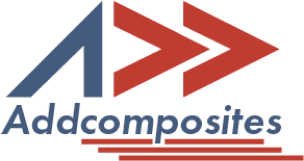
Understanding the key requirements of hydrogen storage for a given application provides a good initial ground for configuring the overall design including the liner shape. This article covers Liners details from the perspective of hydrogen tank storage. Following it up with the over-wrapping of a linerless liner for novel applications. In addition, the liners and the overwrapping materials also affect the performance and sustainability aspects of the H2 tank production. The article dives into thermoset-thermoplastic materials and related challenges. In addition, the article discusses different reinforcements in the context of the application. A summary is presented as a TLDR for the article towards the end.
In a composite pressure vessel, the liner is the component whose function is to act as a mechanical barrier between the fluid and the structural overwrap, preventing permeability from the several micro-cracks that are present in the substrate of composite layers. Materials employed in hydrogen tank construction should not only be safe, reliable, and cost-effective but should not interact or react with the gas.
Liners can be created using metal or plastics. Type II and III pressure vessels employ metallic liners usually composed of steel or aluminum alloys depending on the weight requirements. The manufacture of liners composed of metal is usually achieved with deep-drawing of plates, drawing of heated billets, or hot-spinning of tubes, followed by heat treatments performed to ensure the desired final mechanical properties. Metallic materials like steel in particular, may be at risk of embrittlement and stress corrosion cracking in the presence of hydrogen, leading to the occurrence of premature cracks and the consequent degradation of mechanical properties.
Plastic liners from type IV pressure vessels usually employ a thin layer of high-density polyethylene or aliphatic polyamide. Their manufacturing is obtained using rotomolding, blow molding, or by welding injected domes to an extruded polymer tube. However, polymeric liners present a higher permeability than their metallic counterpart, and, therefore, they need hydrogen permeation tests under high-pressure environments. Polymeric liners may also be vulnerable to collapse and blistering during tank charging and discharging and polymer water uptake could affect the performance of fuel cells.
Composites offer huge potential weight savings for reusable launch vehicles (RLVs). Especially for LH2 propellant tanks. However, as these LH2 tanks undergo cryogenic temperatures and high pressures usage of liners can cause thermal debonding and related issues. In addition, weight is a major concern for aerospace vehicles where tanks can exceed 50% dry weight of the launch vehicle. Given these constraints, linerless pressure vessels for space application have been developed and demonstrated. Below is a list of a few such demonstrated linerless pressure vessels for Cryogenic application
The overall design process of a composite hydrogen tank is closely connected to the liner shape definition, notably the dome region. Tanks for transportation are severely space-constrained and, therefore, must be sized to present a limited total length and diameter, while still providing the largest possible fuel capacity. Furthermore, the shape of the liner is greatly affected by constraints imposed by the fiber placement process, influencing fiber steering/gaps/overlaps and the reinforcement positioning/placement to provide equal strength through its structure. Optimizing the liner shape is usually the first step to maximizing the tank volume and minimizing its total mass.
The thermoelectric matrix once dominated the fiber-reinforced composite market. This includes products from various composite manufacturing technologies, such as resin transfer molding (RTM), resin transfer, extrusion, and filament winding. However, the use of fiber-reinforced thermoplastics instead of thermoset-based composites is gaining momentum in various industrial applications, mainly due to their short consolidation cycles, and reduced production time. Other advantages over thermoset construction include longer shelf life, ease of repair, and recyclability – the latter being a possibility that is particularly attractive for projects focused on a sustainable environment.
However, manufacturing problems limit the widespread use of thermoplastics because they tend to be more complex to handle than thermosets. Thermoplastics are exceptionally high molecular weight, with melt viscosity at least two orders of magnitude higher than that observed in thermoset resins, making their impregnation considerably more difficult. . However, great efforts have been devoted to the development of new techniques and easier-to-handle thermoplastics.
An interesting strategy to improve the manufacturability of thermoplastics has been developed by replacing the fiber impregnation step in the manufacturing process. Accordingly, the impregnation of fibers with thermoplastics is first carried out in a separate process by making special pre-impregnated or tensile tapes, usually supplied in wide sheets or narrow strips with the layout. one-way unit. . Prepreg products have low void content and high fiber volumetric ratio and thermoplastic options are commercially available in different configurations (carbon/PEEK, carbon/PA6, and carbon/PPS).
The employment of thermoplastics has become a green trend due to its potential for the partial or even full recycling of raw materials. Current end-of-life options for carbon-fiber-reinforced thermoplastics consist of:
An important aspect of the hydrogen tank project is a selection of reinforcements as it provides the tank with high sealing strength, a quality important for high-pressure applications that directly impact the burst and puncture resistance.
Carbon fibers are the most common choice for today's modern hydrogen storage solutions due to their high specific tensile strength. They also combine exceptional fatigue performance and resistance to creep and most chemicals. However, carbon fiber alone represents the main cost driver for hydrogen storage systems and their overall demand will increase significantly, so alternative reinforcing fibers have been the subject of extensive research to optimize the cost of storage tanks.
Glass fiber is commonly used as a reinforcing coating in compressed natural gas (CNG) tanks, operates at significantly lower pressures, and is also present in hydrogen tanks as an outer layer, providing both resistance to corrosion and galvanic damage. Glass is a relatively inexpensive material, but it can degrade in strength when exposed to moisture/chemicals and constant loads.
The introduced basalt fiber is a competitive eco-friendly fiber with slightly better mechanical properties and thermochemical stability than glass fiber E. In comparison, the stiffness of basalt can be estimated by half carbon fiber, while its cost is only one-tenth. The weight of a basalt pressure vessel is estimated to be 15% less than that of similar E-glass vessels of the same strength, although such a configuration is still much heavier than a carbon vessel.
Liner is the component whose function is to act as a mechanical barrier between the fluid and the structural overwrap. Optimizing the liner shape is usually the first step to maximizing the tank volume and minimizing its total mass. The employment of thermoplastics has become a green trend due to its potential for the partial or even full recycling of raw materials. The selection of reinforcements is highly important as it provides the tank with high sealing strength. The overall key takeaway from the gained knowledge is designed for the application, so the suggestion here is more for informational purposes. Please do your own research before finalizing your own application.
The above article is part of the course Design and Development of Compressed Hydrogen Storage Tanks. The course covers a lot more, starting with discussing challenges in material selection and manufacturing practices, as well as cutting-edge trends being explored. Key problems in the design and analysis of the hydrogen reservoir are also addressed. Finally, testing and certification requirements are discussed as they play an important role in industry acceptance.
Understanding the key requirements of hydrogen storage for a given application provides a good initial ground for configuring the overall design including the liner shape. This article covers Liners details from the perspective of hydrogen tank storage. Following it up with the over-wrapping of a linerless liner for novel applications. In addition, the liners and the overwrapping materials also affect the performance and sustainability aspects of the H2 tank production. The article dives into thermoset-thermoplastic materials and related challenges. In addition, the article discusses different reinforcements in the context of the application. A summary is presented as a TLDR for the article towards the end.
In a composite pressure vessel, the liner is the component whose function is to act as a mechanical barrier between the fluid and the structural overwrap, preventing permeability from the several micro-cracks that are present in the substrate of composite layers. Materials employed in hydrogen tank construction should not only be safe, reliable, and cost-effective but should not interact or react with the gas.
Liners can be created using metal or plastics. Type II and III pressure vessels employ metallic liners usually composed of steel or aluminum alloys depending on the weight requirements. The manufacture of liners composed of metal is usually achieved with deep-drawing of plates, drawing of heated billets, or hot-spinning of tubes, followed by heat treatments performed to ensure the desired final mechanical properties. Metallic materials like steel in particular, may be at risk of embrittlement and stress corrosion cracking in the presence of hydrogen, leading to the occurrence of premature cracks and the consequent degradation of mechanical properties.
Plastic liners from type IV pressure vessels usually employ a thin layer of high-density polyethylene or aliphatic polyamide. Their manufacturing is obtained using rotomolding, blow molding, or by welding injected domes to an extruded polymer tube. However, polymeric liners present a higher permeability than their metallic counterpart, and, therefore, they need hydrogen permeation tests under high-pressure environments. Polymeric liners may also be vulnerable to collapse and blistering during tank charging and discharging and polymer water uptake could affect the performance of fuel cells.
Composites offer huge potential weight savings for reusable launch vehicles (RLVs). Especially for LH2 propellant tanks. However, as these LH2 tanks undergo cryogenic temperatures and high pressures usage of liners can cause thermal debonding and related issues. In addition, weight is a major concern for aerospace vehicles where tanks can exceed 50% dry weight of the launch vehicle. Given these constraints, linerless pressure vessels for space application have been developed and demonstrated. Below is a list of a few such demonstrated linerless pressure vessels for Cryogenic application
The overall design process of a composite hydrogen tank is closely connected to the liner shape definition, notably the dome region. Tanks for transportation are severely space-constrained and, therefore, must be sized to present a limited total length and diameter, while still providing the largest possible fuel capacity. Furthermore, the shape of the liner is greatly affected by constraints imposed by the fiber placement process, influencing fiber steering/gaps/overlaps and the reinforcement positioning/placement to provide equal strength through its structure. Optimizing the liner shape is usually the first step to maximizing the tank volume and minimizing its total mass.
The thermoelectric matrix once dominated the fiber-reinforced composite market. This includes products from various composite manufacturing technologies, such as resin transfer molding (RTM), resin transfer, extrusion, and filament winding. However, the use of fiber-reinforced thermoplastics instead of thermoset-based composites is gaining momentum in various industrial applications, mainly due to their short consolidation cycles, and reduced production time. Other advantages over thermoset construction include longer shelf life, ease of repair, and recyclability – the latter being a possibility that is particularly attractive for projects focused on a sustainable environment.
However, manufacturing problems limit the widespread use of thermoplastics because they tend to be more complex to handle than thermosets. Thermoplastics are exceptionally high molecular weight, with melt viscosity at least two orders of magnitude higher than that observed in thermoset resins, making their impregnation considerably more difficult. . However, great efforts have been devoted to the development of new techniques and easier-to-handle thermoplastics.
An interesting strategy to improve the manufacturability of thermoplastics has been developed by replacing the fiber impregnation step in the manufacturing process. Accordingly, the impregnation of fibers with thermoplastics is first carried out in a separate process by making special pre-impregnated or tensile tapes, usually supplied in wide sheets or narrow strips with the layout. one-way unit. . Prepreg products have low void content and high fiber volumetric ratio and thermoplastic options are commercially available in different configurations (carbon/PEEK, carbon/PA6, and carbon/PPS).
The employment of thermoplastics has become a green trend due to its potential for the partial or even full recycling of raw materials. Current end-of-life options for carbon-fiber-reinforced thermoplastics consist of:
An important aspect of the hydrogen tank project is a selection of reinforcements as it provides the tank with high sealing strength, a quality important for high-pressure applications that directly impact the burst and puncture resistance.
Carbon fibers are the most common choice for today's modern hydrogen storage solutions due to their high specific tensile strength. They also combine exceptional fatigue performance and resistance to creep and most chemicals. However, carbon fiber alone represents the main cost driver for hydrogen storage systems and their overall demand will increase significantly, so alternative reinforcing fibers have been the subject of extensive research to optimize the cost of storage tanks.
Glass fiber is commonly used as a reinforcing coating in compressed natural gas (CNG) tanks, operates at significantly lower pressures, and is also present in hydrogen tanks as an outer layer, providing both resistance to corrosion and galvanic damage. Glass is a relatively inexpensive material, but it can degrade in strength when exposed to moisture/chemicals and constant loads.
The introduced basalt fiber is a competitive eco-friendly fiber with slightly better mechanical properties and thermochemical stability than glass fiber E. In comparison, the stiffness of basalt can be estimated by half carbon fiber, while its cost is only one-tenth. The weight of a basalt pressure vessel is estimated to be 15% less than that of similar E-glass vessels of the same strength, although such a configuration is still much heavier than a carbon vessel.
Liner is the component whose function is to act as a mechanical barrier between the fluid and the structural overwrap. Optimizing the liner shape is usually the first step to maximizing the tank volume and minimizing its total mass. The employment of thermoplastics has become a green trend due to its potential for the partial or even full recycling of raw materials. The selection of reinforcements is highly important as it provides the tank with high sealing strength. The overall key takeaway from the gained knowledge is designed for the application, so the suggestion here is more for informational purposes. Please do your own research before finalizing your own application.
The above article is part of the course Design and Development of Compressed Hydrogen Storage Tanks. The course covers a lot more, starting with discussing challenges in material selection and manufacturing practices, as well as cutting-edge trends being explored. Key problems in the design and analysis of the hydrogen reservoir are also addressed. Finally, testing and certification requirements are discussed as they play an important role in industry acceptance.