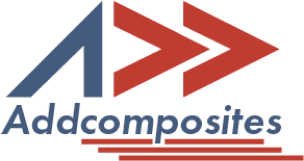
The integration of advanced composite materials has revolutionized the automotive industry by enhancing vehicle performance through innovative structural designs and superior mechanical properties. This introduction outlines the significance of composite materials, particularly honeycomb structures, in automotive applications, detailing their impact on performance, safety, and sustainability.
Advanced Composites in the Automotive Industry
Honeycomb Structures: Core of Innovation
Application and Impact
Overcoming the limitations of traditional materials in automotive applications is a key driver for the adoption of advanced composites like honeycomb structures. Here are the major limitations of traditional materials and how advanced composites address these challenges:
Fabrication Technique
Advantages
Applications
Resin Transfer Molding (RTM)
High fiber volume fractions, consistent quality, complex shapes
Structural components, body panels
Compression Molding
Near-net-shape components, high production volumes
Sheet Molding Compounds (SMCs), Bulk Molding Compounds (BMCs)
Automated Fiber Placement (AFP) and Automated Tape Laying (ATL)
Precise fiber placement, highly optimized structures
Large and complex structures
Filament Winding
High strength-to-weight ratio, suitable for cylindrical parts
Pressure vessels, drive shafts
Vacuum Infusion
Large components, low-volume production
Body panels, structural parts
The automotive industry is witnessing a paradigm shift towards lightweight, high-performance components, and composite materials are at the forefront of this revolution. By leveraging the unique properties and advanced fabrication techniques of composites, manufacturers are unlocking new possibilities in vehicle design and performance.
Composite materials offer a wide range of applications in the automotive sector. One prominent example is their use in structural components such as chassis, body panels, and suspension systems. By replacing traditional metal parts with composite alternatives, significant weight reductions can be achieved without compromising strength or stiffness. This translates to improved fuel efficiency, reduced emissions, and enhanced vehicle dynamics.
Another key application of composites is in the development of lightweight and high-performance brake systems. Composite brake pads and rotors offer superior wear resistance, thermal stability, and noise reduction compared to conventional materials. This not only enhances the braking performance but also extends the service life of the components.
Composites are also revolutionizing the design of automotive interiors. Lightweight composite seat structures, door panels, and dashboard components contribute to overall vehicle weight reduction while offering improved aesthetics and functionality. The ability to mold composites into complex shapes allows for the integration of features such as built-in sensors, heating elements, and acoustic insulation.
In the realm of powertrain components, composites are finding applications in engine parts, transmission systems, and exhaust components. The high thermal and chemical resistance of ceramic matrix composites (CMCs) makes them suitable for high-temperature applications, such as turbocharger housings and exhaust manifolds. The use of composites in these areas helps to reduce weight, improve heat management, and enhance the overall efficiency of the powertrain.
The automotive industry is also exploring the potential of natural fiber composites as a sustainable and eco-friendly alternative to traditional materials. Natural fibers such as flax, hemp, and jute, when combined with biodegradable polymer matrices, offer a reduced environmental impact while maintaining comparable mechanical properties. These bio-composites are finding applications in non-structural components such as interior trim, door panels, and trunk liners.
To fully realize the potential of composite materials, close collaboration between material scientists, engineers, and designers is essential. The development of advanced simulation tools and testing methods is crucial for predicting the behavior of composite components under various loading conditions. Additionally, establishing robust supply chains and investing in specialized manufacturing facilities are key to scaling up the production of composite parts.
let's thank the authors Fardin Khan, Nayem Hossain, Juhi Jannat Mim, SM Maksudur Rahman, Md. Jayed Iqbal, Mostakim Billah, and Mohammad Asaduzzaman Chowdhury for their valuable contribution in writing the research paper titled "Advances of composite materials in automobile applications – A review" which was published in the Journal of Engineering Research. Their extensive research and insights have provided the foundation for this informative blog post, shedding light on the revolutionary role of composite materials in the automotive industry. We greatly appreciate their dedication and expertise in this field, as their work has significantly contributed to the advancements discussed throughout this blog.
Discover the future of composite manufacturing with Addcomposites! Here's how you can get involved:
At Addcomposites, we are dedicated to revolutionizing composite manufacturing. Our AFP systems and comprehensive support services are waiting for you to harness. So, don't wait – get started on your journey to the future of manufacturing today!
The integration of advanced composite materials has revolutionized the automotive industry by enhancing vehicle performance through innovative structural designs and superior mechanical properties. This introduction outlines the significance of composite materials, particularly honeycomb structures, in automotive applications, detailing their impact on performance, safety, and sustainability.
Advanced Composites in the Automotive Industry
Honeycomb Structures: Core of Innovation
Application and Impact
Overcoming the limitations of traditional materials in automotive applications is a key driver for the adoption of advanced composites like honeycomb structures. Here are the major limitations of traditional materials and how advanced composites address these challenges:
Fabrication Technique
Advantages
Applications
Resin Transfer Molding (RTM)
High fiber volume fractions, consistent quality, complex shapes
Structural components, body panels
Compression Molding
Near-net-shape components, high production volumes
Sheet Molding Compounds (SMCs), Bulk Molding Compounds (BMCs)
Automated Fiber Placement (AFP) and Automated Tape Laying (ATL)
Precise fiber placement, highly optimized structures
Large and complex structures
Filament Winding
High strength-to-weight ratio, suitable for cylindrical parts
Pressure vessels, drive shafts
Vacuum Infusion
Large components, low-volume production
Body panels, structural parts
The automotive industry is witnessing a paradigm shift towards lightweight, high-performance components, and composite materials are at the forefront of this revolution. By leveraging the unique properties and advanced fabrication techniques of composites, manufacturers are unlocking new possibilities in vehicle design and performance.
Composite materials offer a wide range of applications in the automotive sector. One prominent example is their use in structural components such as chassis, body panels, and suspension systems. By replacing traditional metal parts with composite alternatives, significant weight reductions can be achieved without compromising strength or stiffness. This translates to improved fuel efficiency, reduced emissions, and enhanced vehicle dynamics.
Another key application of composites is in the development of lightweight and high-performance brake systems. Composite brake pads and rotors offer superior wear resistance, thermal stability, and noise reduction compared to conventional materials. This not only enhances the braking performance but also extends the service life of the components.
Composites are also revolutionizing the design of automotive interiors. Lightweight composite seat structures, door panels, and dashboard components contribute to overall vehicle weight reduction while offering improved aesthetics and functionality. The ability to mold composites into complex shapes allows for the integration of features such as built-in sensors, heating elements, and acoustic insulation.
In the realm of powertrain components, composites are finding applications in engine parts, transmission systems, and exhaust components. The high thermal and chemical resistance of ceramic matrix composites (CMCs) makes them suitable for high-temperature applications, such as turbocharger housings and exhaust manifolds. The use of composites in these areas helps to reduce weight, improve heat management, and enhance the overall efficiency of the powertrain.
The automotive industry is also exploring the potential of natural fiber composites as a sustainable and eco-friendly alternative to traditional materials. Natural fibers such as flax, hemp, and jute, when combined with biodegradable polymer matrices, offer a reduced environmental impact while maintaining comparable mechanical properties. These bio-composites are finding applications in non-structural components such as interior trim, door panels, and trunk liners.
To fully realize the potential of composite materials, close collaboration between material scientists, engineers, and designers is essential. The development of advanced simulation tools and testing methods is crucial for predicting the behavior of composite components under various loading conditions. Additionally, establishing robust supply chains and investing in specialized manufacturing facilities are key to scaling up the production of composite parts.
let's thank the authors Fardin Khan, Nayem Hossain, Juhi Jannat Mim, SM Maksudur Rahman, Md. Jayed Iqbal, Mostakim Billah, and Mohammad Asaduzzaman Chowdhury for their valuable contribution in writing the research paper titled "Advances of composite materials in automobile applications – A review" which was published in the Journal of Engineering Research. Their extensive research and insights have provided the foundation for this informative blog post, shedding light on the revolutionary role of composite materials in the automotive industry. We greatly appreciate their dedication and expertise in this field, as their work has significantly contributed to the advancements discussed throughout this blog.
Discover the future of composite manufacturing with Addcomposites! Here's how you can get involved:
At Addcomposites, we are dedicated to revolutionizing composite manufacturing. Our AFP systems and comprehensive support services are waiting for you to harness. So, don't wait – get started on your journey to the future of manufacturing today!