and seatpost. Carbon fiber is increasingly used in these components to reduce weight, improve comfort, and enhance control. Carbon fiber handlebars provide a lightweight and comfortable grip, reducing fatigue and improving steering precision. Carbon fiber stems offer stiffness and lightweight, contributing to responsive handling. Carbon fiber seatposts provide vibration damping and lightweight, enhancing ride comfort5.
While less prevalent, composite materials are also finding applications in other bicycle parts like bottle cages, saddles, and pedals. These applications demonstrate the versatility of composite materials and their potential to improve various aspects of bicycle design and performance5.
The field of composite materials in the bicycle industry is constantly evolving, with ongoing research and development focused on improving performance, reducing costs, and enhancing sustainability. Here are some of the key advancements and trends shaping the future of composite bicycles:
These advancements and trends highlight the dynamic nature of the composite bicycle industry and its commitment to continuous improvement.
The bicycle industry is increasingly embracing automation to improve the manufacturing process of composite bicycle parts. This trend is driven by the need for greater efficiency, reduced costs, and enhanced quality7. Here's a closer look at some of the key automation techniques being employed:
AFP involves using a robotic arm to precisely place pre-impregnated fiber tapes onto a mold. This technique offers several advantages:
Key components of an AFP system include a fiber placement head, a material delivery system, a compaction system, heating elements for tack control, a precise motion control system, and sophisticated software for path planning and control18.
However, AFP also presents some challenges, particularly when applied to complex tool surfaces. Achieving precise fiber orientations and minimizing defects like puckers, wrinkles, and tow overlaps can be difficult in these cases20.
Filament winding is a process where continuous fibers are wound onto a rotating mandrel to create tubular shapes. This technique is highly efficient for producing components like forks, frame tubes, and even rims7.
Filament winding offers several advantages:
Different winding patterns are used in filament winding to achieve specific strength characteristics:
Despite its advantages, filament winding has some limitations:
LFAM, also known as large-scale 3D printing, is used to create molds and tooling for composite part production, as well as for directly manufacturing bicycle components like frame parts and structural elements19.
LFAM offers several advantages:
Large-format continuous fiber 3D printing combines LFAM with continuous fiber reinforcement, allowing for the direct printing of high-performance composite parts with complex geometries and optimized fiber orientations. This technology is used to create various bicycle components, including frames, forks, and cranks23.
Advantages of large-format continuous fiber 3D printing include:
Several case studies demonstrate the successful implementation of automation techniques in bicycle manufacturing:
These case studies showcase the diverse applications of automation techniques in bicycle manufacturing and their potential to drive innovation and improve product performance.
Addcomposites offers innovative systems and solutions for automating and optimizing the production of composite bicycle parts. Their AFP-XS system combines the benefits of AFP and filament winding, allowing for the creation of complex parts with varying thicknesses and optimized fiber paths18. This system introduces several process improvements:
The AFP-XS system also enables the production of structures with integral stiffeners and components with region-specific properties. This allows for the creation of lighter and more efficient bicycle components with optimized strength and stiffness characteristics18.
In addition to the AFP-XS system, Addcomposites offers:
These systems offer several potential benefits for bicycle manufacturers:
Numerous bicycle manufacturers and brands are incorporating composite materials into their bicycles. These companies can be categorized into different types based on their approach to composite manufacturing:
Some of the key players in the composite bicycle market include:
The cost of composite material bicycles varies significantly depending on the brand, model, and components. Entry-level carbon fiber bikes can be found for around $2,000, while high-end models can cost upwards of $10,000 or more37. The availability of composite material bicycles has increased significantly in recent years, with a wider range of options available through both online retailers and local bike shops39.
Customization and personalization are becoming increasingly important in the composite bicycle market. Programs like the ENVE Custom Road program allow customers to personalize their carbon fiber bikes with bespoke frame geometries, component options, and paint schemes38. Smaller brands like CDuro also offer limited small batch frames, providing personalized attention and customer service to those seeking unique and customized bicycles40.
Composite materials have become integral to the bicycle industry, offering significant advantages in terms of performance, lightweight, and design flexibility. Ongoing advancements in manufacturing techniques and material science are further pushing the boundaries of what's possible with composite bicycles. Automation technologies like AFP, filament winding, and large-format continuous fiber 3D printing are transforming the manufacturing process, enabling greater efficiency, customization, and sustainability.
The increasing adoption of automation and advanced materials is likely to lead to more personalized, high-performance, and sustainable bicycles in the future. Imagine a world where cyclists can order custom-designed bikes tailored to their exact needs and preferences, with frames 3D-printed from advanced composite materials and assembled by robots with unparalleled precision. This vision is becoming increasingly realistic as the lines between traditional manufacturing methods and additive manufacturing continue to blur.
The development of new composite materials and manufacturing techniques is not only improving the performance of bicycles but also enhancing the overall cycling experience. Lighter and more comfortable bikes make cycling more enjoyable and accessible to a wider range of people. Moreover, the focus on sustainability in composite manufacturing is contributing to a greener and more environmentally friendly cycling industry.
As these technologies continue to evolve, we can expect to see even more innovative and high-performance composite bicycles in the future, further enhancing the cycling experience for riders of all levels.