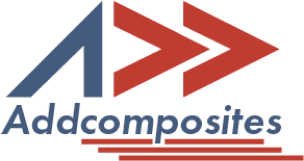
The manufacturing of composite materials presents numerous challenges, chief among them being the occurrence of defects which can significantly hamper the usability and structural integrity of the final products. In industries where composites are pivotal—such as aerospace, automotive, and renewable energy—the impact of these defects goes beyond mere financial losses to encompass safety risks and reduced efficiency.
Defects in composite materials typically manifest during the manufacturing process due to inadequate control over variables such as temperature, pressure, and material consistency. The types of defects include porosity, wrinkles, and misalignments of fibers, which can all lead to compromised material strength and durability. This problem is compounded by the high costs and inefficiencies associated with traditional methods for defect detection and mitigation. These methods often involve extensive trial and error, requiring substantial material consumption and time.
The need to address these challenges is not just about improving material quality, but also about advancing towards more sustainable manufacturing practices. The reduction in waste material directly contributes to environmental sustainability goals, particularly in light of global pushes towards net-zero targets in major industries.
The production of composite materials offers significant benefits, such as high strength-to-weight ratio and durability. However, the manufacturing process is plagued by a critical issue: the high incidence of defects, which include:
These defects not only compromise the structural integrity of the final product but also lead to substantial material waste and financial losses. The traditional approach to mitigating these manufacturing defects involves extensive experimental trials, which are costly, time-consuming, and require significant amounts of raw materials that, if the trials fail, end up as waste. This trial-and-error process exacerbates the cost issues, as each experiment involves additional:
All of these factors contribute to the overheads. Moreover, the environmental impact of this waste cannot be overlooked. In an era where industries are being pushed towards sustainability, the composite manufacturing sector faces pressure to reduce waste and enhance process efficiency.
In tackling these pain points, the necessity for innovative approaches that reduce reliance on physical trials is highlighted. By implementing more sophisticated predictive and optimization technologies, manufacturers can foresee potential defect occurrences and adjust parameters proactively, thereby reducing waste and improving the cost-effectiveness of the production process.
In response to the costly challenges posed by defect-induced waste in composite materials manufacturing, significant strides have been made in the realm of process modeling and optimization. The focus has shifted towards leveraging advanced simulation tools that enable manufacturers to predict and thus prevent defects before they manifest in the physical products.
The core of these advancements lies in:
Additionally, the integration of data-driven methodologies into the manufacturing process marks a pivotal improvement.
The practical application of these techniques has been validated through various initiatives, which have demonstrated significant improvements in defect mitigation. For instance, by optimizing the design of a caul plate based on simulation data, manufacturers have been able to eliminate common defects such as out-of-plane wrinkles and inhomogeneities in thickness.
The culmination of advancements in simulation and optimization techniques has led to a groundbreaking achievement in the field of composites manufacturing: the realization of zero-defect production processes. This section explores the results and effectiveness of implementing new data-driven methods that harness machine learning to optimize the manufacturing of composite parts.
The novel approach integrates a homogenized framework with advanced machine learning algorithms, such as Gaussian Process Regression (GPR) and Differential Evolution (DE), to form a robust predictive and optimization platform. This setup allows for the precise tuning of manufacturing parameters in real-time, drastically reducing the occurrence of defects. By simulating the entire manufacturing process under various conditions, the system can predict potential failure points and suggest adjustments to the caul plate design and process parameters that preemptively mitigate these issues.
A key case study highlighted involves the use of a data-driven optimization process to redesign a caul plate used in the autoclave molding of a complex aerospace component. This optimized caul plate design was then applied in a physical manufacturing trial, which resulted in a part that met all specified quality standards without any detectable defects. This trial not only proved the practical viability of the method but also demonstrated a 25% improvement in the maximum local deviation from the ideal part design.
Furthermore, the successful application of these techniques has significant implications for cost savings and sustainability. Reducing the rate of defect occurrence minimizes waste material and decreases the need for costly rework and scrap. Additionally, the ability to achieve zero defects enhances the efficiency of the production process, leading to faster turnaround times and lower energy consumption.
We owe a tremendous debt of gratitude to Dr. Yi Wang, Dr. Siyuan Chen, Iryna Tretiak, Professor Stephen R. Hallett, and Professor Jonathan P.-H. Belnoue for their invaluable contributions to the research presented in "Virtual data-driven optimisation for zero defect composites manufacture." Their collective expertise and dedication have significantly advanced our understanding of composite manufacturing processes, leading to the innovative strategies outlined in this study.
Their work, meticulously detailed in the paper, underscores the power of collaboration and specialized knowledge in overcoming the challenges of composite material manufacturing. We commend their commitment to excellence and their role in pushing the boundaries of what's technically achievable in the industry.
By sharing their findings, they continue to inspire and guide future innovations, shaping the next generation of manufacturing technologies. We are profoundly thankful for their pioneering efforts and are excited to see how their groundbreaking work will transform the field.
Discover the future of composite manufacturing with Addcomposites! Here's how you can get involved:
At Addcomposites, we are dedicated to revolutionizing composite manufacturing. Our AFP systems and comprehensive support services are waiting for you to harness. So, don't wait – get started on your journey to the future of manufacturing today!
The manufacturing of composite materials presents numerous challenges, chief among them being the occurrence of defects which can significantly hamper the usability and structural integrity of the final products. In industries where composites are pivotal—such as aerospace, automotive, and renewable energy—the impact of these defects goes beyond mere financial losses to encompass safety risks and reduced efficiency.
Defects in composite materials typically manifest during the manufacturing process due to inadequate control over variables such as temperature, pressure, and material consistency. The types of defects include porosity, wrinkles, and misalignments of fibers, which can all lead to compromised material strength and durability. This problem is compounded by the high costs and inefficiencies associated with traditional methods for defect detection and mitigation. These methods often involve extensive trial and error, requiring substantial material consumption and time.
The need to address these challenges is not just about improving material quality, but also about advancing towards more sustainable manufacturing practices. The reduction in waste material directly contributes to environmental sustainability goals, particularly in light of global pushes towards net-zero targets in major industries.
The production of composite materials offers significant benefits, such as high strength-to-weight ratio and durability. However, the manufacturing process is plagued by a critical issue: the high incidence of defects, which include:
These defects not only compromise the structural integrity of the final product but also lead to substantial material waste and financial losses. The traditional approach to mitigating these manufacturing defects involves extensive experimental trials, which are costly, time-consuming, and require significant amounts of raw materials that, if the trials fail, end up as waste. This trial-and-error process exacerbates the cost issues, as each experiment involves additional:
All of these factors contribute to the overheads. Moreover, the environmental impact of this waste cannot be overlooked. In an era where industries are being pushed towards sustainability, the composite manufacturing sector faces pressure to reduce waste and enhance process efficiency.
In tackling these pain points, the necessity for innovative approaches that reduce reliance on physical trials is highlighted. By implementing more sophisticated predictive and optimization technologies, manufacturers can foresee potential defect occurrences and adjust parameters proactively, thereby reducing waste and improving the cost-effectiveness of the production process.
In response to the costly challenges posed by defect-induced waste in composite materials manufacturing, significant strides have been made in the realm of process modeling and optimization. The focus has shifted towards leveraging advanced simulation tools that enable manufacturers to predict and thus prevent defects before they manifest in the physical products.
The core of these advancements lies in:
Additionally, the integration of data-driven methodologies into the manufacturing process marks a pivotal improvement.
The practical application of these techniques has been validated through various initiatives, which have demonstrated significant improvements in defect mitigation. For instance, by optimizing the design of a caul plate based on simulation data, manufacturers have been able to eliminate common defects such as out-of-plane wrinkles and inhomogeneities in thickness.
The culmination of advancements in simulation and optimization techniques has led to a groundbreaking achievement in the field of composites manufacturing: the realization of zero-defect production processes. This section explores the results and effectiveness of implementing new data-driven methods that harness machine learning to optimize the manufacturing of composite parts.
The novel approach integrates a homogenized framework with advanced machine learning algorithms, such as Gaussian Process Regression (GPR) and Differential Evolution (DE), to form a robust predictive and optimization platform. This setup allows for the precise tuning of manufacturing parameters in real-time, drastically reducing the occurrence of defects. By simulating the entire manufacturing process under various conditions, the system can predict potential failure points and suggest adjustments to the caul plate design and process parameters that preemptively mitigate these issues.
A key case study highlighted involves the use of a data-driven optimization process to redesign a caul plate used in the autoclave molding of a complex aerospace component. This optimized caul plate design was then applied in a physical manufacturing trial, which resulted in a part that met all specified quality standards without any detectable defects. This trial not only proved the practical viability of the method but also demonstrated a 25% improvement in the maximum local deviation from the ideal part design.
Furthermore, the successful application of these techniques has significant implications for cost savings and sustainability. Reducing the rate of defect occurrence minimizes waste material and decreases the need for costly rework and scrap. Additionally, the ability to achieve zero defects enhances the efficiency of the production process, leading to faster turnaround times and lower energy consumption.
We owe a tremendous debt of gratitude to Dr. Yi Wang, Dr. Siyuan Chen, Iryna Tretiak, Professor Stephen R. Hallett, and Professor Jonathan P.-H. Belnoue for their invaluable contributions to the research presented in "Virtual data-driven optimisation for zero defect composites manufacture." Their collective expertise and dedication have significantly advanced our understanding of composite manufacturing processes, leading to the innovative strategies outlined in this study.
Their work, meticulously detailed in the paper, underscores the power of collaboration and specialized knowledge in overcoming the challenges of composite material manufacturing. We commend their commitment to excellence and their role in pushing the boundaries of what's technically achievable in the industry.
By sharing their findings, they continue to inspire and guide future innovations, shaping the next generation of manufacturing technologies. We are profoundly thankful for their pioneering efforts and are excited to see how their groundbreaking work will transform the field.
Discover the future of composite manufacturing with Addcomposites! Here's how you can get involved:
At Addcomposites, we are dedicated to revolutionizing composite manufacturing. Our AFP systems and comprehensive support services are waiting for you to harness. So, don't wait – get started on your journey to the future of manufacturing today!