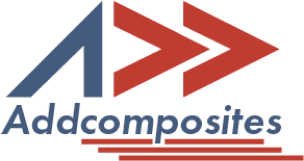
In the world of composite manufacturing, the term "prepreg tack" often surfaces as a pivotal factor dictating the success of automated processes like Automated Fiber Placement (AFP) and Automated Tape Laying (ATL). This seemingly obscure term holds immense significance in the realm of carbon fiber reinforced plastics, which are crucial for lightweight construction in modern aviation and beyond. This blog delves into the intricate world of prepreg tack, guided by insights from a comprehensive research article titled "A Review of Mechanisms, Measurement, and Manufacturing Implication."
At its core, prepreg tack refers to the stickiness of prepreg materials—pre-impregnated with resin fibers—that facilitates their placement and adhesion during automated lay-up processes without intervening in the curing stage of epoxy. This property is not just about being sticky; it embodies a complex interplay of adhesive and cohesive forces influenced by a myriad of factors, including environmental conditions, machine parameters, and intrinsic material properties. Understanding and optimizing prepreg tack is thus a dance with physics, chemistry, and engineering.
The introduction of automated lay-up processes such as AFP and ATL has revolutionized the manufacturing of large-scale composite parts. These technologies offer unparalleled advantages over traditional hand lamination, enhancing quality and productivity. However, the success of these advancements hinges on the optimal management of prepreg tack. Too little tack, and the material may not hold its place; too much, and it might stick to the machine elements or cause defects in the final product.
The journey to understanding prepreg tack takes us through the various parameters that govern its behavior. From the processing framework of AFP/ATL to the unique properties of prepregs, the balance of tack is a delicate one. It must be precisely managed to prevent production-induced defects such as gaps, overlaps, and wrinkles—each of which can significantly detract from the mechanical properties of the final composite part.
One of the challenges in mastering prepreg tack is its measurement. Traditional methods have been largely heuristic, lacking standardization. Recent strides have seen the development of two ASTM test methods designed to quantify tack in resin-impregnated fibers, marking a significant step forward. The Probe Tack Test and the Peel Test, each with its methodology and focus, provide valuable insights into the debonding process and peel resistance of adhesive bonds, respectively.
The quest to unravel the mysteries of prepreg tack is not new. Spanning almost four decades, experimental research has continuously evolved, exploring the effects of process parameters, environmental factors, and material properties. This body of work reveals the nuanced and often complex response of prepreg tack to various influences, underscoring the ongoing relevance and complexity of this field.
Prepreg tack is more than just a technical term in the composite manufacturing industry. It is a critical property that requires deep understanding and careful control to ensure the success of automated lay-up processes. Through a blend of experimental research, innovative measurement methods, and an appreciation for the underlying science, the industry continues to make strides in optimizing this essential factor. As we delve deeper into the nuances of prepreg tack, the future of composite manufacturing looks both challenging and promising, with endless possibilities for innovation and improvement.
Factor Type
Specific Factors
Impact on Tack
Machine Parameters
Automated machinery type
Varies with machinery
Environmental Conditions
Temperature, Humidity
Increases or decreases tack
Material Properties
Resin type, Fiber composition
Determines base tack level
Discover the future of composite manufacturing with Addcomposites! Here's how you can get involved:
At Addcomposites, we are dedicated to revolutionizing composite manufacturing. Our AFP systems and comprehensive support services are waiting for you to harness. So, don't wait – get started on your journey to the future of manufacturing today!
In the world of composite manufacturing, the term "prepreg tack" often surfaces as a pivotal factor dictating the success of automated processes like Automated Fiber Placement (AFP) and Automated Tape Laying (ATL). This seemingly obscure term holds immense significance in the realm of carbon fiber reinforced plastics, which are crucial for lightweight construction in modern aviation and beyond. This blog delves into the intricate world of prepreg tack, guided by insights from a comprehensive research article titled "A Review of Mechanisms, Measurement, and Manufacturing Implication."
At its core, prepreg tack refers to the stickiness of prepreg materials—pre-impregnated with resin fibers—that facilitates their placement and adhesion during automated lay-up processes without intervening in the curing stage of epoxy. This property is not just about being sticky; it embodies a complex interplay of adhesive and cohesive forces influenced by a myriad of factors, including environmental conditions, machine parameters, and intrinsic material properties. Understanding and optimizing prepreg tack is thus a dance with physics, chemistry, and engineering.
The introduction of automated lay-up processes such as AFP and ATL has revolutionized the manufacturing of large-scale composite parts. These technologies offer unparalleled advantages over traditional hand lamination, enhancing quality and productivity. However, the success of these advancements hinges on the optimal management of prepreg tack. Too little tack, and the material may not hold its place; too much, and it might stick to the machine elements or cause defects in the final product.
The journey to understanding prepreg tack takes us through the various parameters that govern its behavior. From the processing framework of AFP/ATL to the unique properties of prepregs, the balance of tack is a delicate one. It must be precisely managed to prevent production-induced defects such as gaps, overlaps, and wrinkles—each of which can significantly detract from the mechanical properties of the final composite part.
One of the challenges in mastering prepreg tack is its measurement. Traditional methods have been largely heuristic, lacking standardization. Recent strides have seen the development of two ASTM test methods designed to quantify tack in resin-impregnated fibers, marking a significant step forward. The Probe Tack Test and the Peel Test, each with its methodology and focus, provide valuable insights into the debonding process and peel resistance of adhesive bonds, respectively.
The quest to unravel the mysteries of prepreg tack is not new. Spanning almost four decades, experimental research has continuously evolved, exploring the effects of process parameters, environmental factors, and material properties. This body of work reveals the nuanced and often complex response of prepreg tack to various influences, underscoring the ongoing relevance and complexity of this field.
Prepreg tack is more than just a technical term in the composite manufacturing industry. It is a critical property that requires deep understanding and careful control to ensure the success of automated lay-up processes. Through a blend of experimental research, innovative measurement methods, and an appreciation for the underlying science, the industry continues to make strides in optimizing this essential factor. As we delve deeper into the nuances of prepreg tack, the future of composite manufacturing looks both challenging and promising, with endless possibilities for innovation and improvement.
Factor Type
Specific Factors
Impact on Tack
Machine Parameters
Automated machinery type
Varies with machinery
Environmental Conditions
Temperature, Humidity
Increases or decreases tack
Material Properties
Resin type, Fiber composition
Determines base tack level
Discover the future of composite manufacturing with Addcomposites! Here's how you can get involved:
At Addcomposites, we are dedicated to revolutionizing composite manufacturing. Our AFP systems and comprehensive support services are waiting for you to harness. So, don't wait – get started on your journey to the future of manufacturing today!