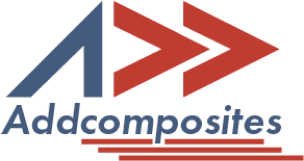
Additive manufacturing (AM) or 3D printing has gained widespread use for fabricating polymer components, from prototypes to final products. Various AM techniques have been developed, such as Stereolithography (SLA), Selective Laser Sintering (SLS), and Fused Deposition Modelling (FDM). FDM is the most widely utilized system for polymer AM manufacturing, offering relatively low costs, low material consumption, and ease of use.
However, one of the main drawbacks of 3D printing technology has been the low mechanical strength of the raw materials used. The most common materials limit the use of 3D printing to prototyping and modeling, without being able to produce usable products, as they are weak and brittle.
To address this issue, researchers have focused on developing fiber-reinforced 3D printed materials. Several studies have reported 3D printing structures reinforced with different kinds of short fibers or inclusions. One of the latest efforts in this direction has been made through the application of Continuous Fiber Fabrication (CFF) 3D printing machines, which lay continuous composite fibers, such as Kevlar and carbon fiber, inside 3D printed thermoplastics to improve their mechanical properties.
The current study aims to investigate the mechanical behavior of 3D printed fiberglass-reinforced nylon honeycomb structures using a CFF 3D printer (Markforged Mark Two). By selectively reinforcing the honeycomb structures with continuous fiberglass, the researchers hope to significantly enhance the mechanical properties of these 3D printed polymer components, making them suitable for more demanding applications.
One of the main challenges faced by manufacturers and researchers in the field of 3D printing is the low mechanical strength of the raw materials used. Most common 3D printing materials, such as PLA and ABS, are relatively weak and brittle compared to traditional engineering materials. This limitation restricts the use of 3D printed parts to prototyping and modeling applications, hindering their potential for producing functional, load-bearing components.
The low mechanical strength of 3D printed parts can be attributed to several factors:
As a result, manufacturers and researchers have been actively seeking solutions to enhance the mechanical properties of 3D printed components. One promising approach is the incorporation of fiber reinforcement into the 3D printing process, which has the potential to significantly improve the strength, stiffness, and overall performance of the printed parts.
To address the issue of low mechanical strength in 3D printed polymer components, the current study focuses on investigating the mechanical behavior of 3D printed fiberglass-reinforced nylon honeycomb structures. The research team employed a systematic approach to fabricate and characterize these reinforced structures:
By employing this comprehensive approach, the researchers aimed to gain a deeper understanding of the mechanical properties and behavior of 3D printed fiberglass-reinforced nylon honeycomb structures, paving the way for the development of stronger and more functional 3D printed polymer components.
The study demonstrates that the incorporation of continuous fiberglass reinforcement in 3D printed nylon honeycomb structures leads to a significant improvement in their flexural properties. The key findings and solutions are as follows:
The significant improvement in flexural properties achieved through continuous fiberglass reinforcement in 3D printed nylon honeycomb structures opens up new possibilities for the application of these lightweight and stiff cellular structures. The research suggests that by strategically placing the fiberglass reinforcement within the honeycomb structure, manufacturers can create 3D printed components with enhanced mechanical performance, suitable for more demanding applications in various industries.
we would like to express our gratitude to the authors of the research paper titled "Mechanical and FEA-Assisted Characterization of 3D Printed Continuous Glass Fiber Reinforced Nylon Cellular Structures", Evangelos Giarmas, Konstantinos Tsongas, Emmanouil K. Tzimtzimis, Apostolos Korlos, and Dimitrios Tzetzis, for their valuable contribution to this study. Their dedication and expertise have been instrumental in advancing our understanding of the mechanical behavior of 3D printed continuous glass fiber reinforced nylon cellular structures.
We appreciate Evangelos Giarmas, Konstantinos Tsongas, Emmanouil K. Tzimtzimis, Apostolos Korlos, and Dimitrios Tzetzis' efforts in conducting a comprehensive investigation, which included the fabrication of honeycomb structures using a Continuous Fiber Fabrication (CFF) 3D printer, the examination of microstructure using Scanning Electron Microscopy (SEM) and Energy Dispersive X-ray Spectroscopy (EDX), the evaluation of material properties through nanoindentation tests, and the validation of experimental results using Finite Element Analysis (FEA).
The insights gained from Evangelos Giarmas, Konstantinos Tsongas, Emmanouil K. Tzimtzimis, Apostolos Korlos, and Dimitrios Tzetzis' research have the potential to revolutionize the field of 3D printing, enabling the production of stronger, stiffer, and more functional polymer components for various applications. We commend Evangelos Giarmas, Konstantinos Tsongas, Emmanouil K. Tzimtzimis, Apostolos Korlos, and Dimitrios Tzetzis for their significant contribution to this field and look forward to their future research endeavors.
Discover the future of composite manufacturing with Addcomposites! Here's how you can get involved:
At Addcomposites, we are dedicated to revolutionizing composite manufacturing. Our AFP systems and comprehensive support services are waiting for you to harness. So, don't wait – get started on your journey to the future of manufacturing today!
Additive manufacturing (AM) or 3D printing has gained widespread use for fabricating polymer components, from prototypes to final products. Various AM techniques have been developed, such as Stereolithography (SLA), Selective Laser Sintering (SLS), and Fused Deposition Modelling (FDM). FDM is the most widely utilized system for polymer AM manufacturing, offering relatively low costs, low material consumption, and ease of use.
However, one of the main drawbacks of 3D printing technology has been the low mechanical strength of the raw materials used. The most common materials limit the use of 3D printing to prototyping and modeling, without being able to produce usable products, as they are weak and brittle.
To address this issue, researchers have focused on developing fiber-reinforced 3D printed materials. Several studies have reported 3D printing structures reinforced with different kinds of short fibers or inclusions. One of the latest efforts in this direction has been made through the application of Continuous Fiber Fabrication (CFF) 3D printing machines, which lay continuous composite fibers, such as Kevlar and carbon fiber, inside 3D printed thermoplastics to improve their mechanical properties.
The current study aims to investigate the mechanical behavior of 3D printed fiberglass-reinforced nylon honeycomb structures using a CFF 3D printer (Markforged Mark Two). By selectively reinforcing the honeycomb structures with continuous fiberglass, the researchers hope to significantly enhance the mechanical properties of these 3D printed polymer components, making them suitable for more demanding applications.
One of the main challenges faced by manufacturers and researchers in the field of 3D printing is the low mechanical strength of the raw materials used. Most common 3D printing materials, such as PLA and ABS, are relatively weak and brittle compared to traditional engineering materials. This limitation restricts the use of 3D printed parts to prototyping and modeling applications, hindering their potential for producing functional, load-bearing components.
The low mechanical strength of 3D printed parts can be attributed to several factors:
As a result, manufacturers and researchers have been actively seeking solutions to enhance the mechanical properties of 3D printed components. One promising approach is the incorporation of fiber reinforcement into the 3D printing process, which has the potential to significantly improve the strength, stiffness, and overall performance of the printed parts.
To address the issue of low mechanical strength in 3D printed polymer components, the current study focuses on investigating the mechanical behavior of 3D printed fiberglass-reinforced nylon honeycomb structures. The research team employed a systematic approach to fabricate and characterize these reinforced structures:
By employing this comprehensive approach, the researchers aimed to gain a deeper understanding of the mechanical properties and behavior of 3D printed fiberglass-reinforced nylon honeycomb structures, paving the way for the development of stronger and more functional 3D printed polymer components.
The study demonstrates that the incorporation of continuous fiberglass reinforcement in 3D printed nylon honeycomb structures leads to a significant improvement in their flexural properties. The key findings and solutions are as follows:
The significant improvement in flexural properties achieved through continuous fiberglass reinforcement in 3D printed nylon honeycomb structures opens up new possibilities for the application of these lightweight and stiff cellular structures. The research suggests that by strategically placing the fiberglass reinforcement within the honeycomb structure, manufacturers can create 3D printed components with enhanced mechanical performance, suitable for more demanding applications in various industries.
we would like to express our gratitude to the authors of the research paper titled "Mechanical and FEA-Assisted Characterization of 3D Printed Continuous Glass Fiber Reinforced Nylon Cellular Structures", Evangelos Giarmas, Konstantinos Tsongas, Emmanouil K. Tzimtzimis, Apostolos Korlos, and Dimitrios Tzetzis, for their valuable contribution to this study. Their dedication and expertise have been instrumental in advancing our understanding of the mechanical behavior of 3D printed continuous glass fiber reinforced nylon cellular structures.
We appreciate Evangelos Giarmas, Konstantinos Tsongas, Emmanouil K. Tzimtzimis, Apostolos Korlos, and Dimitrios Tzetzis' efforts in conducting a comprehensive investigation, which included the fabrication of honeycomb structures using a Continuous Fiber Fabrication (CFF) 3D printer, the examination of microstructure using Scanning Electron Microscopy (SEM) and Energy Dispersive X-ray Spectroscopy (EDX), the evaluation of material properties through nanoindentation tests, and the validation of experimental results using Finite Element Analysis (FEA).
The insights gained from Evangelos Giarmas, Konstantinos Tsongas, Emmanouil K. Tzimtzimis, Apostolos Korlos, and Dimitrios Tzetzis' research have the potential to revolutionize the field of 3D printing, enabling the production of stronger, stiffer, and more functional polymer components for various applications. We commend Evangelos Giarmas, Konstantinos Tsongas, Emmanouil K. Tzimtzimis, Apostolos Korlos, and Dimitrios Tzetzis for their significant contribution to this field and look forward to their future research endeavors.
Discover the future of composite manufacturing with Addcomposites! Here's how you can get involved:
At Addcomposites, we are dedicated to revolutionizing composite manufacturing. Our AFP systems and comprehensive support services are waiting for you to harness. So, don't wait – get started on your journey to the future of manufacturing today!