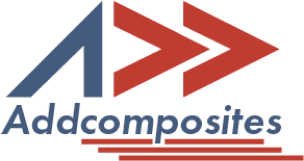
In the sophisticated realm of composite manufacturing, the Automated Fiber Placement (AFP) process stands out for its precision and efficiency in creating complex structures. However, this advanced technique encounters a nuanced challenge that could undermine the integrity of the final composite part: the contamination of the compaction roller with release agent residues. This issue arises due to the roller's design, which, while ensuring tape adhesion, inadvertently picks up and redistributes release agent applied on the mold surface, potentially compromising layer bonding. Addressing this challenge demands a multifaceted approach, blending traditional practices with innovative strategies to ensure the flawless execution of AFP processes. This exploration delves into the problem and examines potential solutions, from the use of release films and edge taping methods to the minimized application of release agents and the imperative for ongoing technological innovation.
In the realm of advanced composites manufacturing, Automated Fiber Placement (AFP) represents a pinnacle of precision and efficiency, enabling the creation of complex structures with high-performance materials. A critical aspect of this process involves the application of release agents to the mold surface, ensuring the seamless release of the composite part once cured. However, the AFP process introduces a nuanced challenge that complicates this seemingly straightforward task.
The compaction roller, a central component of the AFP machine, is designed wider than the tape width. This design choice is strategic, aimed at ensuring the tape adheres firmly to the mold without slipping, a necessity for the accuracy and integrity of the composite layup. While effective for its intended purpose, this design introduces a significant complication: the accumulation of release agent residues on the compaction roller.
As the roller traverses the mold surface, it inevitably picks up release agent applied to the mold. This phenomenon occurs because the roller extends beyond the edges of the tape, coming into direct contact with areas of the mold treated with release agent. Over successive passes, the roller can become contaminated with this agent, leading to a problematic cycle where the roller itself becomes a medium for transferring release agent residues back onto the tape or subsequent layers. This contamination can compromise the bonding between layers, affect the composite's structural integrity, and lead to defects in the final product.
The issue is further compounded by the necessity of a meticulously applied release agent. The standard approach of liberally applying release agent to ensure easy demolding is not viable in AFP processes. An excess of release agent, especially types that are prone to transfer or migration, can exacerbate the issue, leading to increased contamination risks. Consequently, the selection and application method of the release agent in AFP processes cannot follow the traditional paradigms used in other forms of composites manufacturing.
Addressing the challenge of release agent contamination in Automated Fiber Placement (AFP) processes requires innovative strategies that balance the need for effective mold release without compromising the integrity of the composite layup. The strategies you've outlined present a spectrum of solutions, each with its benefits and limitations. Here's an exploration of these strategies, including their potential advantages and challenges:
Advantages:
Challenges:
Advantages:
Challenges:
Advantages:
Challenges:
Given the challenges and limitations of the strategies discussed, a combination of approaches, along with ongoing innovation, may offer the best path forward:
Each of these strategies presents its own set of challenges and opportunities for innovation. Collaboration between material scientists, process engineers, and equipment manufacturers will be crucial in developing effective solutions that enhance the efficiency and quality of AFP-manufactured composite materials.
This challenge necessitates a reevaluation of release agent selection and application strategies tailored specifically for AFP. The ideal release agent for AFP processes must possess characteristics that prevent it from being easily transferred or picked up by the compaction roller, while still providing effective release properties. Additionally, application methods must be refined to minimize the potential for roller contamination, possibly through targeted application techniques or the development of new roller designs that minimize contact with treated mold areas.
The nuanced challenge of release agent application in AFP processes underscores the need for innovation and adaptation in composite manufacturing techniques. Addressing this issue is not merely a matter of improving material properties or refining application methods; it represents a critical intersection of engineering design, material science, and process optimization. Successfully overcoming this hurdle is essential for advancing the capabilities and applications of AFP technology, ensuring that the composites industry can continue to push the boundaries of what is possible.
Discover the future of composite manufacturing with Addcomposites! Here's how you can get involved:
At Addcomposites, we are dedicated to revolutionizing composite manufacturing. Our AFP systems and comprehensive support services are waiting for you to harness. So, don't wait – get started on your journey to the future of manufacturing today!
In the sophisticated realm of composite manufacturing, the Automated Fiber Placement (AFP) process stands out for its precision and efficiency in creating complex structures. However, this advanced technique encounters a nuanced challenge that could undermine the integrity of the final composite part: the contamination of the compaction roller with release agent residues. This issue arises due to the roller's design, which, while ensuring tape adhesion, inadvertently picks up and redistributes release agent applied on the mold surface, potentially compromising layer bonding. Addressing this challenge demands a multifaceted approach, blending traditional practices with innovative strategies to ensure the flawless execution of AFP processes. This exploration delves into the problem and examines potential solutions, from the use of release films and edge taping methods to the minimized application of release agents and the imperative for ongoing technological innovation.
In the realm of advanced composites manufacturing, Automated Fiber Placement (AFP) represents a pinnacle of precision and efficiency, enabling the creation of complex structures with high-performance materials. A critical aspect of this process involves the application of release agents to the mold surface, ensuring the seamless release of the composite part once cured. However, the AFP process introduces a nuanced challenge that complicates this seemingly straightforward task.
The compaction roller, a central component of the AFP machine, is designed wider than the tape width. This design choice is strategic, aimed at ensuring the tape adheres firmly to the mold without slipping, a necessity for the accuracy and integrity of the composite layup. While effective for its intended purpose, this design introduces a significant complication: the accumulation of release agent residues on the compaction roller.
As the roller traverses the mold surface, it inevitably picks up release agent applied to the mold. This phenomenon occurs because the roller extends beyond the edges of the tape, coming into direct contact with areas of the mold treated with release agent. Over successive passes, the roller can become contaminated with this agent, leading to a problematic cycle where the roller itself becomes a medium for transferring release agent residues back onto the tape or subsequent layers. This contamination can compromise the bonding between layers, affect the composite's structural integrity, and lead to defects in the final product.
The issue is further compounded by the necessity of a meticulously applied release agent. The standard approach of liberally applying release agent to ensure easy demolding is not viable in AFP processes. An excess of release agent, especially types that are prone to transfer or migration, can exacerbate the issue, leading to increased contamination risks. Consequently, the selection and application method of the release agent in AFP processes cannot follow the traditional paradigms used in other forms of composites manufacturing.
Addressing the challenge of release agent contamination in Automated Fiber Placement (AFP) processes requires innovative strategies that balance the need for effective mold release without compromising the integrity of the composite layup. The strategies you've outlined present a spectrum of solutions, each with its benefits and limitations. Here's an exploration of these strategies, including their potential advantages and challenges:
Advantages:
Challenges:
Advantages:
Challenges:
Advantages:
Challenges:
Given the challenges and limitations of the strategies discussed, a combination of approaches, along with ongoing innovation, may offer the best path forward:
Each of these strategies presents its own set of challenges and opportunities for innovation. Collaboration between material scientists, process engineers, and equipment manufacturers will be crucial in developing effective solutions that enhance the efficiency and quality of AFP-manufactured composite materials.
This challenge necessitates a reevaluation of release agent selection and application strategies tailored specifically for AFP. The ideal release agent for AFP processes must possess characteristics that prevent it from being easily transferred or picked up by the compaction roller, while still providing effective release properties. Additionally, application methods must be refined to minimize the potential for roller contamination, possibly through targeted application techniques or the development of new roller designs that minimize contact with treated mold areas.
The nuanced challenge of release agent application in AFP processes underscores the need for innovation and adaptation in composite manufacturing techniques. Addressing this issue is not merely a matter of improving material properties or refining application methods; it represents a critical intersection of engineering design, material science, and process optimization. Successfully overcoming this hurdle is essential for advancing the capabilities and applications of AFP technology, ensuring that the composites industry can continue to push the boundaries of what is possible.
Discover the future of composite manufacturing with Addcomposites! Here's how you can get involved:
At Addcomposites, we are dedicated to revolutionizing composite manufacturing. Our AFP systems and comprehensive support services are waiting for you to harness. So, don't wait – get started on your journey to the future of manufacturing today!