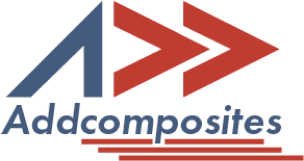
Welcome to this month's edition of Composites Monthly, where we bring you the latest research and developments in the field of composites manufacturing. In this issue, we're focusing on the exciting advancements in laser-assisted automated fiber placement, a cutting-edge technology that's revolutionizing the way composites are made. From in situ consolidation of carbon fiber PAEK to the effects of defects in automated fiber placement laminates, we've got all the latest findings covered. Join us as we delve into these studies and discover the ways they're shaping the future of composites manufacturing. Let's get started!
Research on Laser-Assisted Automated Fiber Placement
Review Articles and Modeling Methodologies
Research on Shape and Topology Optimization
Research on Manufacturing-Induced Imperfections and Defects
In situ consolidation of carbon fiber PAEK via laser-assisted automated fiber placement
This study demonstrates successful in-situ consolidation AFP of TPC tapes (ICAT) of carbon fiber LM-PAEK™ at up to 0.15 m/s. Increasing this speed by three times will likely result in the widespread adoption of TPCs for large-scale aerospace structures. However, even at lower placement rates, it may be economical to use ICAT for the manufacturing of small to medium-sized parts and structures.
This work demonstrates that crystallinity has a significant impact on the NIR optical properties of the PEEK film and its prepreg tape and temperature distribution during the L-AFP process. For thick PEEK films (≧50 μm), an increase in crystallinity leads to multilayer reflections of the transmitted laser from the crystalline structure, thereby making the reflectance increase by up to 17.2% and the transmittance decrease by up to 17.6% in the wavelength of 1080 nm.
This study investigated the crystallization mechanism of carbon fiber/polyphenylene sulfide composites during the automated fiber placement process and its effect on mechanical properties. The results showed that the tool temperature was the main factor influencing the crystallinity of the composites, and that increasing the tool temperature was an effective method to improve crystallinity. The study also found that with the increase of tool temperature, the flexural strength and interlaminar shear strength improved, but the Mode I fracture toughness decreased. The combination of the kinetic method and experiments was helpful in understanding the crystallization mechanism and optimizing processing conditions.
This paper conducts a comprehensive analysis of the robot joint error, so as to improve the accuracy of the robot. A torsional and capsize deformation model for joints is established. In addition, the capsize torque and capsize axis of joint deformation are derived to determine the transformation relationship between joint frames. Chebyshev polynomials are used to describe joint-dependent errors. The Levenberg-Marquarelt (L-M) algorithm was used to identify the error model parameters. The effects of different error factors on the localization accuracy were compared and analyzed. The validation result shows that the proposed model describes 88.08% of the positioning error, and the average residual error of the calibration can reach 0.131 mm. The identified joint-dependent error and the compliance error are 0.254 mm and 0.202 mm, accounting for 24.8% and 19.73% of the positioning error, respectively.
This critical review has summarised the current progress in Type IV and Type V composite pressure vessels and discussed key challenges associated with the progression of their development. Additionally, the use of AFP as a manufacturing process to replace traditional filament winding has been discussed. Filament winding suffers from several limitations that reduce its flexibility, including the need for the fiber to be continuous, the inability to wind around concave surfaces without fiber bridging
The study focuses on the use of modeling techniques in the Automated Fiber Placement (AFP) process to better understand and predict the quality of the final product. The paper highlights the importance of physics-based models (PBMs) and data-driven models (DDMs) in the understanding of the AFP process, but also highlights the limitations of PBMs when dealing with complex or random anomalies. The paper provides a systematic review of the use of PBMs and DDMs in the AFP process and explores the potential of combining them into hybrid models. The review concludes by identifying gaps in current modeling techniques and the efforts being made to advance modeling efforts for AFP manufacturing.
In this paper, a Lagrangian simultaneous shape and topology optimization method is proposed to control the static displacement at arbitrary points of the structure for the purpose of designing fiber bundles of CFRP plate/shell structures. The simultaneous shape and topology optimization problem is formulated as a distributed-parameter optimization problem, and the gradient function for changes in shape and density are theoretically derived.
The study aimed to reduce fiber waviness, a key defect generated during the fiber steering process that affects product quality, especially for parts with large curvature. The study found that fiber waviness was caused by uneven internal and external stress and uneven internal and external laying speeds. The study used an optimized multi-piece compaction roller, which was able to supply different laying speeds for different tows, to decrease this defect. The study also found that uneven interlaminar bonding strength was caused by different laying speeds of the inner and outer tows during the fiber steering process. The interlaminar bonding uniformity was improved by optimizing the compaction force for each tow. The study suggested that improvements will be more significant using the optimized method for fiber steering processes with more tows. Future research will focus on designing, fabricating, and testing a structure of an optimized multi-piece compaction roller that could individually supply different compaction forces for each tow.
In this study, the compressive strength of specimens cut from the laminates with two embedded gaps is tested to investigate the interactive effects of the gaps on the compressive strength. Compressive strengths of quasi-isotropic laminates with embedded gaps were obtained experimentally and the mechanical effects of the gaps were discussed by using fundamental 3D finite element analysis and the present 2D analysis. When the gap ends were set in the gage section of the specimens, the decrease in compressive strengths (16.6 % for Case C) was comparable to the tensile strength reduction obtained for the AFP-manufactured laminates.
The study investigated the effect of different defect configurations on mechanical performance, including tensile strength, flexural strength, and shear strength, and aimed to link the mechanical knockdown caused by defects to the manufacturing data generated by a process monitoring system. The results showed a reduction of up to 20% in ultimate tensile strength, depending on the defect configuration, with a knockdown observed only when defects reached a thickness of 4 plies. A higher reduction of tensile strength was found for gaps compared to overlaps of the same size. Bending and in-plane shear tests both showed an increase in performance for samples with overlaps and a decrease for samples with gaps. The study established a correlation between defect volume and tensile strength, with tensile strength decreasing as defect volume increased. The detection of defects must be performed "inline" for reliable quantification of laminate quality.
The study aimed to reduce fiber waviness, a key defect generated during the fiber steering process that affects product quality, especially for parts with large curvature. The study found that fiber waviness was caused by uneven internal and external stress and uneven internal and external laying speeds. The study used an optimized multi-piece compaction roller, which was able to supply different laying speeds for different tows, to decrease this defect. The study also found that uneven interlaminar bonding strength was caused by different laying speeds of the inner and outer tows during the fiber steering process. The interlaminar bonding uniformity was improved by optimizing the compaction force for each tow. The study suggested that improvements will be more significant using the optimized method for fiber steering processes with more tows. Future research will focus on designing, fabricating, and testing a structure of an optimized multi-piece compaction roller that could individually supply different compaction forces for each tow.
Welcome to this month's edition of Composites Monthly, where we bring you the latest research and developments in the field of composites manufacturing. In this issue, we're focusing on the exciting advancements in laser-assisted automated fiber placement, a cutting-edge technology that's revolutionizing the way composites are made. From in situ consolidation of carbon fiber PAEK to the effects of defects in automated fiber placement laminates, we've got all the latest findings covered. Join us as we delve into these studies and discover the ways they're shaping the future of composites manufacturing. Let's get started!
Research on Laser-Assisted Automated Fiber Placement
Review Articles and Modeling Methodologies
Research on Shape and Topology Optimization
Research on Manufacturing-Induced Imperfections and Defects
In situ consolidation of carbon fiber PAEK via laser-assisted automated fiber placement
This study demonstrates successful in-situ consolidation AFP of TPC tapes (ICAT) of carbon fiber LM-PAEK™ at up to 0.15 m/s. Increasing this speed by three times will likely result in the widespread adoption of TPCs for large-scale aerospace structures. However, even at lower placement rates, it may be economical to use ICAT for the manufacturing of small to medium-sized parts and structures.
This work demonstrates that crystallinity has a significant impact on the NIR optical properties of the PEEK film and its prepreg tape and temperature distribution during the L-AFP process. For thick PEEK films (≧50 μm), an increase in crystallinity leads to multilayer reflections of the transmitted laser from the crystalline structure, thereby making the reflectance increase by up to 17.2% and the transmittance decrease by up to 17.6% in the wavelength of 1080 nm.
This study investigated the crystallization mechanism of carbon fiber/polyphenylene sulfide composites during the automated fiber placement process and its effect on mechanical properties. The results showed that the tool temperature was the main factor influencing the crystallinity of the composites, and that increasing the tool temperature was an effective method to improve crystallinity. The study also found that with the increase of tool temperature, the flexural strength and interlaminar shear strength improved, but the Mode I fracture toughness decreased. The combination of the kinetic method and experiments was helpful in understanding the crystallization mechanism and optimizing processing conditions.
This paper conducts a comprehensive analysis of the robot joint error, so as to improve the accuracy of the robot. A torsional and capsize deformation model for joints is established. In addition, the capsize torque and capsize axis of joint deformation are derived to determine the transformation relationship between joint frames. Chebyshev polynomials are used to describe joint-dependent errors. The Levenberg-Marquarelt (L-M) algorithm was used to identify the error model parameters. The effects of different error factors on the localization accuracy were compared and analyzed. The validation result shows that the proposed model describes 88.08% of the positioning error, and the average residual error of the calibration can reach 0.131 mm. The identified joint-dependent error and the compliance error are 0.254 mm and 0.202 mm, accounting for 24.8% and 19.73% of the positioning error, respectively.
This critical review has summarised the current progress in Type IV and Type V composite pressure vessels and discussed key challenges associated with the progression of their development. Additionally, the use of AFP as a manufacturing process to replace traditional filament winding has been discussed. Filament winding suffers from several limitations that reduce its flexibility, including the need for the fiber to be continuous, the inability to wind around concave surfaces without fiber bridging
The study focuses on the use of modeling techniques in the Automated Fiber Placement (AFP) process to better understand and predict the quality of the final product. The paper highlights the importance of physics-based models (PBMs) and data-driven models (DDMs) in the understanding of the AFP process, but also highlights the limitations of PBMs when dealing with complex or random anomalies. The paper provides a systematic review of the use of PBMs and DDMs in the AFP process and explores the potential of combining them into hybrid models. The review concludes by identifying gaps in current modeling techniques and the efforts being made to advance modeling efforts for AFP manufacturing.
In this paper, a Lagrangian simultaneous shape and topology optimization method is proposed to control the static displacement at arbitrary points of the structure for the purpose of designing fiber bundles of CFRP plate/shell structures. The simultaneous shape and topology optimization problem is formulated as a distributed-parameter optimization problem, and the gradient function for changes in shape and density are theoretically derived.
The study aimed to reduce fiber waviness, a key defect generated during the fiber steering process that affects product quality, especially for parts with large curvature. The study found that fiber waviness was caused by uneven internal and external stress and uneven internal and external laying speeds. The study used an optimized multi-piece compaction roller, which was able to supply different laying speeds for different tows, to decrease this defect. The study also found that uneven interlaminar bonding strength was caused by different laying speeds of the inner and outer tows during the fiber steering process. The interlaminar bonding uniformity was improved by optimizing the compaction force for each tow. The study suggested that improvements will be more significant using the optimized method for fiber steering processes with more tows. Future research will focus on designing, fabricating, and testing a structure of an optimized multi-piece compaction roller that could individually supply different compaction forces for each tow.
In this study, the compressive strength of specimens cut from the laminates with two embedded gaps is tested to investigate the interactive effects of the gaps on the compressive strength. Compressive strengths of quasi-isotropic laminates with embedded gaps were obtained experimentally and the mechanical effects of the gaps were discussed by using fundamental 3D finite element analysis and the present 2D analysis. When the gap ends were set in the gage section of the specimens, the decrease in compressive strengths (16.6 % for Case C) was comparable to the tensile strength reduction obtained for the AFP-manufactured laminates.
The study investigated the effect of different defect configurations on mechanical performance, including tensile strength, flexural strength, and shear strength, and aimed to link the mechanical knockdown caused by defects to the manufacturing data generated by a process monitoring system. The results showed a reduction of up to 20% in ultimate tensile strength, depending on the defect configuration, with a knockdown observed only when defects reached a thickness of 4 plies. A higher reduction of tensile strength was found for gaps compared to overlaps of the same size. Bending and in-plane shear tests both showed an increase in performance for samples with overlaps and a decrease for samples with gaps. The study established a correlation between defect volume and tensile strength, with tensile strength decreasing as defect volume increased. The detection of defects must be performed "inline" for reliable quantification of laminate quality.
The study aimed to reduce fiber waviness, a key defect generated during the fiber steering process that affects product quality, especially for parts with large curvature. The study found that fiber waviness was caused by uneven internal and external stress and uneven internal and external laying speeds. The study used an optimized multi-piece compaction roller, which was able to supply different laying speeds for different tows, to decrease this defect. The study also found that uneven interlaminar bonding strength was caused by different laying speeds of the inner and outer tows during the fiber steering process. The interlaminar bonding uniformity was improved by optimizing the compaction force for each tow. The study suggested that improvements will be more significant using the optimized method for fiber steering processes with more tows. Future research will focus on designing, fabricating, and testing a structure of an optimized multi-piece compaction roller that could individually supply different compaction forces for each tow.