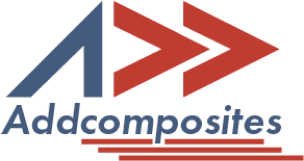
The article covers the design of composite vessels from the physical and mechanical aspects. The design heavily relies on the properties of materials to the geometry. The design cycle of hydrogen tanks begins with general characteristics, such as the tank capacity, working pressure, material attributes, and safety factors. followed by dome design and fiber placement orientation. The same finite element technique has been widely used to predict the failure properties and strengths of composites based on different failure modalities. The ultimate goal of all of these techniques is to arrive at a reliable burst pressure. ensuring the design conforms to the local authorities' standard, the burst pressure design has to be optimized for safety and reliability. The article leaves on a positive note by talking about the prospect of h2 vessels.
The design of the composite vessel relates the physical and mechanical properties of materials to the geometry. Essentially, two main works are required for the design: one is the prediction of burst pressure and another is the optimization. The burst pressure denotes the limited load-carrying ability of the composite vessel. Since the failure mechanisms of composites are complicated from the view of composite micromechanics, including the matrix cracking, fiber/matrix debonding, and fiber breakage as well as their interactions. The optimization attempts to improve the weight, strength, reliability, and lifetime of the composite vessel by designing the wound angles and thickness.
A complete design cycle of a composite hydrogen tank is illustrated in the Figure below. The design cycle of hydrogen tanks begins with step no. 1, which defines the project's general characteristics, such as the tank capacity, working pressure, material attributes, and safety factors. The designer can use this information to compute other parameters that are required for the tank geometry definition, such as the cylinder radius, boss radius, and tank length.
The dome shape of composite tanks has a significant impact on their mechanical performance. The isotensoidal dome geometry, which is based on geodesic winding trajectories, is a common dome geometry. Parameters defined in step no. 1, such as the tank capacity, working pressure, and material characteristics, were the input parameters for the dome profile equations
The optimum dome shapes can be approximated as quasi-elliptic curves. The most important design parameter would be the depth of the elliptical dome. When the dome depths are between 0.6 and 0.775, designed domes present a stronger structure and greater internal volume.
The analytical design solution of composite hydrogen tanks is based on broad assumptions about load and boundary conditions and does not account for stiffness discontinuities near the polar boss. The finite element analysis (FEA) must be used to correctly model these and other effects in order to accurately predict the behavior of filament wound pressure vessels. Most filament wound pressure vessels exhibit first-order non-linear geometry effects, which can only be captured via the FEA.
The accuracy of the numerical analysis is mainly dependent upon the modeling technique and analysis conditions. The table below summarizes some approaches developed in the literature.
Composite tanks are wound using a combination of the alternate hoop and helical windings, whose main features are summarized in the table below. An alternate helical/hoop winding scheme is used to remove the excess resin and to obtain the target fiber volume fraction during the winding process.
Winding Type
Feature
Hoop winding
- Filaments are placed nearly perpendicular to the mandrel axis (α ≈ 90◦).
- Usually used with other strategies to resist circumferential stresses.
- Creates high consolidation pressure.
- Generally applied only to cylindrical sections.
- Placed at high speeds.
- Used to describe geodesics, non-geodesics and combinations thereof.
Low helical winding
- Winding angle varies (5◦ ≤ α ≤ 30◦).
- Low helical angle is used to strengthen the dome regions.
- Placed at moderate speeds.
- Used to describe geodesics, non-geodesics and combinations
thereof.
High helical winding
- Winding angle varies (60◦ ≤ α ≤ 80◦).
- High helical winding is used to strengthen the transition regions
between the cylinder and dome.
- Placed at moderate and high speeds.
- Used to describe geodesics, non-geodesics and combinations
thereof
Exploring the failure properties using progressive failure analysis as the aging of epoxy matrix leads to stiffness and strength degradation, thereby affecting the lifetime of the composite vessel.
There are two distinct failure mechanisms for the composite vessel: intralaminar damage and interlaminar delamination. From the burst experiments of composite vessels, the intralaminar damage instead of interlaminar delamination affects the mechanical performance of the composite vessel. This is because two neighboring composite layers still keep normally pressing and tangentially slipping despite a little interlaminar failure appearing before the burst. Thus, only intralaminar failure is generally considered.
Failure shows the degraded ability to resist the external load. The failure properties of a composite vessel depend on the geometry sizes, the material features, the loading history, and the environment. Over the past five decades, the popular failure criteria are the maximum stress, Hashin, Hoffman, Hinton, Christensen, Rotem, McCartney, Yamada-Sun, Chang-Chang, Tsai-Hill, Tsai-Wu, Puck and Huang’s criteria.
Currently, there is also an evolving trend to develop the fracture energy-based failure criteria to predict the failure of composites using such as the cohesive fracture energy-based criterion and finite element failure-based criterion. However, accurate prediction of fracture properties of composites requires advanced experimental techniques.
Essentially, progressive failure analysis of the composite vessel is to implement the proposed damage constitutive model, the failure criteria, and damage evolution law.
The flow chart for the progressive failure analysis of the composite vessel using the finite element method is illustrated in the figure above and summarized by five points:
The Burst pressure of the composite vessel is the ultimate aim of progressive failure analysis. The prediction of the burst pressure is essentially related to the numerical convergence problem in the finite element analysis. According to the design requirement of the composite vessel, only a little matrix cracking under working pressure is permitted. As the pressure increases, progressive interface debonding and matrix cracking appear. Only when a large number of fibers breakage suddenly appears is the composite vessel
considered to burst.
The aim of the design for the composite vessel is to reach the best match between reliability and practicability.
the working pressure of the composite vessel is taken as the burst pressure divided by the safety coefficient. However, the difficulty lies in how to select a proper safety coefficient which yet depends on the design and manufacturing levels. The CGH2R Draft Revision 10 of the European Union and the ISO/DIS 15869.2 specify the safety coefficients of 2.35 and 2.25, respectively. Then, the optimal design attempts to reach the minimum weight and highest strength under the constraint of the safety coefficient.
For a designed composite vessel, economy and practicability are based on safety and reliability. The reliability and lifetime of the composite vessel relate to many factors such as the material parameters, wound patterns, and manufacturing defects. It is not always feasible to expect to use a single safety coefficient to provide a guarantee for any occasional accident. Thus, it is necessary to develop reliability and lifetime-based methods to perform the probabilistic design.
In recent years, composite pressure vessels develop rapidly in the field of hydrogen storage. With the development of computer-aided design techniques, the composite vessel offers designers much design space. The design is to reach the ideal match among the reliability and lifetime, weight, and cost.
The above article is part of the course Design and Development of Compressed Hydrogen Storage Tanks. The course covers a lot more, starting with discussing challenges in material selection and manufacturing practices, as well as cutting-edge trends being explored. Key problems in the design and analysis of the hydrogen reservoir are also addressed. Finally, testing and certification requirements are discussed as they play an important role in industry acceptance.
The article covers the design of composite vessels from the physical and mechanical aspects. The design heavily relies on the properties of materials to the geometry. The design cycle of hydrogen tanks begins with general characteristics, such as the tank capacity, working pressure, material attributes, and safety factors. followed by dome design and fiber placement orientation. The same finite element technique has been widely used to predict the failure properties and strengths of composites based on different failure modalities. The ultimate goal of all of these techniques is to arrive at a reliable burst pressure. ensuring the design conforms to the local authorities' standard, the burst pressure design has to be optimized for safety and reliability. The article leaves on a positive note by talking about the prospect of h2 vessels.
The design of the composite vessel relates the physical and mechanical properties of materials to the geometry. Essentially, two main works are required for the design: one is the prediction of burst pressure and another is the optimization. The burst pressure denotes the limited load-carrying ability of the composite vessel. Since the failure mechanisms of composites are complicated from the view of composite micromechanics, including the matrix cracking, fiber/matrix debonding, and fiber breakage as well as their interactions. The optimization attempts to improve the weight, strength, reliability, and lifetime of the composite vessel by designing the wound angles and thickness.
A complete design cycle of a composite hydrogen tank is illustrated in the Figure below. The design cycle of hydrogen tanks begins with step no. 1, which defines the project's general characteristics, such as the tank capacity, working pressure, material attributes, and safety factors. The designer can use this information to compute other parameters that are required for the tank geometry definition, such as the cylinder radius, boss radius, and tank length.
The dome shape of composite tanks has a significant impact on their mechanical performance. The isotensoidal dome geometry, which is based on geodesic winding trajectories, is a common dome geometry. Parameters defined in step no. 1, such as the tank capacity, working pressure, and material characteristics, were the input parameters for the dome profile equations
The optimum dome shapes can be approximated as quasi-elliptic curves. The most important design parameter would be the depth of the elliptical dome. When the dome depths are between 0.6 and 0.775, designed domes present a stronger structure and greater internal volume.
The analytical design solution of composite hydrogen tanks is based on broad assumptions about load and boundary conditions and does not account for stiffness discontinuities near the polar boss. The finite element analysis (FEA) must be used to correctly model these and other effects in order to accurately predict the behavior of filament wound pressure vessels. Most filament wound pressure vessels exhibit first-order non-linear geometry effects, which can only be captured via the FEA.
The accuracy of the numerical analysis is mainly dependent upon the modeling technique and analysis conditions. The table below summarizes some approaches developed in the literature.
Composite tanks are wound using a combination of the alternate hoop and helical windings, whose main features are summarized in the table below. An alternate helical/hoop winding scheme is used to remove the excess resin and to obtain the target fiber volume fraction during the winding process.
Winding Type
Feature
Hoop winding
- Filaments are placed nearly perpendicular to the mandrel axis (α ≈ 90◦).
- Usually used with other strategies to resist circumferential stresses.
- Creates high consolidation pressure.
- Generally applied only to cylindrical sections.
- Placed at high speeds.
- Used to describe geodesics, non-geodesics and combinations thereof.
Low helical winding
- Winding angle varies (5◦ ≤ α ≤ 30◦).
- Low helical angle is used to strengthen the dome regions.
- Placed at moderate speeds.
- Used to describe geodesics, non-geodesics and combinations
thereof.
High helical winding
- Winding angle varies (60◦ ≤ α ≤ 80◦).
- High helical winding is used to strengthen the transition regions
between the cylinder and dome.
- Placed at moderate and high speeds.
- Used to describe geodesics, non-geodesics and combinations
thereof
Exploring the failure properties using progressive failure analysis as the aging of epoxy matrix leads to stiffness and strength degradation, thereby affecting the lifetime of the composite vessel.
There are two distinct failure mechanisms for the composite vessel: intralaminar damage and interlaminar delamination. From the burst experiments of composite vessels, the intralaminar damage instead of interlaminar delamination affects the mechanical performance of the composite vessel. This is because two neighboring composite layers still keep normally pressing and tangentially slipping despite a little interlaminar failure appearing before the burst. Thus, only intralaminar failure is generally considered.
Failure shows the degraded ability to resist the external load. The failure properties of a composite vessel depend on the geometry sizes, the material features, the loading history, and the environment. Over the past five decades, the popular failure criteria are the maximum stress, Hashin, Hoffman, Hinton, Christensen, Rotem, McCartney, Yamada-Sun, Chang-Chang, Tsai-Hill, Tsai-Wu, Puck and Huang’s criteria.
Currently, there is also an evolving trend to develop the fracture energy-based failure criteria to predict the failure of composites using such as the cohesive fracture energy-based criterion and finite element failure-based criterion. However, accurate prediction of fracture properties of composites requires advanced experimental techniques.
Essentially, progressive failure analysis of the composite vessel is to implement the proposed damage constitutive model, the failure criteria, and damage evolution law.
The flow chart for the progressive failure analysis of the composite vessel using the finite element method is illustrated in the figure above and summarized by five points:
The Burst pressure of the composite vessel is the ultimate aim of progressive failure analysis. The prediction of the burst pressure is essentially related to the numerical convergence problem in the finite element analysis. According to the design requirement of the composite vessel, only a little matrix cracking under working pressure is permitted. As the pressure increases, progressive interface debonding and matrix cracking appear. Only when a large number of fibers breakage suddenly appears is the composite vessel
considered to burst.
The aim of the design for the composite vessel is to reach the best match between reliability and practicability.
the working pressure of the composite vessel is taken as the burst pressure divided by the safety coefficient. However, the difficulty lies in how to select a proper safety coefficient which yet depends on the design and manufacturing levels. The CGH2R Draft Revision 10 of the European Union and the ISO/DIS 15869.2 specify the safety coefficients of 2.35 and 2.25, respectively. Then, the optimal design attempts to reach the minimum weight and highest strength under the constraint of the safety coefficient.
For a designed composite vessel, economy and practicability are based on safety and reliability. The reliability and lifetime of the composite vessel relate to many factors such as the material parameters, wound patterns, and manufacturing defects. It is not always feasible to expect to use a single safety coefficient to provide a guarantee for any occasional accident. Thus, it is necessary to develop reliability and lifetime-based methods to perform the probabilistic design.
In recent years, composite pressure vessels develop rapidly in the field of hydrogen storage. With the development of computer-aided design techniques, the composite vessel offers designers much design space. The design is to reach the ideal match among the reliability and lifetime, weight, and cost.
The above article is part of the course Design and Development of Compressed Hydrogen Storage Tanks. The course covers a lot more, starting with discussing challenges in material selection and manufacturing practices, as well as cutting-edge trends being explored. Key problems in the design and analysis of the hydrogen reservoir are also addressed. Finally, testing and certification requirements are discussed as they play an important role in industry acceptance.