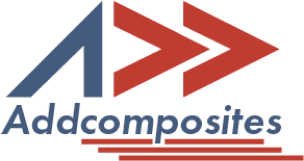
Open mold methods allow for a rapid product development cycle because the tooling fabrication process is simple and relatively low cost.
The simplest molding process, hand lay-up is used in the low-volume production of large products, e.g., wind turbine components, concrete forms, and radomes. In the wet lay-up process, shown in the figure above, a dry reinforcement, usually a woven glass cloth, is placed manually on the mold. A low-viscosity liquid resin is then applied to the reinforcement by pouring, brushing, or spraying. Squeegees or rollers are used to
densify the lay-up, thoroughly wetting the reinforcement with the resin and removing excess resin and entrapped air. The laminate is built up layer by layer until the required thickness is obtained.
Similar to hand lay-up, spray-up offers greater shape complexity and faster production. Spray-up utilizes a low-cost open mold, room temperature curing resin, and is ideal for producing large parts such as tub/shower units and vent hoods in low to moderate quantities.
Chopper/spray guns that mix the resin and spray it out of a gun along with little short strands of fiberglass roving. These machines combined with a skilled operator can laminate really fast – and depending on the attention paid to rolling the laminate – potentially neatly. The resulting laminate is not high performance. It is resin rich: easily 60% resin by weight – and thickness is variable and often hard to control. As with lay-up, manual rolling on top of the sprayed fiber-resin layer removes entrapped air and wets the fiber reinforcement. Woven roving is often added in specific areas for thickness or greater strength. Pigmented gel coats can be used to produce a smooth, colorful surface.
Open mold methods allow for a rapid product development cycle because of low equipment costs. However, the quality is uncertain due to the dependency on the quality of manual labor.
Addcomposites is the provider of the Automated Fiber Placement (AFP) system. The AFP system can be rented on a monthly basis to work with thermosets, thermoplastic, dry fiber placement, or in combination with 3d printers
Structural composites materials
Open mold methods allow for a rapid product development cycle because the tooling fabrication process is simple and relatively low cost.
The simplest molding process, hand lay-up is used in the low-volume production of large products, e.g., wind turbine components, concrete forms, and radomes. In the wet lay-up process, shown in the figure above, a dry reinforcement, usually a woven glass cloth, is placed manually on the mold. A low-viscosity liquid resin is then applied to the reinforcement by pouring, brushing, or spraying. Squeegees or rollers are used to
densify the lay-up, thoroughly wetting the reinforcement with the resin and removing excess resin and entrapped air. The laminate is built up layer by layer until the required thickness is obtained.
Similar to hand lay-up, spray-up offers greater shape complexity and faster production. Spray-up utilizes a low-cost open mold, room temperature curing resin, and is ideal for producing large parts such as tub/shower units and vent hoods in low to moderate quantities.
Chopper/spray guns that mix the resin and spray it out of a gun along with little short strands of fiberglass roving. These machines combined with a skilled operator can laminate really fast – and depending on the attention paid to rolling the laminate – potentially neatly. The resulting laminate is not high performance. It is resin rich: easily 60% resin by weight – and thickness is variable and often hard to control. As with lay-up, manual rolling on top of the sprayed fiber-resin layer removes entrapped air and wets the fiber reinforcement. Woven roving is often added in specific areas for thickness or greater strength. Pigmented gel coats can be used to produce a smooth, colorful surface.
Open mold methods allow for a rapid product development cycle because of low equipment costs. However, the quality is uncertain due to the dependency on the quality of manual labor.
Addcomposites is the provider of the Automated Fiber Placement (AFP) system. The AFP system can be rented on a monthly basis to work with thermosets, thermoplastic, dry fiber placement, or in combination with 3d printers
Structural composites materials