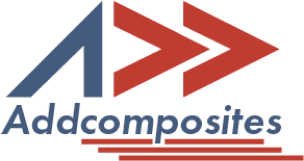
We would like to express our deepest gratitude to the authors of the article "Crystallization mechanism and mechanical properties of CF/PPS thermoplastic composites manufactured by laser-assisted automated fiber placement". The authors, Dacheng Zhao, Zhefu Li, Weiping Liu, Ting Li, Guangquan Yue, and Lijian Pan, have provided invaluable insights into the crystallization process of CF/PPS composites during the automated fiber placement process and its effect on the mechanical properties of the composites. Their work has significantly contributed to the following blog.
The key problem the article addresses is the challenge of controlling the performance and quality of thermoplastic composites manufactured by automated fiber placement (AFP) or tape laying (ATL). The unique processing characteristics of these methods, such as the short dwell time of temperature and pressure on layers and the exceptionally high cooling rate, make it difficult to achieve perfect consolidation and good crystallinity of the composites.
The article focuses explicitly on the crystallization mechanism of carbon fiber/polyphenylene sulfide (CF/PPS) composites during the AFP process and its effect on mechanical properties. Understanding this complicated crystallization process is crucial for controlling the performance of the composites.
We approach the problem by investigating the crystallization mechanism of carbon fiber/polyphenylene sulfide (CF/PPS) composites during the automated fiber placement (AFP) process and its effect on the mechanical properties.
The crystallization kinetics analysis indicated that the crystallinity of the CF/PPS composites was influenced by parameters including laser temperature, placement speed, and tool temperature, with the tool temperature being the main factor. The authors found that increasing the tool temperature was an effective method to achieve high crystallinity.
Table: Crystallinity of thermoplastic composites manufactured by AFP/ATP in the literatures.
When the tool temperature was in the range of the crystallization window, the composites could experience isothermal crystallization, which could further improve the crystallinity. With the increase of the tool temperature, the flexural strength and interlaminar shear strength were improved due to the enhanced self-adhesion of the matrix, while the Mode I fracture toughness was decreased because of the reduction of the matrix ductility.
Understanding the crystallization process is crucial for controlling the performance of composites manufactured by automated fiber placement (AFP) for several reasons:
The crystallinity of carbon fiber/polyphenylene sulfide (CF/PPS) thermoplastic composites manufactured by automated fiber placement is influenced by several factors:
Here is a step-by-step guide for an Automated Fiber Placement (AFP) process operator to achieve better crystallinity in CF/PPS thermoplastic composites:
Discover the future of composite manufacturing with Addcomposites! Here's how you can get involved:
At Addcomposites, we are dedicated to revolutionizing composite manufacturing. Our AFP systems and comprehensive support services are waiting for you to harness. So, don't wait – get started on your journey to the future of manufacturing today!
We would like to express our deepest gratitude to the authors of the article "Crystallization mechanism and mechanical properties of CF/PPS thermoplastic composites manufactured by laser-assisted automated fiber placement". The authors, Dacheng Zhao, Zhefu Li, Weiping Liu, Ting Li, Guangquan Yue, and Lijian Pan, have provided invaluable insights into the crystallization process of CF/PPS composites during the automated fiber placement process and its effect on the mechanical properties of the composites. Their work has significantly contributed to the following blog.
The key problem the article addresses is the challenge of controlling the performance and quality of thermoplastic composites manufactured by automated fiber placement (AFP) or tape laying (ATL). The unique processing characteristics of these methods, such as the short dwell time of temperature and pressure on layers and the exceptionally high cooling rate, make it difficult to achieve perfect consolidation and good crystallinity of the composites.
The article focuses explicitly on the crystallization mechanism of carbon fiber/polyphenylene sulfide (CF/PPS) composites during the AFP process and its effect on mechanical properties. Understanding this complicated crystallization process is crucial for controlling the performance of the composites.
We approach the problem by investigating the crystallization mechanism of carbon fiber/polyphenylene sulfide (CF/PPS) composites during the automated fiber placement (AFP) process and its effect on the mechanical properties.
The crystallization kinetics analysis indicated that the crystallinity of the CF/PPS composites was influenced by parameters including laser temperature, placement speed, and tool temperature, with the tool temperature being the main factor. The authors found that increasing the tool temperature was an effective method to achieve high crystallinity.
Table: Crystallinity of thermoplastic composites manufactured by AFP/ATP in the literatures.
When the tool temperature was in the range of the crystallization window, the composites could experience isothermal crystallization, which could further improve the crystallinity. With the increase of the tool temperature, the flexural strength and interlaminar shear strength were improved due to the enhanced self-adhesion of the matrix, while the Mode I fracture toughness was decreased because of the reduction of the matrix ductility.
Understanding the crystallization process is crucial for controlling the performance of composites manufactured by automated fiber placement (AFP) for several reasons:
The crystallinity of carbon fiber/polyphenylene sulfide (CF/PPS) thermoplastic composites manufactured by automated fiber placement is influenced by several factors:
Here is a step-by-step guide for an Automated Fiber Placement (AFP) process operator to achieve better crystallinity in CF/PPS thermoplastic composites:
Discover the future of composite manufacturing with Addcomposites! Here's how you can get involved:
At Addcomposites, we are dedicated to revolutionizing composite manufacturing. Our AFP systems and comprehensive support services are waiting for you to harness. So, don't wait – get started on your journey to the future of manufacturing today!