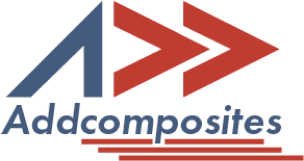
Composite materials have revolutionized various industries by offering a combination of strength, lightness, and durability. The process of joining composite materials plays a crucial role in harnessing their full potential. Two prominent methods for joining composites are adhesive bonding and mechanical joints. In this comprehensive blog post, we will delve into the intricacies of these methods, examining their advantages, considerations, and best practices for joining composite materials.
Adhesive bonding involves the use of adhesives to create strong bonds between different materials. Adhesives can form bonds through chemical reactions (chemical adhesives) or by interlocking on a microscale level (mechanical adhesives). Here are some key aspects of adhesive bonding:
Mechanical joints rely on physical fasteners, such as bolts, rivets, and screws, to connect composite materials. Let's explore some key aspects of mechanical joints:
To determine the most suitable joining method for your composite materials, consider the following factors:
Joining composite materials is a critical step in optimizing their strength, performance, and durability. Adhesive bonding and mechanical joints offer distinct advantages and considerations. Adhesive bonding provides lightweight construction, strength, durability, and repairability, while mechanical joints offer high load-carrying capacity, simplicity, and cost-effectiveness. By thoroughly assessing the requirements of your application and considering factors such as material compatibility, load conditions, environmental factors, weight considerations, and cost, you can make an informed decision on the most suitable joining method. Striking the right balance between adhesive bonding and mechanical joints will help you unlock the full potential of composite materials and create structures that excel in strength and performance.
Composite materials have revolutionized various industries by offering a combination of strength, lightness, and durability. The process of joining composite materials plays a crucial role in harnessing their full potential. Two prominent methods for joining composites are adhesive bonding and mechanical joints. In this comprehensive blog post, we will delve into the intricacies of these methods, examining their advantages, considerations, and best practices for joining composite materials.
Adhesive bonding involves the use of adhesives to create strong bonds between different materials. Adhesives can form bonds through chemical reactions (chemical adhesives) or by interlocking on a microscale level (mechanical adhesives). Here are some key aspects of adhesive bonding:
Mechanical joints rely on physical fasteners, such as bolts, rivets, and screws, to connect composite materials. Let's explore some key aspects of mechanical joints:
To determine the most suitable joining method for your composite materials, consider the following factors:
Joining composite materials is a critical step in optimizing their strength, performance, and durability. Adhesive bonding and mechanical joints offer distinct advantages and considerations. Adhesive bonding provides lightweight construction, strength, durability, and repairability, while mechanical joints offer high load-carrying capacity, simplicity, and cost-effectiveness. By thoroughly assessing the requirements of your application and considering factors such as material compatibility, load conditions, environmental factors, weight considerations, and cost, you can make an informed decision on the most suitable joining method. Striking the right balance between adhesive bonding and mechanical joints will help you unlock the full potential of composite materials and create structures that excel in strength and performance.