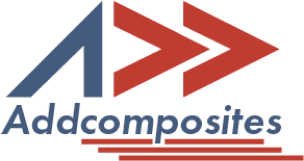
Additive manufacturing (AM), particularly through techniques such as Fused Filament Fabrication (FFF), presents revolutionary opportunities in various industries, including aerospace, by allowing for the production of complex geometrical parts without the need for extensive tooling. However, one significant hurdle that persists is achieving strong and reliable bonding between high-performance polymers like PEEK (poly ether ether ketone) and carbon fiber-reinforced composites.
The integrity and mechanical strength of 3D-printed parts are fundamentally dependent on the quality of bonding between the polymer filaments. This bonding is predominantly influenced by the thermal energy during the printing process, where the polymer is extruded in a semi-molten state and must fuse properly with its preceding layers. In the case of high-performance materials like PEEK and PEI (polyetherimide), this is particularly challenging due to their high processing temperatures which introduce high thermal gradients. These gradients can result in:
The bonding issues primarily arise from the rapid cooling and solidification of these materials, which can prevent proper interlayer adhesion. This necessitates a controlled environment where the temperature and speed of extrusion are meticulously managed to optimize bonding. Unfortunately, existing technologies often show that under standard processing conditions, the bonding achieved is still below the necessary mechanical strength standards, indicating a significant gap in current manufacturing capabilities and the ideal outcomes.
While the potential for using AM to create functionally superior and geometrically complex structures is vast, the challenge of achieving strong and durable bonds in high-performance polymers remains a substantial barrier that needs addressing. This issue underscores the need for ongoing research and development to refine the processing conditions that allow for optimal thermal control and material behavior during printing.
The production of composite structures using 3D printing technologies, particularly through fused filament fabrication (FFF), is fraught with technical challenges that impede the achievement of strong and reliable interlayer bonding. These difficulties primarily stem from the nature of the materials used, such as PEEK (poly ether ether ketone) and PEI (poly ether imide), which are known for their high performance in terms of temperature resistance and mechanical strength but are notoriously difficult to process.
The primary challenge in bonding these polymers lies in their requirement for high extrusion temperatures, which in turn creates steep thermal gradients during the printing process. These gradients can lead to:
The rapid change in temperature prevents the polymer chains from interdiffusing adequately at the interface of the layers, resulting in weak adhesion points that can lead to delamination under mechanical stress.
Further complicating the situation is the precision required in controlling the processing environment. Factors such as ambient temperature, extrusion speed, and cooling rates must be meticulously managed to ensure that the material maintains a temperature conducive to bonding throughout the printing process. This is often challenging in standard laboratory or production settings without specialized equipment capable of sustaining the necessary conditions.
Moreover, even with optimal processing parameters, the bonding quality achieved between high-performance polymer layers often fails to meet the desired standards. This is evidenced by various tests, where despite the high potential for thermal compatibility between PEI and PEEK, the interfacial bonding remains insufficient for high-strength applications.
In the realm of fused filament fabrication (FFF), achieving strong and consistent bonding between layers of high-performance polymers presents significant challenges, primarily due to the high thermal gradients and rapid cooling involved in the process. To address these issues, innovative approaches and advancements in printing technology and methodology are essential.
One such innovative approach involves manipulating the thermal environment during the printing process. By controlling the temperature precisely at the point of filament deposition, it's possible to maintain the polymer in a more conducive state for bonding. For example:
Moreover, the integration of automated systems such as 6-axis robots for 3D printing also allows for more precise control over the deposition of materials on complex composite parts. This helps in maintaining consistent conditions across the interface of the materials, which is crucial for achieving strong bonding.
Optimized process parameters for effective bonding of PEEK/carbon fiber laminates entail meticulous control over various aspects of the FFF process to significantly improve the bonding strength and quality of these materials. This includes:
These innovative approaches not only aim to overcome the intrinsic challenges of FFF with high-performance polymers but also push the boundaries of what can be achieved with additive manufacturing. By continually refining these techniques, the industry can better harness the potential of FFF for producing structurally sound and mechanically robust parts.
We extend our gratitude to Isciane Caprais, Pierre Joyot, Emmanuel Duc, and Simon Deseur for their in-depth studies and valuable insights which laid the groundwork for understanding the complex interactions in the bonding process of high-performance polymers processed by Fused Filament Fabrication and PEEK/carbon fiber laminates. Their meticulous research and pioneering work are detailed in the document "Bonding between high-performance polymer processed by Fused Filament Fabrication and PEEK/carbon fiber laminate." Their expertise and commitment to advancing this field are deeply appreciated.
Discover the future of composite manufacturing with Addcomposites! Here's how you can get involved:
At Addcomposites, we are dedicated to revolutionizing composite manufacturing. Our AFP systems and comprehensive support services are waiting for you to harness. So, don't wait – get started on your journey to the future of manufacturing today!
Additive manufacturing (AM), particularly through techniques such as Fused Filament Fabrication (FFF), presents revolutionary opportunities in various industries, including aerospace, by allowing for the production of complex geometrical parts without the need for extensive tooling. However, one significant hurdle that persists is achieving strong and reliable bonding between high-performance polymers like PEEK (poly ether ether ketone) and carbon fiber-reinforced composites.
The integrity and mechanical strength of 3D-printed parts are fundamentally dependent on the quality of bonding between the polymer filaments. This bonding is predominantly influenced by the thermal energy during the printing process, where the polymer is extruded in a semi-molten state and must fuse properly with its preceding layers. In the case of high-performance materials like PEEK and PEI (polyetherimide), this is particularly challenging due to their high processing temperatures which introduce high thermal gradients. These gradients can result in:
The bonding issues primarily arise from the rapid cooling and solidification of these materials, which can prevent proper interlayer adhesion. This necessitates a controlled environment where the temperature and speed of extrusion are meticulously managed to optimize bonding. Unfortunately, existing technologies often show that under standard processing conditions, the bonding achieved is still below the necessary mechanical strength standards, indicating a significant gap in current manufacturing capabilities and the ideal outcomes.
While the potential for using AM to create functionally superior and geometrically complex structures is vast, the challenge of achieving strong and durable bonds in high-performance polymers remains a substantial barrier that needs addressing. This issue underscores the need for ongoing research and development to refine the processing conditions that allow for optimal thermal control and material behavior during printing.
The production of composite structures using 3D printing technologies, particularly through fused filament fabrication (FFF), is fraught with technical challenges that impede the achievement of strong and reliable interlayer bonding. These difficulties primarily stem from the nature of the materials used, such as PEEK (poly ether ether ketone) and PEI (poly ether imide), which are known for their high performance in terms of temperature resistance and mechanical strength but are notoriously difficult to process.
The primary challenge in bonding these polymers lies in their requirement for high extrusion temperatures, which in turn creates steep thermal gradients during the printing process. These gradients can lead to:
The rapid change in temperature prevents the polymer chains from interdiffusing adequately at the interface of the layers, resulting in weak adhesion points that can lead to delamination under mechanical stress.
Further complicating the situation is the precision required in controlling the processing environment. Factors such as ambient temperature, extrusion speed, and cooling rates must be meticulously managed to ensure that the material maintains a temperature conducive to bonding throughout the printing process. This is often challenging in standard laboratory or production settings without specialized equipment capable of sustaining the necessary conditions.
Moreover, even with optimal processing parameters, the bonding quality achieved between high-performance polymer layers often fails to meet the desired standards. This is evidenced by various tests, where despite the high potential for thermal compatibility between PEI and PEEK, the interfacial bonding remains insufficient for high-strength applications.
In the realm of fused filament fabrication (FFF), achieving strong and consistent bonding between layers of high-performance polymers presents significant challenges, primarily due to the high thermal gradients and rapid cooling involved in the process. To address these issues, innovative approaches and advancements in printing technology and methodology are essential.
One such innovative approach involves manipulating the thermal environment during the printing process. By controlling the temperature precisely at the point of filament deposition, it's possible to maintain the polymer in a more conducive state for bonding. For example:
Moreover, the integration of automated systems such as 6-axis robots for 3D printing also allows for more precise control over the deposition of materials on complex composite parts. This helps in maintaining consistent conditions across the interface of the materials, which is crucial for achieving strong bonding.
Optimized process parameters for effective bonding of PEEK/carbon fiber laminates entail meticulous control over various aspects of the FFF process to significantly improve the bonding strength and quality of these materials. This includes:
These innovative approaches not only aim to overcome the intrinsic challenges of FFF with high-performance polymers but also push the boundaries of what can be achieved with additive manufacturing. By continually refining these techniques, the industry can better harness the potential of FFF for producing structurally sound and mechanically robust parts.
We extend our gratitude to Isciane Caprais, Pierre Joyot, Emmanuel Duc, and Simon Deseur for their in-depth studies and valuable insights which laid the groundwork for understanding the complex interactions in the bonding process of high-performance polymers processed by Fused Filament Fabrication and PEEK/carbon fiber laminates. Their meticulous research and pioneering work are detailed in the document "Bonding between high-performance polymer processed by Fused Filament Fabrication and PEEK/carbon fiber laminate." Their expertise and commitment to advancing this field are deeply appreciated.
Discover the future of composite manufacturing with Addcomposites! Here's how you can get involved:
At Addcomposites, we are dedicated to revolutionizing composite manufacturing. Our AFP systems and comprehensive support services are waiting for you to harness. So, don't wait – get started on your journey to the future of manufacturing today!