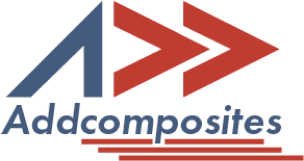
Ceramic matrix composites (CMCs) have emerged as a critical class of materials for demanding high-temperature applications due to their unique combination of properties, including:
However, manufacturing high-performance CMCs that can fully leverage these properties remains a significant challenge. Some of the key issues include:
Conventional methods for fabricating CMCs, such as chemical vapor infiltration (CVI) and polymer infiltration and pyrolysis (PIP), often involve complex, multi-step processes that are time- and cost-intensive. These limitations have hindered the widespread adoption of CMCs in various industries, despite their potential for enabling new levels of performance in extreme environments.
To address these challenges, researchers have been exploring novel manufacturing approaches that can streamline the production of CMCs while maintaining or even enhancing their mechanical and thermal properties. One promising direction is the use of additive manufacturing techniques, which offer the potential for greater design flexibility, faster processing times, and reduced material waste compared to traditional methods.
Conventional methods for fabricating ceramic matrix composites (CMCs) face several limitations that have hindered their widespread adoption in various industries. Two of the most commonly used techniques are chemical vapor infiltration (CVI) and polymer infiltration and pyrolysis (PIP).CVI involves the infiltration of a porous fiber preform with gaseous precursors that decompose to form the ceramic matrix. While CVI can produce high-quality CMCs with good mechanical properties, it has several drawbacks:
PIP, on the other hand, involves the repeated infiltration of a fiber preform with a polymer precursor, followed by pyrolysis to convert the polymer into a ceramic matrix. Although PIP is generally faster than CVI, it still suffers from some limitations:
In addition to these process-specific issues, both CVI and PIP involve complex, multi-step processing that requires specialized equipment and skilled operators. This complexity contributes to the high cost and limited scalability of CMC production.
The need for more efficient and cost-effective manufacturing methods is a major pain point for industries seeking to adopt CMCs for high-temperature applications.
To address the limitations of conventional CMC manufacturing methods, researchers have developed a novel approach that combines additive manufacturing, specifically AFP, with reactive melt infiltration (RMI). This innovative process enables the rapid and cost-effective production of carbon fiber-reinforced carbon matrix composites (C/C) that can be further densified with silicon carbide (SiC) to form C/C-SiC composites.
The key steps in this AFP-based process are as follows:
This additive manufacturing approach offers several advantages over traditional CMC fabrication methods:
By combining the benefits of additive manufacturing with the unique properties of C/C-SiC composites, this novel approach has the potential to unlock new applications for high-temperature materials in industries such as aerospace, energy, and transportation.
The novel additive manufacturing approach based on AFP and reactive melt infiltration (RMI) has demonstrated the potential to revolutionize the production of ceramic matrix composites (CMCs), particularly carbon fiber-reinforced carbon-silicon carbide (C/C-SiC) composites.
The C/C-SiC composites manufactured using this AFP-based process exhibit several desirable properties:
The damage tolerance of these composites arises from the unique microstructure developed during processing. The carbon fibers are partially protected by the pyrolyzed carbon matrix, which provides a weak interface for crack deflection and fiber pullout. The SiC matrix, formed through the reaction of infiltrated silicon with the carbon matrix, further enhances the strength and stiffness of the composite.
Microstructural characterization using techniques such as optical microscopy, scanning electron microscopy (SEM), energy-dispersive X-ray spectroscopy (EDS), and Raman spectroscopy confirms the presence of the desired phases (carbon fibers, pyrolyzed carbon matrix, SiC, and residual silicon) and their distribution within the composite.
The mechanical properties and microstructural features of the C/C-SiC composites produced via this AFP-based process are comparable to those of CMCs manufactured using conventional methods, while offering the benefits of faster production times and greater design flexibility.
Further optimization of the process parameters, such as placement settings, pyrolysis conditions, and melt infiltration cycles, can help to minimize defects such as porosity and delamination, thereby improving the overall performance of the composites.
In summary, the AFP-based additive manufacturing approach, coupled with reactive melt infiltration, provides a promising solution for the rapid and cost-effective production of damage-tolerant C/C-SiC composites. This novel process has the potential to expand the adoption of CMCs in various high-temperature applications across multiple industries.
let's thank the authors Corson L. Cramer, Bola Yoon, Michael J. Lance, Ercan Cakmak, Quinn A. Campbell, and David J. Mitchell for their valuable contributions to this research and for providing the foundation for this informative blog post. Their work, as detailed in the paper "Additive Manufacturing of C/C-SiC Ceramic Matrix Composites by Automated Fiber Placement of Continuous Fiber Tow in Polymer with Pyrolysis and Reactive Silicon Melt Infiltration," has opened up exciting new possibilities in the field of ceramic matrix composite manufacturing. We are grateful for their dedication and expertise, which have enabled us to share these insights with our readers.
Discover the future of composite manufacturing with Addcomposites! Here's how you can get involved:
At Addcomposites, we are dedicated to revolutionizing composite manufacturing. Our AFP systems and comprehensive support services are waiting for you to harness. So, don't wait – get started on your journey to the future of manufacturing today!
Ceramic matrix composites (CMCs) have emerged as a critical class of materials for demanding high-temperature applications due to their unique combination of properties, including:
However, manufacturing high-performance CMCs that can fully leverage these properties remains a significant challenge. Some of the key issues include:
Conventional methods for fabricating CMCs, such as chemical vapor infiltration (CVI) and polymer infiltration and pyrolysis (PIP), often involve complex, multi-step processes that are time- and cost-intensive. These limitations have hindered the widespread adoption of CMCs in various industries, despite their potential for enabling new levels of performance in extreme environments.
To address these challenges, researchers have been exploring novel manufacturing approaches that can streamline the production of CMCs while maintaining or even enhancing their mechanical and thermal properties. One promising direction is the use of additive manufacturing techniques, which offer the potential for greater design flexibility, faster processing times, and reduced material waste compared to traditional methods.
Conventional methods for fabricating ceramic matrix composites (CMCs) face several limitations that have hindered their widespread adoption in various industries. Two of the most commonly used techniques are chemical vapor infiltration (CVI) and polymer infiltration and pyrolysis (PIP).CVI involves the infiltration of a porous fiber preform with gaseous precursors that decompose to form the ceramic matrix. While CVI can produce high-quality CMCs with good mechanical properties, it has several drawbacks:
PIP, on the other hand, involves the repeated infiltration of a fiber preform with a polymer precursor, followed by pyrolysis to convert the polymer into a ceramic matrix. Although PIP is generally faster than CVI, it still suffers from some limitations:
In addition to these process-specific issues, both CVI and PIP involve complex, multi-step processing that requires specialized equipment and skilled operators. This complexity contributes to the high cost and limited scalability of CMC production.
The need for more efficient and cost-effective manufacturing methods is a major pain point for industries seeking to adopt CMCs for high-temperature applications.
To address the limitations of conventional CMC manufacturing methods, researchers have developed a novel approach that combines additive manufacturing, specifically AFP, with reactive melt infiltration (RMI). This innovative process enables the rapid and cost-effective production of carbon fiber-reinforced carbon matrix composites (C/C) that can be further densified with silicon carbide (SiC) to form C/C-SiC composites.
The key steps in this AFP-based process are as follows:
This additive manufacturing approach offers several advantages over traditional CMC fabrication methods:
By combining the benefits of additive manufacturing with the unique properties of C/C-SiC composites, this novel approach has the potential to unlock new applications for high-temperature materials in industries such as aerospace, energy, and transportation.
The novel additive manufacturing approach based on AFP and reactive melt infiltration (RMI) has demonstrated the potential to revolutionize the production of ceramic matrix composites (CMCs), particularly carbon fiber-reinforced carbon-silicon carbide (C/C-SiC) composites.
The C/C-SiC composites manufactured using this AFP-based process exhibit several desirable properties:
The damage tolerance of these composites arises from the unique microstructure developed during processing. The carbon fibers are partially protected by the pyrolyzed carbon matrix, which provides a weak interface for crack deflection and fiber pullout. The SiC matrix, formed through the reaction of infiltrated silicon with the carbon matrix, further enhances the strength and stiffness of the composite.
Microstructural characterization using techniques such as optical microscopy, scanning electron microscopy (SEM), energy-dispersive X-ray spectroscopy (EDS), and Raman spectroscopy confirms the presence of the desired phases (carbon fibers, pyrolyzed carbon matrix, SiC, and residual silicon) and their distribution within the composite.
The mechanical properties and microstructural features of the C/C-SiC composites produced via this AFP-based process are comparable to those of CMCs manufactured using conventional methods, while offering the benefits of faster production times and greater design flexibility.
Further optimization of the process parameters, such as placement settings, pyrolysis conditions, and melt infiltration cycles, can help to minimize defects such as porosity and delamination, thereby improving the overall performance of the composites.
In summary, the AFP-based additive manufacturing approach, coupled with reactive melt infiltration, provides a promising solution for the rapid and cost-effective production of damage-tolerant C/C-SiC composites. This novel process has the potential to expand the adoption of CMCs in various high-temperature applications across multiple industries.
let's thank the authors Corson L. Cramer, Bola Yoon, Michael J. Lance, Ercan Cakmak, Quinn A. Campbell, and David J. Mitchell for their valuable contributions to this research and for providing the foundation for this informative blog post. Their work, as detailed in the paper "Additive Manufacturing of C/C-SiC Ceramic Matrix Composites by Automated Fiber Placement of Continuous Fiber Tow in Polymer with Pyrolysis and Reactive Silicon Melt Infiltration," has opened up exciting new possibilities in the field of ceramic matrix composite manufacturing. We are grateful for their dedication and expertise, which have enabled us to share these insights with our readers.
Discover the future of composite manufacturing with Addcomposites! Here's how you can get involved:
At Addcomposites, we are dedicated to revolutionizing composite manufacturing. Our AFP systems and comprehensive support services are waiting for you to harness. So, don't wait – get started on your journey to the future of manufacturing today!