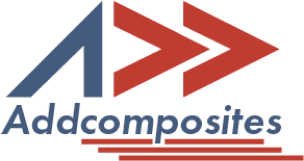
Manufacturing aerospace structures with Automated Fiber Placement (AFP) presents a blend of opportunities and challenges. AFP, a leading method in composite manufacturing, is celebrated for its ability to construct stronger, lighter, and more efficient aerospace structures compared to traditional materials. Major aircraft manufacturers and space industry companies are increasingly adopting AFP for its precision and efficiency in creating complex composite structures.
The AFP process, characterized by the robotic layup of material strips on a tool surface, entails rigorous process planning to achieve optimal results. However, the intricate interactions between the tows, the underlying tool surface geometry, and the process limitations introduce various potential defects. These defects, including gaps, overlaps, wrinkles, and more, can significantly impact the mechanical integrity and performance of the final composite laminate.
To address these challenges, a comprehensive approach involving Computer Aided Process Planning (CAPP) tools and combinatorial optimization algorithms is employed. CAPP aids in identifying optimal layup strategies for each ply, focusing on minimizing defects such as gaps and overlaps, which are critical for maintaining the structural integrity of the laminate. By leveraging advanced algorithms like genetic algorithm, differential evolution, particle swarm, and greedy search, optimal combinations of ply-level layup strategies are identified, significantly reducing defect stacking within the laminate's thickness.
In the quest to enhance the structural integrity and performance of composite materials, the AFP process is pivotal, especially in aerospace manufacturing. AFP's potential, however, is often undermined by the occurrence of through-thickness defects such as gaps and overlaps. These defects, when stacked across multiple layers (plies) of a laminate, can significantly weaken the material's mechanical properties.
A novel approach to identifying and quantifying these stacked defects involves discretizing each ply into binary arrays, where '1' denotes a defect and '0' indicates defect-free areas. This method allows for a precise through-thickness comparison, culminating in a 3D array model that encapsulates the entire defect distribution within the laminate. By summing the defects through the third dimension of this array, areas prone to high defect stacking are identified, providing a visual and quantitative basis for optimization.
Furthermore, the severity of defect stacking is quantified through a scoring system, distinguishing between levels of defect accumulation. This "levels concept" serves as a foundation for both global and local scoring methods, facilitating a comprehensive evaluation of the defect distribution and its impact on laminate strength and reliability.
This challenge necessitates advanced optimization strategies to mitigate the adverse effects of defect stacking. By employing combinatorial optimization algorithms—such as genetic algorithms, differential evolution, and particle swarm optimization—alongside a Computer Aided Process Planning (CAPP) tool, the AFP process can be optimized. This optimization aims to reduce defect stacking, thereby enhancing the material's mechanical properties and extending its application potential in critical aerospace structures.
The ramifications of unaddressed through-thickness defects are profound, potentially compromising the safety and performance of aerospace structures. Hence, the development and implementation of sophisticated defect management and optimization techniques are not just beneficial but essential for the advancement of composite material manufacturing.
In the realm of AFP for composite material manufacturing, particularly within aerospace engineering, the pursuit of minimizing defects such as gaps and overlaps through the thickness of composite laminates is a critical challenge. We focus on implementation and evaluation of four distinct combinatorial optimization algorithms:
all aimed at enhancing the AFP process.
These algorithms are employed within a Computer Aided Process Planning (CAPP) tool framework to identify the most effective ply-level layup strategies. By analyzing defect stacking using two objective functions—global and local scores—these methods seek to optimize the placement of composite material strips, thereby reducing the likelihood of defect stacking that can compromise the structural integrity and performance of the final composite laminate.
A digital case study on a complex tool surface outlines the experimentation setup, revealing how each algorithm processes a randomized design space of 20 plies with five scenarios per ply. The optimization tasks are computationally executed on a standard PC setup, showcasing the practical feasibility of these algorithms in real-world manufacturing environments.
The results underscore the significant potential of these algorithms in minimizing defect stacking within laminates. The genetic algorithm and differential evolution, in particular, demonstrated superior performance in reducing global and local defect scores, indicating less gap and overlap defect stacking. This optimized laminate manufacturing strategy not only promises to enhance the structural integrity of composite materials but also streamlines the manufacturing process, making it more efficient and cost-effective.
The exploration of these optimization algorithms represents a pioneering step towards mitigating the challenges associated with AFP manufacturing. By integrating these advanced computational techniques, manufacturers can achieve higher-quality composite structures, driving forward the capabilities and applications of composite materials in aerospace and beyond.
The culmination of efforts in optimizing the AFP process for composite manufacturing has led to significant advancements in achieving precision and efficiency through advanced layup strategies. These strategies are centered around minimizing defects, particularly those that affect the through-thickness integrity of composite laminates, such as gaps and overlaps. By leveraging a sophisticated CAPP tool in conjunction with cutting-edge combinatorial optimization algorithms, the research presents a robust methodology for enhancing the quality and performance of composite materials.
The CAPP tool plays a pivotal role in this optimization process by facilitating the identification of optimal starting points and layup strategies for each ply within a laminate. This tool, developed to expedite and refine the process planning workflow for AFP, incorporates Ply Level Optimization (PLO) functions that measure and score geometry-based defects. This approach is further extended to Laminate Level Optimization (LLO), selecting the best combination of ply-level inputs to construct the complete laminate with minimal defect stacking.
Four distinct combinatorial optimization algorithms—Genetic Algorithm (GA), Differential Evolution (DE), Particle Swarm Optimization (PS), and Greedy Search (GS)—are evaluated for their efficacy in minimizing defect stacking. These algorithms are applied within the CAPP framework, showcasing their potential to significantly reduce gaps and overlaps through innovative ply and laminate-level strategies.
A digital case study illustrates the practical application of these optimization strategies, highlighting the potential for increased design allowables and eliminating knockdowns for gap and overlap defects. This not only enables more efficient designs but also promises savings in manufacturing time and material costs. The study's approach could be adapted to optimize defect stacking for laminates with tow-steering or variable stiffness, broadening the scope of applications in composite manufacturing.
This research represents a leap forward in process planning for AFP, providing a comprehensive toolkit for minimizing defect stacking and enhancing the overall quality of composite laminates. The integration of advanced optimization algorithms with CAPP tools marks a significant advancement in the pursuit of precision and efficiency in composite manufacturing, promising a future where composite structures are produced with unprecedented accuracy and reliability.
We extend our sincere gratitude to Noah Swingle, Alex Brasington, Joshua Halbritter, and Ramy Harik from the University of South Carolina, McNair Center Department of Mechanical Engineering, for their invaluable contributions to the research and writing of the document on "Optimization for Mitigation: Automated Fiber Placement Laminate Level Optimization for Mitigation of Through Thickness Defect Stacking." Their dedication to advancing the field of composite manufacturing and automated fiber placement technology has significantly enriched the content and insights shared in this blog.
Discover the future of composite manufacturing with Addcomposites! Here's how you can get involved:
At Addcomposites, we are dedicated to revolutionizing composite manufacturing. Our AFP systems and comprehensive support services are waiting for you to harness. So, don't wait – get started on your journey to the future of manufacturing today!
Manufacturing aerospace structures with Automated Fiber Placement (AFP) presents a blend of opportunities and challenges. AFP, a leading method in composite manufacturing, is celebrated for its ability to construct stronger, lighter, and more efficient aerospace structures compared to traditional materials. Major aircraft manufacturers and space industry companies are increasingly adopting AFP for its precision and efficiency in creating complex composite structures.
The AFP process, characterized by the robotic layup of material strips on a tool surface, entails rigorous process planning to achieve optimal results. However, the intricate interactions between the tows, the underlying tool surface geometry, and the process limitations introduce various potential defects. These defects, including gaps, overlaps, wrinkles, and more, can significantly impact the mechanical integrity and performance of the final composite laminate.
To address these challenges, a comprehensive approach involving Computer Aided Process Planning (CAPP) tools and combinatorial optimization algorithms is employed. CAPP aids in identifying optimal layup strategies for each ply, focusing on minimizing defects such as gaps and overlaps, which are critical for maintaining the structural integrity of the laminate. By leveraging advanced algorithms like genetic algorithm, differential evolution, particle swarm, and greedy search, optimal combinations of ply-level layup strategies are identified, significantly reducing defect stacking within the laminate's thickness.
In the quest to enhance the structural integrity and performance of composite materials, the AFP process is pivotal, especially in aerospace manufacturing. AFP's potential, however, is often undermined by the occurrence of through-thickness defects such as gaps and overlaps. These defects, when stacked across multiple layers (plies) of a laminate, can significantly weaken the material's mechanical properties.
A novel approach to identifying and quantifying these stacked defects involves discretizing each ply into binary arrays, where '1' denotes a defect and '0' indicates defect-free areas. This method allows for a precise through-thickness comparison, culminating in a 3D array model that encapsulates the entire defect distribution within the laminate. By summing the defects through the third dimension of this array, areas prone to high defect stacking are identified, providing a visual and quantitative basis for optimization.
Furthermore, the severity of defect stacking is quantified through a scoring system, distinguishing between levels of defect accumulation. This "levels concept" serves as a foundation for both global and local scoring methods, facilitating a comprehensive evaluation of the defect distribution and its impact on laminate strength and reliability.
This challenge necessitates advanced optimization strategies to mitigate the adverse effects of defect stacking. By employing combinatorial optimization algorithms—such as genetic algorithms, differential evolution, and particle swarm optimization—alongside a Computer Aided Process Planning (CAPP) tool, the AFP process can be optimized. This optimization aims to reduce defect stacking, thereby enhancing the material's mechanical properties and extending its application potential in critical aerospace structures.
The ramifications of unaddressed through-thickness defects are profound, potentially compromising the safety and performance of aerospace structures. Hence, the development and implementation of sophisticated defect management and optimization techniques are not just beneficial but essential for the advancement of composite material manufacturing.
In the realm of AFP for composite material manufacturing, particularly within aerospace engineering, the pursuit of minimizing defects such as gaps and overlaps through the thickness of composite laminates is a critical challenge. We focus on implementation and evaluation of four distinct combinatorial optimization algorithms:
all aimed at enhancing the AFP process.
These algorithms are employed within a Computer Aided Process Planning (CAPP) tool framework to identify the most effective ply-level layup strategies. By analyzing defect stacking using two objective functions—global and local scores—these methods seek to optimize the placement of composite material strips, thereby reducing the likelihood of defect stacking that can compromise the structural integrity and performance of the final composite laminate.
A digital case study on a complex tool surface outlines the experimentation setup, revealing how each algorithm processes a randomized design space of 20 plies with five scenarios per ply. The optimization tasks are computationally executed on a standard PC setup, showcasing the practical feasibility of these algorithms in real-world manufacturing environments.
The results underscore the significant potential of these algorithms in minimizing defect stacking within laminates. The genetic algorithm and differential evolution, in particular, demonstrated superior performance in reducing global and local defect scores, indicating less gap and overlap defect stacking. This optimized laminate manufacturing strategy not only promises to enhance the structural integrity of composite materials but also streamlines the manufacturing process, making it more efficient and cost-effective.
The exploration of these optimization algorithms represents a pioneering step towards mitigating the challenges associated with AFP manufacturing. By integrating these advanced computational techniques, manufacturers can achieve higher-quality composite structures, driving forward the capabilities and applications of composite materials in aerospace and beyond.
The culmination of efforts in optimizing the AFP process for composite manufacturing has led to significant advancements in achieving precision and efficiency through advanced layup strategies. These strategies are centered around minimizing defects, particularly those that affect the through-thickness integrity of composite laminates, such as gaps and overlaps. By leveraging a sophisticated CAPP tool in conjunction with cutting-edge combinatorial optimization algorithms, the research presents a robust methodology for enhancing the quality and performance of composite materials.
The CAPP tool plays a pivotal role in this optimization process by facilitating the identification of optimal starting points and layup strategies for each ply within a laminate. This tool, developed to expedite and refine the process planning workflow for AFP, incorporates Ply Level Optimization (PLO) functions that measure and score geometry-based defects. This approach is further extended to Laminate Level Optimization (LLO), selecting the best combination of ply-level inputs to construct the complete laminate with minimal defect stacking.
Four distinct combinatorial optimization algorithms—Genetic Algorithm (GA), Differential Evolution (DE), Particle Swarm Optimization (PS), and Greedy Search (GS)—are evaluated for their efficacy in minimizing defect stacking. These algorithms are applied within the CAPP framework, showcasing their potential to significantly reduce gaps and overlaps through innovative ply and laminate-level strategies.
A digital case study illustrates the practical application of these optimization strategies, highlighting the potential for increased design allowables and eliminating knockdowns for gap and overlap defects. This not only enables more efficient designs but also promises savings in manufacturing time and material costs. The study's approach could be adapted to optimize defect stacking for laminates with tow-steering or variable stiffness, broadening the scope of applications in composite manufacturing.
This research represents a leap forward in process planning for AFP, providing a comprehensive toolkit for minimizing defect stacking and enhancing the overall quality of composite laminates. The integration of advanced optimization algorithms with CAPP tools marks a significant advancement in the pursuit of precision and efficiency in composite manufacturing, promising a future where composite structures are produced with unprecedented accuracy and reliability.
We extend our sincere gratitude to Noah Swingle, Alex Brasington, Joshua Halbritter, and Ramy Harik from the University of South Carolina, McNair Center Department of Mechanical Engineering, for their invaluable contributions to the research and writing of the document on "Optimization for Mitigation: Automated Fiber Placement Laminate Level Optimization for Mitigation of Through Thickness Defect Stacking." Their dedication to advancing the field of composite manufacturing and automated fiber placement technology has significantly enriched the content and insights shared in this blog.
Discover the future of composite manufacturing with Addcomposites! Here's how you can get involved:
At Addcomposites, we are dedicated to revolutionizing composite manufacturing. Our AFP systems and comprehensive support services are waiting for you to harness. So, don't wait – get started on your journey to the future of manufacturing today!