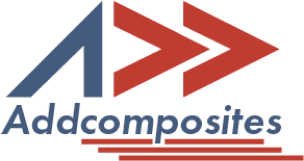
Achieving reliable first-layer adhesion is essential in large-format additive manufacturing (LFAM) to prevent warping, delamination, and print failures. This blog examines key adhesion methods, evaluating their efficiency, scalability, and industrial applicability. The heated build platform with a specialized surface coating is identified as the most effective solution, providing optimal adhesion through controlled temperature regulation. Automated control systems further enhance adhesion by dynamically adjusting first-layer parameters, ensuring consistency without manual intervention. The use of rafts or brims offers additional adhesion support but increases material consumption and post-processing efforts. Manual adhesive application, while occasionally used, is the least practical for LFAM due to its labor-intensive nature and inconsistent results. This analysis provides a comparative evaluation of these techniques, offering insights into their practical benefits and industry relevance.
Achieving reliable first-layer adhesion is essential in large-format additive manufacturing (LFAM) to prevent warping, delamination, and print failures. This blog examines key adhesion methods, evaluating their efficiency, scalability, and industrial applicability. The heated build platform with a specialized surface coating is identified as the most effective solution, providing optimal adhesion through controlled temperature regulation. Automated control systems further enhance adhesion by dynamically adjusting first-layer parameters, ensuring consistency without manual intervention. The use of rafts or brims offers additional adhesion support but increases material consumption and post-processing efforts. Manual adhesive application, while occasionally used, is the least practical for LFAM due to its labor-intensive nature and inconsistent results. This analysis provides a comparative evaluation of these techniques, offering insights into their practical benefits and industry relevance.
The most efficient method involves using a heated build platform, often equipped with a surface coating like polyimide foil, to ensure optimal temperature and adhesion for the first layer. This approach is standard in large format additive manufacturing (LFAM) systems, minimizing user intervention and enhancing reliability.
Many LFAM systems, such as those from BigRep, use automated control systems to optimize first layer parameters like temperature, speed, and layer thickness. This method ensures consistent adhesion without manual adjustments, making it highly efficient for industrial applications.
For complex geometries, adding a raft or brim can improve first layer adhesion by increasing the contact area with the build platform. However, this method is less efficient due to higher material consumption and longer print times, particularly for large parts.
In some cases, manually applying adhesive to the build platform can help, but it's the least efficient for LFAM due to the large scale, making it time-consuming and impractical for industrial settings.
This analysis explores the strategies for ensuring first layer adhesion in large format additive manufacturing (LFAM), a critical aspect for the success of large-scale 3D printing processes. LFAM, often used for producing parts over 1 meter in all directions, presents unique challenges compared to standard 3D printing, such as managing thermal gradients and ensuring adhesion over large build platforms. The following sections detail the methods identified, ranked from most to least efficient based on reliability, practicality, and industrial applicability, with a focus on polymer extrusion-based systems, given their prevalence in LFAM.
LFAM extends the principles of additive manufacturing to create large, complex parts, often used in industries like aerospace, automotive, and construction. The first layer's adhesion to the build platform is crucial, as poor adhesion can lead to warping, delamination, or print failure, especially given the scale and material properties involved. Research has shown that thermal management and surface preparation are key factors, with heated build platforms being a common feature in LFAM systems to mitigate thermal contraction and enhance bonding.
Efficiency is defined here as the method's reliability in ensuring adhesion, minimal need for user intervention, and practicality for large-scale industrial use. Methods were identified through a review of academic papers, industry reports, and manufacturer documentation, focusing on their applicability to LFAM. The ranking considers cost, time, and effectiveness, with an emphasis on scalability.
The following table summarizes the methods, their efficiency, and practicality for LFAM:
An unexpected finding is the integration of compaction techniques in some LFAM systems, such as substrate heating and compaction for enhanced bonding, as noted in research on continuous fiber printing (First Ever LFAM with High Volume Continuous Fiber Printing). While not widely detailed, this suggests potential for mechanical methods to improve adhesion, particularly in advanced composite printing, which may become more common in LFAM.
For LFAM, the most efficient strategy is a heated build platform with a suitable surface coating, followed by automated control systems for parameter optimization. Rafts or brims and manual adhesive application are less efficient, with the latter being impractical for large scales. These findings align with industry practices and research, emphasizing thermal management and automation for industrial-scale 3D printing.