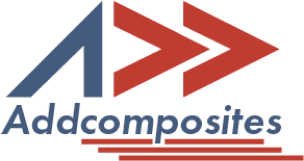
Wind turbine technology is at the forefront of renewable energy solutions, aiming to harness the power of the wind efficiently and sustainably. A critical component of wind turbine performance lies in the materials used for the blades. Traditional materials for wind turbine blades have been predominantly synthetic composites, favored for their strength-to-weight ratio and durability. However, these materials come with a set of challenges that limit their performance and sustainability.
The quest for improved wind turbine blade materials has led to the exploration of hybrid composites, which combine synthetic fibers with natural fibers. This innovative approach aims to address the shortcomings of traditional materials by reducing costs, enhancing performance, and improving environmental sustainability. Natural fibers such as bamboo, aloe vera, banana, sisal, and bagasse offer unique properties that can complement synthetic fibers, leading to the development of blades that are not only more efficient and durable but also environmentally friendly.
The exploration of composite materials for wind turbine blades has revealed several limitations inherent in conventional composite materials. These limitations are primarily centered around efficiency, cost, environmental sustainability, and the physical properties of the materials used.
Conventional composites, typically made from synthetic fibers like glass or carbon embedded in a polymer matrix, face significant challenges:
These limitations highlight the need for alternative materials that can address the challenges posed by conventional composites. Hybrid composites, which combine natural fibers with synthetic ones, emerge as a promising solution. They aim to leverage the unique properties of natural fibers, such as lower cost, reduced environmental impact, and improved mechanical properties, to overcome the limitations of traditional materials. By exploring the potential of hybrid composites, the wind energy sector can move towards more sustainable, efficient, and cost-effective solutions for turbine blade manufacturing.
The transition from conventional to hybrid composites in wind turbine blade manufacturing marks a significant leap towards addressing the limitations of traditional materials. This innovative approach combines the strengths of both synthetic and natural fibers to create materials that are not only more efficient but also environmentally friendly and cost-effective.
Hybrid composites, consisting of natural fibers like bamboo, aloe vera, banana, sisal, and bagasse, integrated with synthetic fibers, offer a unique set of advantages:
The innovative use of hybrid composites in wind turbine blades represents a paradigm shift in renewable energy technology. By leveraging the unique properties of natural and synthetic fibers, this approach addresses the critical challenges of cost, environmental impact, and material performance. As the industry continues to evolve, hybrid composites stand at the forefront, promising a more sustainable, efficient, and cost-effective future for wind energy.
The culmination of this study in hybrid composite manufacturing and testing for wind turbine blades showcases a significant stride toward enhancing the efficiency and sustainability of wind turbines. This research integrates new and current technologies like Computer-Aided Design (CAD), Rapid Prototyping (3D Printing), Advanced Manufacturing techniques such as Vacuum Assisted Resin Transfer Molding (VARTM), and Finite Element Analysis (FEA) to optimize wind turbine blade design and performance.
The study underscores the importance of understanding the environmental impact on composite life and strength, particularly when incorporating natural fibers into the manufacturing process. Natural fibers introduce a sustainable and environmentally friendly component to composite materials, reducing the carbon footprint of wind turbines while maintaining, if not improving, the material strength and durability necessary for efficient energy capture and long-term operation.
Different types of hybrid composites, including natural and glass fiber-reinforced polymeric composites, were prepared and rigorously tested. Their mechanical strength, thermal capabilities, environmental stability, and failure morphologies were assessed through various experimental methods.
The experimentally predicted mechanical strength values were then compared with the finite element analysis results, offering insights into the material behaviors under different conditions and loads. This approach not only addresses the limitations of conventional composite materials but also paves the way for the development of more efficient, cost-effective, and environmentally sustainable wind turbine blades. The integration of advanced manufacturing techniques and the exploration of hybrid composites signify a promising future for wind energy technology, where the emphasis is on maximizing efficiency and minimizing environmental impact.
By leveraging the unique properties of hybrid composites, this research contributes to the broader goal of economic and industrial development through sustainable energy solutions. It highlights the potential of hybrid composites in revolutionizing wind turbine blade manufacturing, aiming for a balance between performance, cost, and environmental sustainability.
We'd like to extend our heartfelt gratitude to Dr. Sujesh G, Abhijith D, Giri, Arathi Menon, Nanditha K P, and Vinayak S Menon for their invaluable contributions to the research detailed in this blog. Their expertise and dedication have significantly advanced our understanding of hybrid composite materials for wind turbine blades, marking a pivotal step towards more sustainable and efficient renewable energy solutions. Their work exemplifies the collaborative spirit and innovative approach that drive progress in the field of renewable energy engineering.
Discover the future of composite manufacturing with Addcomposites! Here's how you can get involved:
At Addcomposites, we are dedicated to revolutionizing composite manufacturing. Our AFP systems and comprehensive support services are waiting for you to harness. So, don't wait – get started on your journey to the future of manufacturing today!
Wind turbine technology is at the forefront of renewable energy solutions, aiming to harness the power of the wind efficiently and sustainably. A critical component of wind turbine performance lies in the materials used for the blades. Traditional materials for wind turbine blades have been predominantly synthetic composites, favored for their strength-to-weight ratio and durability. However, these materials come with a set of challenges that limit their performance and sustainability.
The quest for improved wind turbine blade materials has led to the exploration of hybrid composites, which combine synthetic fibers with natural fibers. This innovative approach aims to address the shortcomings of traditional materials by reducing costs, enhancing performance, and improving environmental sustainability. Natural fibers such as bamboo, aloe vera, banana, sisal, and bagasse offer unique properties that can complement synthetic fibers, leading to the development of blades that are not only more efficient and durable but also environmentally friendly.
The exploration of composite materials for wind turbine blades has revealed several limitations inherent in conventional composite materials. These limitations are primarily centered around efficiency, cost, environmental sustainability, and the physical properties of the materials used.
Conventional composites, typically made from synthetic fibers like glass or carbon embedded in a polymer matrix, face significant challenges:
These limitations highlight the need for alternative materials that can address the challenges posed by conventional composites. Hybrid composites, which combine natural fibers with synthetic ones, emerge as a promising solution. They aim to leverage the unique properties of natural fibers, such as lower cost, reduced environmental impact, and improved mechanical properties, to overcome the limitations of traditional materials. By exploring the potential of hybrid composites, the wind energy sector can move towards more sustainable, efficient, and cost-effective solutions for turbine blade manufacturing.
The transition from conventional to hybrid composites in wind turbine blade manufacturing marks a significant leap towards addressing the limitations of traditional materials. This innovative approach combines the strengths of both synthetic and natural fibers to create materials that are not only more efficient but also environmentally friendly and cost-effective.
Hybrid composites, consisting of natural fibers like bamboo, aloe vera, banana, sisal, and bagasse, integrated with synthetic fibers, offer a unique set of advantages:
The innovative use of hybrid composites in wind turbine blades represents a paradigm shift in renewable energy technology. By leveraging the unique properties of natural and synthetic fibers, this approach addresses the critical challenges of cost, environmental impact, and material performance. As the industry continues to evolve, hybrid composites stand at the forefront, promising a more sustainable, efficient, and cost-effective future for wind energy.
The culmination of this study in hybrid composite manufacturing and testing for wind turbine blades showcases a significant stride toward enhancing the efficiency and sustainability of wind turbines. This research integrates new and current technologies like Computer-Aided Design (CAD), Rapid Prototyping (3D Printing), Advanced Manufacturing techniques such as Vacuum Assisted Resin Transfer Molding (VARTM), and Finite Element Analysis (FEA) to optimize wind turbine blade design and performance.
The study underscores the importance of understanding the environmental impact on composite life and strength, particularly when incorporating natural fibers into the manufacturing process. Natural fibers introduce a sustainable and environmentally friendly component to composite materials, reducing the carbon footprint of wind turbines while maintaining, if not improving, the material strength and durability necessary for efficient energy capture and long-term operation.
Different types of hybrid composites, including natural and glass fiber-reinforced polymeric composites, were prepared and rigorously tested. Their mechanical strength, thermal capabilities, environmental stability, and failure morphologies were assessed through various experimental methods.
The experimentally predicted mechanical strength values were then compared with the finite element analysis results, offering insights into the material behaviors under different conditions and loads. This approach not only addresses the limitations of conventional composite materials but also paves the way for the development of more efficient, cost-effective, and environmentally sustainable wind turbine blades. The integration of advanced manufacturing techniques and the exploration of hybrid composites signify a promising future for wind energy technology, where the emphasis is on maximizing efficiency and minimizing environmental impact.
By leveraging the unique properties of hybrid composites, this research contributes to the broader goal of economic and industrial development through sustainable energy solutions. It highlights the potential of hybrid composites in revolutionizing wind turbine blade manufacturing, aiming for a balance between performance, cost, and environmental sustainability.
We'd like to extend our heartfelt gratitude to Dr. Sujesh G, Abhijith D, Giri, Arathi Menon, Nanditha K P, and Vinayak S Menon for their invaluable contributions to the research detailed in this blog. Their expertise and dedication have significantly advanced our understanding of hybrid composite materials for wind turbine blades, marking a pivotal step towards more sustainable and efficient renewable energy solutions. Their work exemplifies the collaborative spirit and innovative approach that drive progress in the field of renewable energy engineering.
Discover the future of composite manufacturing with Addcomposites! Here's how you can get involved:
At Addcomposites, we are dedicated to revolutionizing composite manufacturing. Our AFP systems and comprehensive support services are waiting for you to harness. So, don't wait – get started on your journey to the future of manufacturing today!