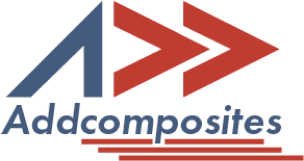
Welcome to the fascinating world of Continuous Fiber Composites (CFCs), where innovation meets performance, and the possibilities are boundless. In this comprehensive guide, we will embark on a journey to explore the intricacies of CFCs, unraveling their unique properties, manufacturing techniques, and wide array of applications. Whether you are a seasoned engineer, a student of materials science, or simply someone with a curiosity for advanced materials, this blog is tailored for you.
Continuous fiber composites are advanced materials that combine high-strength fibers with a supportive polymer matrix. The fibers, often made from carbon or glass, run the entire length of the material, providing exceptional tensile strength and rigidity. The polymer matrix, typically a resin, surrounds and bonds with the fibers, protecting them and distributing stress evenly throughout the material. This synergistic combination results in a material that exhibits superior mechanical properties compared to traditional materials.
To fully appreciate the capabilities of continuous fiber composites, it's essential to understand the roles of their two main constituents:
The fibers are the backbone of continuous fiber composites, providing high tensile strength and stiffness. They resist stretching and bending, enabling the material to withstand substantial loads without deforming. The choice of fiber type (e.g., carbon, glass, aramid) and their alignment within the matrix can be tailored to achieve specific performance characteristics.
The polymer matrix plays a crucial role in protecting the fibers and maintaining the integrity of the composite. It absorbs impacts, distributes stress, and prevents the fibers from buckling or fracturing. The matrix also contributes to the material's durability, protecting it from environmental factors such as moisture and UV radiation.
One of the remarkable aspects of continuous fiber composites is their versatility. By adjusting the type, orientation, and arrangement of fibers, as well as the properties of the polymer matrix, manufacturers can tailor the material's properties to suit specific applications. This customization enables the creation of composites that are optimized for strength, flexibility, lightweight, or a combination of these and other properties.
In this section, we've unveiled the basics of continuous fiber composites, shedding light on their constituents and the roles they play. These materials stand out for their ability to be customized, providing solutions across a wide range of industries and applications. As we move forward, we will delve deeper into the unique properties of continuous fiber composites and how they translate into real-world performance advantages.
Continuous Fiber Composites (CFCs) stand out in the materials world due to their unique combination of strength, stiffness, and durability, all while maintaining a lightweight profile. In this section, we will delve into the specific properties that make CFCs a preferred choice in various industries.
CFCs are renowned for their exceptional strength without the added weight. This high strength-to-weight ratio is a critical factor in applications such as aerospace and automotive, where reducing weight is essential for performance and efficiency. The continuous fibers provide the necessary tensile strength and stiffness, while the polymer matrix ensures that the material remains lightweight.
The continuous fibers in CFCs distribute applied loads effectively along their length, maintaining structural integrity and preventing stress concentration. This results in increased strength and stiffness compared to short fibers or particle-filled composites. Additionally, the fiber alignment can be strategically adjusted to maximize reinforcement in the required direction, leading to higher strength and stiffness in targeted areas.
CFCs exhibit excellent resistance to fatigue, corrosion, and environmental degradation. The polymer matrix protects the fibers, enhancing the material's durability and resulting in longer service life and reduced maintenance needs. This resistance to wear and tear is a significant advantage, especially in industries where materials are subjected to harsh conditions.
The matrix material in CFCs helps balance the composite's coefficient of thermal expansion, ensuring dimensional stability and minimizing potential failure due to temperature changes. This property is crucial in applications where materials are exposed to varying temperatures, ensuring consistent performance and longevity.
The stiffness of CFCs can be tailored to meet specific design requirements by adjusting the fiber orientation, volume, and type. This customization allows for materials that can be both incredibly stiff and flexible as needed, providing versatility in application and design.
Continuous Fiber Composites offer a unique set of properties that set them apart from traditional materials. Their high strength-to-weight ratio, enhanced load distribution, durability, and tailored stiffness make them a versatile and reliable choice in various industries. As we continue to explore CFCs, we will delve into the fabrication techniques and their impact on these remarkable materials.
The fabrication of Continuous Fiber Composites (CFCs) is a crucial process that significantly influences their final properties, including strength, stiffness, and durability. Various techniques are employed to create these advanced materials, each with unique advantages and effects on the composite's performance. In this section, we will explore some of the common fabrication methods used for CFCs.
In the prepreg layup method, fibers are pre-impregnated with resin and laid up in specific orientations, followed by curing under heat and pressure. This technique results in an excellent fiber-to-resin ratio, producing parts with high strength and stiffness. It is particularly beneficial for creating components with complex geometries and tailored mechanical properties.
Filament winding involves winding fibers onto a rotating mandrel, impregnating them with resin, and then curing the composite. This method is well-suited for cylindrical or spherical components and offers good fiber alignment, translating to improved strength in the winding direction.
Pultrusion is a continuous process where fibers are pulled through a resin bath and then through a heated die, curing the resin. This method produces parts with consistent cross-sectional profiles and high fiber volume fractions, resulting in high strength and stiffness along the length of the part.
In RTM, fibers are placed in a mold, and resin is injected under pressure. This technique can produce complex geometries and offers good control over the fiber-to-resin ratio, allowing for the tailoring of mechanical properties.
Continuous fibers can be incorporated into 3D printed parts using specialized printers that combine fibers with thermoplastic resins. This innovative technique enables the creation of complex geometries and the customization of fiber orientations, providing optimized mechanical properties for specific applications.
AFP utilizes a robotic system to precisely lay down continuous fiber tapes onto a mold or tooling surface. This method enables accurate control of fiber orientation and placement, resulting in highly tailored mechanical properties and complex geometries. It also reduces material waste and improves production efficiency.
The chosen fabrication technique directly impacts the properties of CFCs, influencing factors such as fiber alignment, fiber-to-resin ratio, and curing conditions. By understanding and selecting the appropriate fabrication method, manufacturers can optimize the performance of CFC components, ensuring they meet the specific requirements of their applications.
Continuous Fiber Composites (CFCs) have found their place in a myriad of industries, thanks to their exceptional properties and performance. In this section, we will explore some of the typical applications of CFCs and the advantages they bring to these fields.
In the aerospace industry, CFCs are a material of choice for various aircraft components including wings, fuselage, and interior structures. The high strength-to-weight ratio, stiffness, and corrosion resistance of CFCs contribute to lighter and more fuel-efficient aircraft designs, without compromising safety and performance. The ability to tailor the stiffness and strength of CFCs according to specific load requirements makes them ideal for aerospace applications.
The automotive sector leverages CFCs for manufacturing vehicle components such as body panels, chassis, and suspension systems. The use of CFCs results in a significant reduction in weight, leading to improved fuel efficiency and performance. Additionally, the durability and resistance to wear and tear of CFCs contribute to the longevity and reliability of automotive parts.
Wind turbine blades manufactured from CFCs exhibit increased stiffness and fatigue resistance, which are crucial for larger, more efficient designs. The material's ability to withstand demanding environmental conditions ensures the longevity and performance of wind turbines, contributing to the sustainability of renewable energy sources.
CFCs are extensively used in sports equipment like bicycles, golf clubs, tennis racquets, and more. The lightweight, high-strength, and tailored stiffness properties of CFCs enhance performance and durability, providing athletes with reliable and efficient equipment.
In the field of infrastructure, CFCs find applications in bridge decks, reinforcing bars, and other structural elements. Their corrosion resistance, reduced weight, and ease of installation lead to lower maintenance costs and extended service life, making CFCs a cost-effective solution for infrastructure projects.
The marine industry benefits from the use of CFCs in ship hulls, masts, and propellers. The materials provide improved strength, reduced weight, and better resistance to the harsh marine environment, contributing to the efficiency and longevity of marine vessels.
The versatility and superior properties of Continuous Fiber Composites make them a preferred choice in various industries, offering unparalleled advantages in terms of strength, weight, durability, and performance. As we continue to innovate and explore new applications, the potential of CFCs in revolutionizing industries is boundless.
The field of Continuous Fiber Composites (CFCs) is rapidly evolving, with numerous advancements and innovations enhancing their capabilities and expanding their applications. In this section, we will explore some of the current developments that are shaping the future of CFCs.
Innovations in manufacturing techniques are playing a pivotal role in optimizing the properties of CFCs. Automated Fiber Placement (AFP) is a notable example, where a robotic system precisely lays down continuous fiber tapes onto a mold or tooling surface. This technique ensures accurate control of fiber orientation and placement, resulting in highly tailored mechanical properties and complex geometries. Additionally, it reduces material waste and improves production efficiency.
The integration of 3D printing technology, such as Continuous Fiber 3D Printing (CF3D), is revolutionizing the production of CFCs. This technology enables the direct manufacturing of complex geometries with tailored fiber reinforcement, paving the way for lightweight, high-performance components across various industries.
The development of hybrid composites, which combine continuous fibers with other materials like nanoparticles or metallic foams, results in enhanced properties such as improved thermal or electrical conductivity, impact resistance, and vibration damping. Additionally, multifunctional composites integrate additional functionalities like sensing capabilities or self-healing properties, leading to the creation of smart structures capable of monitoring their own health and responding to damage.
In response to growing environmental concerns, there is a significant push towards developing bio-based and recyclable matrix materials for CFCs. These sustainable alternatives aim to address issues related to end-of-life disposal and contribute to the overall sustainability of composite materials.
Advanced modeling techniques and simulation tools are being employed to better understand and predict the behavior of CFCs under various conditions. This leads to more efficient designs, improved performance, and the ability to tailor composites to specific applications.
These advancements and innovations are not only enhancing the properties and capabilities of Continuous Fiber Composites but also opening up new avenues for their application. As we continue to push the boundaries of what is possible with these materials, the future holds exciting prospects for industries ranging from aerospace and automotive to renewable energy and beyond.
Discover the future of composite manufacturing with Addcomposites! Here's how you can get involved:
At Addcomposites, we are dedicated to revolutionizing composite manufacturing. Our AFP systems and comprehensive support services are waiting for you to harness. So, don't wait – get started on your journey to the future of manufacturing today!
Welcome to the fascinating world of Continuous Fiber Composites (CFCs), where innovation meets performance, and the possibilities are boundless. In this comprehensive guide, we will embark on a journey to explore the intricacies of CFCs, unraveling their unique properties, manufacturing techniques, and wide array of applications. Whether you are a seasoned engineer, a student of materials science, or simply someone with a curiosity for advanced materials, this blog is tailored for you.
Continuous fiber composites are advanced materials that combine high-strength fibers with a supportive polymer matrix. The fibers, often made from carbon or glass, run the entire length of the material, providing exceptional tensile strength and rigidity. The polymer matrix, typically a resin, surrounds and bonds with the fibers, protecting them and distributing stress evenly throughout the material. This synergistic combination results in a material that exhibits superior mechanical properties compared to traditional materials.
To fully appreciate the capabilities of continuous fiber composites, it's essential to understand the roles of their two main constituents:
The fibers are the backbone of continuous fiber composites, providing high tensile strength and stiffness. They resist stretching and bending, enabling the material to withstand substantial loads without deforming. The choice of fiber type (e.g., carbon, glass, aramid) and their alignment within the matrix can be tailored to achieve specific performance characteristics.
The polymer matrix plays a crucial role in protecting the fibers and maintaining the integrity of the composite. It absorbs impacts, distributes stress, and prevents the fibers from buckling or fracturing. The matrix also contributes to the material's durability, protecting it from environmental factors such as moisture and UV radiation.
One of the remarkable aspects of continuous fiber composites is their versatility. By adjusting the type, orientation, and arrangement of fibers, as well as the properties of the polymer matrix, manufacturers can tailor the material's properties to suit specific applications. This customization enables the creation of composites that are optimized for strength, flexibility, lightweight, or a combination of these and other properties.
In this section, we've unveiled the basics of continuous fiber composites, shedding light on their constituents and the roles they play. These materials stand out for their ability to be customized, providing solutions across a wide range of industries and applications. As we move forward, we will delve deeper into the unique properties of continuous fiber composites and how they translate into real-world performance advantages.
Continuous Fiber Composites (CFCs) stand out in the materials world due to their unique combination of strength, stiffness, and durability, all while maintaining a lightweight profile. In this section, we will delve into the specific properties that make CFCs a preferred choice in various industries.
CFCs are renowned for their exceptional strength without the added weight. This high strength-to-weight ratio is a critical factor in applications such as aerospace and automotive, where reducing weight is essential for performance and efficiency. The continuous fibers provide the necessary tensile strength and stiffness, while the polymer matrix ensures that the material remains lightweight.
The continuous fibers in CFCs distribute applied loads effectively along their length, maintaining structural integrity and preventing stress concentration. This results in increased strength and stiffness compared to short fibers or particle-filled composites. Additionally, the fiber alignment can be strategically adjusted to maximize reinforcement in the required direction, leading to higher strength and stiffness in targeted areas.
CFCs exhibit excellent resistance to fatigue, corrosion, and environmental degradation. The polymer matrix protects the fibers, enhancing the material's durability and resulting in longer service life and reduced maintenance needs. This resistance to wear and tear is a significant advantage, especially in industries where materials are subjected to harsh conditions.
The matrix material in CFCs helps balance the composite's coefficient of thermal expansion, ensuring dimensional stability and minimizing potential failure due to temperature changes. This property is crucial in applications where materials are exposed to varying temperatures, ensuring consistent performance and longevity.
The stiffness of CFCs can be tailored to meet specific design requirements by adjusting the fiber orientation, volume, and type. This customization allows for materials that can be both incredibly stiff and flexible as needed, providing versatility in application and design.
Continuous Fiber Composites offer a unique set of properties that set them apart from traditional materials. Their high strength-to-weight ratio, enhanced load distribution, durability, and tailored stiffness make them a versatile and reliable choice in various industries. As we continue to explore CFCs, we will delve into the fabrication techniques and their impact on these remarkable materials.
The fabrication of Continuous Fiber Composites (CFCs) is a crucial process that significantly influences their final properties, including strength, stiffness, and durability. Various techniques are employed to create these advanced materials, each with unique advantages and effects on the composite's performance. In this section, we will explore some of the common fabrication methods used for CFCs.
In the prepreg layup method, fibers are pre-impregnated with resin and laid up in specific orientations, followed by curing under heat and pressure. This technique results in an excellent fiber-to-resin ratio, producing parts with high strength and stiffness. It is particularly beneficial for creating components with complex geometries and tailored mechanical properties.
Filament winding involves winding fibers onto a rotating mandrel, impregnating them with resin, and then curing the composite. This method is well-suited for cylindrical or spherical components and offers good fiber alignment, translating to improved strength in the winding direction.
Pultrusion is a continuous process where fibers are pulled through a resin bath and then through a heated die, curing the resin. This method produces parts with consistent cross-sectional profiles and high fiber volume fractions, resulting in high strength and stiffness along the length of the part.
In RTM, fibers are placed in a mold, and resin is injected under pressure. This technique can produce complex geometries and offers good control over the fiber-to-resin ratio, allowing for the tailoring of mechanical properties.
Continuous fibers can be incorporated into 3D printed parts using specialized printers that combine fibers with thermoplastic resins. This innovative technique enables the creation of complex geometries and the customization of fiber orientations, providing optimized mechanical properties for specific applications.
AFP utilizes a robotic system to precisely lay down continuous fiber tapes onto a mold or tooling surface. This method enables accurate control of fiber orientation and placement, resulting in highly tailored mechanical properties and complex geometries. It also reduces material waste and improves production efficiency.
The chosen fabrication technique directly impacts the properties of CFCs, influencing factors such as fiber alignment, fiber-to-resin ratio, and curing conditions. By understanding and selecting the appropriate fabrication method, manufacturers can optimize the performance of CFC components, ensuring they meet the specific requirements of their applications.
Continuous Fiber Composites (CFCs) have found their place in a myriad of industries, thanks to their exceptional properties and performance. In this section, we will explore some of the typical applications of CFCs and the advantages they bring to these fields.
In the aerospace industry, CFCs are a material of choice for various aircraft components including wings, fuselage, and interior structures. The high strength-to-weight ratio, stiffness, and corrosion resistance of CFCs contribute to lighter and more fuel-efficient aircraft designs, without compromising safety and performance. The ability to tailor the stiffness and strength of CFCs according to specific load requirements makes them ideal for aerospace applications.
The automotive sector leverages CFCs for manufacturing vehicle components such as body panels, chassis, and suspension systems. The use of CFCs results in a significant reduction in weight, leading to improved fuel efficiency and performance. Additionally, the durability and resistance to wear and tear of CFCs contribute to the longevity and reliability of automotive parts.
Wind turbine blades manufactured from CFCs exhibit increased stiffness and fatigue resistance, which are crucial for larger, more efficient designs. The material's ability to withstand demanding environmental conditions ensures the longevity and performance of wind turbines, contributing to the sustainability of renewable energy sources.
CFCs are extensively used in sports equipment like bicycles, golf clubs, tennis racquets, and more. The lightweight, high-strength, and tailored stiffness properties of CFCs enhance performance and durability, providing athletes with reliable and efficient equipment.
In the field of infrastructure, CFCs find applications in bridge decks, reinforcing bars, and other structural elements. Their corrosion resistance, reduced weight, and ease of installation lead to lower maintenance costs and extended service life, making CFCs a cost-effective solution for infrastructure projects.
The marine industry benefits from the use of CFCs in ship hulls, masts, and propellers. The materials provide improved strength, reduced weight, and better resistance to the harsh marine environment, contributing to the efficiency and longevity of marine vessels.
The versatility and superior properties of Continuous Fiber Composites make them a preferred choice in various industries, offering unparalleled advantages in terms of strength, weight, durability, and performance. As we continue to innovate and explore new applications, the potential of CFCs in revolutionizing industries is boundless.
The field of Continuous Fiber Composites (CFCs) is rapidly evolving, with numerous advancements and innovations enhancing their capabilities and expanding their applications. In this section, we will explore some of the current developments that are shaping the future of CFCs.
Innovations in manufacturing techniques are playing a pivotal role in optimizing the properties of CFCs. Automated Fiber Placement (AFP) is a notable example, where a robotic system precisely lays down continuous fiber tapes onto a mold or tooling surface. This technique ensures accurate control of fiber orientation and placement, resulting in highly tailored mechanical properties and complex geometries. Additionally, it reduces material waste and improves production efficiency.
The integration of 3D printing technology, such as Continuous Fiber 3D Printing (CF3D), is revolutionizing the production of CFCs. This technology enables the direct manufacturing of complex geometries with tailored fiber reinforcement, paving the way for lightweight, high-performance components across various industries.
The development of hybrid composites, which combine continuous fibers with other materials like nanoparticles or metallic foams, results in enhanced properties such as improved thermal or electrical conductivity, impact resistance, and vibration damping. Additionally, multifunctional composites integrate additional functionalities like sensing capabilities or self-healing properties, leading to the creation of smart structures capable of monitoring their own health and responding to damage.
In response to growing environmental concerns, there is a significant push towards developing bio-based and recyclable matrix materials for CFCs. These sustainable alternatives aim to address issues related to end-of-life disposal and contribute to the overall sustainability of composite materials.
Advanced modeling techniques and simulation tools are being employed to better understand and predict the behavior of CFCs under various conditions. This leads to more efficient designs, improved performance, and the ability to tailor composites to specific applications.
These advancements and innovations are not only enhancing the properties and capabilities of Continuous Fiber Composites but also opening up new avenues for their application. As we continue to push the boundaries of what is possible with these materials, the future holds exciting prospects for industries ranging from aerospace and automotive to renewable energy and beyond.
Discover the future of composite manufacturing with Addcomposites! Here's how you can get involved:
At Addcomposites, we are dedicated to revolutionizing composite manufacturing. Our AFP systems and comprehensive support services are waiting for you to harness. So, don't wait – get started on your journey to the future of manufacturing today!